Die 5 wichtigsten Fehler bei der Kalibrierung und wie man sie vermeidet
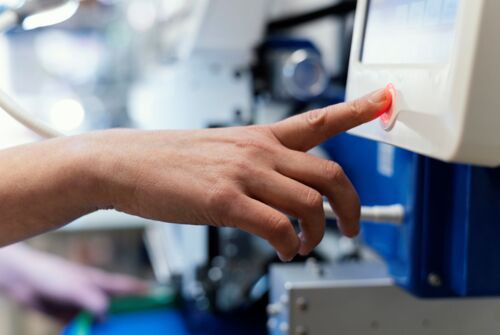
Die Dichtheitsprüfung ist ein wesentlicher Bestandteil der Qualitätskontrolle für viele Komponenten in der industriellen Fertigung. Eine genaue Kalibrierung des Dichtheitsprüfsystems ist eine Voraussetzung für die Erzielung genauer Dichtheitsprüfergebnisse. Eine ungenaue Kalibrierung kann entweder dazu führen, dass undichte Teile nicht als undicht eingestuft werden (wenn die ermittelte Leckrate zu gering ist), so dass fehlerhafte Teile weiterverarbeitet werden, oder dazu, dass zu viele Teile als nicht gut eingestuft werden, wenn die Leckrate zu groß ist, und so die Ausbeute des Produktionsprozesses verringert wird.
Im Folgenden erläutern wir die 5 häufigsten Fehler bei der Kalibrierung und wie Sie sie vermeiden können.
Fehler 1: Die Kalibrierung wird mit einer Leckage durchgeführt, die genauso groß ist wie die Rückweisleckrate
Auf den ersten Blick scheint die Kalibrierung des Dichtheitsprüfsystems mit einem Leck, das der exakten Ausschussleckrate entspricht, sehr attraktiv. Betrachtet man jedoch die Details, birgt dies einige Risiken. Obwohl der natürliche Heliumhintergrund in der Luft nur 5 ppm beträgt, kann er bei industriellen Dichtheitsprüfungen leicht erhöht sein, da kleine Mengen Helium freigesetzt werden können, wenn jedes Teil, das zuvor mit Helium gefüllt war, abgeklemmt wird. Außerdem ist der Heliumhintergrund in der Regel kein fester Wert, sondern weist im Laufe der Zeit erhebliche Schwankungen auf (Rauschen). Das Gleiche gilt z. B. für die Erkennung von Kältemittellecks, bei denen der Gashintergrund stark durch Gase beeinflusst wird, die versehentlich von nahe gelegenen Tankstellen freigesetzt werden.
Für eine stabile Kalibrierung ist es immer ratsam, ein Kalibrierleck mit einer Leckrate zu verwenden, die mindestens eine Dekade höher ist als die des Hintergrunds, damit der Lecksucher deutlich zwischen dem Hintergrund- und dem Testlecksignal unterscheiden kann und etwaige Schwankungen des Hintergrunds nur einen geringen Einfluss auf das Kalibriersignal haben.
