Automated leak test system for bipolar plates
EcoBoost enables testing in spite of fluctuating helium background
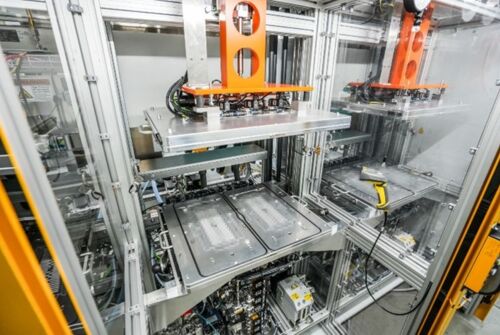
The EcoBoost function (formerly I∙ZERO) patented by INFICON is ground-breaking. This is because, for the first time, it dynamically determines the helium background remaining after evacuation during a vacuum test with helium as the test gas - and not statically, as all previous Zero functions do. INFICON's new software algorithm takes into account the development of the background in each of the past two seconds and, on this basis, constantly extrapolates how high the background is that needs to be calculated out of the current helium measurement. The positive effect is that with EcoBoost, it is now possible to:
- measure much earlier, after shorter evacuation
- check against smaller leak rates, which would simply disappear in a statically determined background, or even in vacuum chambers, whose dead volume would otherwise be too large for smaller test parts.
- enjoy cost-savings with highly diluted helium test gas
Dynamic background compensation is also used in practical scenarios where background contamination with helium is almost unavoidable. Worthmann Maschinenbau GmbH provides the prime example with its system for leak detection on bipolar plates.
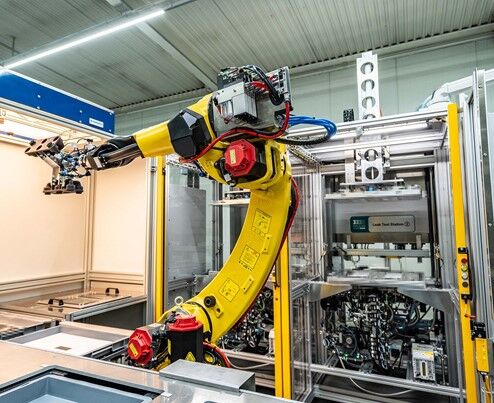
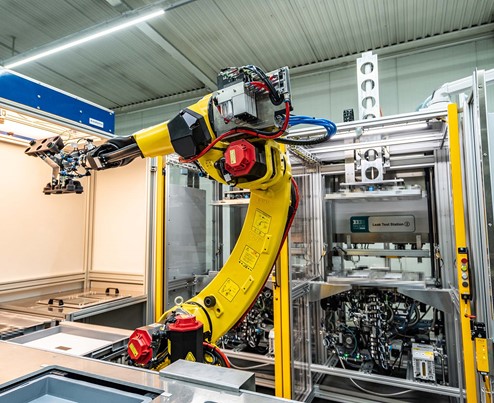
An unavoidable helium background
In fact, Worthmann Maschinenbau GmbH or its subsidiary MACEAS was one of the very first users of the EcoBoost algorithm - in combination with INFICON's LDS3000 leak detector.
