现代自动驾驶汽车电子设备和传感器的泄漏测试任务
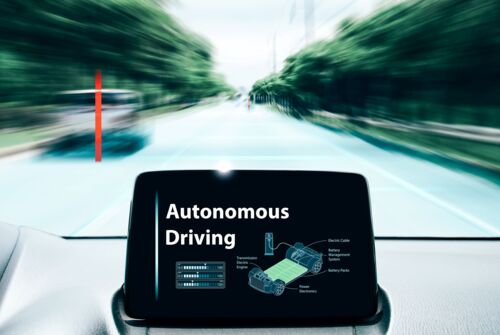
如果车辆需要自动或半自动 行驶,就必须配备各种传感器和电子元件,即高级驾驶辅助系统(ADAS)。
为了确保乘客和其他道路使用者的安全,ADAS组件必须在车辆的使用寿命内可靠运行。然而,水是所有电子设备和传感器的天敌。因此,不仅需要防止液态水进入,还要防止大气中的湿气进入。因此,许多ADAS传感器不仅必须防水,而且必须气密。制造商使用灵敏且可靠的现代测试气体方法来确保这一点。
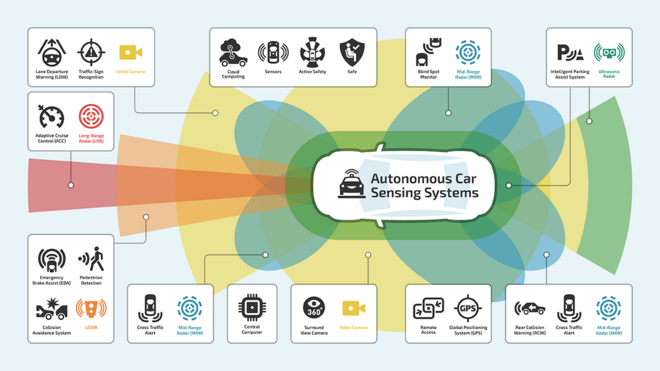
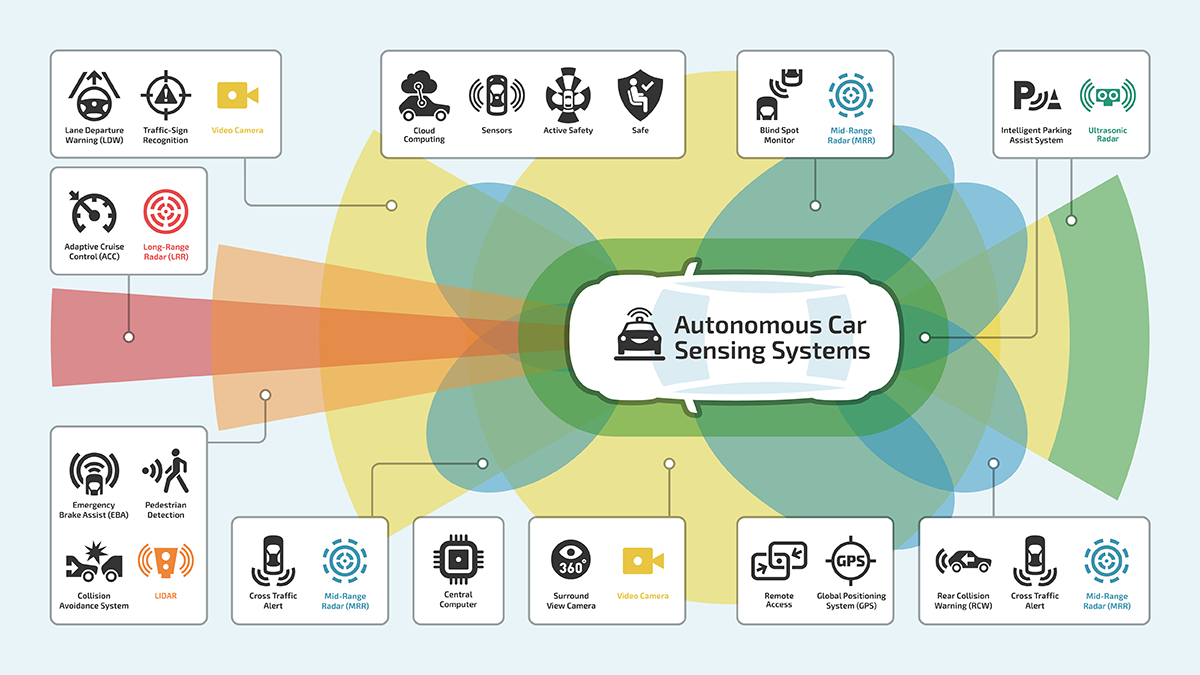
零缺陷战略,而非六西格玛
在消费类电子设备中,对半导体技术的坚固性和密封性的要求自然远低于对车辆安全关键部件的要求。在消费类电子设备中,需要在0至40摄氏度的温度范围内运行,而车辆电子设备通常需要在-40至150摄氏度的温度范围内可靠运行。从ADAS传感器技术来看,与消费类电子设备相比,对ADAS传感器技术的要求更为严格。
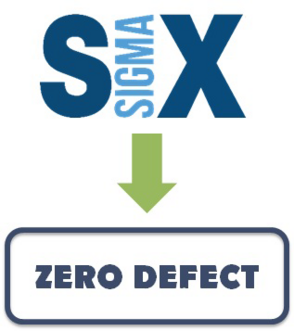
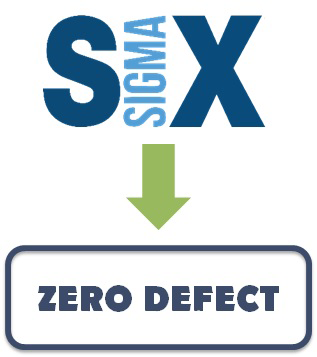
如果采用六西格玛方法,那么在一百万个零件中允许有3.4个缺陷,这是不可想象的。相反,ADAS组件制造商追求零缺陷战略——在十亿个零件中允许有一个缺陷——以确保车辆在密集的城市交通和高速公路上安全运行。
外壳材料作为密封因素
车辆中所有电气和电子元件的天敌是水。保护电子元件外壳免受水侵对于避免短路风险至关重要。ADAS传感器通常必须符合IP67甚至IP69K防护等级。