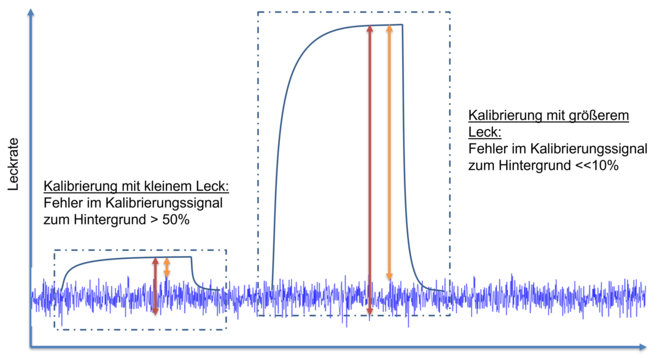
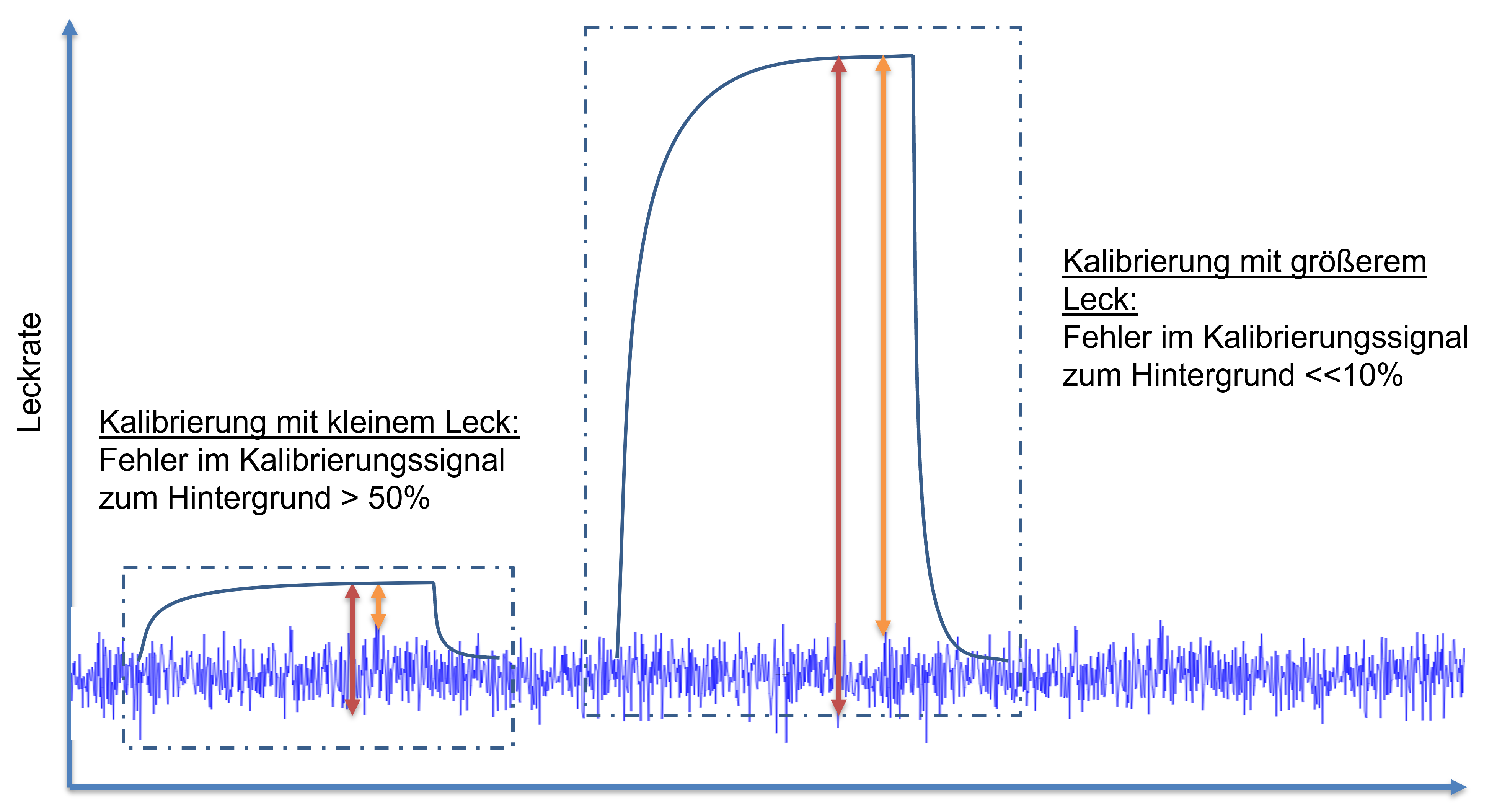
Die Anwendung dieses sicheren Kalibrierverfahrens erfordert Leckdetektoren, die eine gute Linearität aufweisen, so dass auch eine deutlich kleinere (oder größere) Leckrate noch genau angezeigt wird.
