Industrial Manufacturing
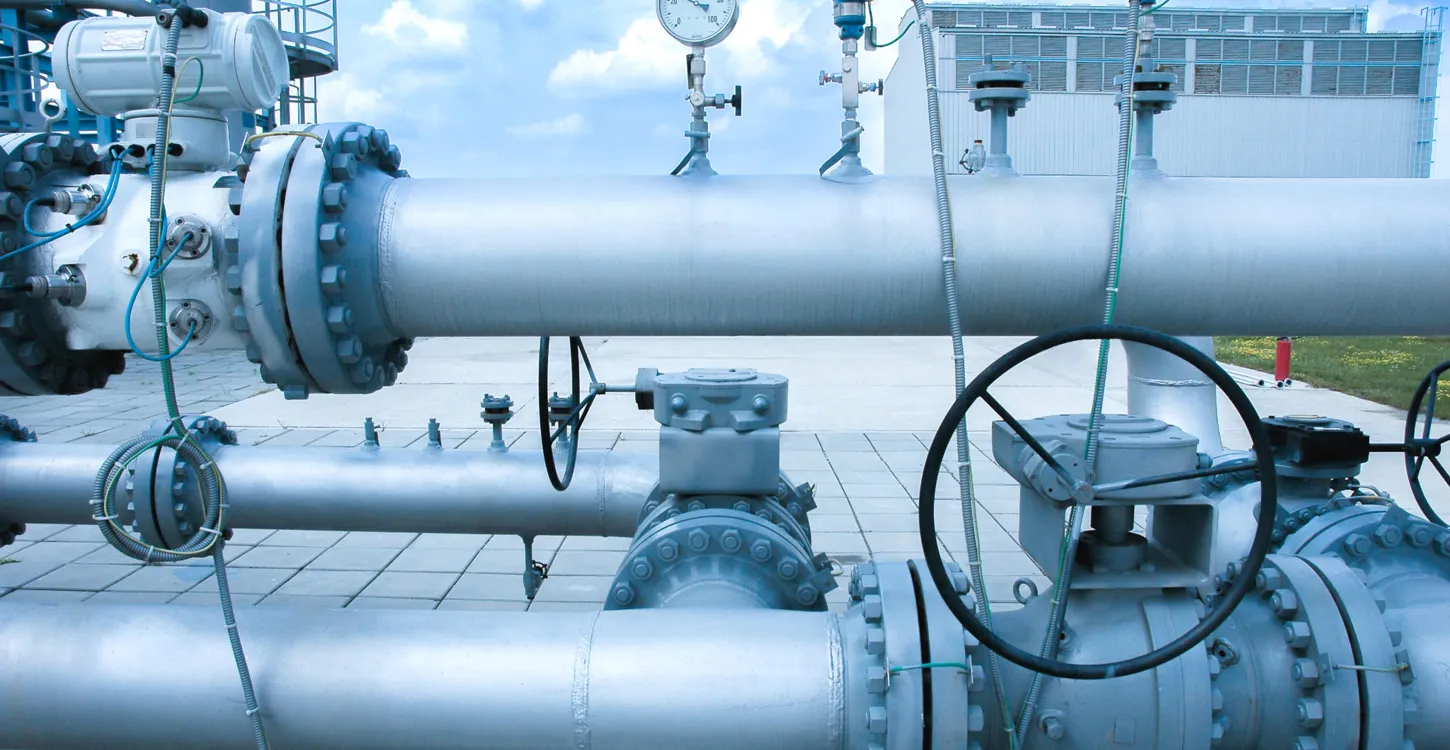
The industrial manufacturing industry is responsible for the fabrication of products intended for industrial use. Vacuum is used more often to guarantee a clean environment and is needed for several processes, that would not function properly without vacuum. With our vacuum sensors and leak detectors, we improve the output of this industry which has made further mass manufacturing possible in most other industries.
