Dichtheitsprüfungsaufgaben für Elektronik und Sensoren moderner ADAS-Fahrzeuge
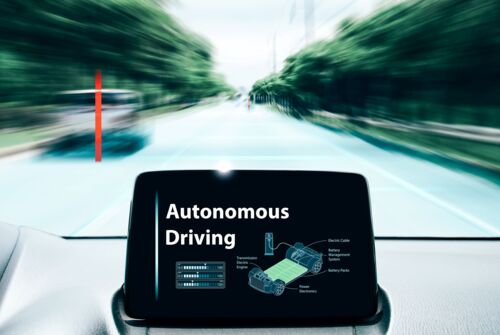
Wenn Fahrzeuge in der Lage sein sollen, sich autonom oder teilautonom zu bewegen, müssen sie dafür mit einer Vielzahl an Sensoren und elektronischen Komponenten ausgestattet sein: die Idee hinter den fortschrittlichen Advanced Driver Assistance Systems (ADAS).
Dass ADAS-Komponenten zuverlässig funktionieren, ein Fahrzeugleben lang, ist eine unverzichtbare Sicherheitsanforderung. Wasser aber ist der Feind jeder Elektronik und auch aller Sensoren. Oft gilt es, schon ein Eindringen von Luftfeuchtigkeit zu verhindern. Viele ADAS-Sensoren müssen deshalb nicht nur wasser-, sondern sogar gasdicht sein. Deswegen nutzen Hersteller zur Qualitätssicherung moderne Prüfgasmethoden, die ebenso empfindlich wie zuverlässig sind. Für viele Szenarien empfehlen sich darum Heliumprüfungen in der Vakuumkammer.
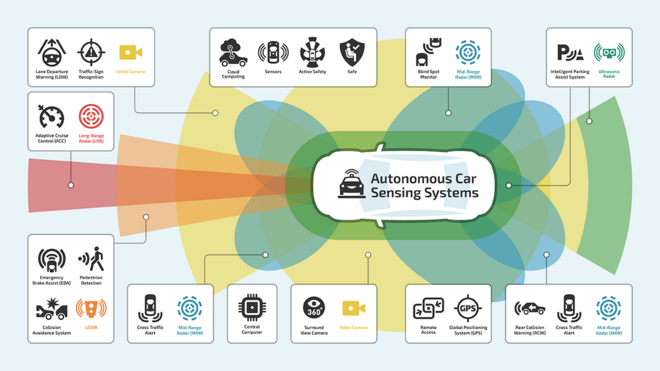
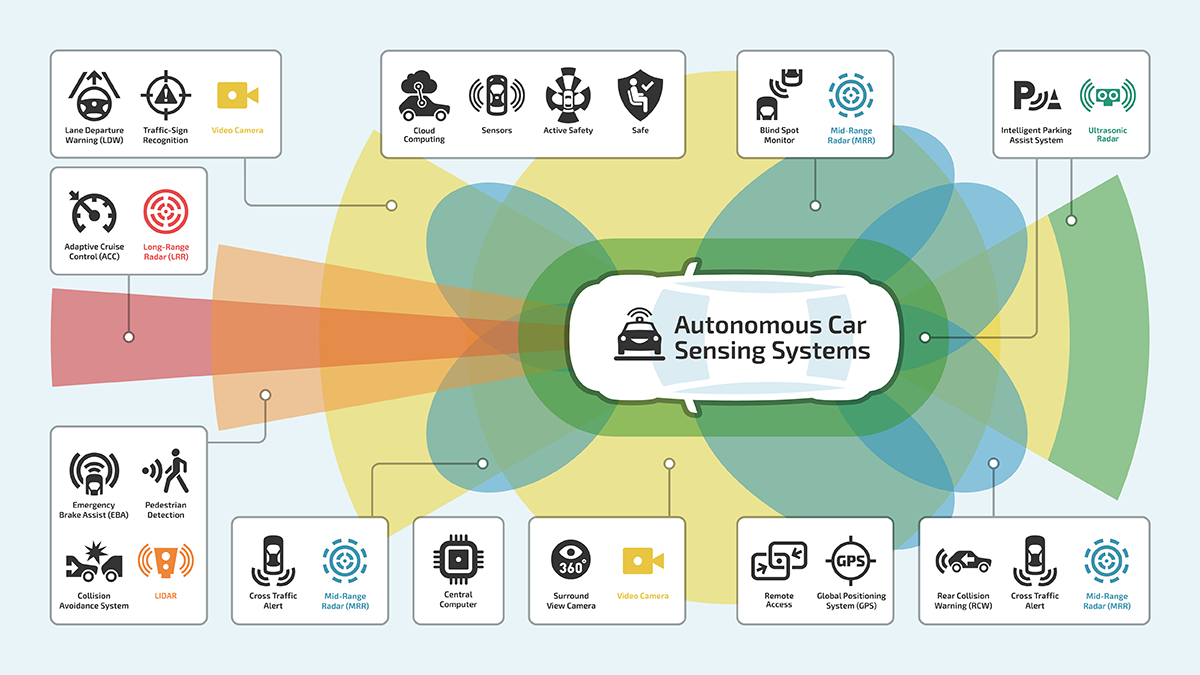
Null-Fehler-Strategie statt Six Sigma
Bei Geräten der Unterhaltungselektronik sind die Anforderungen an die Robustheit und Dichtigkeit der Halbleitertechnologie naturgemäß weitaus geringer als bei sicherheitskritischen Komponenten