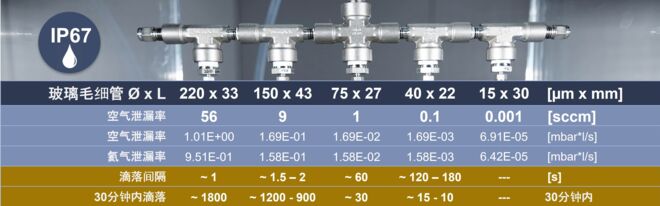
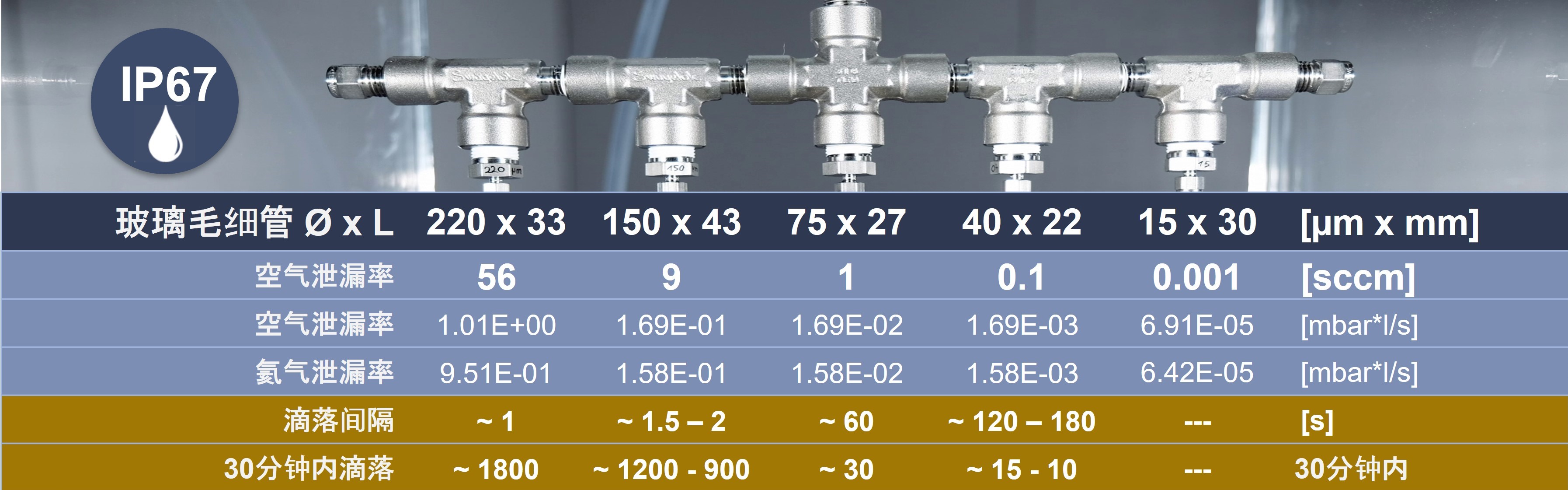
外壳材料和待测泄漏率之间存在密切关联。有趣的是,塑料或钢制外壳的要求比铝制外壳的要求低 (参见防护等级IP67)。这是因为水通过一定长度和直径的泄漏通道渗入外壳的难易程度,对水滴从外壳材料上脱离的难易程度有决定性影响。
例如,铝比塑料材料更严格,因为水更容易从铝上脱落。为确保塑料外壳不会进水,可使用简单的累积法测试其氦气泄漏率,要求泄漏率不超过10-3 mbar∙l/s。首先,将外壳充满测试气体,然后放置在简单的累积室中。接着,用检漏仪测量在指定时间内从外壳泄漏到累积室的测试气体量,并根据测量结果确定泄漏率。
铝制外壳的真空测试
如果外壳不是由塑料或钢材制成,而是由铝制成,则需要对泄漏率小于100倍的泄漏进行测试。对于泄漏率10-5 mbar∙l/s的泄漏测试,真空室中的氦气测试是唯一的选择。铝制外壳充满氦气,然后放置在一个抽空空气的腔室中。真空泄漏探测器甚至可以检测到泄漏到真空中的最小量的氦气。然而,有时无法将外壳充满氦气,例如外壳已经密封。在这种情况下,可以使用所谓的轰炸法。在轰炸法中,首先将测试部件暴露在氦气环境中,以便测试气体能够通过任何泄漏点渗入外壳内部。然后才能将测试部件放入真空室,并按照上述方法检测逸出的氦气。
带Gore-Tex®薄膜的控制模块
在某些制造工艺中,已经考虑到了后续泄漏测试的需要——在最终密封前,立即向外壳中注入1%的氦气,从而避免爆炸。然后,可以通过真空泄漏测试再次检测泄漏。
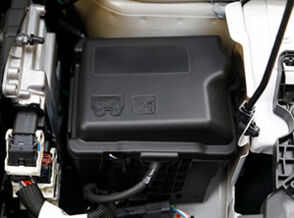
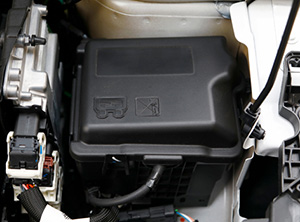
