Wie eine korrekte Kalibrierung die Qualität Ihrer Produktion verbessern kann
Einfache Handgriffe mit großer Wirkung.
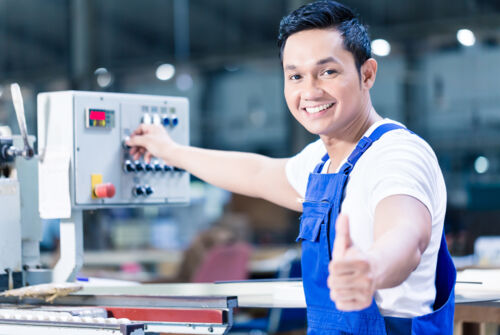
David Xu, ein fleißiger und engagierter Produktionsingenieur, der bei einem renommierten Hersteller von Lithium-Ionen-Batteriezellen arbeitet, trägt eine entscheidende Verantwortung: Er ist für die Durchführung von Helium-Lecktests an Batteriezellen zuständig, bevor diese mit Elektrolyt gefüllt werden.
Um diese wichtige Aufgabe zu erfüllen, verlässt sich David auf ein automatisches Helium-Lecktestsystem, das von seinen Kollegen in der Abteilung Systemintegration entwickelt wurde. Doch trotz des Einsatzes dieses leistungsstarken Systems gibt es immer wieder Qualitätsprobleme. Einige Batteriezellen fallen beim End-of-Line-Test durch oder weisen kurz nach der Auslieferung Probleme auf, was zu Gewährleistungsansprüchen und Kundenunzufriedenheit führt.
Entschlossen, diese Probleme zu lösen, beschloss David, das Problem weiter zu untersuchen. Er erkannte, dass der Schlüssel im Kalibrierungsprozess des Helium-Lecktestsystems liegen könnte. In Zusammenarbeit mit seinen Kollegen stellte David sicher, dass das System zu Beginn jeder Schicht mit einem Testleck kalibriert wurde, das dem kleinsten Leck entsprach, das es zu entdecken galt.
Trotz ihrer Bemühungen blieben die Qualitätsprobleme bestehen, und David wurde zunehmend frustriert. Dann stieß er auf ein Webinar über Helium-Lecktests, das ihm die Augen öffnete. In dem Webinar wurde die Bedeutung der Platzierung des Testlecks hervorgehoben.
Neugierig geworden, inspizierte David den Aufbau des Helium-Lecktestsystems und stellte fest, dass das Testleck sehr nahe am Einlass des Lecksuchers installiert war. David erkannte die möglichen Auswirkungen dieser Konfiguration auf die Genauigkeit der Ergebnisse und wandte sich sofort an seine Abteilung für Systemintegration.
Gemeinsam versuchten sie zunächst, das Testleck direkt an die Kammer anzuschließen und dann die Messung zu starten. Zu ihrer Überraschung konnte das System das Leck nicht erkennen. Das konnte nur bedeuten, dass es auch ein Problem mit dem Lecksuchgerät geben könnte. Entschlossen, dieses Problem zu lösen, beschlossen sie, den Leckdetektor auszutauschen und das System mit dem an der Kammer befestigten Testleck neu zu kalibrieren. Diesmal konnte das System das Leck erfolgreich aufspüren. Damit bestätigte sich ihr Verdacht, dass die vorherige Einrichtung nicht so leistungsfähig war wie erwartet, und sie waren nun sicher, dass sie endlich eine korrekte Messzeit und eine erfolgreiche Kalibrierung des Systems hatten.
