了解泄漏测试过程中的工作内容
锂离子电池电解液直接泄漏测试的五个重要事实.
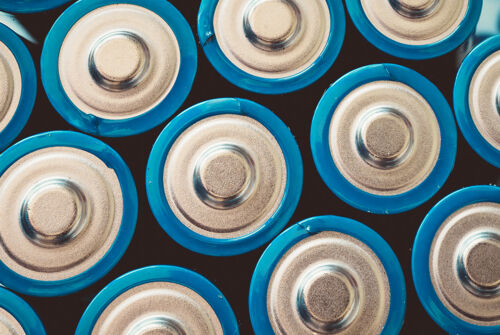
过去,不可能对已经注入电解液或甚至已经完成化成过程的锂离子和钠离子电池进行泄漏测试。INFICON 获得专利的直接电解液泄漏测试方法改变了这一切。我们的独立式 ELT3000 PLUS 和在线式 ELT Vmax 都采用了这种突破性的测试方法,以检测电解液是否从个位数微米范围内的微小泄漏泄漏到真空测试室中。然而,有一些常见的误解会妨碍对电池芯进行准确的泄漏测试。以下五个事实将帮助您在泄漏测试过程中确保工艺的可靠性。
1. 为什么氦气和电解液泄漏率永远无法精确换算
氦气可能是真空检漏中最著名的微量气体。它是一个既定的标准。因此,电池的电解液泄漏率通常以氦气当量泄漏率的形式进行校准。然而,液体的泄漏率在很大程度上取决于相应液体的特性。由于通常无法精确了解这些特性,ELT 系列的所有设备,即 ELT3000 PLUS 和 ELT Vmax, 在 100% 碳酸二甲酯 (DMC) 和大气填充压力下都显示标准化的氦气当量泄漏率。
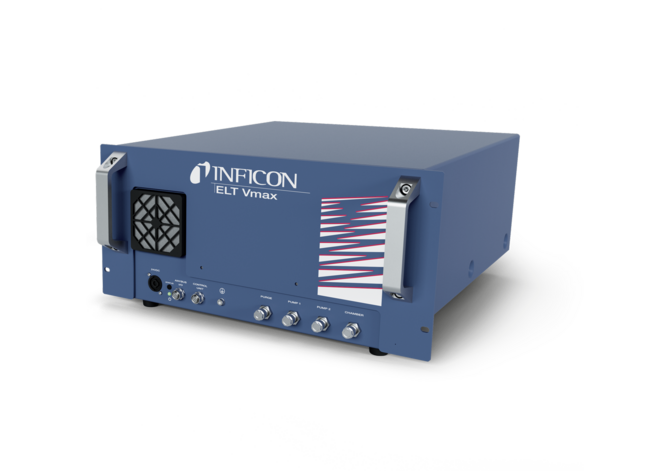
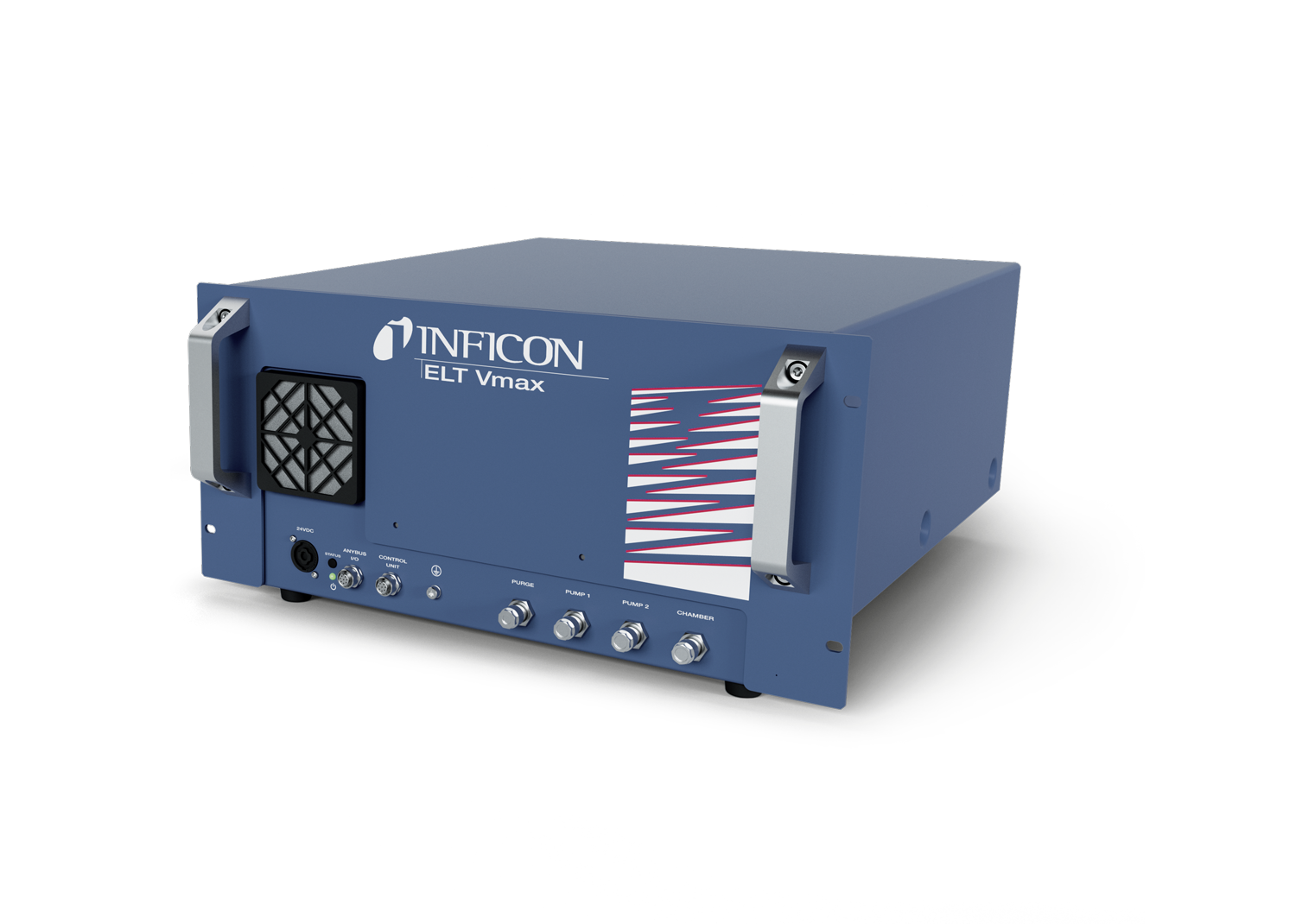
这就意味着,以 E-Check 漏液测试为例,只有在常压下用纯 DMC 填充电芯时,才能通过校准获得精确的氦气等效漏率。. 然而,真实的电芯内部只有一定比例的 DMC,而且通常还有一定的欠压。
即使经过仔细校准,两种泄漏率的具体差别有多大取决于许多因素。两个使用简化模型计算的例子说明了实际中的差异有多大。在确定合适的剔除泄漏率时,必须牢记这一点。
