INFICON System-Ingenieur gewinnt RUAG Innovation Award
Dominic Moser, System-Ingenieur, erhält den RUAG Innovation Award für seine Bachelorarbeit in Mobile Robotics an der FH Graubünden, Schweiz.
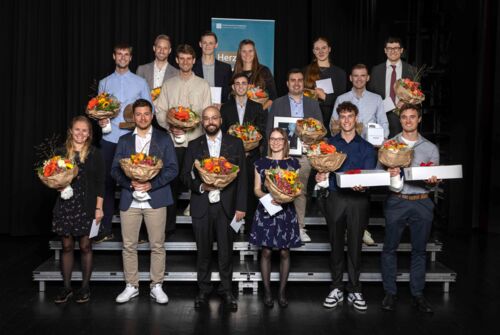
UPDATE: Dominic Moser erreicht ersten Platz beim schweizweiten Innovationswettbewerb
Nach dem Gewinn des renommierten RUAG Innovation Award für seine Bachelorarbeit an der Fachhochschule Graubünden hat Dominic Moser nun auch den ersten Platz beim nationalen Innovationswettbewerb in der Schweiz erzielt. Diese weitere Auszeichnung unterstreicht die Bedeutung seiner innovativen Ansätze zur Lösung kritischer Herausforderungen in den Bereichen Technik und Nachhaltigkeit.
(Dezember 2024)
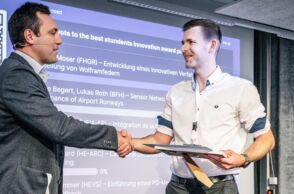
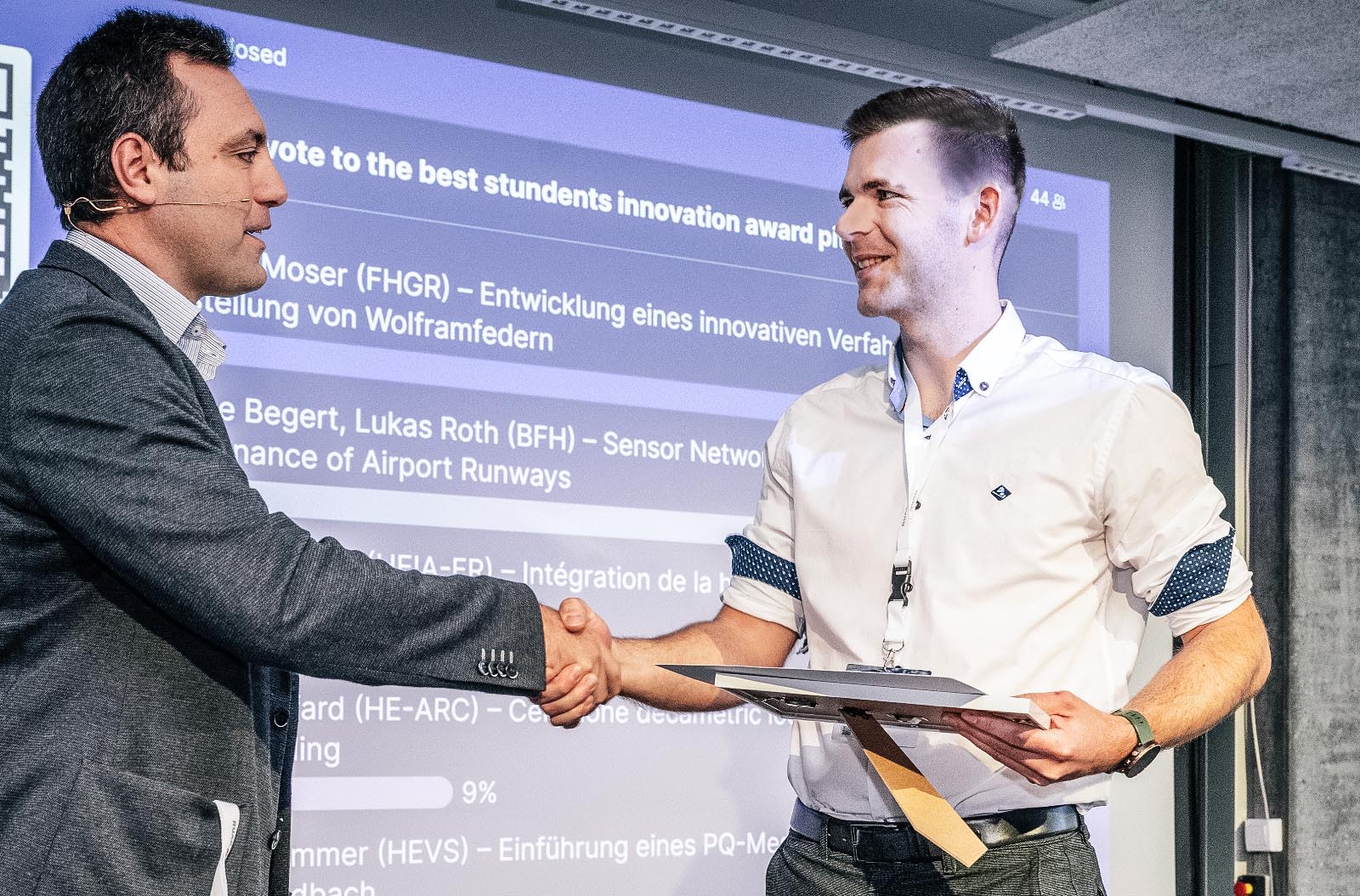
RUAG Innovationspreis der Fachhochschule Graubünden
Dominic Moser hat für seine Bachelorarbeit an der Fachhochschule Graubünden im Bereich Mobile Robotics den renommierten RUAG Innovation Award erhalten. Der RUAG Innovation Award zeichnet junge Talente aus, die sich in wissenschaftlich fundierter und praxisorientierter Weise mit sicherheitsrelevanten Fragestellungen der Schweiz auseinandersetzen und dabei herausragende Leistungen zeigen. Im Mittelpunkt seiner Arbeit steht die Entwicklung eines umweltfreundlichen und automatisierbaren Verfahrens zur