晶圆厂的瓦丁顿效应
探讨定期维护有时会导致计划外停机时间短期增加的情况。
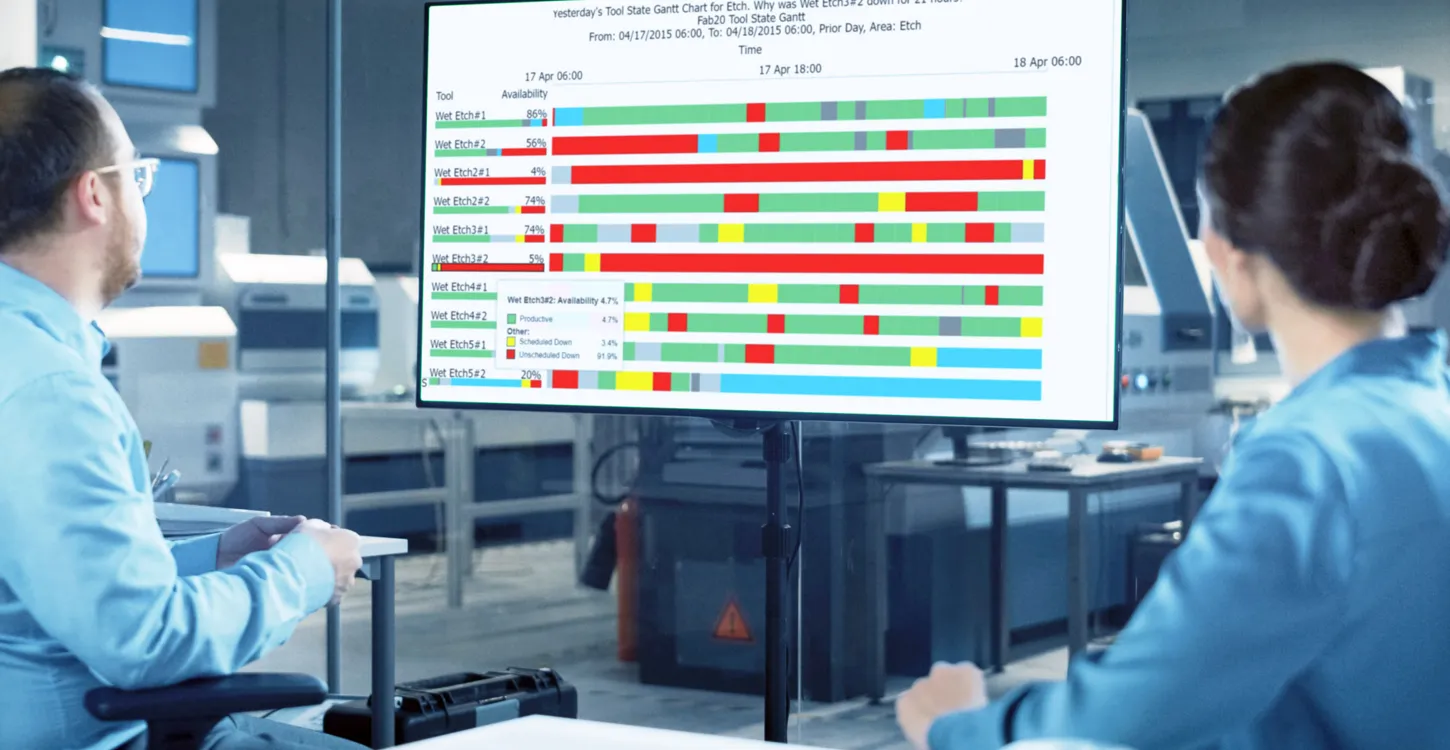
作者:詹妮弗-罗宾逊
正如我们一直推荐的 减轻停机对工厂周期时间影响的指标,我们一直在思考瓦丁顿效应(The Waddington Effect)的影响。由作者 James P. Ignizio 命名和推广的 “瓦丁顿效应 ”是基于二战时期对英国皇家空军 B-24 型解放者轰炸机的维护研究。研究人员 C. H. 瓦丁顿和他的团队发现,这些飞机的定期维护如果过于频繁,可能会 “扰乱相对令人满意的状态,从而造成积极的损害”。具体地说,Waddington 发现,计划外停机事件在定期维护后不但没有减少,反而有所增加。(有关概述,请参阅 Mike Busch 在《运动航空》杂志上发表的文章)。
这一结果似乎与本通讯(见第 22.01 期等)和我们的周期时间课程中关于避免将维护事件分组的建议有潜在冲突。我们提出这一观点的依据是,较长的不可用时间比较短的不可用时间更不利于周期时间。在其他条件相同的情况下,这当然是对的。但是,如果更频繁的计划内维护事件会导致随后更长的计划外停机事件,那么整体周期时间可能会更长。
在本文中,我们将介绍瓦丁顿效应以及瓦丁顿效应图。然后,我们将提出一个解决方案,以解决我们建议增加维护次数与瓦丁顿隐含的减少维护次数之间的明显冲突。我们一如既往地欢迎您的反馈。
什么是瓦丁顿效应?