eines Fahrzeugs. In der Unterhaltungselektronik ist ein Betrieb in Temperaturbereichen von 0 bis 40 °Celsius erforderlich, während die Fahrzeugelektronik in der Regel in einem Temperaturfenster von -40 bis 150 °Celsius zuverlässig funktionieren muss. Betrachtet man die ADAS-Sensortechnologie, so sind die Anforderungen im Vergleich zur Unterhaltungselektronik wesentlich höher.
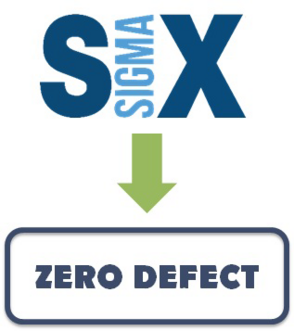
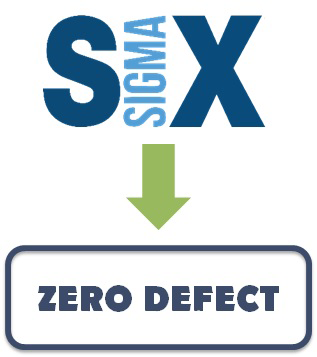
Ein Six-Sigma-Ansatz, der 3,4 Fehler in einer Million Teilen zulässt, wäre undenkbar. Stattdessen verfolgen die Hersteller von ADAS-Komponenten eine Null-Fehler-Strategie – mit weniger als einem Fehler in einer Milliarde Teilen –, um den sicheren Betrieb von Fahrzeugen zu gewährleisten, die sich sowohl im dichten Stadtverkehr als auch bei Autobahngeschwindigkeiten autonom oder teilautonom bewegen sollen.
Das Gehäusematerial als Dichtungsfaktor
Der natürliche Feind aller elektrischen und elektronischen Komponenten in einem Fahrzeug ist Wasser. Der Schutz der Gehäuse elektronischer Komponenten vor Wassereintritt ist entsprechend wichtig, um das Risiko eines Kurzschlusses zu vermeiden. ADAS-Sensoren müssen in der Regel die Schutzklassen IP67 oder sogar IP69K erfüllen.