Herstellung von Wolframfedern für Vakuumsensoren, um die Abhängigkeit von externen Lieferanten und den Einsatz von Chemikalien zu vermeiden. Diese Anerkennung unterstreicht seinen innovativen Ansatz zur Lösung kritischer Herausforderungen in den Bereichen Technik und Nachhaltigkeit.
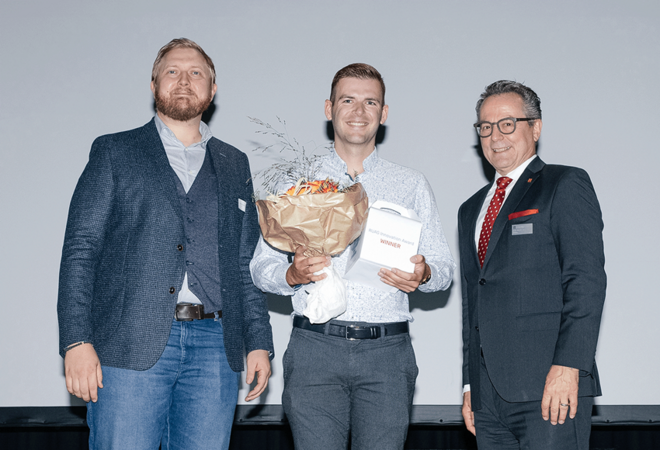
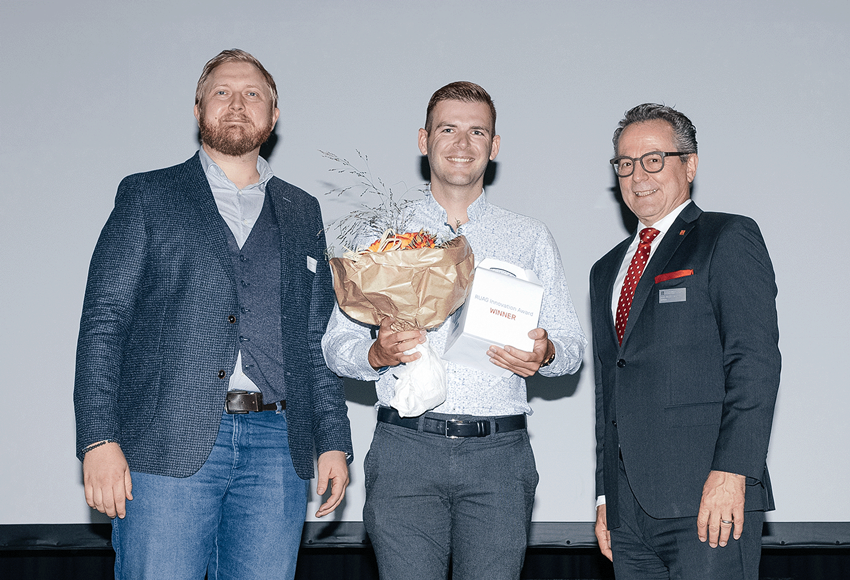
Dominics Schwerpunkt: Nachhaltige Herstellung von Wolframfedern
INFICON verwendet für die Vakuumsensoren Wolframfedern als Sensorelemente zur Messung des Vakuumdrucks. Derzeit werden diese Federn von einem externen Hersteller bezogen. Sie bestehen aus Wolfram, das um einen Molybdänkern gewickelt und anschließend auf die gewünschte Länge zugeschnitten wird. Danach wird der Kern durch Ätzen mit Königswasser entfernt. Diese Abhängigkeit von einem externen Lieferanten sowie der gefährliche und umweltschädliche Ätzprozess sollen vermieden werden. Zusätzlich greift das Königswasser das Wolfram allmählich an, was die Qualität der Federn beeinträchtigt. Der Einsatz von Königswasser sowie die Dauer des Ätzprozesses erschweren zudem eine Automatisierung, sowohl technisch als auch wirtschaftlich.
Ziel dieser Arbeit ist es daher, Wolframfedern umweltfreundlich und in Eigenproduktion herzustellen. Hierfür wurde ein Wolframdraht mit einem Durchmesser von 10 µm verwendet, aus dem eine Feder mit einem