On the Benefits of Cycle Time Education
Why fabs should provide training for people who work in manufacturing on the fundamental drivers of cycle time
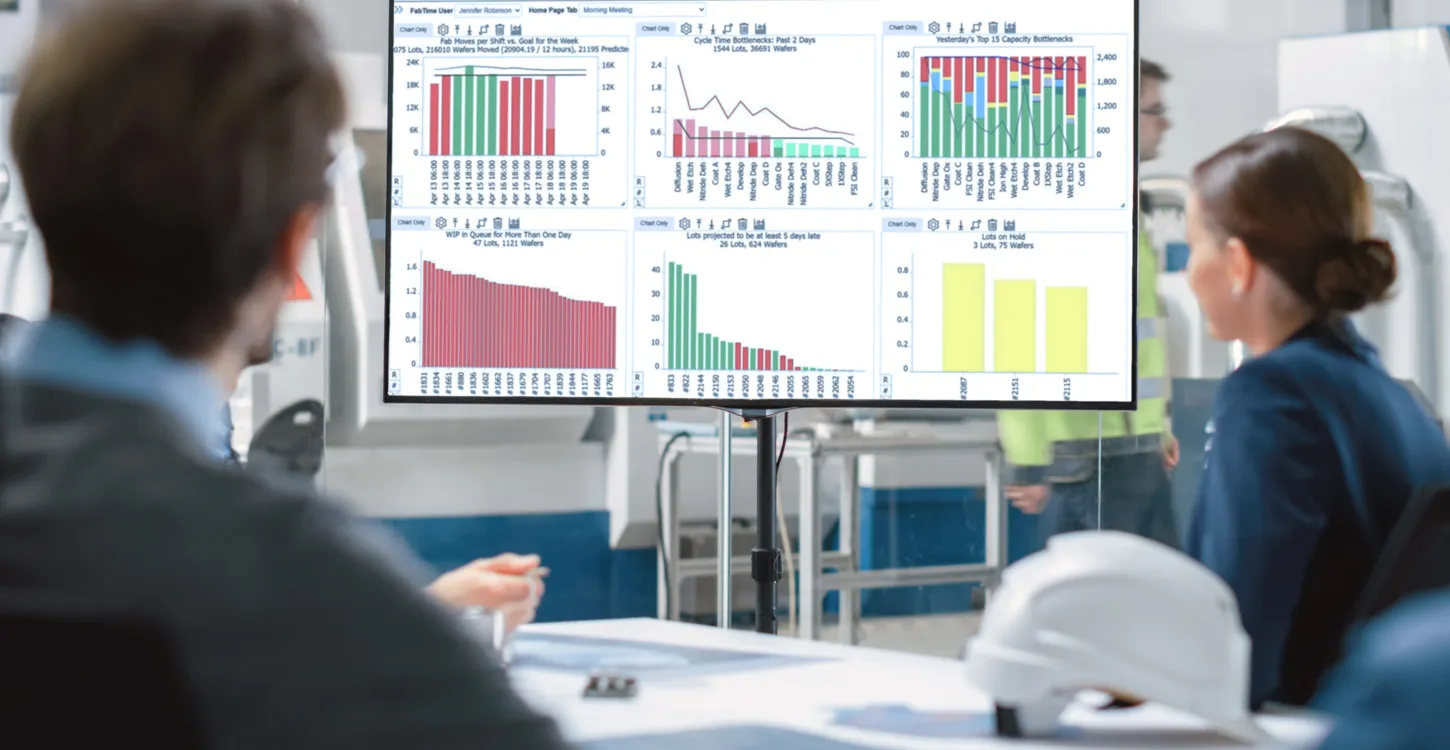
Skilled labor in the semiconductor industry is known to be in short supply. This shortage extends beyond operators and maintenance technicians into the realms of industrial engineers and fab management. Many skilled, knowledgeable people who have worked in the industry for decades are retiring and are difficult, if not impossible, to replace. One implication of this is that fabs are bringing in people who are less experienced. These fabs are providing training themselves and in some areas working with local universities. The SEMI Foundation is working on the training issue, as are the National Institute for Innovation and Technology (NIIT) and state governments like Arizona (working with NXP).
At INFICON, we believe that it is especially important for fabs to provide training for people who work in manufacturing on the fundamental drivers of cycle time, particularly utilization and variability. This training needs to comprehend and address the unique complexities of fabs that make running them so challenging, particularly the ones that have counter-intuitive implications. It also needs to teach participants to take advantage of data to identify real-time improvement opportunities.