Zur Überprüfung der Auslegung des Dichtheitsprüfsystems kann ein zweites Validierungsleck verwendet werden, das die Ausschussleckrate darstellt, um zu beweisen, dass das System die gewünschte Leckgröße zuverlässig finden kann und über eine
Fehler 2: Verwendung bekannter undichter Teile als Prüflecks
Manchmal wird das Qualitätspersonal mit der täglichen Aufgabe betraut, das ordnungsgemäße Funktionieren eines Dichtheitsprüfsystems zu überprüfen. Die Verwendung eines Teils mit einem bekannten Leck kann ein guter Ansatz sein, da dadurch das gesamte Dichtheitsprüfsystem überprüft wird. Die Verwendung undichter Teile aus der Produktion oder sogar die absichtliche Herstellung undichter Teile (z. B. durch Bohren von Löchern) ist jedoch keine zuverlässige Option. Teile aus der Produktion können ihre Leckrate im Laufe der Zeit verändern (weil Schmutz aus der Produktion in den Leckagepfad gelangt und diesen verstopft). Außerdem ist es sehr schwierig, ein Produktionsteil mit einer Leckrate zu finden oder herzustellen, die der Leckrate im Ausschuss nahe kommt.
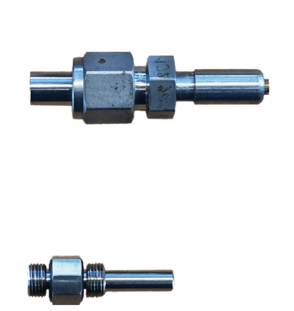
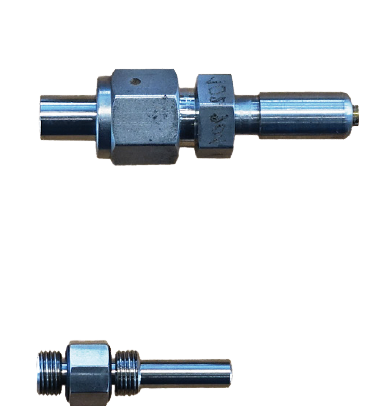
Eine gute Möglichkeit, dieses Problem zu umgehen, ist die Verwendung eines Produktionsteils mit einem eingebauten offenen Leck, das eine Leckrate aufweist, die der Ausschussleckrate entspricht. Offene Lecks sind sehr wiederholbar und werden mit einem Testleckzertifikat geliefert, das auf nationale Standards rückführbar ist. Mit diesem Ansatz kann der gesamte Prüfprozess getestet werden, z. B. auch, ob die für die Befüllung mit Prüfgas verwendeten Werkzeuge eine ordnungsgemäße Abdichtung des Teils gewährleisten.
Fehler 3: Das Kalibrierleck wird an der falschen Stelle des Dichtheitsprüfsystems installiert
Bei einigen Vakuumdichtheitsprüfsystemen wird das Testleck sehr nahe am Einlass des Lecksuchgeräts installiert oder es wird eine interne Kalibrierung des Lecksuchgeräts verwendet. Im Vergleich zu einem Leck in den zu prüfenden Teilen führt dies zu Unterschieden in der vom Lecksuchgerät erkannten Leckgröße. Die Ansprechzeit des Systems (die Zeit, die das Helium braucht, um zum Sensor zu gelangen) kann bei Helium, das aus dem Teil kommt, länger sein als bei Helium, das aus dem nahe gelegenen Testleck kommt. Bei einer gegebenen Messzeit steigt das Signal vom Teil möglicherweise nicht auf seinen vollen Pegel an (während das Signal vom Testleck dies tut), was zu einem zu niedrigen Leckratenwert für das zu erfassende Teil führt.