Durchmesser von 150 µm und einer Steigung von 50 µm gefertigt wurde mit einer Länge von 2cm. Um die Formstabilität der Feder zu gewährleisten, muss sie Erhitzt werden. Zunächst wurde ein geeignetes Kernmaterial ermittelt, das eine einfache Trennung der Feder vom Kern ermöglicht und zugleich für die Erhitzung der Feder geeignet ist. Verschiedene Materialien wurden in einem Versuchsaufbau getestet, wobei sich eine Glasfaser mit Polymermantel als die beste Lösung herausstellte. Um die Form der Feder zu stabilisieren und Oxidation zu verhindern, wurde eine spezielle Box konstruiert, die kontinuierlich mit Argon gespült wird. Die Erwärmung der Feder erfolgt durch elektrischen Strom, der an beiden Enden angelegt wird. Für die mechanische Verarbeitung des Drahtes ist es essentiell, dass er stets unter Spannung steht. Durch eine präzise Drahtführung und innovative Klemmmechanismen kann der Draht automatisiert verarbeitet und gewickelt werden. Der Aufbau zeigte, dass es möglich ist, eine Feder ohne den Einsatz von Chemikalien herzustellen. Zudem können Steigung und Länge der Feder variabel eingestellt werden
Werde Teil von INFICON
Haben Sie sich von Dominics Weg und Geist inspirieren lassen und denken Sie über eine Karriere bei INFICON nach? - Machen Sie den ersten Schritt und erfahren Sie mehr über eine Karriere bei INFICON und die aktuellen Stellenangebote.