Training on cycle time and factory behavior becomes even more necessary as background knowledge as software in the smart factory becomes more complicated. For example, configuring advanced scheduler features like automatic line balancing requires an understanding of cycle time fundamentals. Without such understanding, users may not recognize when advanced features are not working or are incorrectly configured.
The most forward-thinking fabs always take advantage of any relative demand slump to prepare for the next upturn. A great way to do that is by training staff on how to combine the right intuitions with the right data so that they can drive better future performance.
In this article, we share a brief history of the FabTime cycle time improvement class and explain what we cover and why. We highlight a few of our favorite concepts to teach, and close with some success stories.
FabTime Cycle Time Management Course History
Long before being acquired by INFICON, FabTime offered a course on cycle time improvement. The course was an off-shoot of this newsletter, in fact, so let’s start there. We sent out the first FabTime Cycle Time Management Newsletter in April of 2000. The welcome message for that issue said:
“The purpose of this newsletter is to build a community of people who are interested in cycle time management and give these people a way to communicate with each other and share new ideas. We’re also trying to better define cycle time management as a category within manufacturing management, because we think that it’s an important area. Newsletter topics will include definitions (Little’s Law, Hawthorne Effect, etc.), cycle time management ideas, success stories, discussion topics (where we aggregate feedback) and announcements/industry news.”
We’ve kept to that purpose and format rather well over the years.
In 2002, a fab manager who was an early subscriber to the newsletter called Jennifer Robinson to ask if we could provide some training that he was seeking. He wanted something that would convey cycle time/factory management to production personnel all the way down to technicians, or at least supervisors. He asked for something fab focused, but comprehensive. The idea was to show how fabs could use data from tools like the FabTime reporting software to improve things, starting by building intuition around core fundamentals such as how cycle time relates to utilization.
Jennifer Robinson and Frank Chance, who both studied Industrial Engineering in graduate school, worked with this fab manager on the outline for the course, drawing from material that we had already included in the newsletter and on the FabTime website. We created spreadsheet companion tools, quizzes, and pencil and paper exercises, to make the course as interactive as possible. We even used dice to simulate possible batch sizes for one exercise. We delivered the first session of the course in August of 2002.
We subsequently delivered the class in person as a one-day or two-day course to many fabs over the next 18 years. Memorable experiences included a trip to Ireland for multiple sessions, and an extremely cold trip to Minneapolis one February. The class helped us to stay in business during industry downturns, particularly 2009, when several companies hosted multiple sessions of the class.
We focused mainly on doing sessions for individual companies, except for one multi-company session held in the Bay Area. The logistics for charging individuals made multi-company sessions challenging, and we also felt that it was better to have an audience from a single company, so that people could speak openly about their specific challenges.
With the advent of Covid in 2020, we converted the class to a four-hour online course delivered via Teams. The new format worked well. It forced us to condense the material down to what was most important and enabled us to deliver the class to people from more different time zones. Travel time had previously made doing international sessions of the course impractical.
Now that we’re with INFICON, we anticipate that the course may change further. Perhaps future versions will integrate more content focused on managing Smart Manufacturing tools, addressing topics like automated line balancing with a factory scheduler or enhanced cycle time models. Perhaps we will add a recorded, self-paced version, instead of the current instructor-led Teams version. But for this article, we’ll focus on the course as it is currently offered.
What’s Included in Our Course and Why
We encourage companies hosting our course to invite people from different parts of the organization, including manufacturing, process engineering, equipment engineering, industrial engineering, and production control. We do this because people in each of these positions affect the cycle time of the fab in different ways. Having everyone be part of a single discussion can help with the implementation of changes.
We have found that it can be particularly helpful to include process engineers in cycle time training. Process restrictions and holds have a much bigger cycle time impact than is commonly realized. Including senior management in cycle time training can also be useful in setting expectations for how much cycle time can be improved in a given environment.
We’ve also learned over the years that a key success factor for our courses is having at least one participant who is willing to speak up and answer questions about the site. Often this person is someone senior in the manufacturing organization. Alternatively, this may be an industrial engineer who is already familiar with the general concepts taught in the class. Without someone willing to speak up in the audience, it can be difficult to get audience participation, and thus to tailor the discussion to the specific needs of the site. For Teams-based classes, having engagement with the audience is important to keep people from tuning out (or tuning back in to their email instead of to the material).
Our current course is usually delivered in two two-hour sub-sessions on different days. Breaking up the material gives people a chance to process the content and makes scheduling easier for disparate time zones.