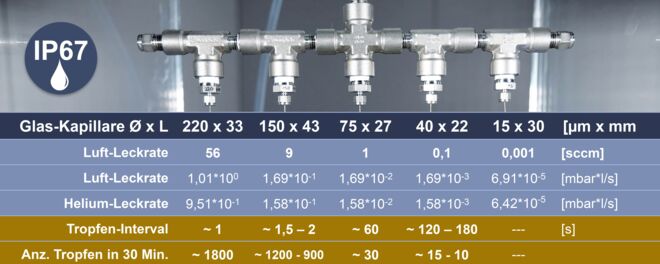
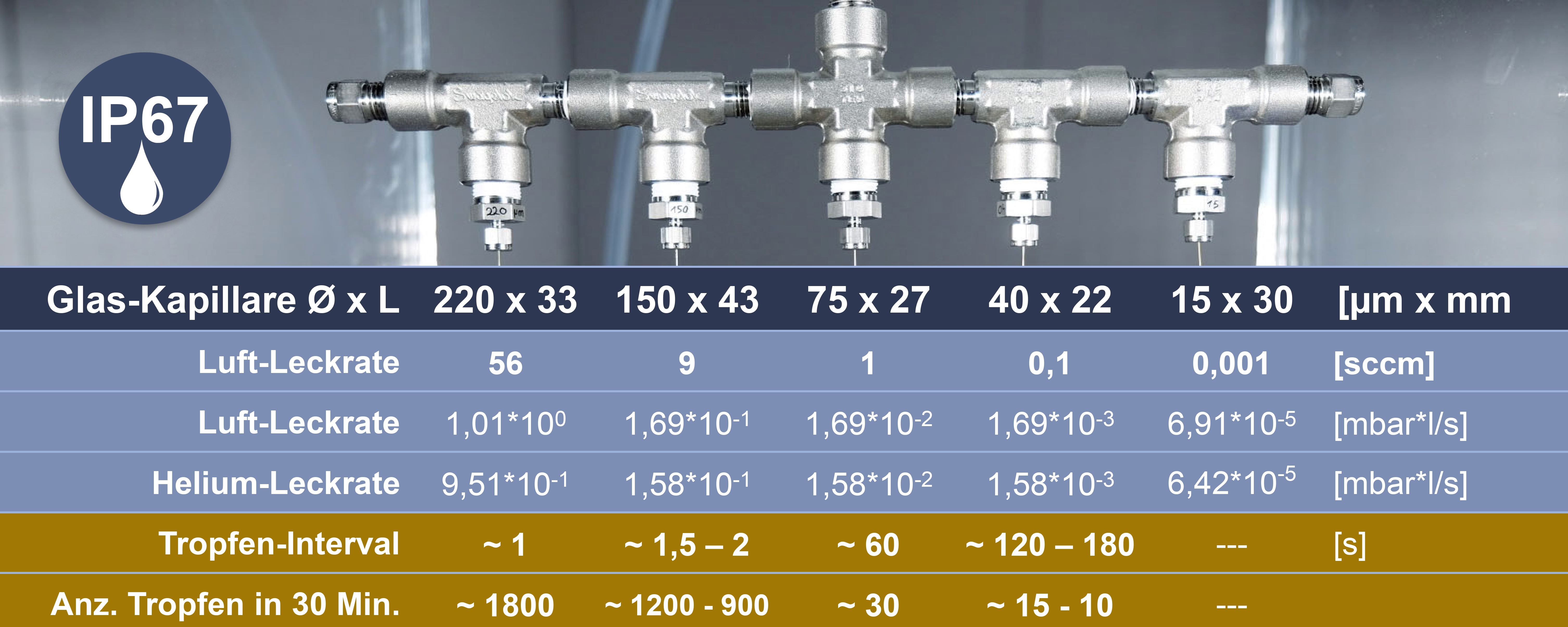
Es besteht ein enger Zusammenhang zwischen dem Gehäusematerial und den zu prüfenden begrenzenden Leckageraten. Interessanterweise gelten für Gehäuse aus Kunststoff oder Stahl weniger strenge Anforderungen als für Gehäuse aus Aluminium (siehe Ingress Protection Class IP67). Dies liegt daran, dass die Leichtigkeit, mit der Wasser durch einen Leckagekanal mit definierter Länge und definiertem Durchmesser in ein Gehäuse eindringt, einen entscheidenden Einfluss darauf hat, wie leicht sich ein Wassertropfen vom Gehäusematerial lösen kann.