詹姆斯-伊格尼齐奥(James Ignizio)在 PHALANX 杂志 2010 年 9 月刊 (C. H. 瓦丁顿是一名遗传学家,二战期间被派往英国军事行动研究小组工作。作战研究小组被要求通过减少飞机在两次飞行之间的地面停留时间来提高英国轰炸机指挥部的效率。
伊格尼西奥报告说
“瓦丁顿和他的团队大胆地停下来思考,然后才匆匆忙忙地就一个可能有效也可能无效的计划进行华而不实的介绍。他们要求并分析了辅助数据,与维修人员进行了交谈,并花时间仔细和亲自观察了实际的维修活动。
Ignizio 将他们的发现称为 “沃丁顿效应”。他们绘制了计划外停机事件的数量以及最近一次计划内维护事件发生后的时间。他们的图表显示,在计划维护事件发生后不久,所需的维修次数就会增加,并随着时间的推移逐渐减少,直到大约下次计划维护事件发生时为止。
Waddington 的结论是(正如 Ignizio 所引用的那样):"检查往往会导致维修次数的增加:
“检查往往会增加故障,而这只能是因为检查扰乱了相对令人满意的状态,造成了积极的损害。其次,没有任何迹象表明,在飞机飞行 40-50 小时后,即飞机即将进行下一次[预防性维护]时,故障率又开始上升"。
换句话说,伊格尼西奥说:
“瓦丁顿效应的定义是,计划外事件的数量和频率'紧随'计划外事件之后出现'峰值'--随后计划外事件的发生率逐渐下降到'更正常的水平',直到下一次计划外维护事件之后再次出现同样的麻烦效应"。
为此,Waddington 团队提出的解决方案是改进维护活动的执行和时间安排,包括增加更好的文档记录。这些改进的结果是,在不增加设备和人员的情况下,英国海岸司令部机队的有效规模增加了 60%。工业工程所取得的成就难道不令人惊叹吗?
还有一点值得注意的是,瓦丁顿效应可被视为许多机械设备中观察到的浴缸形故障率曲线中故障率下降(DFR)部分的一部分。由于初始缺陷导致故障率下降的初期是故障率(CFR)相对恒定的时期。随后,随着系统的老化和开始磨损,故障率(IFR)会进入上升期。(详见 Hopp 和 Spearman 的《工厂物理学》(Irwin,1996 年))。在晶圆厂中,IFR 的后果很严重,因此最好在故障率上升期之前进行 PM。
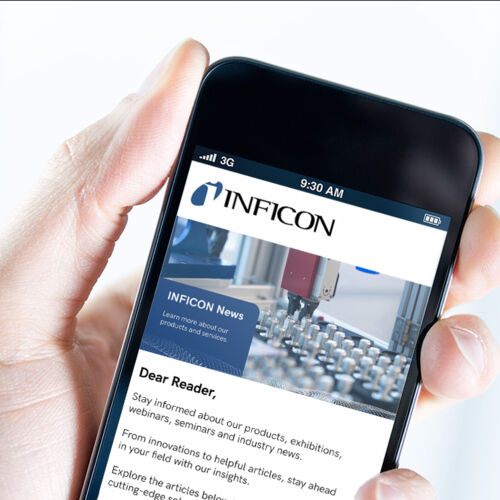
什么是瓦丁顿效应地块?