Here is the current agenda:
Part 1: Fundamentals
- Introduction
- The fundamental drivers of cycle time: Utilization, Variability, Number of qualified tools
- Little's Law
Part 2: Implications for Metrics + Operating Practices
- WIP-related metrics to drive cycle time improvements
- Cycle time and equipment downtime
- Other operational recommendations: Quick tips on holds, mix, hot lots, dispatching, staffing, and batching
- Conclusion
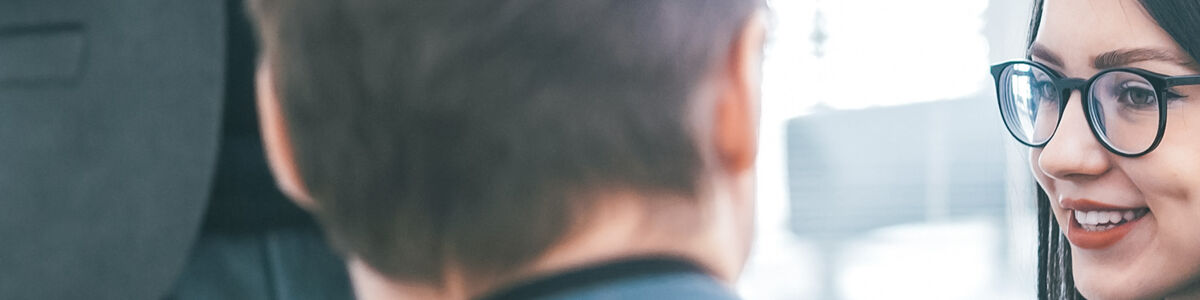
Part 1: Fundamentals
The first part of the course focuses primarily on the three fundamental drivers of cycle time at the tool group level: utilization, variability, and number of qualified tools. We start with definitions, so that everyone is on the same page when they talk about each of these attributes. We encourage discussion and questions, because the most important thing about this course is that participants internalize these core concepts.
Why are the three fundamental drivers important? Because everything else that impacts cycle time in a wafer fab does so because of the impact that it has on one or more of these fundamentals. Downtime, for example, increases cycle time because it takes away standby time, driving up effective tool utilization. Downtime also increases variability and decreases the number of available qualified tools. Lot release affects arrival variability. Hand carry lots cause forced idle time (driving up utilization) and increase arrival variability. And so on.
Why does the class focus on these drivers at the tool group level? Because the delays incurred at the tool / operation level are what accumulate, lot by lot, step by step, driving up total cycle time. And it’s at the tool level where the things we do make a difference, even when we are changing something global in the fab. For example, the scheduler drives which lots get processed