Detecting Leaks on Heat Pumps in Manufacturing
Prevent refrigerant losses through accurate leak detection
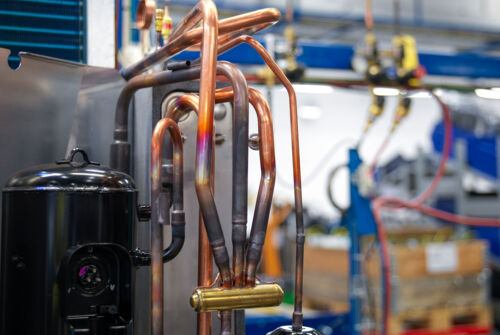
Heating and cooling systems are the largest part of energy use in most homes throughout the world. In Europe, they account for 50 % of total energy consumption. In the attempt to decarbonize the heating sector, heat pumps offer an efficient, sustainable, and progressively more affordable heating alternative replacing traditional fossil fuels such as oil and gas, and contribute to the journey toward a cleaner and more environmentally friendly future. Heat pumps are key to enabling the clean energy transition and achieving the EU’s carbon neutrality goal by 2050.
Leak-free heat pumps for safe, clean and long-lasting operation
Whether for residential, commercial or industrial use, these systems require rigorous leak testing to meet the demands of product life, efficiency and today's environmental concerns. Accurate leak testing, performed during both manufacturing and operation, plays a crucial role to prevent refrigerant loss.
Refrigerant gases like R32, R290 and R410 are used to heat up the condenser in HVAC/R systems, such as heat pumps. Some refrigerants have a big impact on the environment when released into the air. Some gases are flammable and pose a potential risk to the safety of personnel and property. In addition, gas losses affect heating efficiency and result in higher energy consumption.
Besides the environmental aspect, preventing leaks is important to maintain optimal performance and ensure long-lasting operation of the heat pumps. As these systems are designed to efficiently transfer heat, any leaks can compromise their effectiveness and lead to expensive repairs or replacements.
By accurately testing heat pumps for leaks, cost and inconveniences are minimized for both manufacturers and end-users.
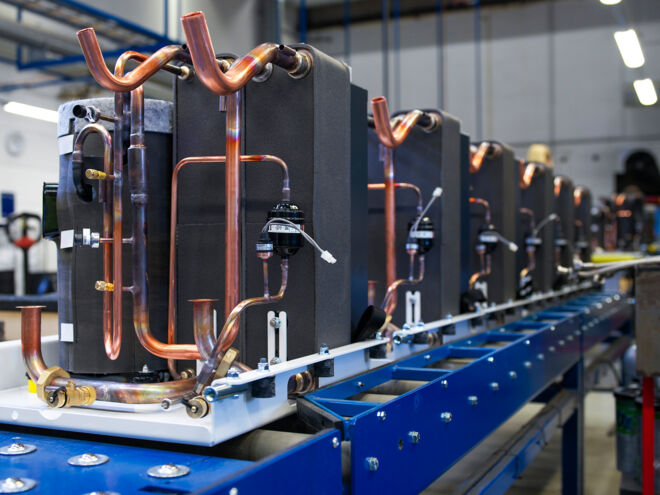
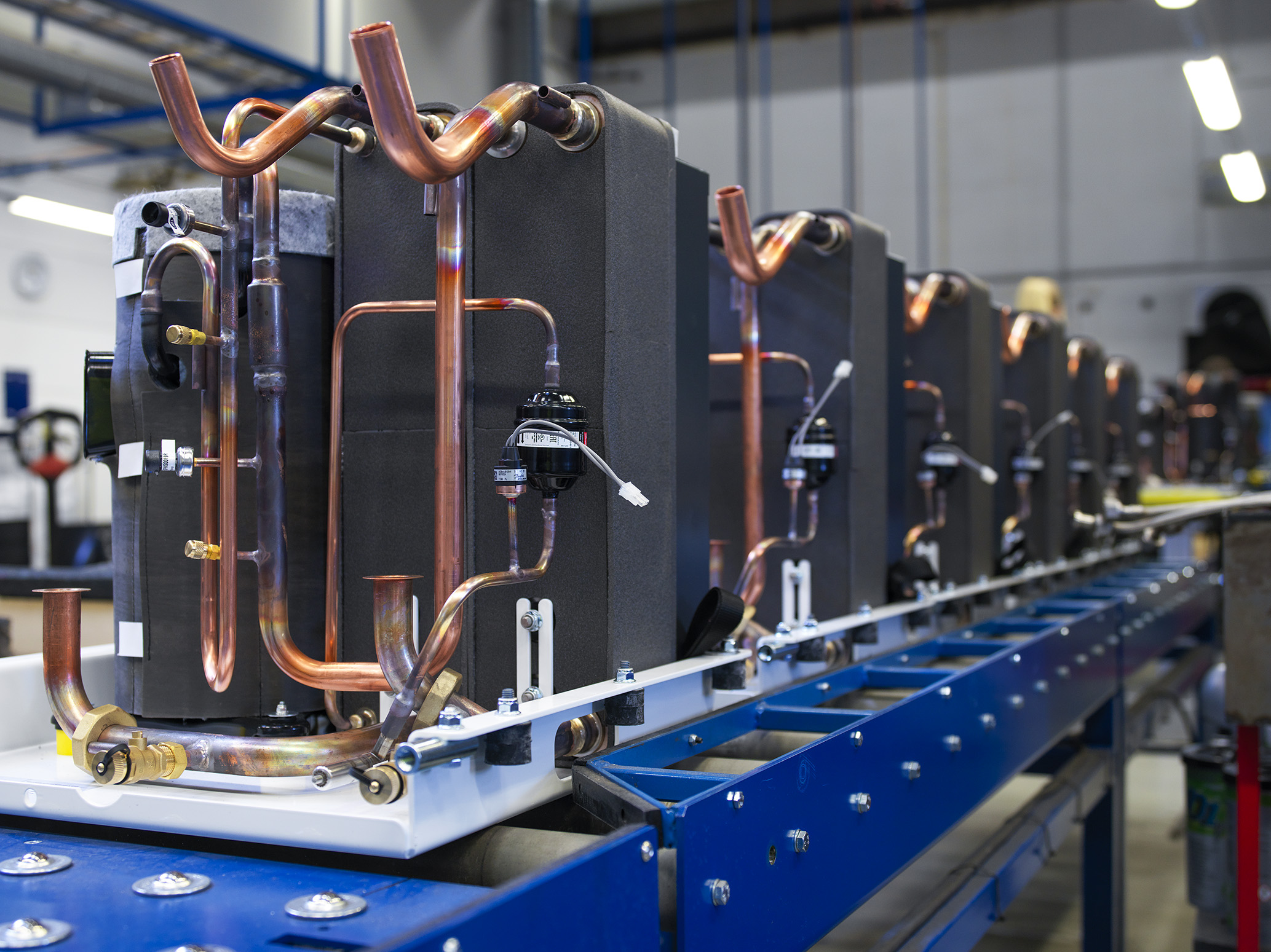
Preventing refrigerant losses through accurate leak detection
Heat pump assemblies are made up of individual components such as compressors, heat exchangers, pipes and various smaller components that must also meet the strict leak rate criteria as they are a part of the refrigerant circuit.