在 Ignizio 的《优化工厂绩效》(McGraw Hill,2009 年)一书中,他建议使用瓦丁顿效应图来分析和减少工厂的设备停机时间。瓦丁顿效应图是一种类似于瓦丁顿和他的团队所使用的图表,用于识别预防性维护事件(PM)之后计划外停机时间增加的情况。
Ignizio 说,要为工具绘制 Waddington 效果图,需要绘制一个条形图,X 轴上标注每个小时,条形图的高度表示该小时内的停机时间,用颜色表示计划内或计划外停机时间。Ignizio 在书中展示了一个基于实际工厂数据的例子,该工具需要每 40 小时进行一次 5 小时(平均)的 PM。该示例显示,在 PM 结束后不久就会出现大量计划外停机,然后在接下来的 12 小时内逐渐减少。
下面是一个在 Excel 中创建的类似示例。第一个长时间 PM(黄色显示)持续 3.8 小时,随后不久出现 2.7 小时的计划外停机时间。随后是更多的停机时间,然后逐渐缩短。第二个长时间 PM 持续 4.5 小时,随后同样是一段更长的计划外停机时间,然后逐渐缩短。
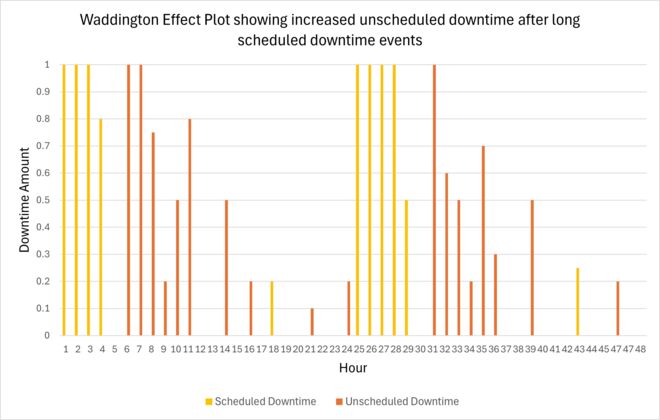
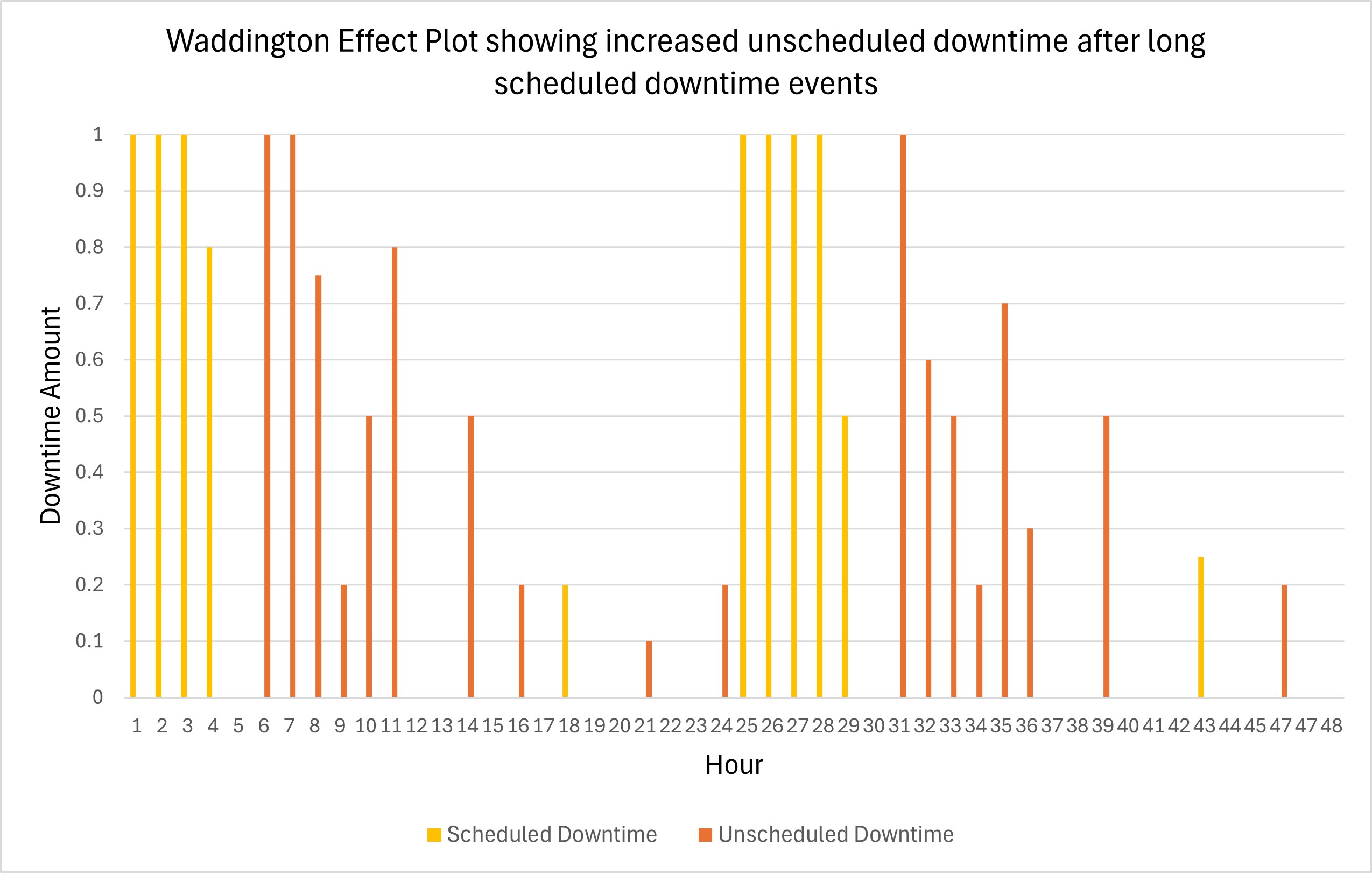
