How Proper Calibration Can Improve the Quality of Your Production
Simple moves with big impact.
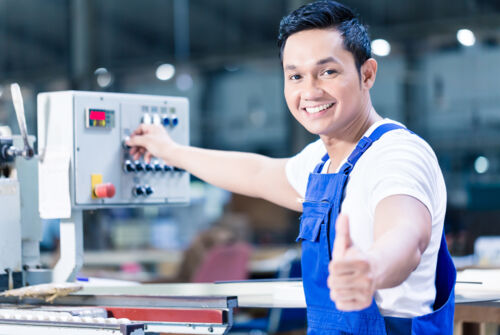
David Xu, a diligent and dedicated production engineer working at a renowned lithium-ion battery cell manufacturing company has a crucial responsibility: he is in charge of conducting helium leak testing on battery cells before they are filled with electrolyte.
To carry out this important task, David is relying on an automated helium leak testing system that has been designed by his colleagues in the system integration department. However, despite using this high performing system, quality problems persist. Some battery cells fail the end-of-line test or encounter issues shortly after being shipped, leading to warranty claims and customer dissatisfaction.
Determined to resolve these issues, David decided to investigate the problem further. He realized that the key might lie in the calibration process of the helium leak testing system. In collaboration with his colleagues, David ensured that the system was calibrated at the beginning of each shift using a test leak that matched the smallest leak they needed to detect.
Despite their efforts, the quality problems remained, and David became increasingly frustrated. It was then that he stumbled upon a helium leak testing webinar that proved to be an eye-opener. The webinar highlighted the importance of the placement of the test leak.
Curiosity piqued, David inspected the setup of the helium leak testing system and discovered that the test leak was installed very close to the leak detector inlet. Recognizing the potential impact of this configuration on the accuracy of the results, David immediately reached out to his system integration department.
Together, they first tried to connect the test leak directly to the chamber and then to initiate measurement. To their surprise, the system failed to detect the leak. This could only mean that there might also be a problem with the leak detector. Determined to solve this issue, they decided to exchange the leak detector and to re calibrate the system with the test leak attached to the chamber. This time, the system successfully detected the leak, confirming their suspicion that the previous setup wasn’t as performant as expected and now being sure that they finally have a proper measurement time and a successful calibration of the system.
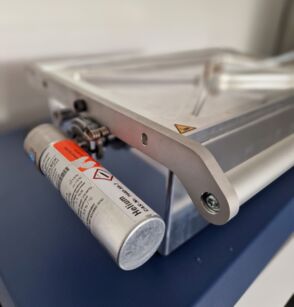
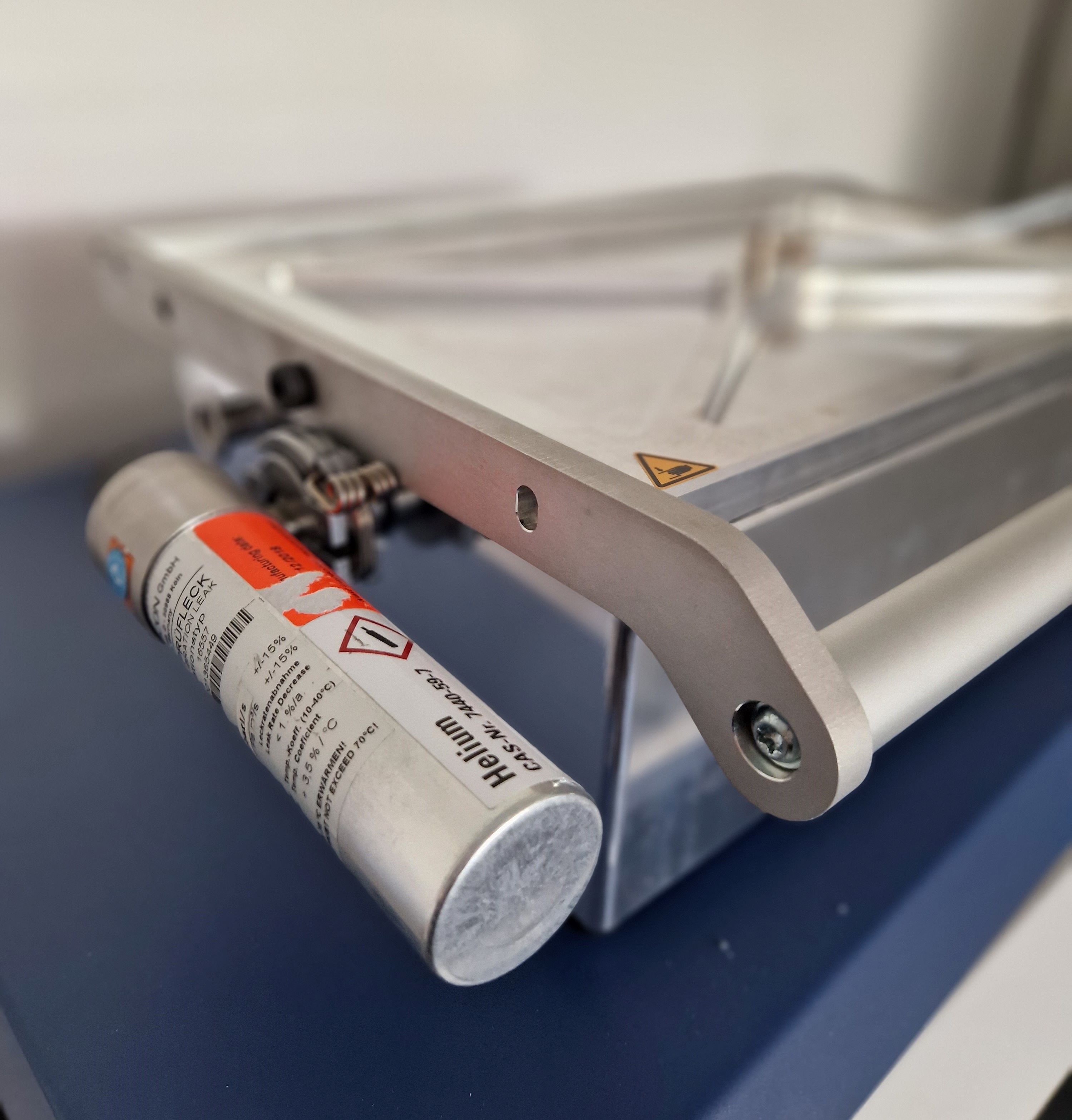
With the implementation of this process changes – new leak detector and location of the leak test directly at the chamber, the company witnesses not only a significant reduction in battery failures during the end-of-line test but also early field failures. The battery tests are more reliable and eventually meet the quality standards that customers are expecting.