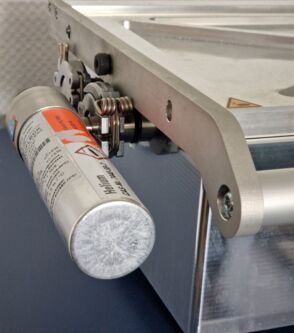
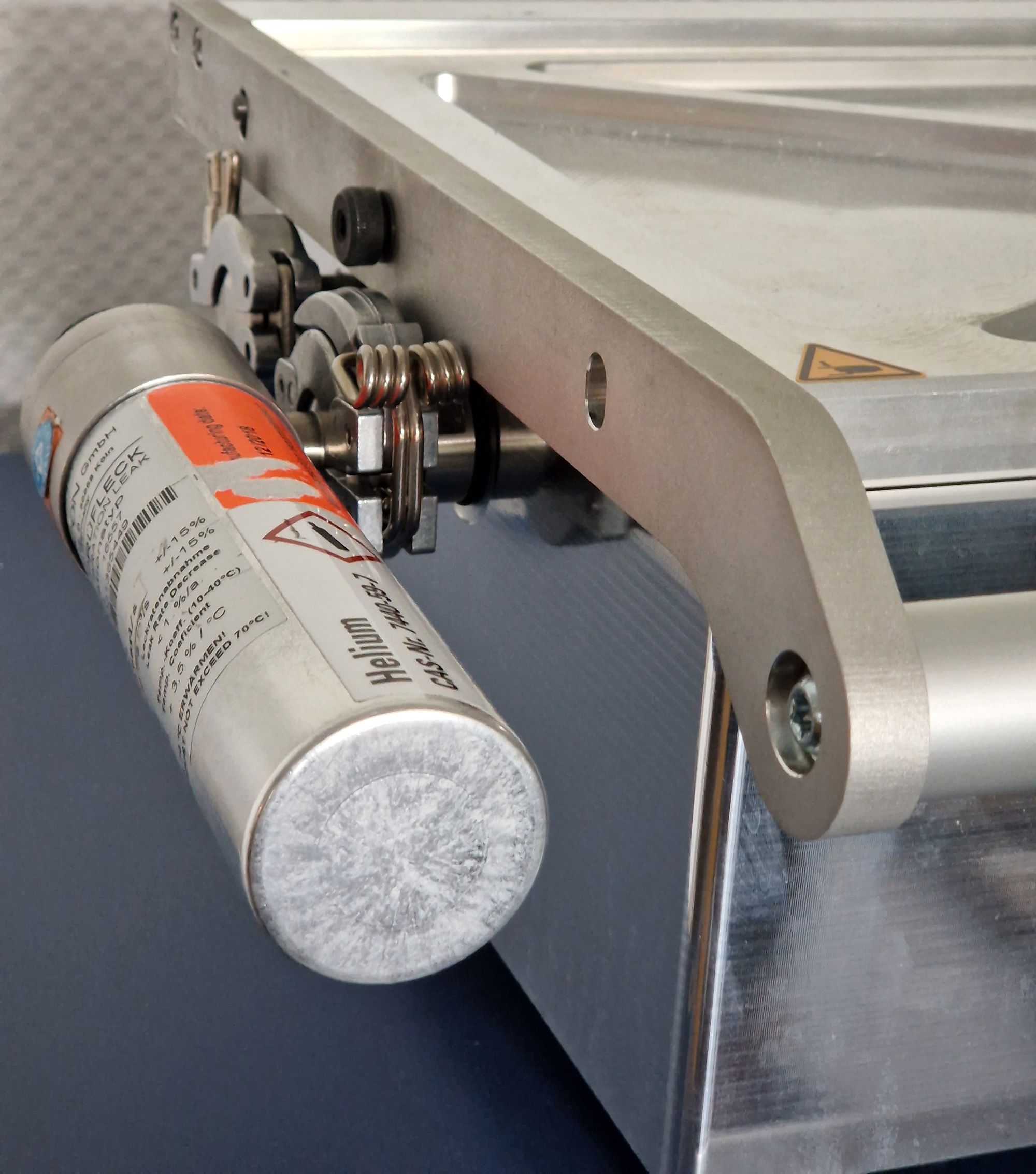
Defekte Teile können den Test in diesem Fall trotzdem bestehen! Oder schlimmer noch, das System kann so ausgelegt sein, dass große Pumpen verwendet werden und nur ein Teil des Heliums, das vom Teil in der Kammer kommt, zum Lecksuchgerät gepumpt wird (Teilstromdesign), was ebenfalls zu einem deutlich reduzierten Heliumsignal vom Teil im Vergleich zum Signal vom Testleck führen wird. Das Kalibrierleck sollte entweder an der Prüfkammer installiert werden, oder es kann ein Originalteil mit einem zertifizierten Prüfleck, das auf dem Teil installiert ist, zur Kalibrierung verwendet werden.
