From Soap Spray to Tracer Gas: The Path to Faster Leak Detection
The tracer gas leak detection method helps finding smaller leaks much quicker, than bubble test or leak detection spray
Bob is a quality technician working at a major automotive supplier in the US. In his daily job, Bob is responsible for checking electric battery cases for leaks. He is new at this position and enthusiastic about working with the vehicles of the future. Assuring electric vehicles run efficiently gives Bob a great feeling of job satisfaction.
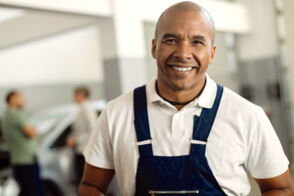
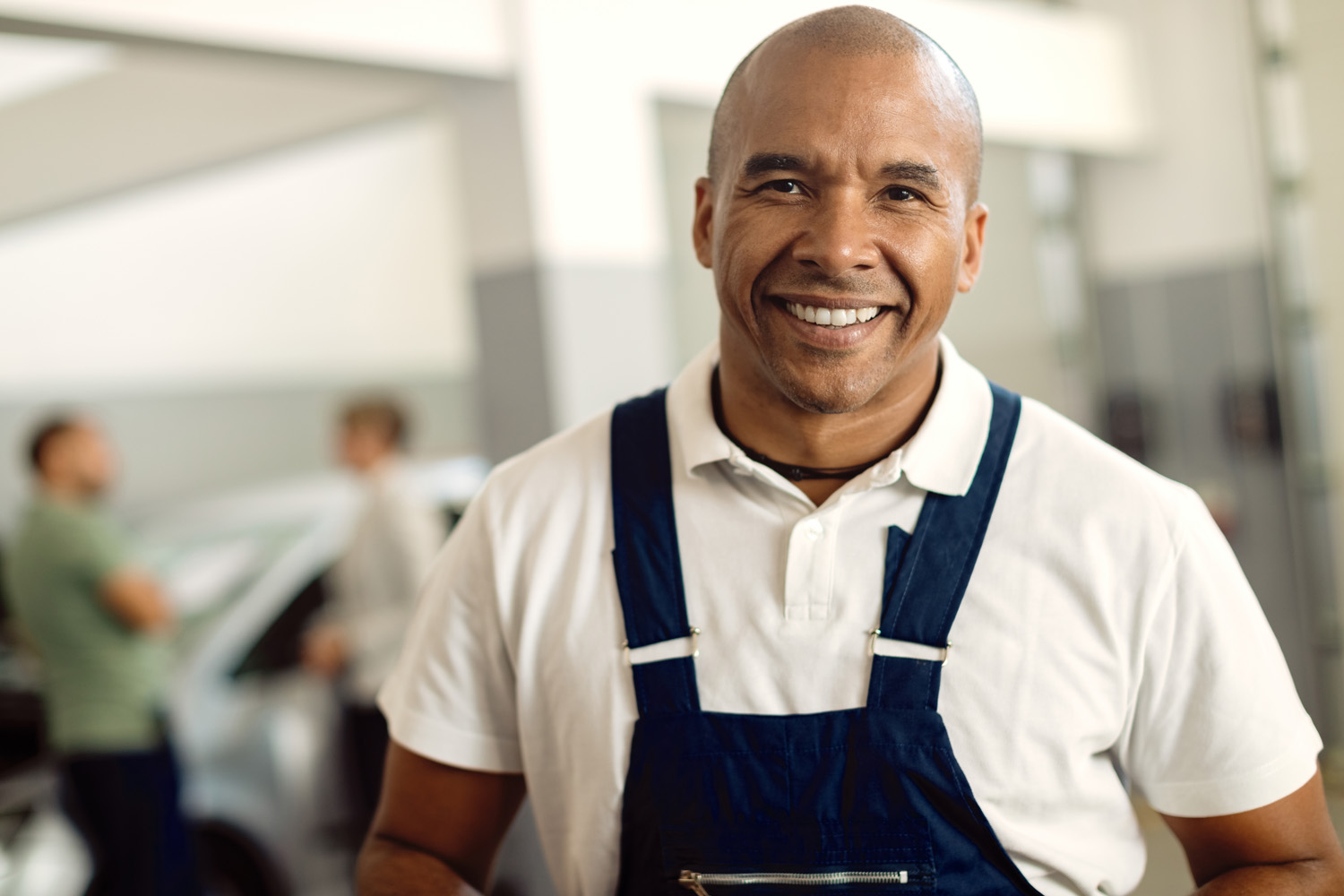
When he started, Bob’s company was performing bubble tests and using leak detection spray for finding leaks. Soapy water is cheap and easy to use, and time and money saving is important in today’s fast manufacturing processes. Bob simply applied the leak detection soap and looked for leaks. As air coming out of a hole makes a bubble, he understood that “No bubble means No leak” and that a “Yes bubble means Yes Leak.” He was trained to inspect fittings first, since those caused most of the faults. In addition, he inspects accurately every suspected leak point. He was also trained to be very careful to dry the batteries, both inside and out, after the test, as any soap water left could cause corrosion. At the end of the day, he also cleans-up his working station as soap water leaves residue on the floor, which can result in a safety hazard.