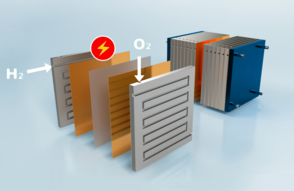
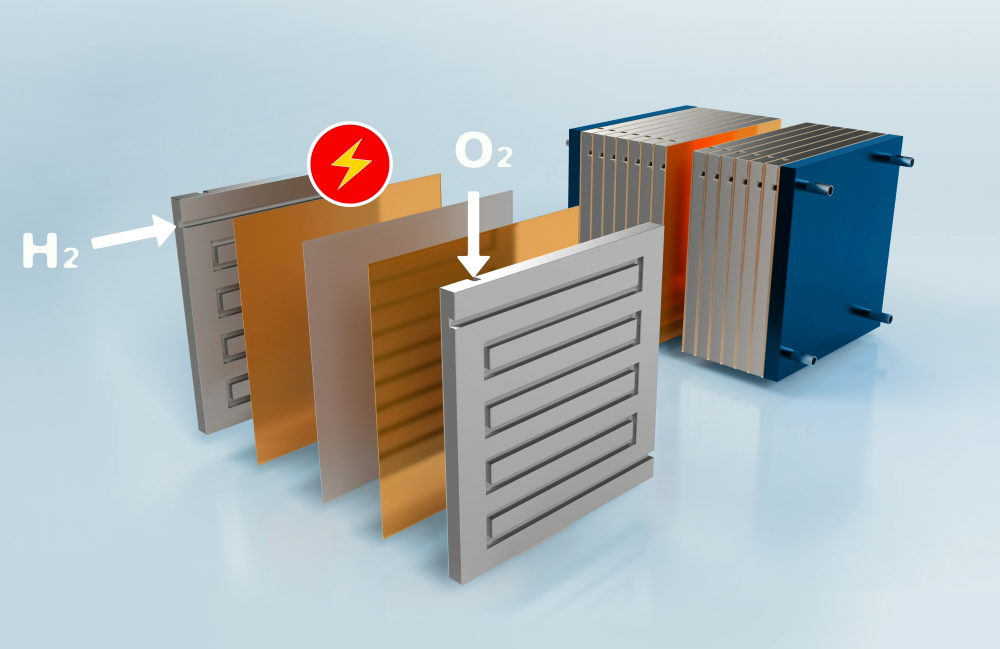
For the complex testing tasks in the field of fuel cell bipolar plates, MACEAS engineers have designed and built a new system for a customer that performs the tests on the three circuits of a bipolar plate in immediate succession. Bipolar plates are the heart of a hydrogen fuel cell. Stacked in hundreds, bipolar plates form the so-called fuel cell stacks that are installed in vehicles. Each bipolar plate contains three channels: two for the process gases hydrogen and oxygen and one for the coolant circuit. It is essential that these three channels are reliably leak-tight both to the outside and to each other.
A modular leak tester for bipolar plates
MACEAS has designed the new helium leak tester for bipolar plates in a modular way. A system consists of at least one main module, which also includes a control cabinet and the operating elements. However, the system can be expanded as needed, and robot-assisted, fully automatic loading is also possible. Typically, two bipolar plates are inserted into the actual test chamber. Once the two bipolar plates are in the system, a mold closes around the two plates. This tool itself forms the vacuum chamber for the leak test to the outside. At the same time, it seals and valves allow the relevant channels of the plate to become vacuum chambers for the test themselves, one after the other. For cost reasons and to keep the helium background low, MACEAS does not work with pure helium gas here: the system itself produces