Fehler 4: Ignorieren der Temperaturabhängigkeit eines Membran-Testlecks
Die Leckrate eines Testlecks ist im Grunde ein reduzierter Gasfluss aus einem Gasreservoir. Es gibt zwei Möglichkeiten, den Durchfluss zu verringern: durch die Schaffung einer sehr kleinen Öffnung (so genannte Diffusions- oder Kapillarlecks) oder durch die Steuerung des Durchflusses durch eine Membran (so genannte Permeations- oder Membranlecks). Die Permeation durch eine Membran ist stark temperaturabhängig, während die Diffusion von Gas nahezu temperaturunabhängig ist. Daher können Kapillarlecks in einem größeren Temperaturbereich eingesetzt werden (innerhalb der Temperaturschwankungen, die in einem Produktionsbereich auftreten können), während Permeationslecks immer einen Korrekturfaktor für den Temperatureffekt benötigen.
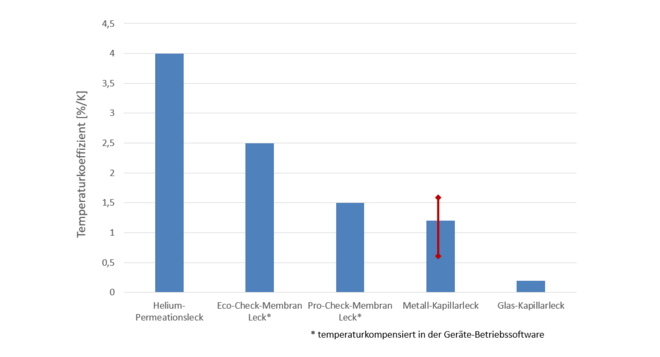
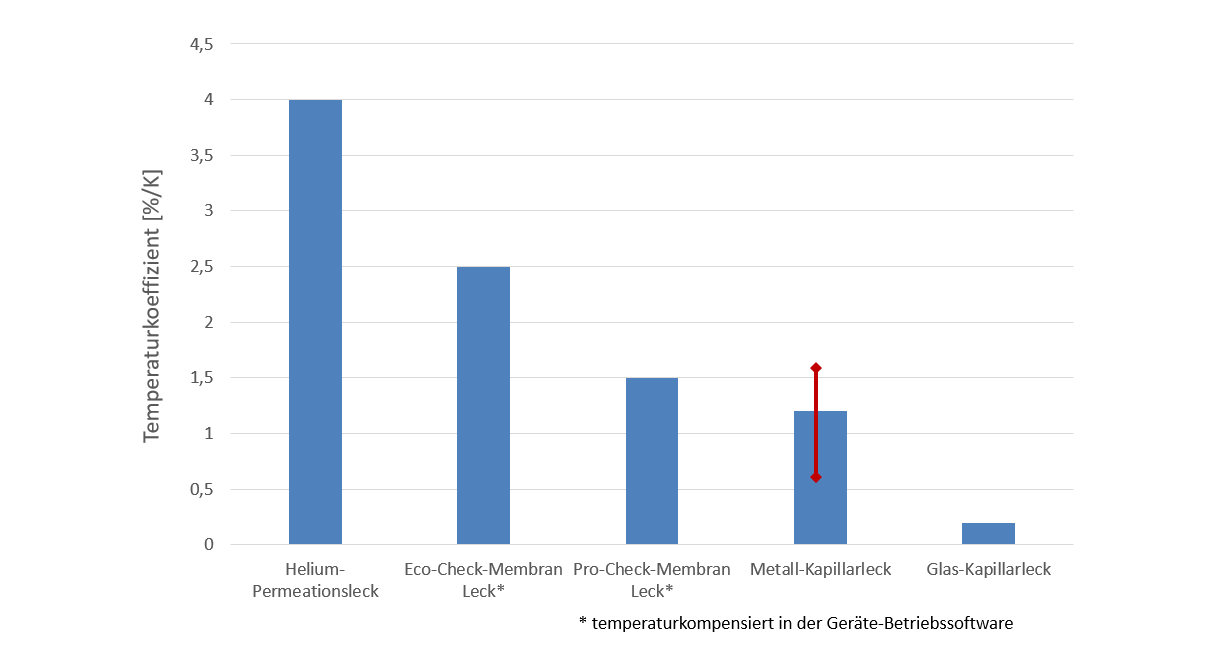
Fehler 5: Nicht alle Kapillarlecks sind gleich
Kapillarlecks können entweder aus Glaskapillaren oder aus Metallkapillaren hergestellt werden. Bei Glaskapillarlecks wird die erforderliche Leckrate durch die Wahl eines geeigneten Innendurchmessers der