The leaks are usually caused by poor assembly and manufacturing and cause damage in both the short and long term. Typical leak rates for leak tests in manufacturing processes are set between 1 and 3 gr/y, to meet the heat pump’s calculated lifetime.
In the past, leak detection was usually performed by pressurizing the system with air and monitoring the pressure over a predetermined period of time. A drop in pressure indicated a potential leak. Immersing the heat pump or its components in a water bath or applying a soapy leak-testing solution and looking for bubbles was an easy way to locate leaks after a pressure decay test, for example.
The challenges with these methods are many, starting with sensitivity. Bubble testing can detect larger leaks, but is not suitable for detecting very small ones. Pressure decay measurements are very sensitive to temperature and can therefore give erroneous measurements. In addition, most of these technologies do not allow for repeatable results nor measurement of the leak rate. In many cases, manufacturers have used a combination of these methods to ensure comprehensive leak testing and to meet industry standards.
An accurate method for leak detection on heat pumps implies the use of a tracer gas like helium or hydrogen. By filling the system with gas and detecting any escaping gas, leaks can be easily identified and measured with the help of leak detectors. This method provides highly selective, repeatable results and is now the industry standard. It is a dry (no need to clean up the part), temperature independent and non-destructive method.
In contemporary heat pump manufacturing, individual components typically undergo rigorous testing within a vacuum chamber before final assembly. While this method ensures the quality of individual parts, it presents a challenge when it comes to exact leak location, necessitating additional manual testing and rework during later stages of production.
Once all components are connected or welded together, the heat pump system is filled with refrigerant. At this point, the last welded connections or filling ports need to be tested, — a step not feasible during earlier manufacturing processes. To address this, manual testing is conducted using a leak detector with the requisite sensitivity, ensuring that any potential leaks are identified and repaired before the system is put into operation.