Unfortunately, with soapy leak tests, tiny leaks are tough to catch. Bob realized after a while that this simple testing method would not find all the leaks, even though most of them were big and easy to locate. Also, he was annoyed by the fact that battery cases got soaked inside. He considered trying leak testing alternatives but his boss said soap was the correct method to use.
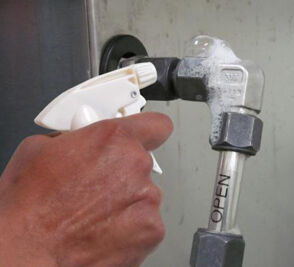
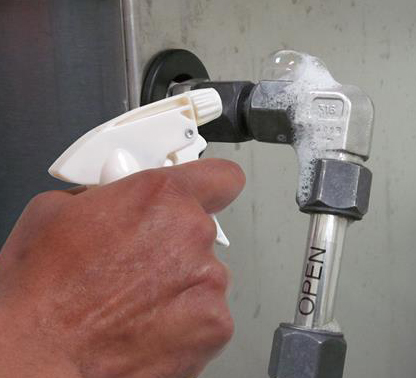
Bob was convinced there would be a better way to test the battery cases reliably and quickly. Complaints from customers regarding rusted connections/fittings, as well as the time needed to dry each case inspired him to look for alternatives. He was not convinced that the cars of the future should be tested with soap and water.
