正确校准如何提高生产质量
简单动作,重大影响。
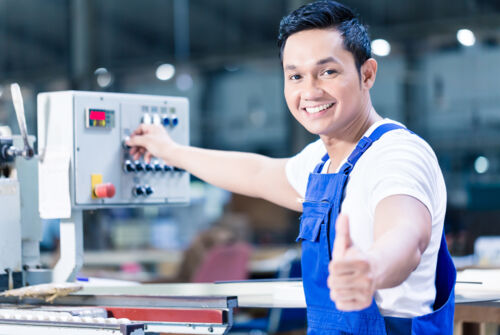
Xu Gong 是一名勤奋敬业的生产工程师,在一家知名的锂离子电池制造公司工作,他肩负着一项重要职责:负责在电池芯注入电解液之前对其进行氦泄漏测试。
为了完成这项重要任务,戴维依靠系统集成部门的同事设计的自动氦气泄漏测试系统。然而,尽管使用了这一高性能系统,质量问题依然存在。一些电池单元未能通过生产线末端测试,或者在发货后不久就出现问题,导致保修索赔和客户不满。
大卫决心解决这些问题,决定进一步调查这个问题。他意识到,关键可能在于氦气泄漏测试系统的校准过程。戴维与同事合作,确保在每个班次开始时使用与他们需要检测的最小泄漏相匹配的测试泄漏来校准系统。
尽管他们做出了努力,但质量问题依然存在,戴维变得越来越沮丧。就在这时,他偶然参加了一个氦气泄漏测试网络研讨会,结果让他大开眼界。网络研讨会强调了测试泄漏位置的重要性。
大卫好奇地检查了氦气泄漏测试系统的设置,发现测试漏孔安装在非常靠近检漏仪入口的地方。大卫意识到这种配置可能会影响结果的准确性,于是立即联系了系统集成部门。