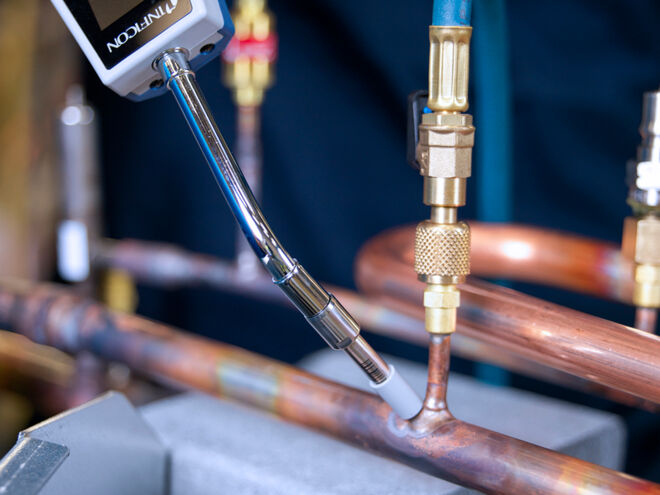
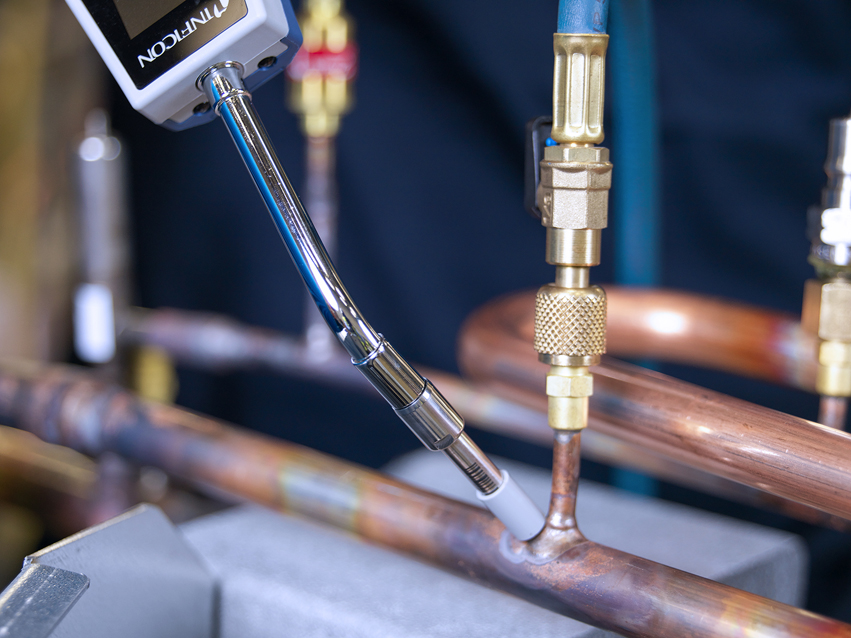
From manual to robotic leak test solutions
INFICON has a wide portfolio of leak detectors and offers manual, automatic and semi-automatic leak test solutions to meet the industry's needs.
The XL3000flex Hydrogen and Helium Leak Detector can be used with either helium or hydrogen, offering the highest sensitivity. The device operates with a gas flow selectable between 300 sccm or 3000 sccm. The high gas flow, 3000 sccm, allows the sniffer tip to be moved over the test piece at some distance and at a higher speed, so even the most inexperienced operators can achieve reliable results.
The Ecotec® E3000 Multigas Leak Detector is specifically designed for demanding production environments. Numerous features make it easy and comfortable to use while making it more immune to careless operation and minimizing operator errors.
The HLD6000 Refrigerant Leak Detector is a compact and lightweight device. It uses a long-life infrared sensor with high sensitivity and extremely short response time, and has been specifically developed for the detection of refrigerant. Two LED lights in the sniffer tip simplify leak detection at poorly lit inspection locations, facilitate precise leak location, and notify the user by flashing when the allowable leakage rate is exceeded.
The Sensistor® Sentrac® Hydrogen Leak Detector is a modern leak detector for industrial use. Based on the highly selective and sensitive Sensistor sensor, the instrument offers leak locating in a variety of situations both on production and repair lines. Thanks to its unique ability to handle small and large leaks as well as high background levels of tracer gas, this leak detector is highly adaptable. For manual, semi- or fully automatic leak testing.
The 3D Robotic Leak Testing System locates very small leaks on pipes with millimetric precision. The system includes a leak detector, equipped with a sniffer tip designed specifically for automation, and a 3D image recognition system. The system not only handles this dynamic localization, but also incorporates optimized path planning to ensure that the leak test is performed within the set cycle time.
Benefits of leak detection with tracer gas
- Improves quality
- All leaks detected, even in hard to access areas
- Fast response time
- Independent of temperature variations
- Fast pin-pointing of the leak position
- No operator interpretation of the leak size
- Repair only the relevant sites (those leaking above the reject level)
- Clean and dry test method
Do you want to know more?
Interested in our leak detection solutions for HVAC/R manufacturing? Check out here
Interested in our tools for HVAC/R and Service? INFICON offers a full line of products for both residential and commercial HVAC/R service. Discover more!