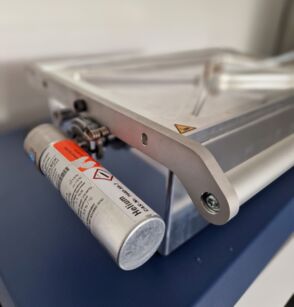
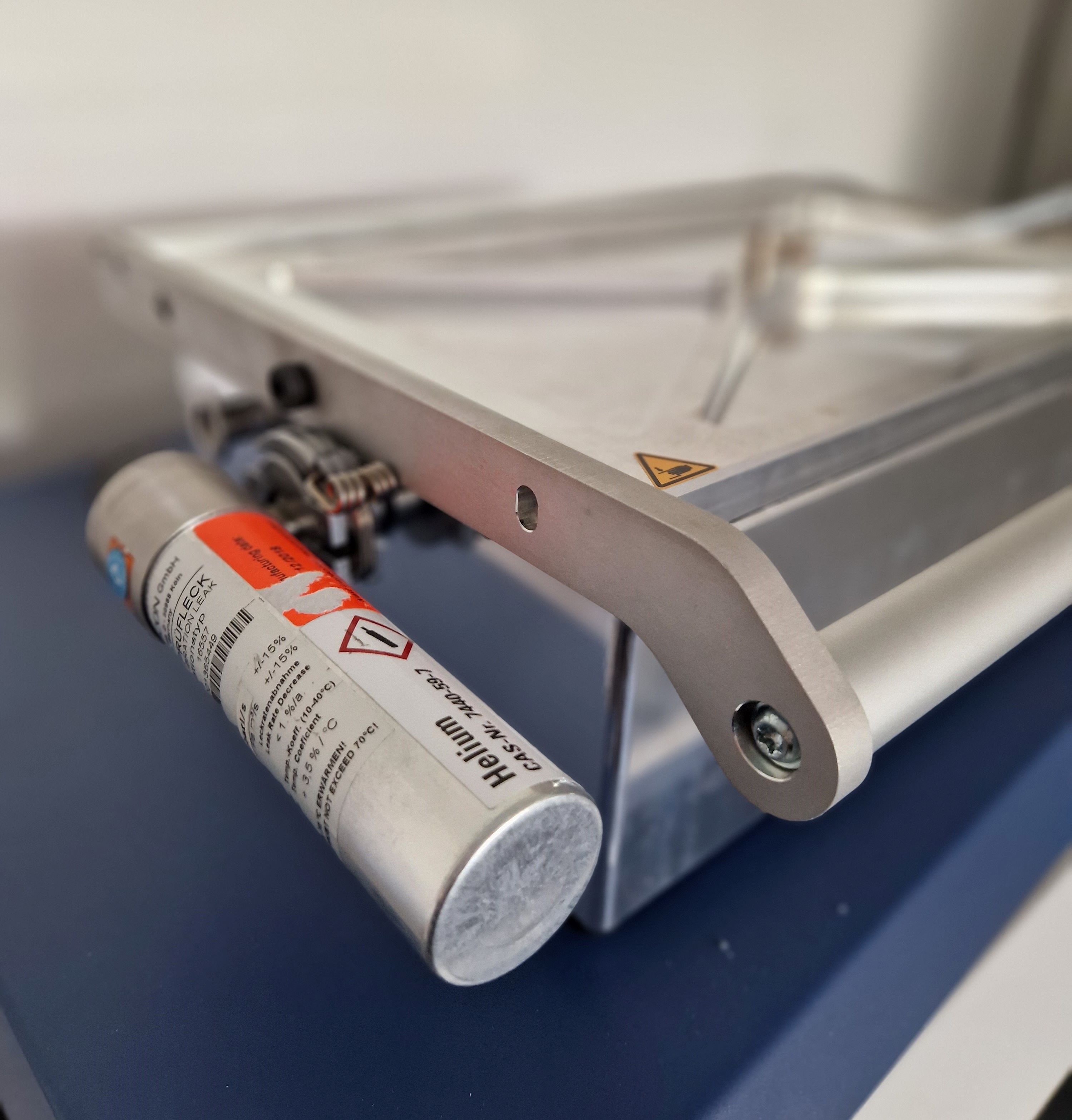
Mit der Einführung dieser Prozessänderung - neuer Lecksucher und Anordnung der Dichtheitsprüfung direkt an der Kammer - beobachtet das Unternehmen nicht nur eine erhebliche Verringerung der Batterieausfälle während der End-of-Line-Prüfung, sondern auch frühe Feldausfälle. Die Batterietests sind zuverlässiger und erfüllen letztendlich die Qualitätsstandards, die die Kunden erwarten.
In Anerkennung von Davids Engagement, seiner Problemlösungskompetenz und seines Beitrags zur Verbesserung der Produktqualität des Unternehmens erhielt er eine QS-Belohnung für diese großartige Leistung. Sein Engagement und seine Beharrlichkeit hatten nicht nur ein kritisches Problem gelöst, sondern auch große Anerkennung für seine Arbeit gebracht.
Die Geschichte von David Xu erinnert uns daran, wie wichtig kontinuierliche Verbesserungen, die Liebe zum Detail und die Auswirkungen selbst kleiner Änderungen auf die Produktqualität insgesamt sind.