in which order on each tool. Equipment technicians do maintenance tool by tool. Process engineers focus on the process time of every step that a lot goes through. We must understand what’s happening at the tool/operation level to make improvements. More specifically, we must understand how the things we do affect utilization, variability and number of qualified tools at that tool level, before we can think about making fab-wide changes.
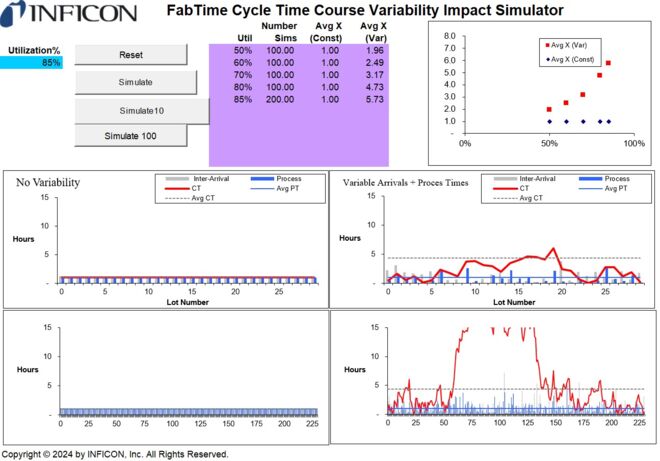
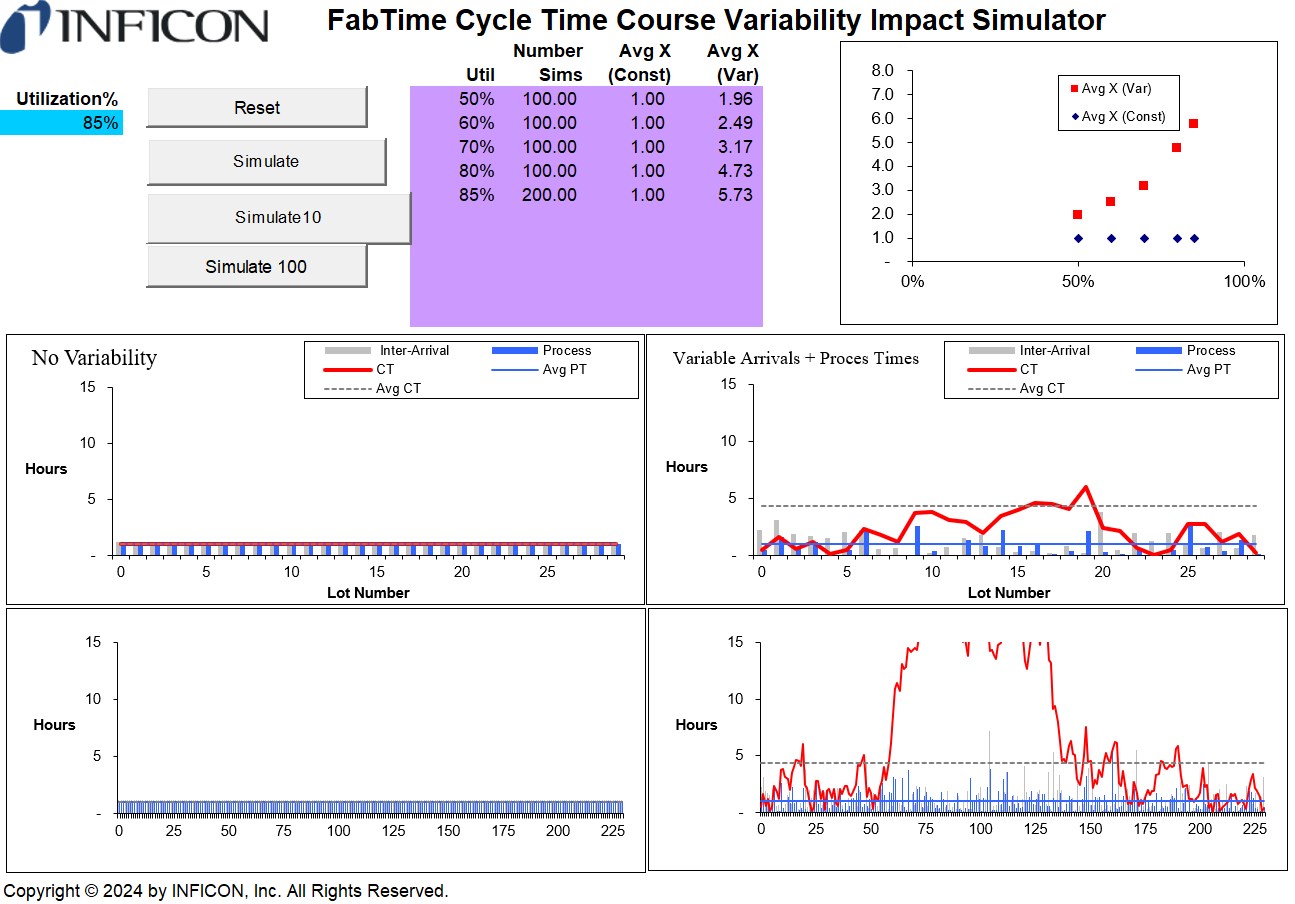
What the course brings in addition to our narrative introduction to the Fundamental Drivers of Fab Cycle Time is: moderated discussions (“What do you think makes cycle time higher than you would like to see in your fab?”; quizzes (“Which of the following choices to you think is a reasonable approximation for the shape of the utilization vs. cycle time curve?"); shared anecdotes by the instructor from prior experience; and three spreadsheet tools:
- Cycle Time / Variability Impact Simulator: This spreadsheet (shown above) uses Excel’s random number generator to explore the relationship between cycle time and utilization, with and without variability. By performing replications at different utilization levels, participants build an operating curve.
- Cycle Time Operating Curve Generator: This spreadsheet uses queueing models to let participants explore the impact of different variables (arrival variation, process time variation, percentage of hot lots, number of qualified tools, etc.) on the shape of the operating curve.
- Course Exercise Spreadsheet: This spreadsheet (one exercise shown below) asks participants to fill in numbers and formulas for examples, as shown to the right. It’s easy to nod your head to say “yes, I understand,” but much better for memory and understanding to have to fill in the right numbers yourself.
