Cycle Time Improvement for 300mm Fabs
Addressing which performance improvement recommendations are more relevant for 300mm wafer fabs vs. 200mm fabs
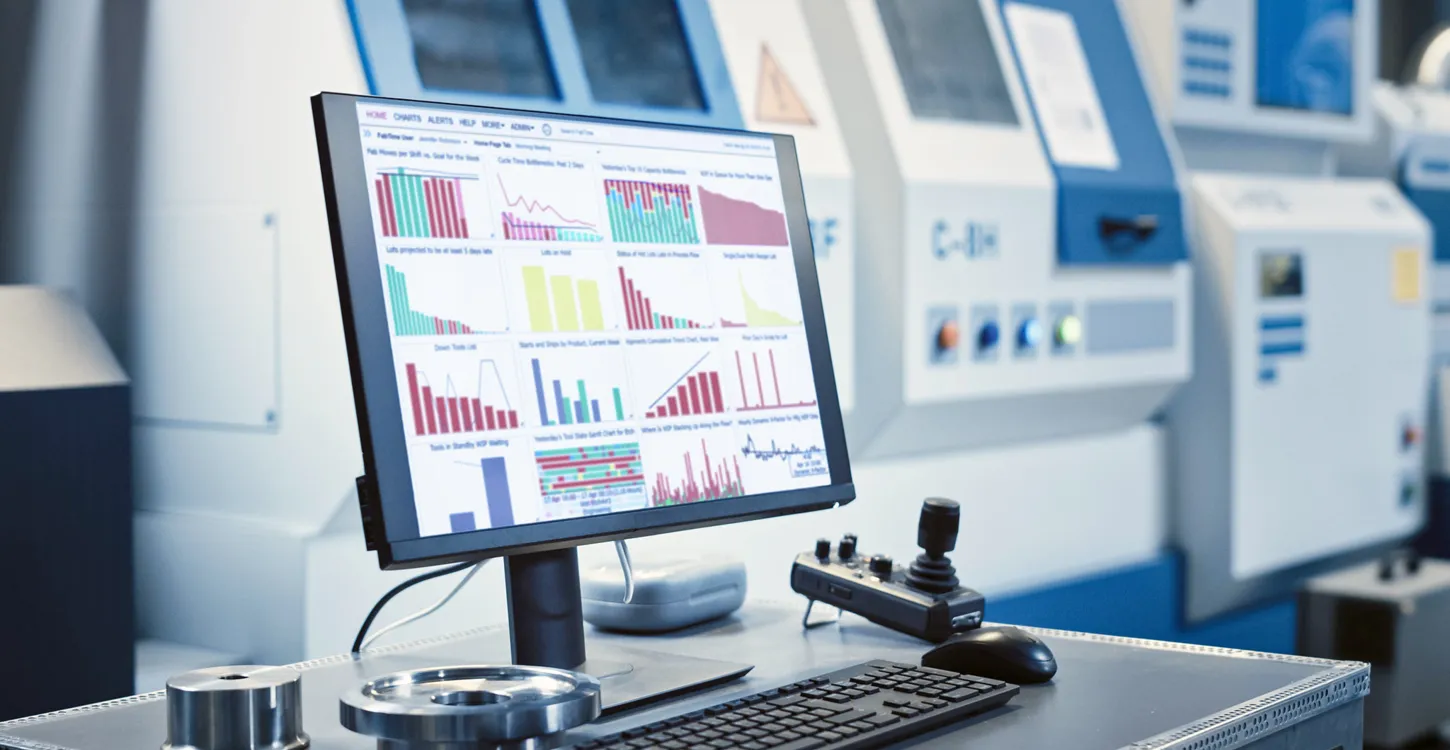
By Jennifer Robinson, Cycle Time Evangelist
This article addresses which fab cycle time-related issues and topics are more relevant for 300mm fabs and which are more useful for 200mm and smaller fabs. Because my personal experience has been more with the latter category than the former, I reached out to my LinkedIn community to help me frame the discussion. Based on that feedback, I outline some characteristics of 300 mm (and highly automated 200mm) fabs, and then share some specific recommendations.
Community Input to Frame the Discussion
I asked my LinkedIn community the following: “Looking for Input on 300mm vs. 200mm Manufacturing: What would you say are the differences between the types of fabs that would impact operational improvement strategies? Generally speaking, I’d expect more automation, more advanced scheduling/dispatching, and fewer one-of-a-kind tools in 300mm fabs. What else am I missing?”
Marc Engel, CEO at Agileo Automation, wrote: “automation between 200mm and 300mm wafer fabs is no longer necessarily a differentiating criterion, since the so-called GEM300 standards, designed for 300mm wafer fabs, are now being used in some new 200mm wafer fabs that are state-of-the-art in terms of automation. Indeed, more and more new 200mm wafer fabs are using OHT/AMHS or AGV-type carrier delivery systems. 200mm and 300mm fabs also use standard EFEM with atmospheric and vacuum robots to load/unload wafers within process modules. This distinction between 200 mm and 300 mm remains valid for plants built several years ago from an automation standpoint. Indeed, these 200mm fabs were using SECSGEM standard only without any standardization of job definition and carrier delivery, which was a clear disadvantage for cycle time optimization throughout the fab. So, I’d say that the MES generation and carrier delivery automation used are more important in differentiating cycle time than the wafer size! Of course, 300mm is clearly an advantage for the quantity of chips produced per wafer, and therefore has an impact on overall cycle time.”