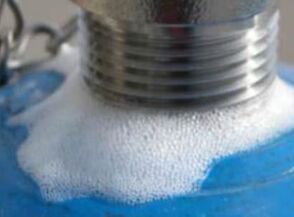
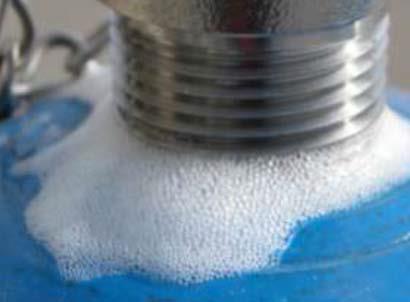
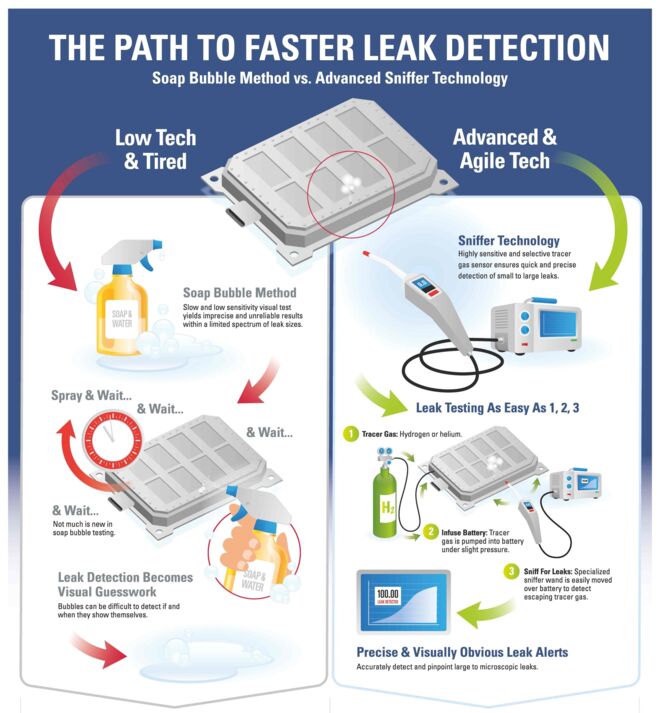
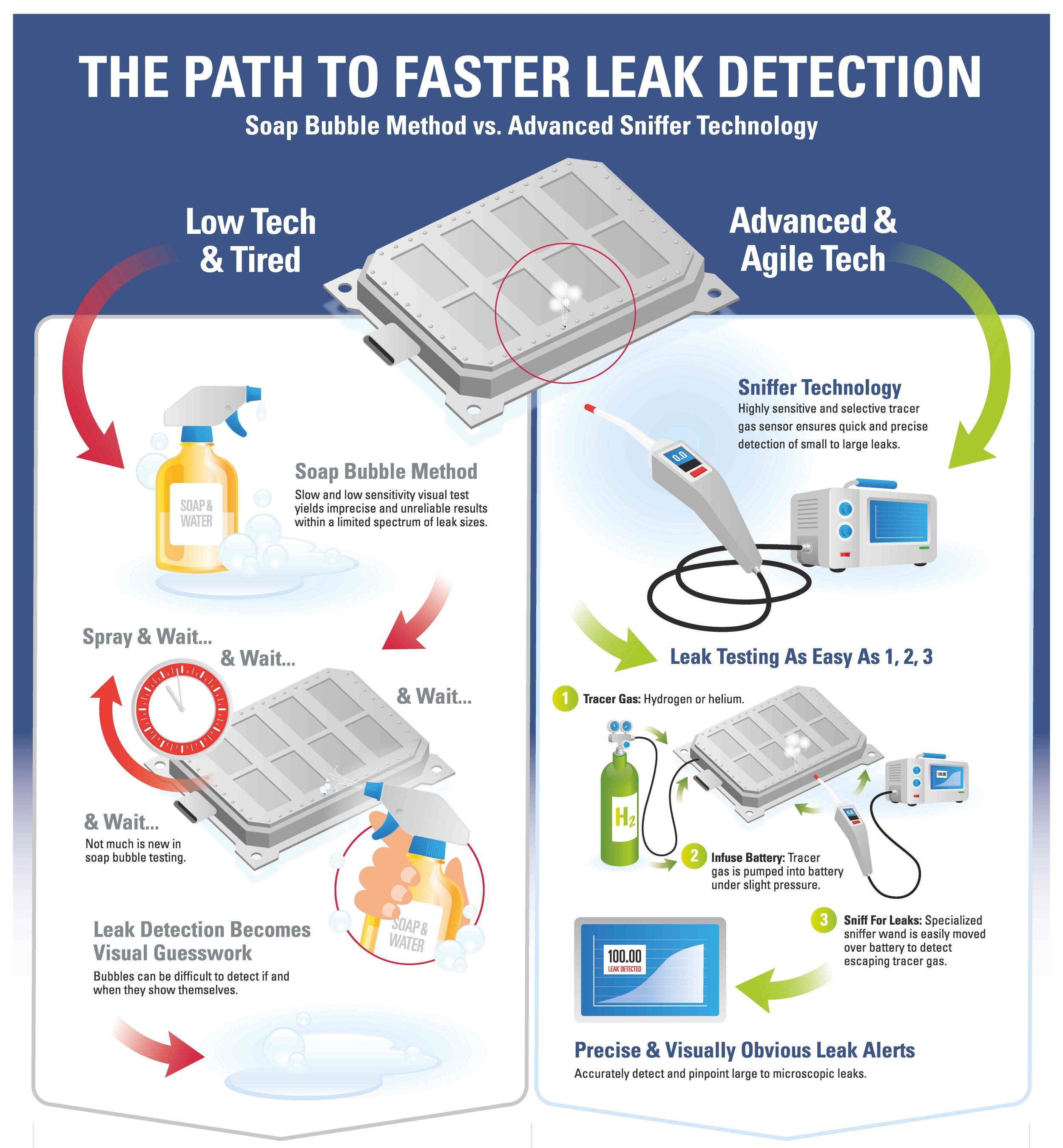
After some quick research, Bob found that leak testing with tracer gas was used as standard in many automotive manufacturing applications. Switching to tracer gas leak testing implied higher costs at the beginning, but the investment would soon provide a return on the investment. It would definitely help him catch the smallest leaks, even if located in hard-to-see-places, without wasting time trying to see where exactly bubbles are coming from. Also, he would eliminate the need to clean up the mess left after the test.