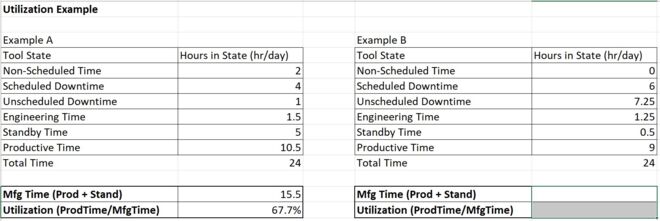
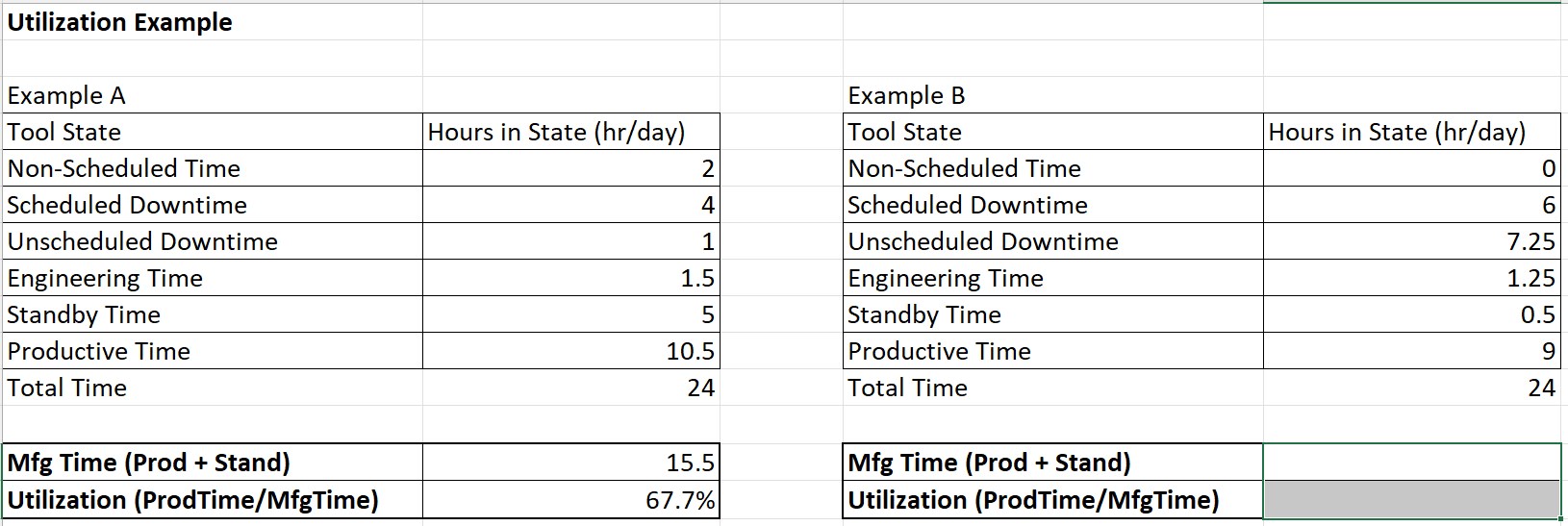
Part 1 closes with one more fundamental of fab behavior: Little’s Law. Little’s Law is about the relationship between cycle time, WIP and start rate (or throughput rate). It applies to all types of factories, not just fabs. The primary implication of Little’s Law in the context of the course is that if the fab start rate remains relatively constant, WIP and cycle time move together, meaning that WIP can be used as a proxy for cycle time in metrics selection (addressed in Part 2).
Part 2: Implications for Metrics and Operating Practices
In Part 2, we move from fundamentals to more tactical/operational recommendations. We start, following on the Little’s Law discussion, by highlighting a few metrics that drive future cycle time improvement. We note that many of the metrics used in fabs day-to-day are more focused on increasing throughput than on decreasing cycle time, and argue to improve cycle time, a fab must also have metrics that focus on cycle time and/or WIP.
We then do a deep dive into the impact of equipment downtime on cycle time. We discuss, using the Operating Curve Generator to look at examples, the impact of downtime on utilization and variability. We offer several recommendations for mitigating the impact of downtime on fab cycle time and suggest cycle time-focused metrics related to downtime.
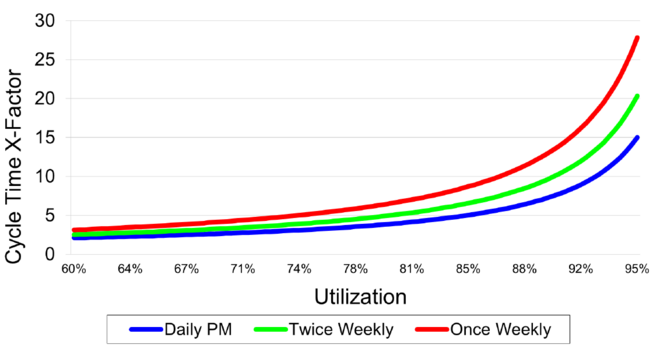
We next take a quick tour through several aspects of the typical fab that drive up cycle time: product mix, holds, hot lots, dispatching, staffing, and batch processing. When this was a two-day class, we delved into each of these topics in considerable detail. In shortening the class for online delivery, however, we pruned this content down to primarily focus on concrete recommendations (with continuing discussion about site-specific habits, and quizzes to build and test intuition). In most cases, we point participants to past newsletter issues, where they can find more details.