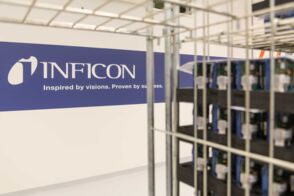
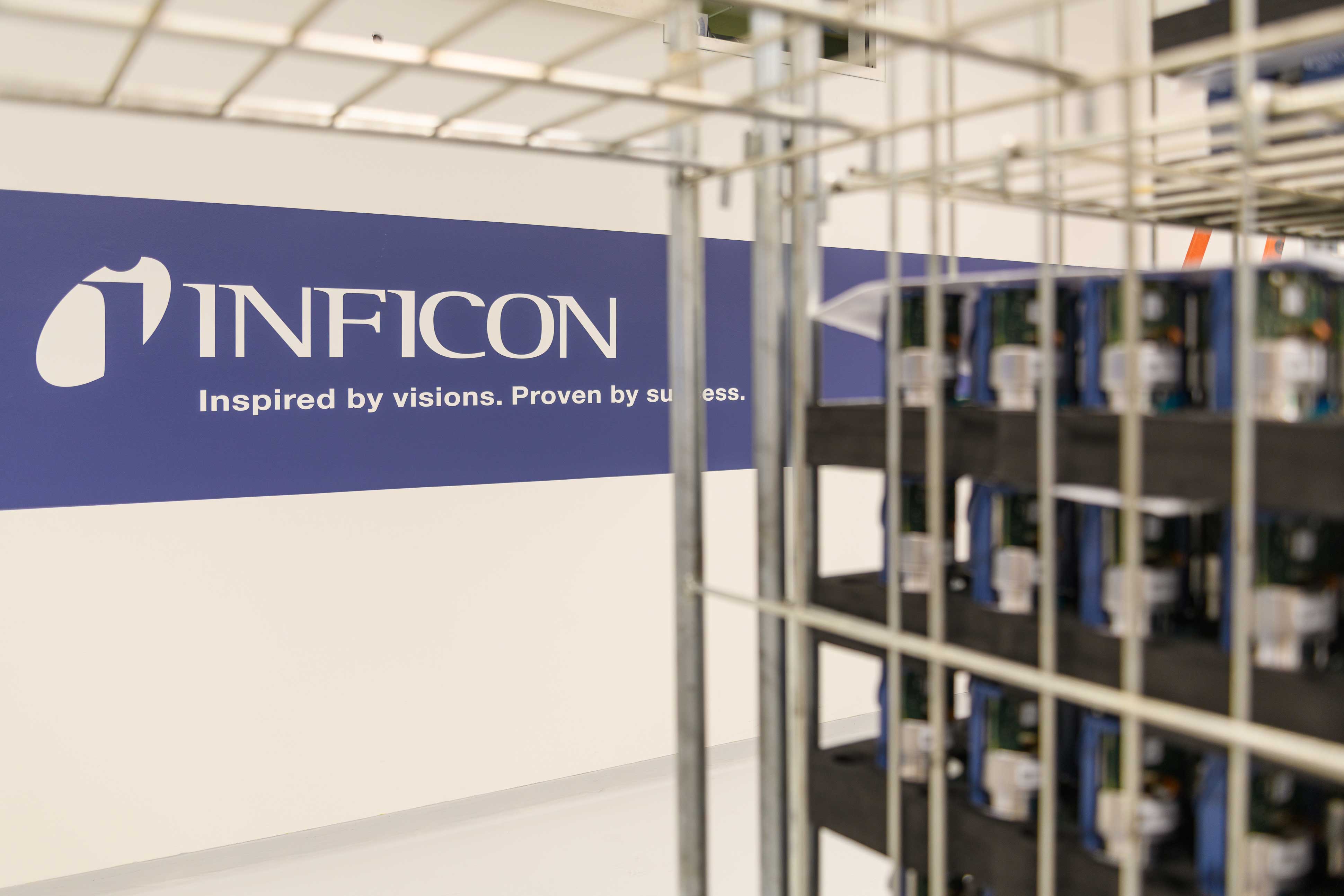
Verwandte Artikel
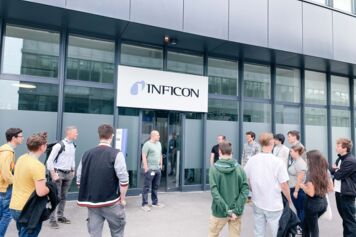
INFICON war Teil des jährlichen Photonic's Day der Fachhochschule Graubünden, Schweiz.
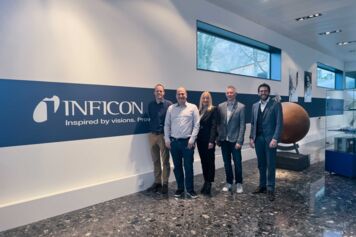
Ein Hochschulstudium mit integrierten Praxisphasen in einem Unternehmen – das ermöglicht eine Kooperation mit der Fachhochschule Graubünden. Dieses sogenannte duale Studium legt den Fokus auf eine praxisnahe Ausbildung sowie die Kombination von Studium und Arbeit.