Aluminium ist beispielsweise viel kritischer als Kunststoff, da sich Wasser viel leichter von Aluminium löst. Um sicherzustellen, dass kein Wasser in Kunststoffgehäuse eindringen kann, können diese mit der einfachen Akkumulationsmethode auf eine Helium-Leckrate von 10-3 mbar∙l/s getestet werden. Dabei wird das Gehäuse mit dem Testgas gefüllt und in eine einfache Akkumulationskammer gestellt. Ein Lecksucher misst dann, wie viel Testgas aus eventuellen Lecks in einem bestimmten Zeitraum aus dem Gehäuse in die Kammer entweicht, und bestimmt anhand dieser Messungen die Leckrate.
Vakuumtests für Aluminiumgehäuse
Wenn Gehäuse nicht aus Kunststoff oder Stahl, sondern aus Aluminium bestehen, sind Tests auf hundertmal kleinere Lecks erforderlich. Für solche Tests auf Leckraten von 10-5 mbar∙l/s ist die Heliumprüfung in der Vakuumkammer die einzige Option. Das Aluminiumgehäuse wird mit Helium gefüllt und in eine Kammer gegeben, die anschließend von der Luft evakuiert wird. Ein Vakuum-Leckdetektor spürt selbst kleinste Mengen Helium auf, die in das Vakuum entweichen. Manchmal ist es jedoch nicht möglich, das Gehäuse zu befüllen – beispielsweise weil es bereits hermetisch abgedichtet ist. In diesem Fall wird die sogenannte Bombing-Methode angewendet. Beim Bombing wird das Testteil zunächst einer Heliumatmosphäre ausgesetzt, damit das Testgas durch etwaige Lecks in das Innere des Gehäuses eindringen kann. Erst dann kann das Testteil in die Vakuumkammer eingebracht werden, wo das austretende Helium wie zuvor beschrieben nachgewiesen wird.
Steuermodule mit Gore-Tex®-Membran
Bei einigen Fertigungsprozessen wird die Notwendigkeit einer anschließenden Dichtheitsprüfung bereits berücksichtigt – und eine Bombardierung wird vermieden, indem das Gehäuse unmittelbar vor dem endgültigen Verschließen mit einem Prozent Helium gefüllt wird. Undichte Stellen können dann erneut durch eine Vakuum-Dichtheitsprüfung erkannt werden.
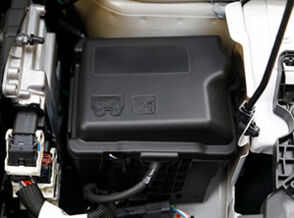
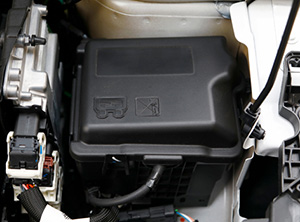
Es gibt jedoch eine andere Möglichkeit, das Prüfgas in das Bauteil zu bringen. Steuergeräte sind sehr oft mit einer semipermeablen Gore-Tex-Membran ausgestattet, um temperaturbedingte Luftdruckunterschiede auszugleichen und einen Druckunterschied zwischen dem Inneren des Gehäuses und der Umgebung zu verhindern. Die Tatsache, dass solche Gehäuse durch ihre Membran atmen, wird genutzt, um sie während der Dichtheitsprüfung mit Helium unter Druck zu setzen. Das austretende Prüfgas kann dann in einer Akkumulationskammer oder in einer Vakuumkammer nachgewiesen werden. Die Prüfung in einer Vakuumkammer hat immer den Vorteil einer höheren Prüfgeschwindigkeit und kürzerer Zykluszeiten, während die Prüfung in der einfachen Akkumulationskammer weniger Investitionen erfordert, aber in der Regel längere Prüfzyklen benötigt.