Industrial manufacturing equipment can be grouped into several submarkets like Vacuum Furnace, Packaging, Insulation Vacuum, Gas Transport, E-beam Welding and Petrochemical. Our reliable and precise measurement products, allow you to maximize your output and thus, create a competitive advantage to avoid customer complaints.
Submarkets
Vacuum furnace as a controlled heat treating or furnace environment is required for accurate process control. RGAs are used to monitor "vacuum quality" while vacuum gauges are required to both measure and control pressures from Atmosphere to pressures as low as 10-11 mbar. Leak detectors are used for troubleshooting the vacuum systems themselves as well as leak checking individual high quality parts. To complete this portfolio, we also offers a large selection of vacuum components like ISO-KF, ISO-K and CF. INFICON supplies a wide range of products to meet the needs of even the most demanding vacuum processes.
INFICON offers a wide portfolio of products for vacuum pressure measurement, gas analysis solutions and leak detectors for final test of the insulation. Today, technical gases are required in large quantities for countless processes. Depending on the type of gas, it may be necessary to store the gas in liquid form, usually in cryogenic temperature ranges. For example, classic industrial gases such as nitrogen are kept at a constantly low temperature level in large insulated containers to keep them liquified and thereby be able to store much higher quantities per volume. A high degree of tightness of the insulated container is essential and protects the liquified gas from the influence of ambient heat. Failure of the vacuum insulation runs the risk of the contents heating up with consequent rise in pressure.
Demand for environmentally friendly natural gas as a fossil fuel will continue to increase over the long term. More than 40% of total natural gas transport volumes traded and transported worldwide is liquefied, which reduces transport volumes by a factor of 600. The LNG process chain consists of natural gas production, purification and liquefaction, ship loading, transportation and subsequent off-loading, storage and regasification, and, ultimately, injection into a gas distribution grid. The majority of gas is distributed with gas pipeline. The testing of natural gas requires fast and precise analysis of fixed gases and light hydrocarbons and reliable leak detections for easy and effective survey of gas pipeline.
Electron beam welding can also be used to weld metals with high melting points (such as tungsten) as well as active metals that may oxidize during welding (such as titanium). It is a fusion welding process whereby electrons are generated by an electron gun and accelerated to high speeds using electrical fields. This high speed stream of electrons is tightly focused using magnetic fields and applied to the materials to be joined. This process is under vacuum and needs vacuum pressure measurement and leak detectors to guarantee high uptime of welding tools and to fulfill high quality requirements.
Traditional oil and gas production has seen an increase in demand over the last several decades and is being propelled by population growth, urbanization, and the consumer middle class in developing countries. Technological advances have reduced exploration and processing costs, thereby capping energy prices and solidifying fossil fuel as the primary source of energy.
In addition, there is a growing interest in alternate energy, a broad category composed of various sources of non-fossil based fuels including: hydrogen, syngas, biomass, and biomethane. Of particular interest are renewable, or sustainable, fuels able to provide clean, efficient, and economical alternatives to traditional oil, gas, and coal.
Using a gas analyzer for component monitoring and compositional analysis ensures that energy is produced in a safe and economical manner. The highly configurable Micro GC Fusion Gas Analyzer meets gas analysis needs for a wide variety of energy applications including: natural gas, refinery gas, catalyst research, biomethane, biomass, and syngas.
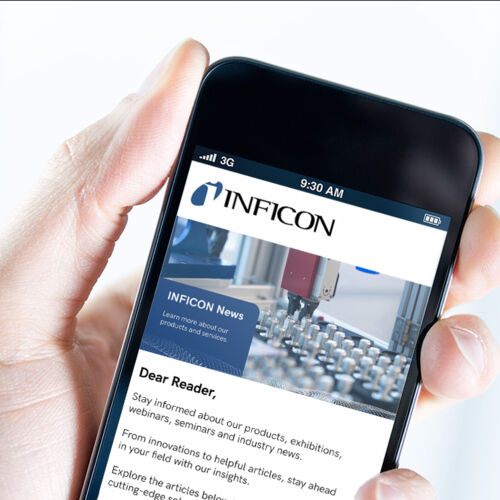