案例研究 A:圆柱形电芯 | |
---|---|
充气压力 | 750 mbar |
电解液 | 基于 DMC (50 % DMC/50 % EC, 1.0 M LiPF6) |
现有泄漏的真空氦气泄漏率为: | 10-5 mbar∙l/s |
电解液泄漏率由 ELT 系列校准检漏仪显示: | 5∙10-7 mbar∙l/s |
案例研究 B: 软包电芯 | |
---|---|
充气压力 | 250 mbar |
电解液 | 基于 EMC 的电解质 (100 % EMC, 1.0 M LiPF6) |
现有泄漏的真空氦气泄漏率为: | 10-5 mbar∙l/s |
电解液泄漏率由 ELT 系列校准检漏仪显示: | 10-6 mbar∙l/s |
2. 泄漏率为零不是合理的质量要求
物理学的一个基本事实是,泄漏率永远不可能真正为零。即使泄漏率可以为零,也无法测量。因此,将泄漏率限制为零是毫无意义的。相反,重要的是在确定剔除泄漏率时,不能再出现对电池有害的错误模式。
电芯泄漏造成的严重后果
- 液态电解液流失,导致相应的容量损失
- 湿气渗入,与电解液反应形成腐蚀性氢氟酸--导致更大的泄漏和更多的容量损失
- 软包失去机械完整性
必须尽一切可能防止电芯与大气之间的液体和气体交换。下文第 3 节讨论了有助于防止这种情况发生的泄漏率具体要求。
3. 液体可有效堵塞泄漏通道
并非电芯的每一次泄漏都会造成严重后果。在生产过程中,电芯会被注入液体。对于气体泄漏,泄漏直径与泄漏率之间存在直接的相关性,但对于液体泄漏,情况并非如此(至少在泄漏通道直径的大范围内并非如此)。因此,好消息是、表面张力可以使泄漏通道中的液体直接堵塞通道。通过这种堵塞的泄漏通道,液体和气体既无法渗入电芯,也无法逃逸。也就是说,被堵塞的泄漏通道可以被认为是严密的。