他们首先尝试将测试泄漏直接连接到试验室,然后开始测量。令他们惊讶的是,系统未能检测到泄漏。这只能说明检漏仪也可能存在问题。 为了解决这个问题,他们决定更换检漏仪,并将测试漏孔连接到腔室中重新校准系统。这一次,系统成功检测到了泄漏,证实了他们的猜测,即之前的设置并不像预期的那样性能良好,现在他们终于可以确定正确的测量时间并成功校准系统了。
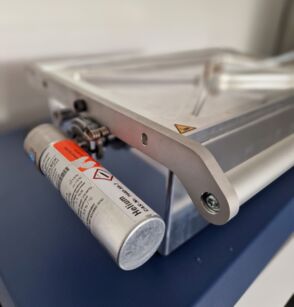
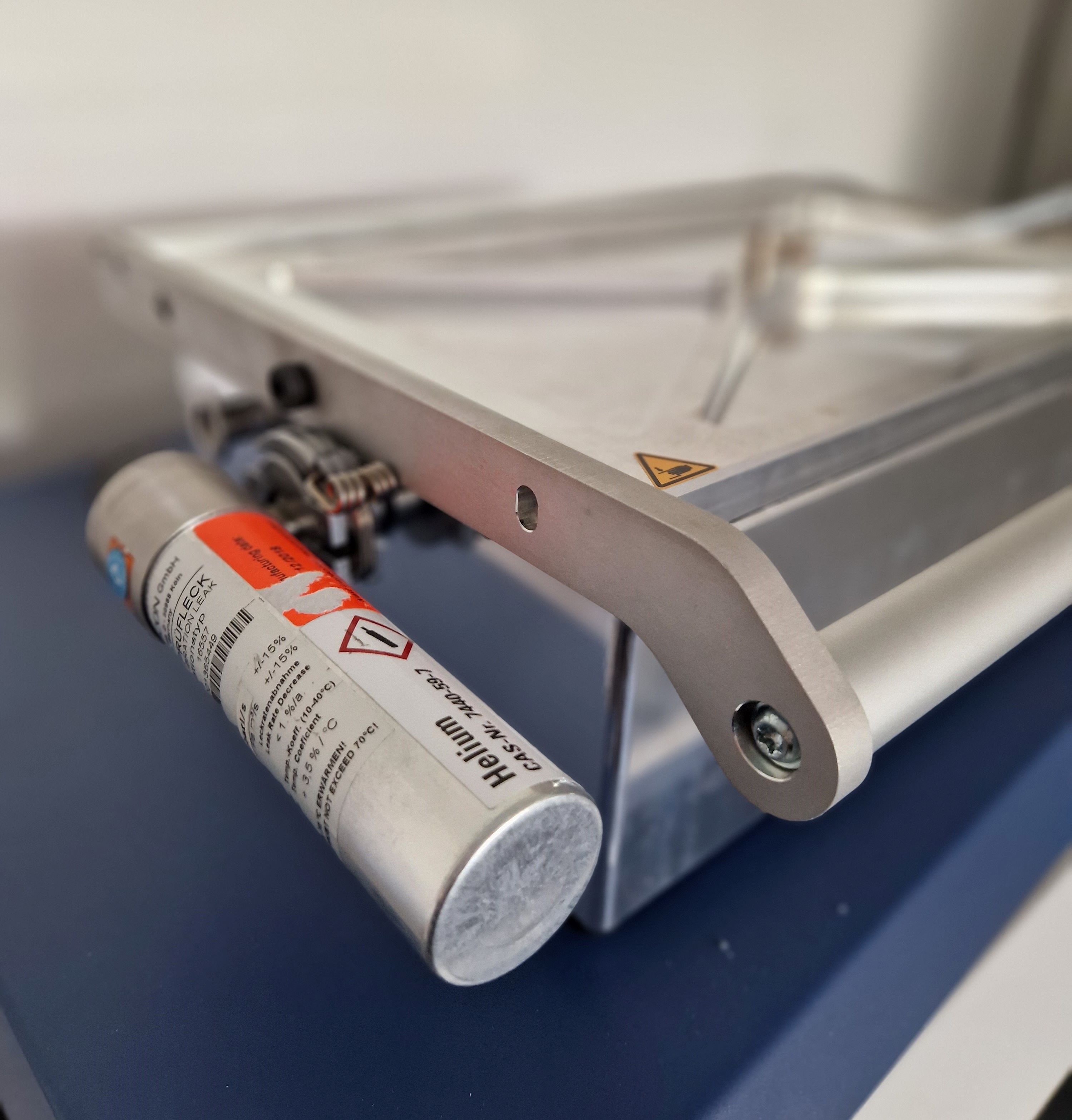
随着工艺流程的改变--新的检漏仪和将检漏位置直接设在检测室,公司不仅见证了生产线末端测试期间电池故障的显著减少,也见证了早期现场故障的显著减少。电池测试更加可靠,最终达到了客户期望的质量标准。
为了表彰 David 的敬业精神、解决问题的能力以及为提高公司产品质量所做的贡献,他获得了质量保证部的奖励。他的奉献精神和毅力不仅解决了一个关键问题,也为他的工作带来了极大的认可。
因此,David Xu 的故事提醒了我们持续改进、关注细节的重要性,以及即使是微小的变化也能对整体产品质量产生的影响。
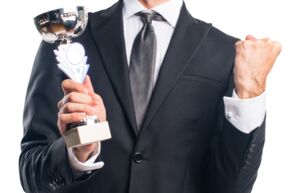
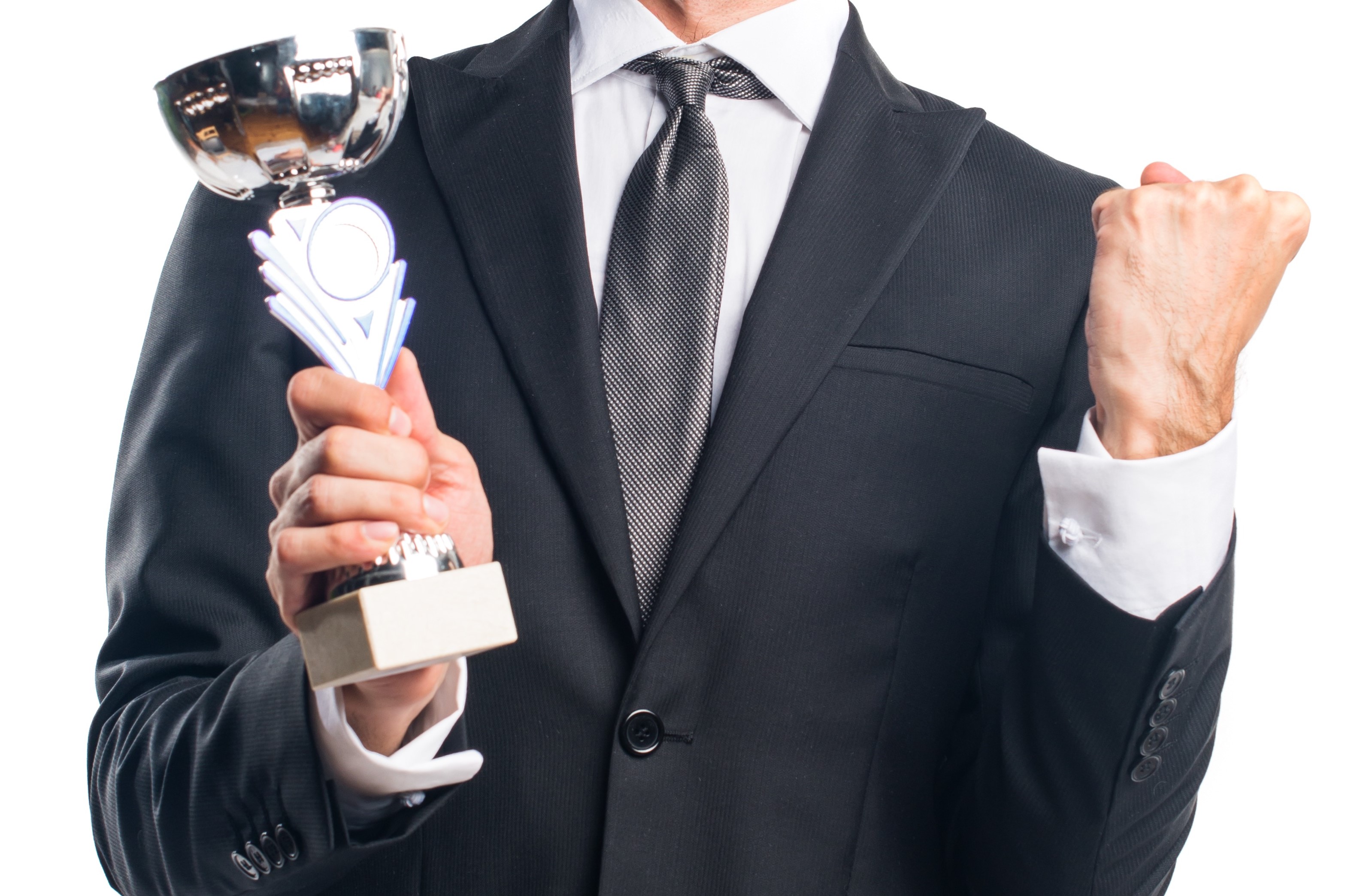