Kapillare und die genaue Einstellung der Kapillarlänge erreicht. Bei Lecks in Metallkapillaren wird der Durchfluss durch Quetschen der Metallkapillare verringert, um den Querschnitt zu verkleinern und eine Öffnung für die Durchflussverringerung zu schaffen. Bei gleicher Leckgröße ist die kleinste Öffnung der Kapillare in einer Glaskapillare wesentlich größer als der gewellte Querschnitt einer Metallkapillare. Daher sind Metallkapillarlecks anfälliger für Verstopfungen durch kleine Staubpartikel. Außerdem sind Kapillarlecks aus Metall etwas stärker temperaturabhängig, da sich Metall mit der Temperatur stärker ausdehnt als Glas und sich der kleine gewellte Querschnitt bei der Ausdehnung des Metalls unvorhersehbar verändern kann (ausdehnen oder sogar weiter zusammengedrückt werden kann).
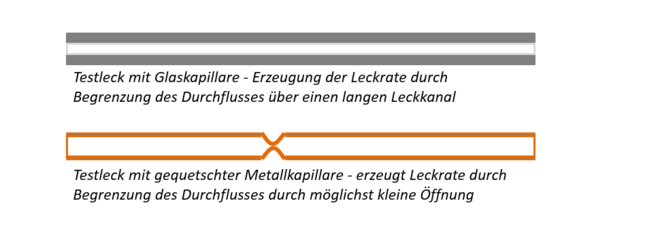
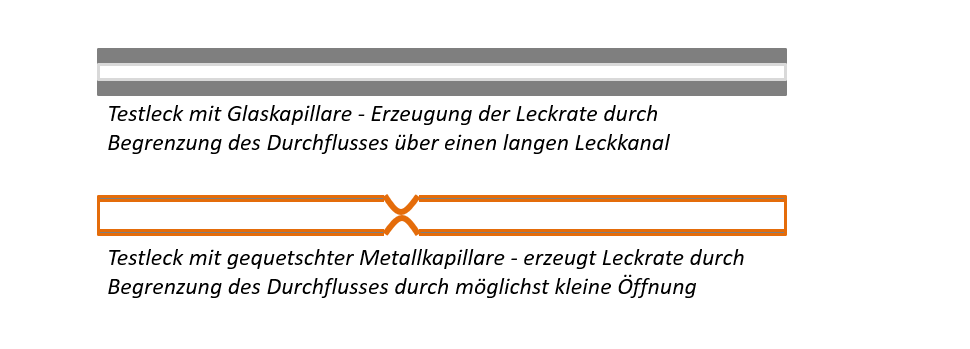
Das korrekte Kalibrieren von Dichtheitsprüfungen kann eine komplexe Aufgabe sein.
Schauen Sie sich unser On-Demand-Webinar (Englisch) zum Thema "Korrekte Kalibrierverfahren zur Dichtheitsprüfung für eine hochpräzise Qualitätskontrolle" an und erfahren Sie mehr.