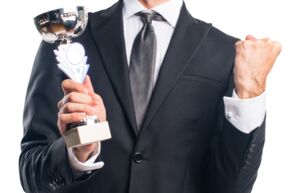
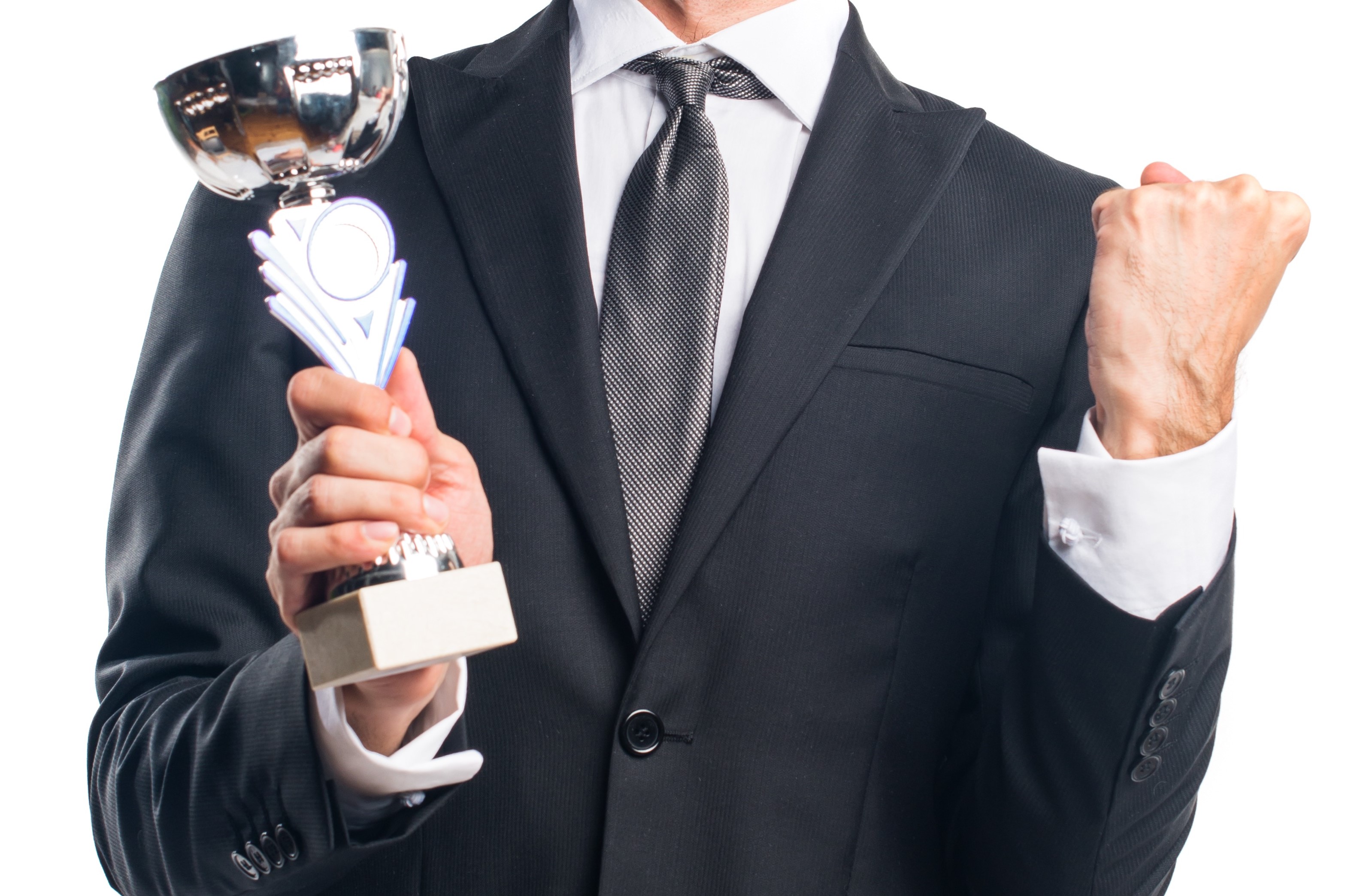
Stehen Sie vor ähnlichen Herausforderungen?
Unsere Experten helfen Ihnen gerne!