a test gas mixture with 10 percent helium. However, in order to be able to test with such diluted test gas, the system must also be more sensitive by a factor of ten than when testing with pure helium. The smallest limiting leak rate against which the system can test the tightness of the bipolar plates today with INFICON's LDS3000 leak detector is at a helium leak rate of 1 ∙ 10-5 mbar∙l/s at 10 percent helium concentration.
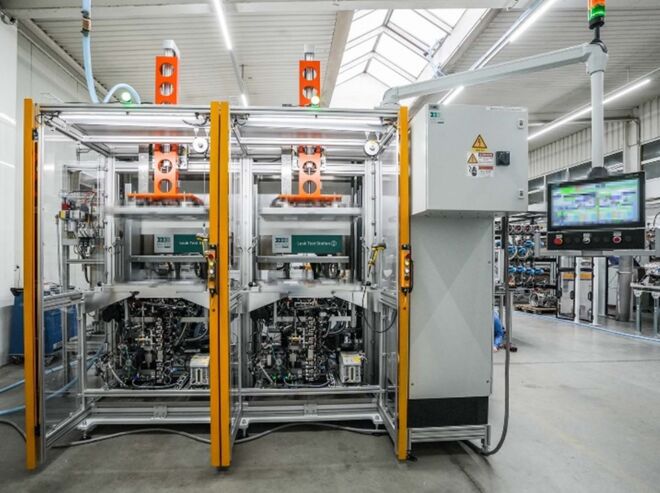
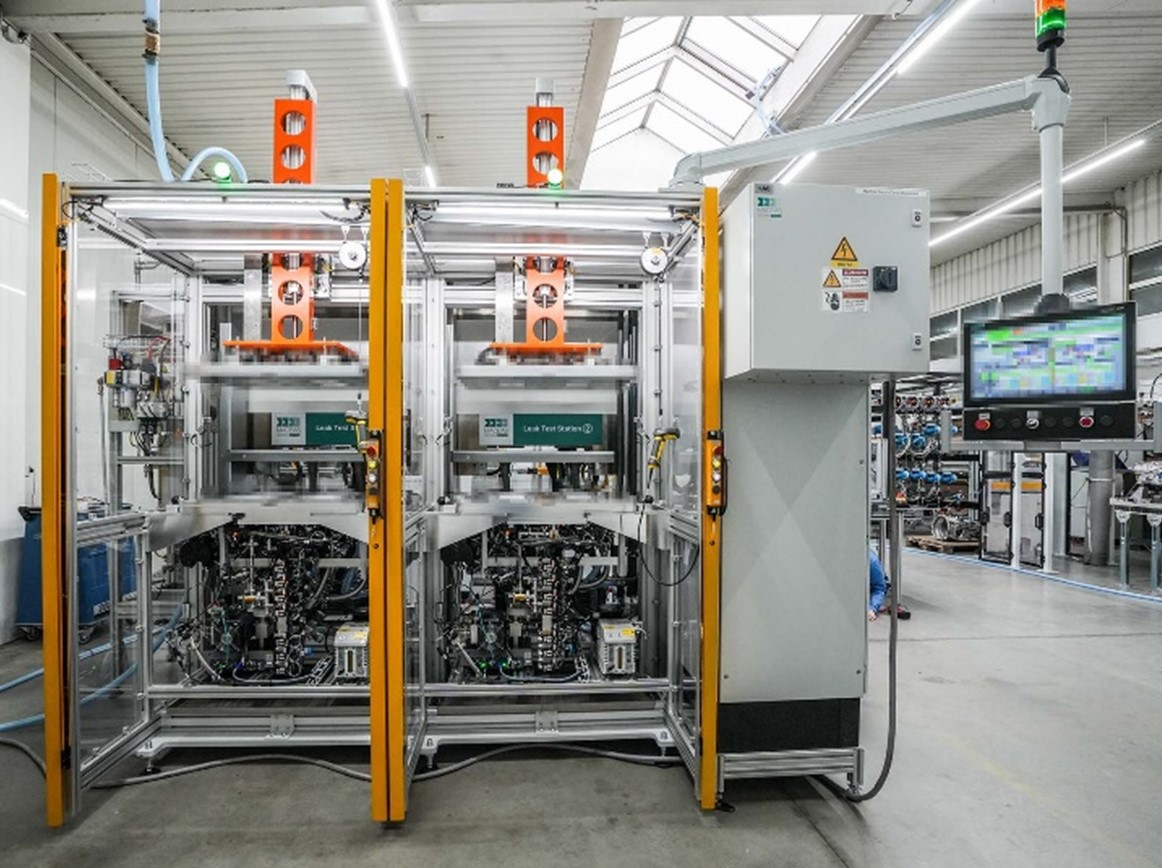
Surprising helium peaks during evacuation
In developing the new test system for bipolar plates, however, the helium background initially proved to be a challenge for MACEAS. There was no continuously falling and then stable helium background during evacuation, but surprising peaks. The plant engineer identified the dead spaces in the test chamber and also in the moulds as helium sources. In order to eliminate these helium sources, MACEAS relied on structural measures, designed new guides, modified the valve technology and installed larger turbomolecular pumps. The fact that INFICON was currently working on a prototype EcoBoost was a stroke of luck for the plant manufacturer. This was another reason why it was possible to get control of the helium background and significantly shorten the evacuation time. Before each of the total of three test processes on a bipolar plate, the plant now carries out a dynamic and continuous determination of the helium background concentration using the EcoBoost function. The result: cycle times that are as short as possible.