在这个虚构的例子中,只看图表就可以直接推断出可能存在瓦丁顿效应。当然,如果我们要在实践中使用这些图表,我们需要:a) 一种能够持续轻松生成这些图表的方法;b) 一种能够从数据中自动检测出瓦丁顿效应的方法;c) 如果我们确实检测出了瓦丁顿效应,下一步该怎么做的建议。让我们依次来看看这些方面。
如何使用 FabTime 绘制瓦丁顿效应图
虽然我们没有直接将瓦丁顿效应地块列入FabTime 报告模块 我们确实有工具状态甘特图,如果过滤后只包括计划内和计划外停机时间,也能传达类似的信息。下图显示了五天内两个工具的计划内和计划外停机模式。此示例来自我们的演示服务器,确实显示了每个工具在计划内停机后立即发生的大量计划外停机。我们看到这个图表后可能会得出结论:计划内停机时间影响了计划外停机时间(尽管在实际操作中,我们希望看到更多的数据和更长的时间)。
FabTime 软件用户可以轻松创建类似的视图,方法是过滤工具状态甘特图,使其包括感兴趣的工具(使用 “工具”、“工具组 ”或 “区域 ”过滤器),选择感兴趣的时间窗口,并在 “E10St ”过滤器中输入 “Sched, Unsch”。然后,他们就可以将图表添加到主页选项卡中进行保存。
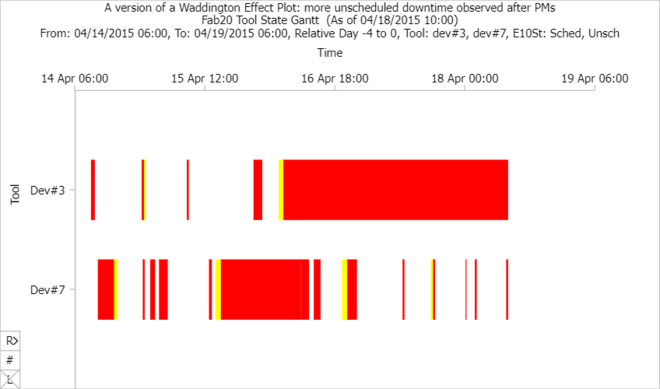
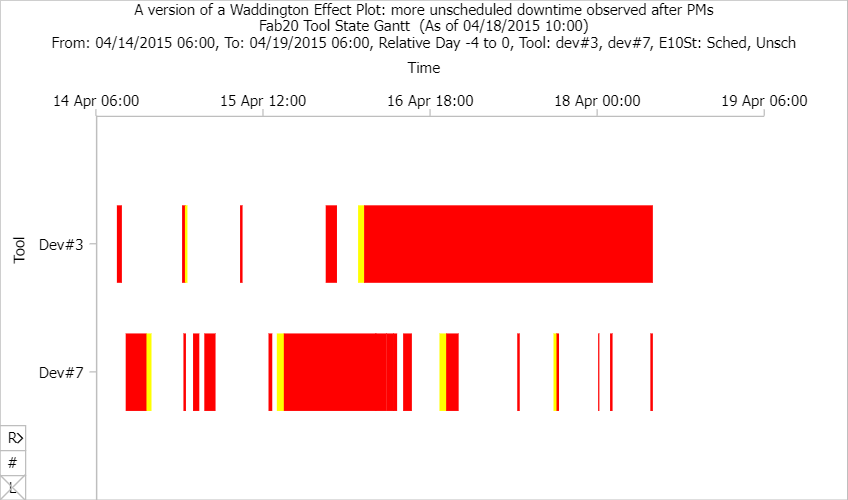
如何持续检测瓦丁顿效应?