We close Part 2 by returning to the three fundamental drivers and highlighting specific recommendations related to each one. For example, in summarizing the impact of utilization, we share several recommendations for reducing forced idle time on tools. This reflects the overall goal of the class: to build people’s intuition about how their actions affect cycle time, and then give them concrete recommendations to implement.
Our Favorite Things When Teaching the Course
Some things that we talk about in the course match the intuitions of most participants (at least to those who have experience in the fab). Losing capacity on the bottleneck because you’re waiting for a hand carry lot is bad for throughput and cycle time. If a future hold is triggered when the engineer who placed the hold is on vacation, there is likely to be extra delay for the lot in question. Long downtimes on one-of-a-kind tools are a problem pretty much everywhere that they occur. The things that are the most fun to teach are the ones that are counter-intuitive for many participants. Chief among these are, in our experience:
- Why it’s (much) better for cycle time to break up PMs instead of grouping them together.
- Why you shouldn’t have a blanket policy requiring you to wait for full batches on furnaces. (The picture to the right shows what happens to the operating curve under a full batch policy.)
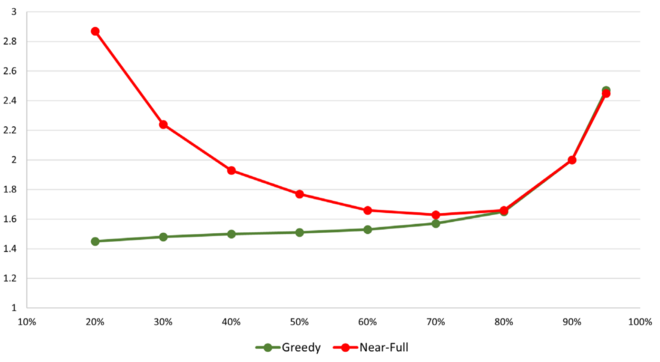
We like it in general when we can broaden someone’s perspective about something important. A key example here would be a manager who expects the manufacturing team to increase utilization and decrease cycle time at the same time. We can use the operating curve to show why these two goals are in conflict in general (shown below), but then show how reducing variability can help resolve the conflict.
