后端处理故障检测
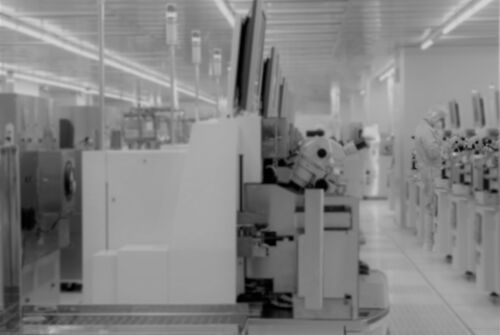
在FDC解决方案在前端晶圆加工领域取得成功后,多家半导体制造商选择在其后端晶圆组装工艺中应用FDC。对这些制造商而言,将FDC应用于后端研磨、切割和引线键合等单元操作是重中之重。
在半导体生产流程的后期应用FDC甚至比在流程的早期应用更为重要。每个完成的工艺都会增加晶圆的价值;当晶圆到达后端处理时,其价值已经很高,而故障的成本更高。半导体制造商在模拟领域还有额外的好处。模拟组装成本占总生产成本的35%。相比之下,逻辑组装仅占总生产成本的15%[1]。
数据收集方法
有多种数据收集方法可用于各种后端处理设备,包括:
- SECS GEM和EDA通信
- 文件导入
- 模拟
- 可编程逻辑控制器
许多现代后端研磨机、切割机、线焊机都支持SECS通信标准,这是首选的数据收集方法。当工具不支持SECS通信时,或者记录的数据比通过SECS通信获得的数据具有更高的保真度时,则使用其他方法。
回磨示例
后端加工的第一步是将晶圆背面研磨至所需厚度。FabGuard FDC在行业标准波兰研磨机上使用1Hz的SECS通信。这款特殊研磨机的挑战在于工具内不同加工单元的数量。为两个研磨站、一个抛光站、一个旋转站、一个UV站、一个OCR站以及工具级设施管理配置了主动数据收集。
FDC的实施重点是监控以下磨削站参数:主轴扭矩、砂轮转速、卡盘转速和冷却水供应。与前端工艺监控一样,后端工艺监控取决于工具利用率和产品组合。检测工艺故障的方法需要考虑这些操作条件的变化。
切块示例
晶圆磨削到所需厚度后,沿着切缝线切割成单个芯片,为线键合和封装做准备。FabGuard FDC在行业标准刀片和激光切割工具上以1Hz的频率使用SECS通信。对于使用刀片切割的切割机,监测以下参数:转速、刀片电流和冷却水流。
实际切割时间可能不到10秒。1Hz的典型SECS通信速率可能不足以检测所有切割故障。如果需要,外部传感器可以更快地收集数据,从而汇总每个切口的数据。
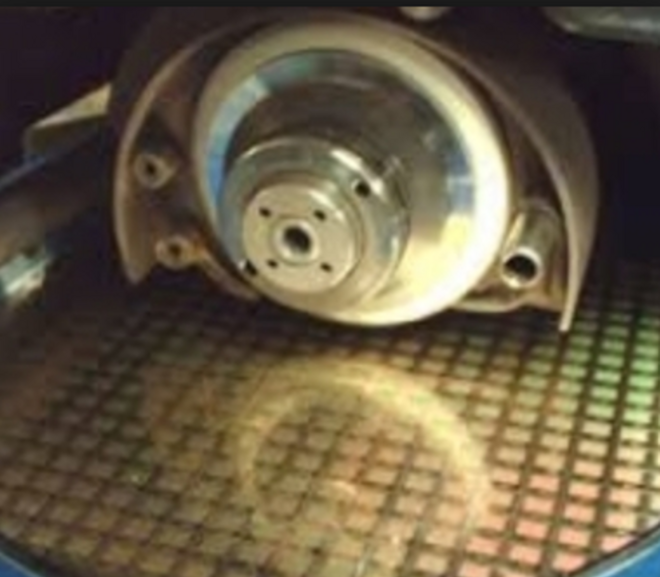
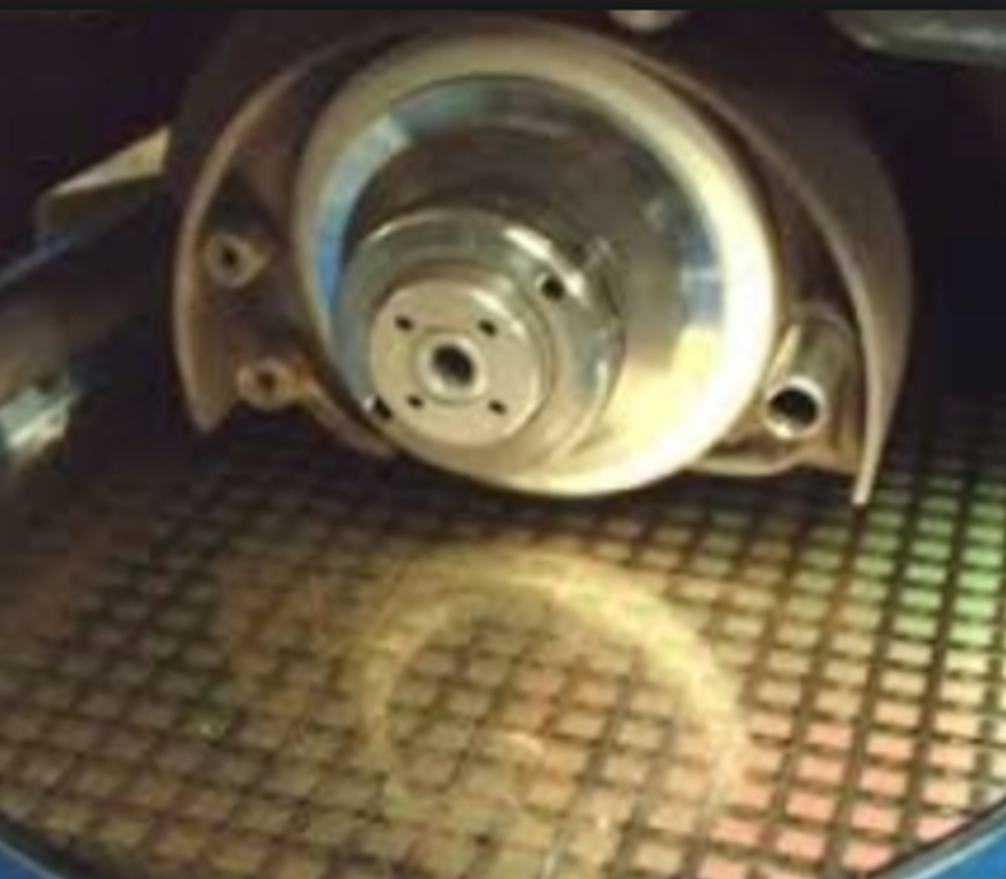
线键合示例
在行业标准线焊机上成功部署 FabGuard FDC 需要使用文件导入器。每个焊点的焊接过程相对较快,从不到一秒到大约两秒不等。对于大多数工具而言,使用低于 1 Hz 的 SECS 通信来收集这些数据非常困难。
大多数工具供应商会在每个晶圆工艺结束时提供一个数据文件,其中包含每个键合点的时间序列数据。由于这种文件格式在键合机制造商之间是标准化的,因此使用这种数据收集方法配置FDC是快速而直接的。通常监测的参数是元件温度和覆盖(偏离目标)。
总结
FabGuard FDC已成功应用于背面研磨、切粒和线键合后端加工工具。当晶圆处于最高价值时,后端FDC为制造过程提供额外的保护。