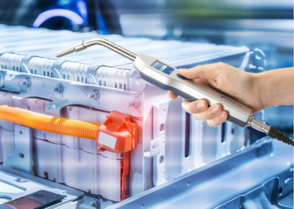
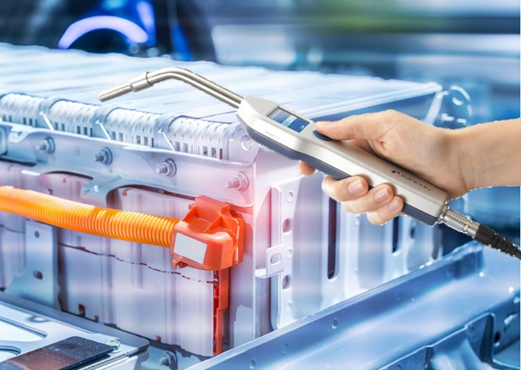
Finding slow leaks quickly was a strong argument in a time where cars have to be produced fast in order to meet the increasing demand. He convinced his boss that tougher leakage limits required innovative test methods and switching from soap water to hydrogen tracer gas leak detection was the right thing to do.
Four months later, the old battery case test standards were replaced by new ones and new, more innovative test instruments were installed at Bob’s test site. One year later, Bob was recognized for introducing the best 3I initiative: Inspect – Improve - Increase.
- Inspected workflow
- Improved quality
- Increased efficiency

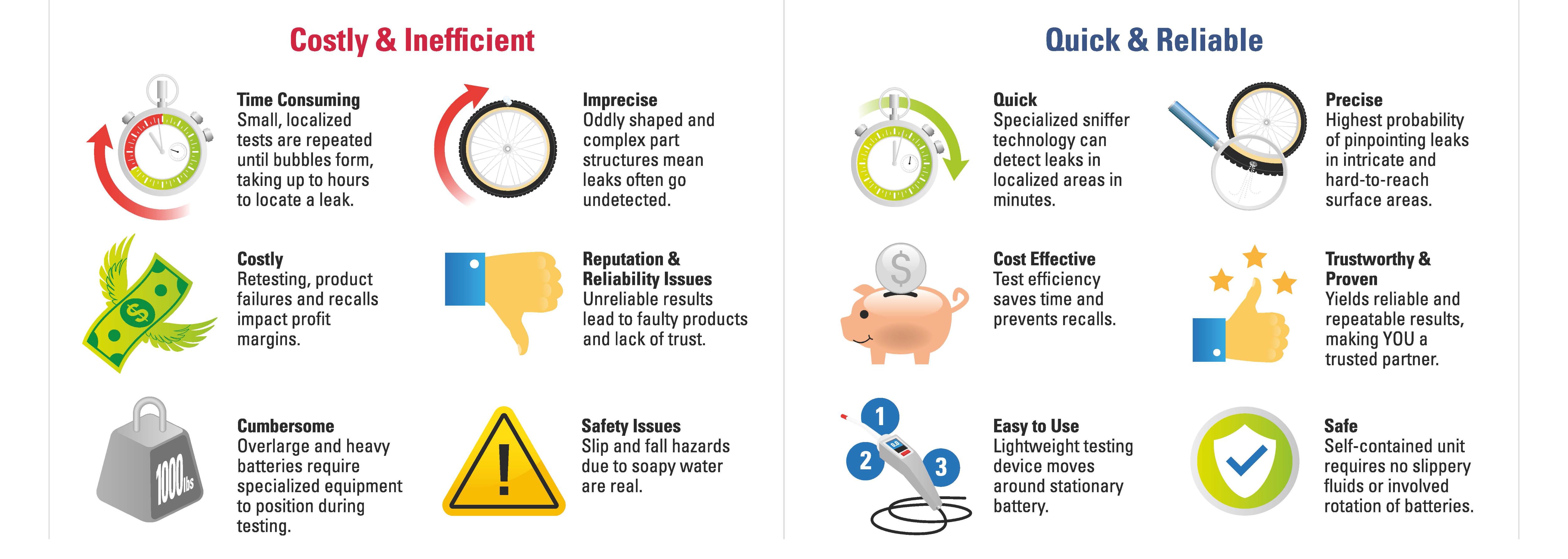
Interested in how you can be successful, like Bob, and accurately test electric vehicles for leaks? Or do you want to know more about the benefits of tracer gas leak detection in automotive manufacturing applications? Read more here.