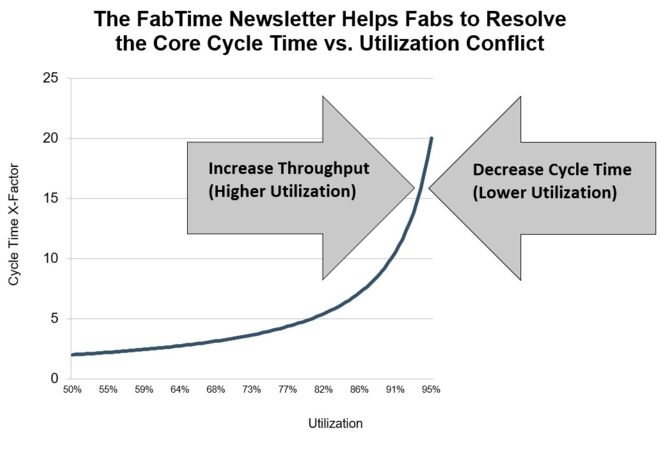
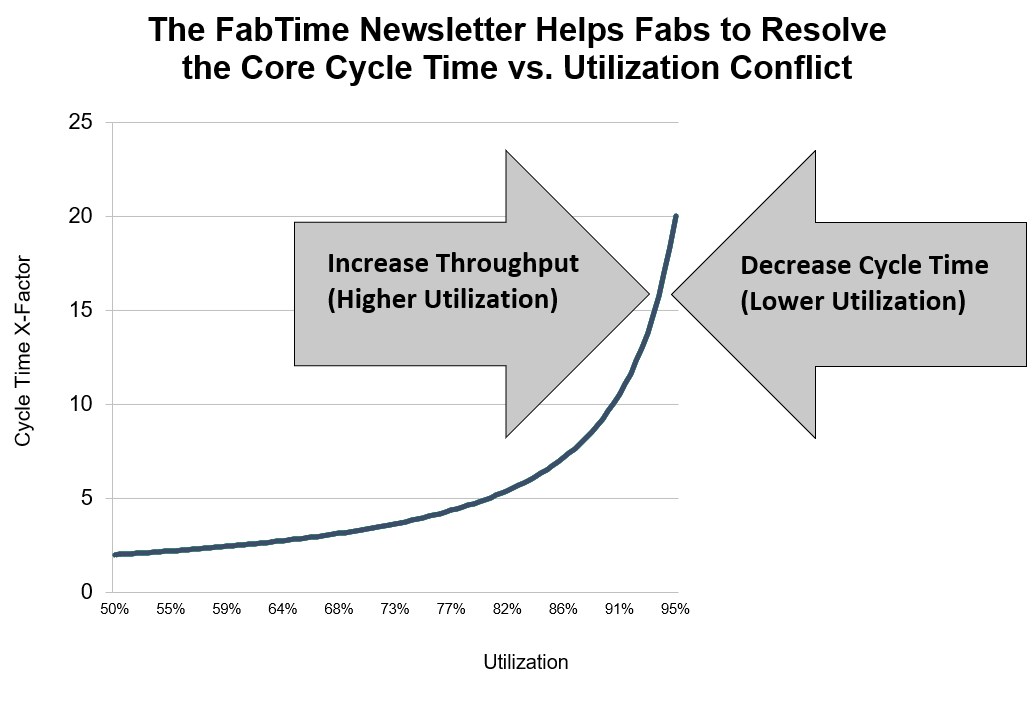
But our favorite part of teaching the course is the discussions with each audience. We always open by asking “What are the causes of cycle time in your fab?” Many of the answers to this question are the same from fab to fab, of course (downtime, product mix, etc.). But every time we do the class, some other quirky response comes up, too. Then later, when we talk about hot lots, we hear different names for hand carry lots. (Pizza lots is a relatively new one that we heard last year. We thought this was meant to evoke the pizza delivery person, rushing to get the lot delivered in time. But it turned out, successful completion of a pizza lot led to pizzas being ordered for the team. Who knew?)
Fabs are such fascinating places. Even after 30 years of working with them, every time we sit down with a different team (even if it’s a different team from the same company we did a class for last month), we learn something new. And we try to integrate the new knowledge into the class material, so that it can grow, too.
Conclusions
Fabs are complex environments. There are strong financial reasons for improving fab cycle time, but doing so isn’t easy. One can theoretically improve cycle time by throwing money at the problem, by adding tools, hiring more people, paying for service contracts, etc. But this isn’t always practical. And even where there is some money to spend to improve cycle time, we want to make sure to use that money wisely, spending where the improvement will be greatest.