Andy Beers, President at ABM Consulting, added: “All true except; the complexity of the 300mm Factory Automation design and reliability means…. If the overhead track gets backed up even for a few minutes it can take away hours of productivity to clear the stack-up. Defectivity requirements also mean more critical wet cleans and recovery requirements (chamber seasoning).”
FabTime Response: Marc’s main point is that it’s not so much a matter of 300mm vs. 200mm, but a matter of more automated fabs, using newer MES systems, vs. less automated fabs. Andy highlighted in particular the additional risk carried by fabs with automated material handling of the overhead system tying up, well, everything. We’ll wrap each of these points into the discussion below, with thanks to Andy and Marc for taking the time to respond to my question.
Characteristics of Larger, More Automated Fabs (300mm or newer 200mm)
Distinguishing characteristics of 300mm (or newer, highly automated 200mm) fabs may include:
- Wafer level tracking (vs. only lot level tracking) of move transactions.
- More automated logging of transactions (e.g., the tool sends an end run transaction to the MES when the lot is done processing, vs. less automated fabs where there is no transaction recorded until an operator is there to load the tool).
- Automated material handling, via overhead transit system or via AGV-type carrier systems (robots!).
- More advanced scheduling and dispatching, necessary to run the most automated systems, in contrast to more manual fabs where operators have some leeway in selecting the next lot to process.
- Fewer one-of-a-kind tools (simply as a matter of scale, because the fabs are larger).
- More chips per wafer for 300mm wafers (meaning that each wafer is more valuable, such that scrap is more expensive).
- Greater cost of the fab overall, meaning more pressure to maintain high utilization of the tools.
- More stringent processing requirements in some cases (wet cleans, etc.). Possibly more time links between process steps(?).
Of course, there is a spectrum in terms of level of automation for fabs, independent of wafer size. An older fab might undergo a project to add robots for material transfer, or upgrade to a more advanced MES. But this list is sufficient to give us some ideas about specific cycle time improvement recommendations that are relevant for the larger, more automated fabs, many of which are 300mm fabs.
Recommendations for Cycle Time Improvement in 300 Fabs
Here are a few recommendations that are applicable for 300mm and highly automated 200mm fabs
- Minimize process restrictions to ensure that each operation can be run on at least 2 qualified tools (ideally 3-4). Just because a fab has a high level of tool redundancy does not necessarily mean that this fab has at least two qualified tools for every recipe, particularly for fabs doing foundry work. But it’s not helpful to have plenty of redundant tools if individual recipes are not cross-qualified.
- Subject to not violating 1, consider some creation of sub-groups within the tool groups to reduce process time variability (different process times from lot to lot). It’s also important when doing this to keep an eye on the relative utilization of the sub-groups in the presence of product mix changes. See The Three Fundamental Drives of Cycle Time for more on the impact of utilization and process time variability.
- Look for and reduce long periods of unavailable time on tools (whether scheduled or unscheduled), especially in toolsets with less redundancy. That is, go beyond availability to look at variability of availability and green-to-green time. See On Breaking Up PMs and Other Unavailable Periods for more on the impact of long downtimes and green-to-green.
- Use dispatch rules or scheduling algorithms that look downstream to avoid starving bottleneck tools and allowing too much WIP to pile up in one place (line balance).
- Analyze the efficiency of the AMHS to ensure that lots aren’t being grouped unnecessarily for transit or spending excessive time in transit.
- Put heavy focus on the reliability of the overhead transit system. It is something of a mega one-of-akind tool in the fab and can delay every lot if it fails.
- Take advantage of more automated logging of transactions to report time that WIP spends in states like travel and post-processing. The former may indicate a need for optimization or expansion of the material handling system. The latter can be used to identify places where additional operators are needed (post-process time is time from when the tool finished processing until an operator logged a move out – it can be an indicator of insufficient operators).
Conclusions
The fundamental things that drive up cycle time in a discrete manufacturing environment are common to all factories. At the tool level, they boil down to utilization, variability, and number of qualified tools. The many complexities of wafer fabs (see Issue 24.04 for a recap) ultimately impact cycle time because they impact one or more of those three variables. Because we take a factory physics approach that focuses on these fundamentals, we’ve never differentiated much in this newsletter between the different types of fabs in our recommendations. Our experience base is more with people working in 200mm and smaller fabs, so our recommendations have probably slanted somewhat in that direction (like Issue 23.05 about managing true one-of-a-kind tools). In this issue, we have focused more specifically on 300mm fabs (or, as pointed out by one of our colleagues on LinkedIn, highly automated 200mm fabs). After thinking about characteristics of those fabs, we’ve shared some specific recommendations.
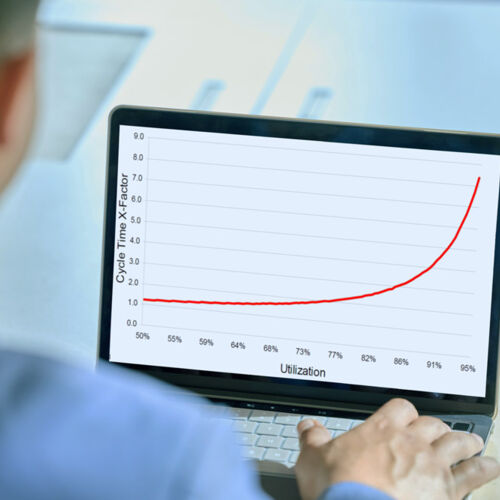