ADAS-Sensoren müssen gasdicht sein
Viele ADAS-Sensoren müssen nicht nur wasserdicht, sondern auch gasdicht sein. Eine nicht gasdichte Komponente birgt immer das Risiko, dass eingedrungene Feuchtigkeit bei Temperaturänderungen kondensiert und ihre absolute und dauerhafte Funktionssicherheit beeinträchtigt. Beschlag durch Feuchtigkeit ist ein ähnliches Problem für LIDAR (Light Detection And Ranging) und für Kameraoptiken. Um die Gasdichtheit der sicherheitskritischen LIDAR- und Kamerakomponenten zu überprüfen und jegliches Eindringen von Luftfeuchtigkeit auszuschließen, sind Dichtheitsprüfungen gegen sehr kleine Grenzleckraten im Bereich von 10-6 bis 10-7 mbar∙l/s erforderlich. Diese geringen Leckraten können nur durch Helium-Vakuumtests nachgewiesen werden. Die gleichen strengen Dichtheitsanforderungen gelten auch für die Gasdichtungen in einem Sensorgehäuse mit elektrischen Durchführungen.
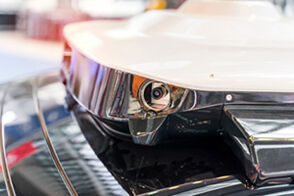
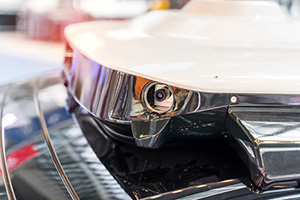
Kein autonomes Fahren ohne Dichtheitsprüfung
Das Ziel der Hersteller von ADAS-Komponenten, eine Ausfallrate von weniger als einem Fall pro Milliarde Teile zu erreichen, mag ehrgeizig erscheinen, ist aber unerlässlich. Die Funktionalität aller sicherheitskritischen Systeme muss langfristig gewährleistet sein. Eine intensive und zuverlässige Dichtheitsprüfung dieser Komponenten auf Gasdichtheit während der Produktion und das Ausschließen selbst kleinster Lecks reduziert das Risiko des Eindringens von Feuchtigkeit. Sensoren, die sozusagen mitten im Betrieb „erblinden“, wären bei den höheren ADAS-Autonomiestufen undenkbar. Kein autonomes Fahren ohne Dichtheitsprüfung. Man sollte sich also vor Augen halten, dass ein erfolgreiches Dichtheitsprüfprogramm zu sicherem, zuverlässigem autonomen Fahren führt.
Für tiefere Einblicke können Sie sich auch unser On-Demand Webinar über die Dichtheitsprüfung von Fahrzeugelektronik und ADAS-Sensoren ansehen.
Sie Hilfe bei Ihren spezifischen Anforderungen an die autonome Dichtheitsprüfung benötigen, wenden Sie sich bitte an Ihren nächstgelegenen Vertriebsmitarbeiter.
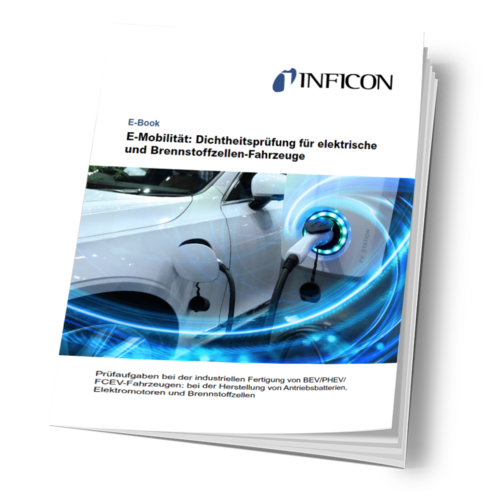