The good news is that a lot can be done to improve fab cycle time without spending large amounts of money, by focusing on the fundamentals. Focusing on availability and avoiding forced idle time improves utilization. Making operational decisions to reduce arrival and process time variability flattens the operating curve and improves cycle time. Having a dedicated focus on path importance throughout the fab drives step by step cycle time improvements.
People don’t always know instinctively what changes to make to improve cycle time. They need training to build their intuition about the fundamentals of factory behavior (such as the shape of the operating curve, shown below). Because fabs are so complicated, this training needs to be tailored to a fab-specific audience. (Time constraints between process steps are not a thing in other types of manufacturing. Nor is reentrant flow.)
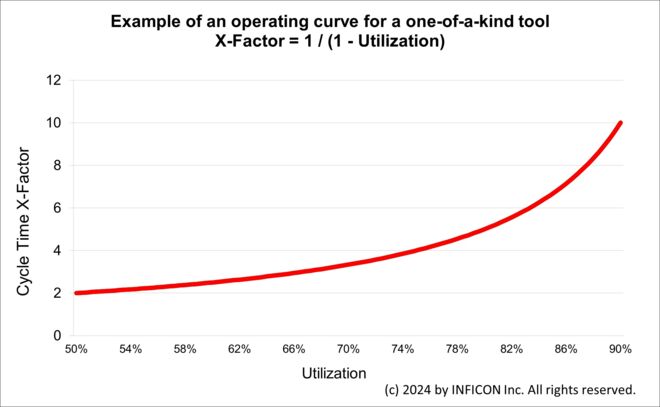
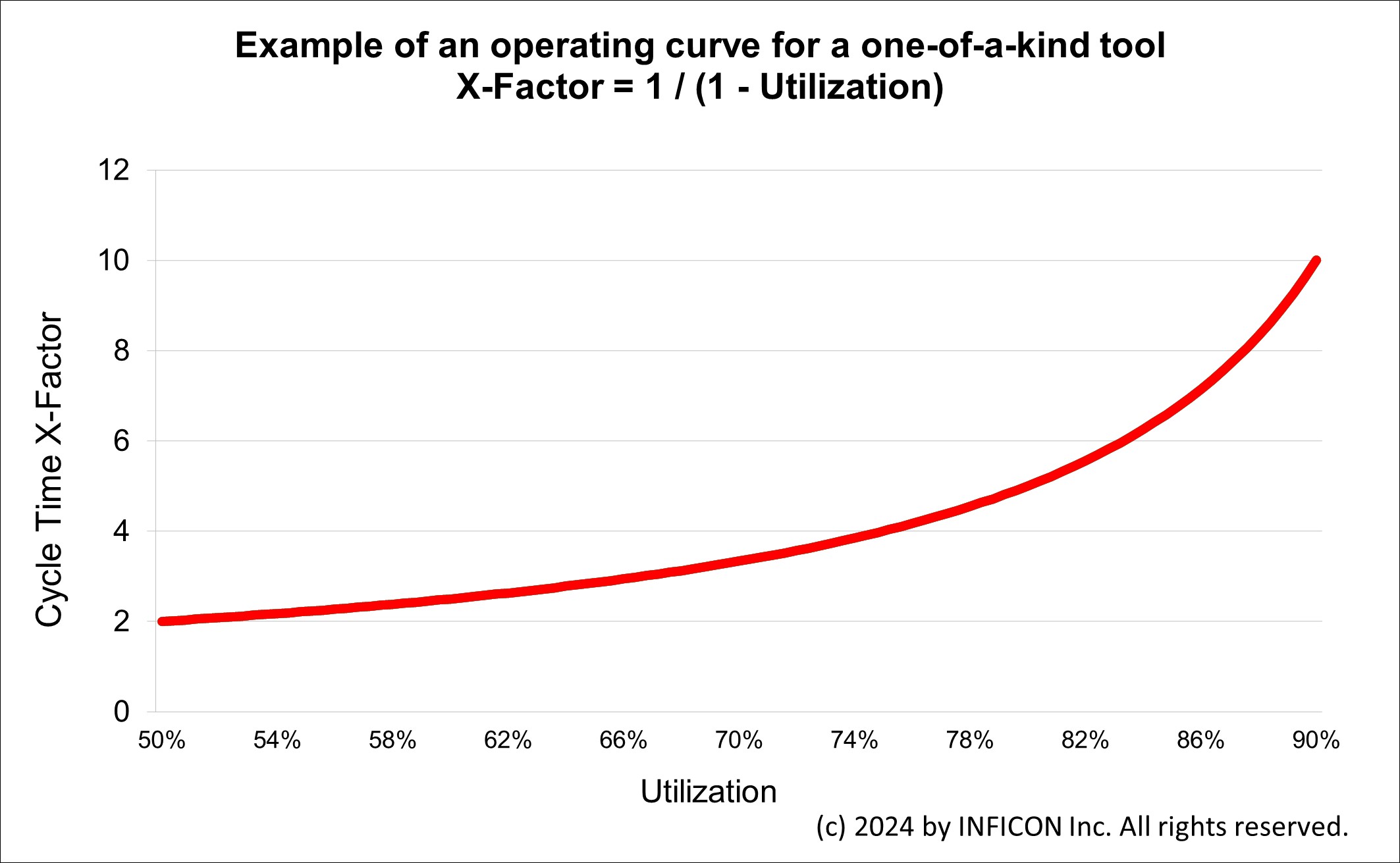
Ideally, the training should also be paired with efforts to increase data availability. Because that’s the next step. Once you build people’s intuition about what to do, you need to give them data to know where to start. We’ll talk more about that in future articles.
We’ll conclude here by noting, again, that if things are a bit slower at your fab right now than they have been for the past few years, this is a good time to think about training your team. Then they’ll be ready to hold variability down and stay laser-focused on utilization and process restrictions, during the next upturn. We would be more than happy to help!
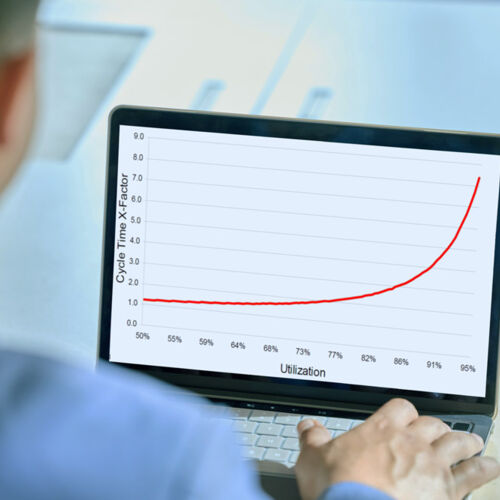