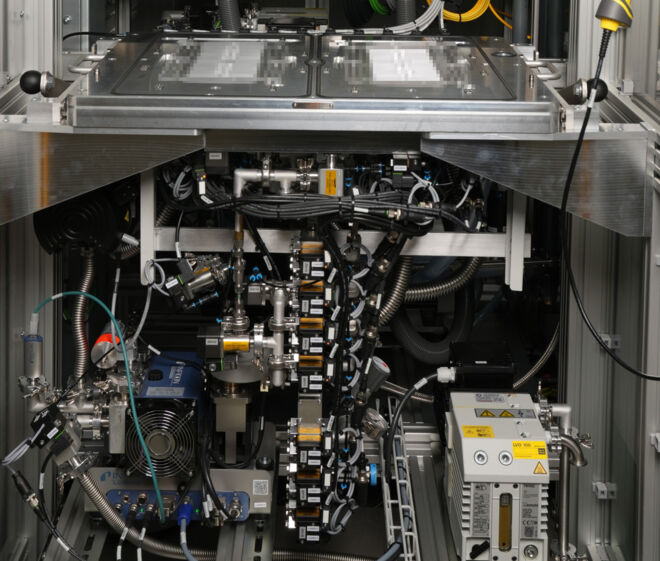
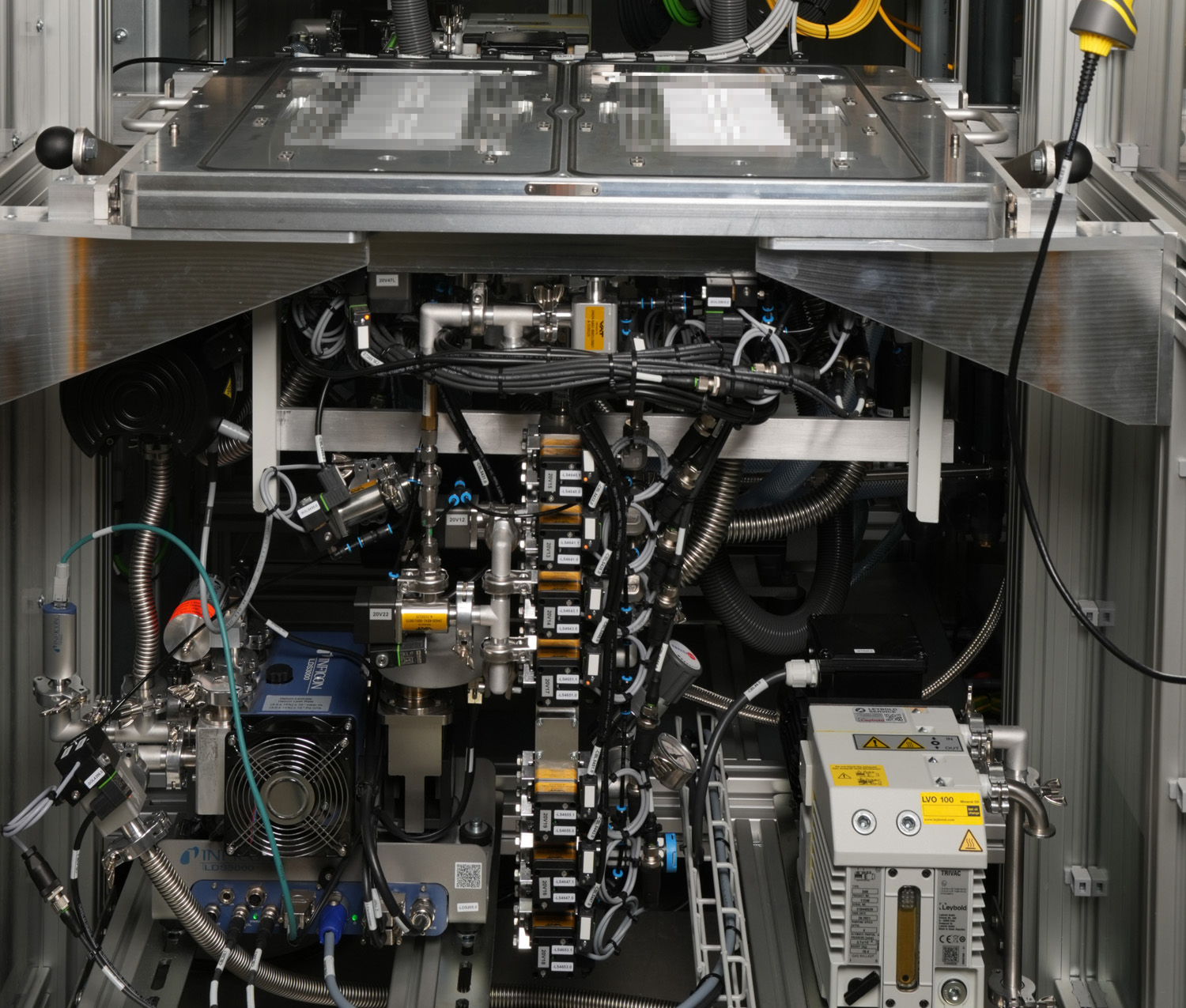
Cycle times down to 12 seconds - thanks to EcoBoost
The entire test cycle consisting of feeding the system, three evacuations and three test processes now takes just 48 seconds. This means that the system effectively tests a bipolar plate in one station every 24 seconds. And because each main module can be extended by a secondary module, throughput is doubled again. This results in an effective cycle time of 12 seconds - which corresponds to 300 bipolar plates per hour. Daniel Schönbohm, Sales Manager at Worthmann/MACEAS, puts it this way, "Being able to test faster with EcoBoost is always an advantage from a cycle time perspective."
To learn more about the EcoBoost function of the LDS3000, watch our on-demand webinar or call you nearest sales representative.