Ignizio 建议使用目测或 “自动模式识别分析 ”来识别是否存在瓦丁顿效应。使用 FabTime 中的工具状态甘特图创建瓦丁顿效应图的下一步,是以某种方式自动检测瓦丁顿效应,而不是依赖某人目测特定工具的瓦丁顿效应。
要做到这一点,一种方法是记录计划内停机事件发生后在规定时间窗口内发生的计划外停机时间的百分比,并将其与工具上计划外停机时间的总百分比进行比较。但我们应该使用什么时间窗口呢?是对每个 PM 都这样做,还是只对超过一定时间的 PM 才这样做?
幸运的是,INFICON 拥有一个全新的数据科学团队,其成员能够仔细思考这些问题,并推荐实施的解决方案。如果任何用户已经考虑和/或实施了瓦丁顿效应检测,并愿意分享您的想法,请将其发送给 Jennifer Robinson。我们将在以后的期刊中跟进这一话题。
那么,“瓦丁顿效应 ”是否与本通讯之前提出的周期时间改进建议相冲突呢?
在继续讨论检测到瓦丁顿效应时该怎么办之前,让我们先回到瓦丁顿的结果是否与本期通讯中关于分开维护事件的建议相冲突的问题上来。
瓦丁顿效应表明,在某些情况下,如果系统运行平稳,进行 PM 维护可能会干扰系统并导致问题。 如果出现这种效应,就可以支持对 PM 进行分组的想法。 如果每次 PM 都会增加大量计划外停机时间的发生几率,那么我们最好减少 PM 的次数。
不过,我们也从周期时间运行曲线中了解到,较长的不可用时间通常比较短的不可用时间对周期时间的影响要大得多。 例如,下图描述了在总可用时间相同的情况下,较短、较频繁的 PM(蓝色图)与较长、较不频繁的 PM(绿色和红色图)的影响。 较长的 PM 对周期时间的影响要大得多,每周 PM 的每次访问周期时间几乎是每日 PM(七分之一)的两倍。
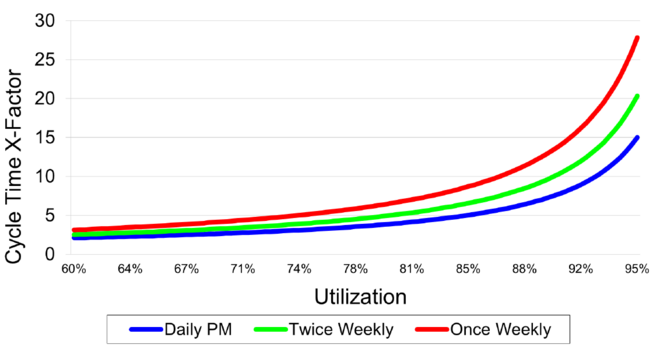
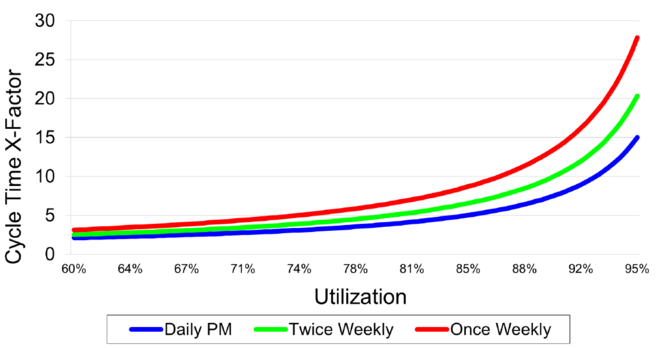
因此,我们要重复一个问题,我们在 循环时间历程.对于相同数量的定期维护,您是否应该对 PM 进行分组?
