计量抽样的演变

Metrology Sampling Optimizer(MSO)旨在使用时间或百分比规则来处理基准计量抽样。除了基准抽样外,还可以配置规则来处理基于事件的抽样。事件规则确保在特定工具停机或质量事件后对高风险批次进行抽样。对于时间、百分比和事件抽样三种情况,MSO 优化抽样计划,以防止独立或叠加抽样。此优化最小化了满足所有抽样规则所需的批次数量。
新功能和改进
与试点客户的合作使我们的开发团队能够快速改进应用程序。
- 新的抽样覆盖仪表板功能可以快速调查并理解产品风险
- 用户界面 (UI) 的更新使规则管理变得快速而简单
- 新的工厂场景已包含在我们的核心逻辑更新中,以满足客户需求
- 自适应抽样以便根据不断变化的工厂需求调整抽样
抽样覆盖仪表板包含可配置的风险参数
抽样计划的主要目标之一是确保没有工具被低估抽样。我们为抽样覆盖仪表板开发了两个参数,使工程师可以按工具设定可接受的风险水平:
- 处于风险中的批次数量
- 处于风险中的晶圆数量
- 检测时间
这些限制通过易于诊断的颜色(红色、黄色、绿色)在仪表板中显示,以突出显示超出可接受限制的工具或模块。用户可以调整抽样率,以确保没有工具被低估或过度抽样。
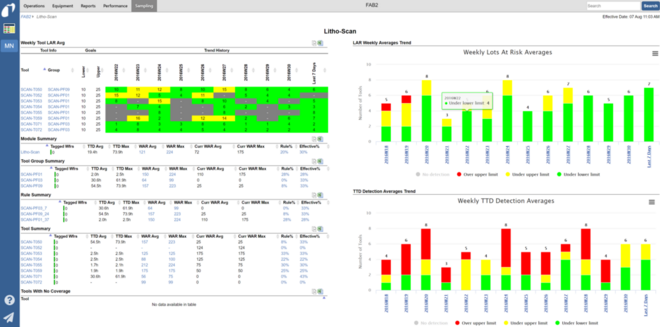
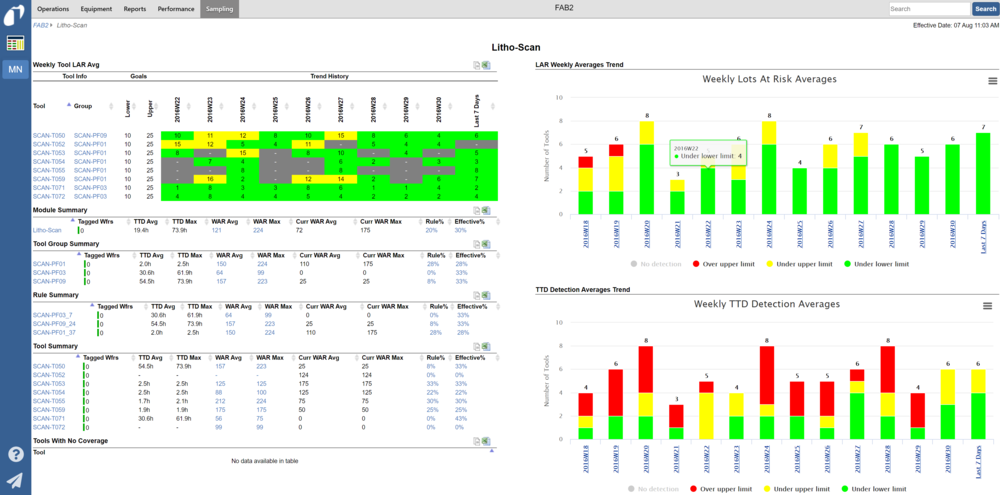
简化的规则管理
规则配置用户界面的改进集中在简化创建和编辑规则的过程。进行了显著的设计更改,带来了简洁明了的布局。添加了附加功能,以便在将处理步骤与计量相链接时轻松搜索步骤。

核心逻辑改进处理新抽样案例
以下核心逻辑增强功能已开发用于处理新的抽样案例:
标签条件 – 并非所有经过处理工具的批次都可以被标记。某些批次在计量步骤中没有配方。其他批次是某些特定产品或批次类型,这些批次永远不应被抽样。标签条件功能告诉系统在满足规则条件时哪些批次可以被抽样。
链接的计量 – 用户可以确保在链接的计量步骤中标记相同的批次。最常见的例子是确保相同的批次被标记用于前后测量。
MES 操作限制 – 为规则添加了限制,以确保对批次进行抽样并接收计量数据。如果抽样条件不满足且 MSO 找不到要测量的材料,这些限制允许 MSO 通过与 MES 交互(例如,将工具下线)来防止工厂不断增加风险。
未来的 MSO
FabGuard FDC 集成实现快速学习
MSO 和 FabGuard FDC 的集成将提供快速提高故障检测能力的功能。当检测到故障时,MSO 会强制进行计量测量,以了解是否存在相应的计量缺陷结果。如果存在计量缺陷结果但没有故障检测信号,则可以将信息提供给工程师,以调查为什么没有检测到故障,并识别出改进检测或传感的区域。两个产品的结合将产生独立运作无法实现的新学习。
基于扫描结果和计量在制品管理的自适应抽样
随着我们添加基于扫描结果的自适应抽样率以及在计量步骤中处理在制品队列管理的能力,MSO 将继续改进以应对容量有限的场景。
总结
感谢我们从客户那里收到的所有宝贵反馈,我们能够进行显著的改进,真正将 MSO 产品提升到一个新的水平。目前的版本提供了更好的抽样覆盖,管理更容易,并能处理更复杂的抽样情况。