在一篇有关锂离子电池测试的详细 SAE Paper 论文中,我们全面、定量地描述了漏电通道堵塞现象及其导致的漏电率。在下面的两个案例研究中,我们确定了会被液态电解液堵塞的剔除泄漏率。
案例研究 A:圆柱形电芯 | |
---|---|
充气压力 | 750 mbar |
电解液 | 基于 DMC (50 % DMC/50 % EC, 1.0 M LiPF6) |
限制泄漏率,有效堵漏 | 5∙10-6 mbar∙l/s |
案例研究 B: 软包电芯 | |
---|---|
充气压力 | 250 mbar |
电解液 | 基于 EMC (100 % EMC, 1.0 M LiPF6) |
限制泄漏率,有效堵漏 | 5∙10-7 mbar∙l/s |
4. 泄漏电池不适合用作校准标准
使用漏电电池校准电解液泄漏测试仪乍看起来似乎是一个可行的选择。但仔细观察后发现,这种方法太不可靠了。原因有很多:
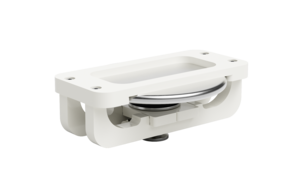
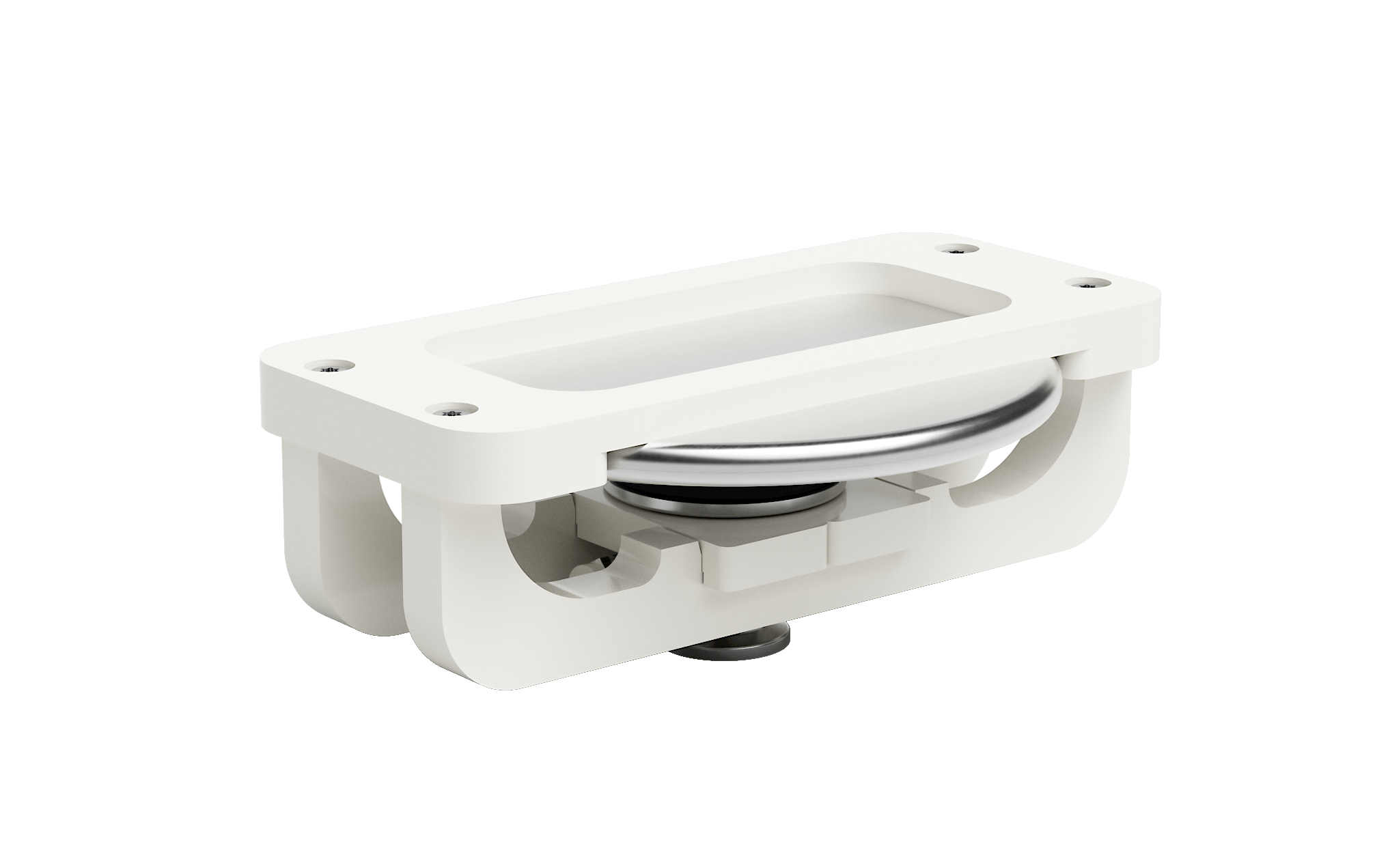
- 泄漏电池上原本存在的泄漏通道可能会被堵塞。
- 泄漏电池不可能实现测量的可重复性(见第 5 点)。
- 这样,您就无法使用经过认证的泄漏率。
- 作为一个有缺陷的部件,泄漏电池本身就不稳定。
- 要想通过刻意操作电池达到所需的泄漏率是非常困难的。
- 对每个漏液电池进行 "校准 "不会产生任何工艺可靠性。