我们认为这个问题的答案一般还是否定的。 不过,我们建议增加一项定期检查,以了解您的工厂是否出现了瓦丁顿效应。 对于没有观察到瓦丁顿效应的工具组,我们可以坚持之前的建议,不对 PM 进行分组。 (在特殊情况下可能会有例外,比如没有 WIP 在等待工具,工厂对工程师的限制很严格,或者额外的资格认证非常昂贵)。
当你观察到潜在的瓦丁顿效应时,答案不应该是尽量少做项目管理。 这就好比听到汽车发动机发出 "哐当哐当 "的响声,却决定把收音机音量调到最小。 瓦丁顿效应意味着您的维护方法出了问题。 因此,答案应该是找出导致该工具组出现瓦丁顿效应的原因,并加以消除。
如果我们发现了沃丁顿效应,应该怎么做?
回到《PHALANX》杂志的文章,Ignizio 重点强调要找出瓦丁顿效应背后的原因,然后针对不必要的复杂性和过多的可变性消除或减少这种效应。 他指出,清晰地记录维护规范尤为重要。
根据这一建议,我们向工厂提出以下建议。 在检测到瓦丁顿效应时,我们应该
- 分析现有数据,找出产生该效应的根本原因。
- 消除这些根本原因,重点是减少变异性。
- 从中吸取经验教训,并与团队沟通如何在未来避免出现问题。
举例来说,我们曾采访过一位工程师,他在一家工厂工作,在对某一特定集群工具进行重大项目管理(长达 40 小时)后,发现了瓦丁顿效应。 尽管该工厂做了大量努力来找出造成这种效应的根本原因,但仍难以消除这一问题。 最终,他们从后来的工艺流程中放弃了这一工具。 然而,在其他情况下,他们能够通过注重质量和可重复性来减少发生瓦丁顿效应的机会。
该研究普遍发现,较短的项目管理时间 "走偏 "的风险较小,因此,较短、较频繁的项目管理时间与较长的项目管理时间相比,受瓦丁顿效应的影响较小。 当然,这与我们的总体建议是一致的,即寻求较短的不可用时间。
或许值得注意的是,长期以来一直提倡 "瓦丁顿效应 "的伊格尼西奥也主张在工厂中 "分散 "项目管理人员,以减少他们对周期时间的影响。
结论
二战期间,C. H. 瓦丁顿和他的运筹小组致力于提高英国飞机的设备可靠性。 研究小组发现,在某些情况下,当一台设备性能良好时,介入进行预防性维护可能会增加此后不久发生计划外停机的可能性。 詹姆斯-伊格尼齐奥教授后来将这种行为称为 "瓦丁顿效应",并提出使用 "瓦丁顿效应图 "来检测现代工厂中的这种行为。 伊格尼西奥主张通过找出根本原因、降低复杂性和可变性以及改进文档来消除瓦丁顿效应。
在阅读了有关 "瓦丁顿效应 "的文章后,我们起初担心这可能会与我们在本期通讯中反复提出的建议相冲突,即执行更短、更频繁的维护活动,而不是将它们分组。 但经过进一步思考,我们得出的结论是,晶圆厂应防止出现瓦丁顿效应,并在观察到瓦丁顿效应的地方消除它,同时继续努力缩短不可用时间。
在本文中,我们展示了如何使用 FabTime 报告模块生成瓦丁顿效应图。 我们还开始讨论自动识别瓦丁顿效应的方法。 我们还简要讨论了在发现瓦丁顿效应时如何减轻其影响的建议。 我们期待着在未来分享更多成果,同时也欢迎您提供反馈意见。