Recognizing David's commitment, problem-solving skills, and contribution to improving the company's product quality, he got a QA reward for this great accomplishment. His dedication and perseverance had not only resolved a critical issue but also brought great recognition for his job.
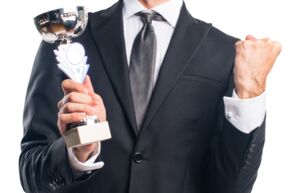
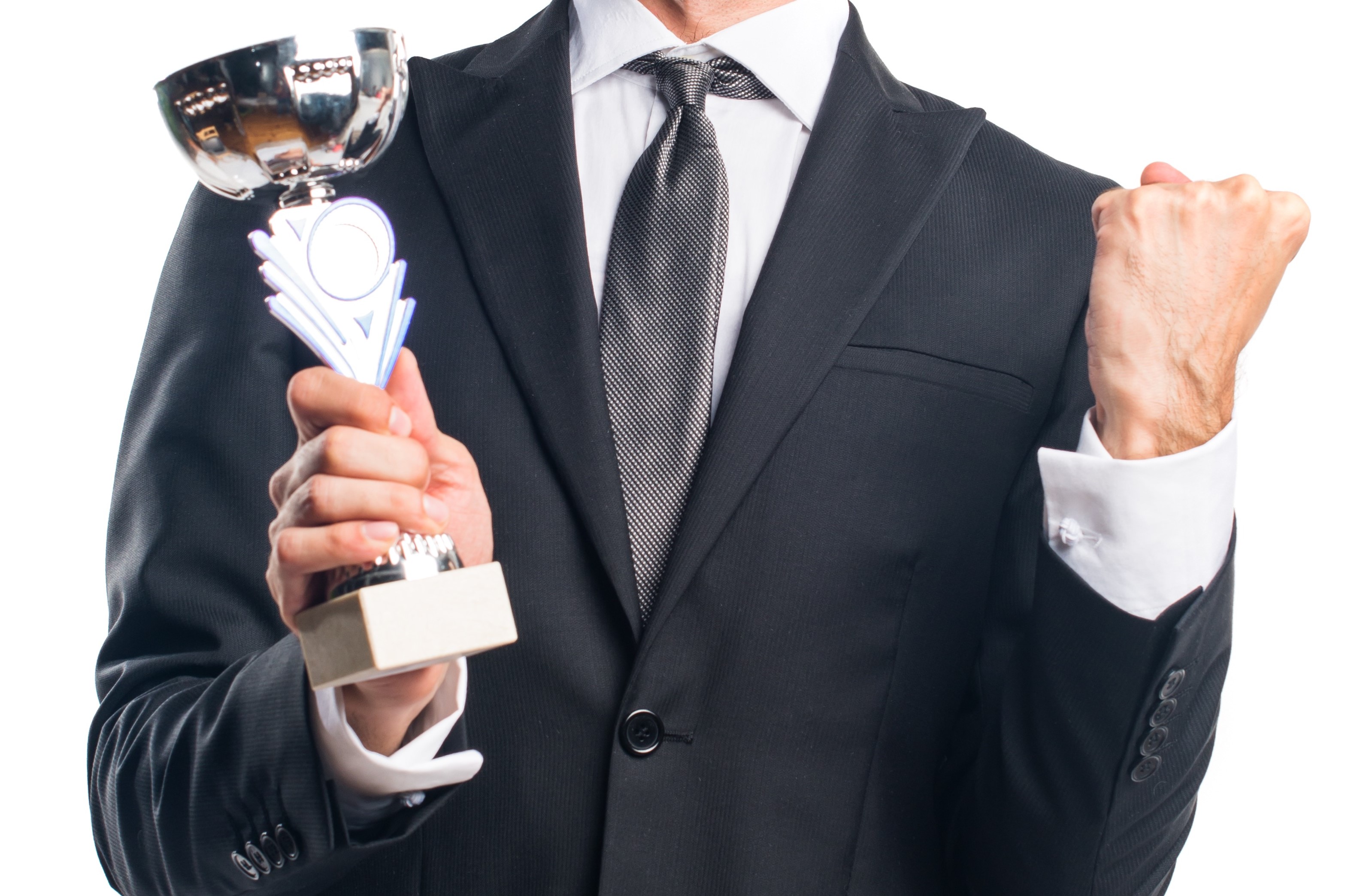
And so, David Xu's story serves as a reminder of the importance of continuous improvement, attention to detail, and the impact that even small changes can have on overall product quality.