然而,还有一种方法可以将测试气体注入零件内部。控制模块通常配备半透膜戈尔特斯(Gore-Tex)膜,以补偿与温度相关的气压差异,防止壳体内部与外界之间出现压力差。在泄漏测试中,这种外壳通过其膜进行呼吸,从而利用氦气对其进行加压。然后可以在累积室或真空室中检测逸出的测试气体。在真空室中进行测试的优势在于测试速度更快、周期更短,而在简单的累积室中进行测试所需的投资更少,但测试周期通常更长。
ADAS传感器必须气密
许多ADAS传感器不仅必须防水,而且必须气密。不气密的部件始终存在风险,即渗透的湿气会随着温度变化而凝结,从而损害其绝对和永久的功能可靠性。对于激光雷达(LIDAR,即光探测和测距)和摄像头光学元件而言,潮湿导致的雾化是一个类似的问题。为了验证对安全至关重要的激光雷达和摄像头组件的气密性,并排除任何大气湿气的进入,需要进行针对10-6至10-7毫巴·升/秒范围内极小极限泄漏率的泄漏测试。这些极小的泄漏率只能通过氦气真空测试来检测。同样严格的密封性要求也适用于带有电气馈通的传感器外壳的气体密封。
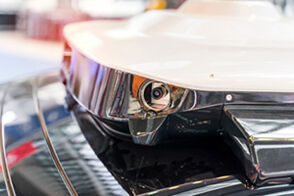
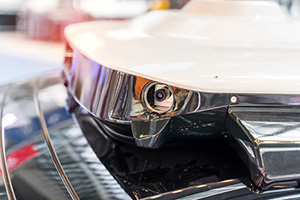
没有泄漏测试就没有自动驾驶
ADAS组件制造商的目标是使每十亿个零件的故障率低于1例,这看似雄心勃勃,但却是必不可少的。所有安全关键系统的功能必须得到长期保证。在生产过程中对这些组件进行密集、可靠的密封性泄漏检查,排除哪怕是最微小的泄漏,都能降低水分进入的风险。在ADAS自动 性更高的级别上,运行过程中传感器失灵是不可想象的。没有泄漏测试,就没有自动驾驶。因此,重要的是要记住,成功的泄漏测试计划将带来安全、可靠的自动驾驶。
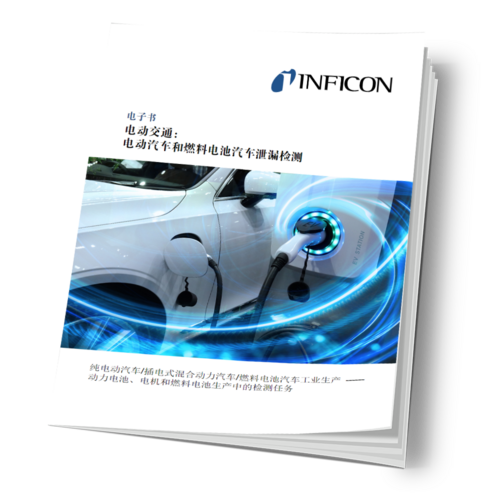