在此背景下,使用经过认证的校准漏液(如 INFICON 的 E-Check 2.0)要方便得多。E-Check 2.0 装满了 DMC 电解质溶剂,集成在真空室中,可随时投入使用。这意味着在预设的时间间隔内,例如每两小时或每班开始时,只需几秒钟即可完成自动测试测量。与有缺陷的样品池不同,经过认证的校准漏孔可以稳定地抵御外部影响,并具有确定且始终可重复的泄漏率。因此,全自动在线测试的过程可靠性最高。
5. 泄漏电池的泄漏率随着进一步测量而降低
如果连续第二次测试同一个泄漏电池,测得的泄漏率会有所不同,通常会比之前的略低。这会导致一些用户得出错误的结论。这并不表明测试设备不可靠,事实上,这是泄漏通道的真实特征。
这是直接电解液泄漏测试的原理:渗入泄漏通道的电解液溶剂在测试室的真空中蒸发。这可以将其转化为测试气体,其浓度由测试装置中的质谱仪检测。因此,每次在真空中进行测量时,泄漏通道中电解液溶剂的浓度最初都会降低。随后的测量只会显示溶剂浓度降低,从而导致泄漏率相应降低。
但是,如果在两次测量之间等待一段时间(一小时或更长),泄漏通道中的电解液溶剂就会通过扩散作用恢复到原来的浓度,从而大大降低明显缩小的泄漏的影响。
下图显示了在六次测量过程中这种效果的示例--使用三个具有不同大小漏孔的电池。
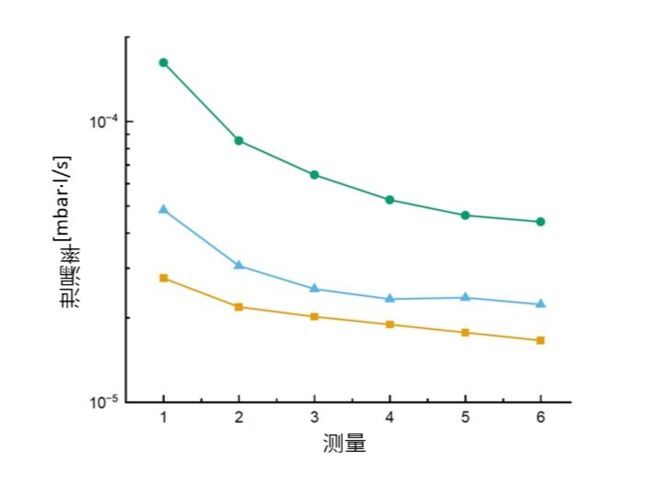
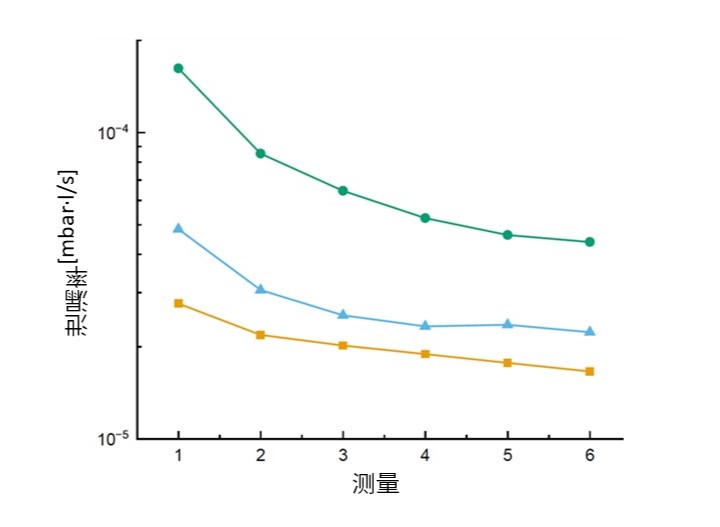
从所有这些考虑因素中得出的决定性结论是 最初、第一次测量所确定的泄漏率仍然是正确的。如果您想在不久之后再次测试同一个泄漏电池,可测量的电解液溶剂浓度--也就是可测量的泄漏率--就会降低。然而,造成这种情况的原因并不是测试系统出现故障或缺乏过程可靠性,而是泄漏通道的物理特性。