Expanding Horizons: INFICON EDC's Commitment to Quality and Growth
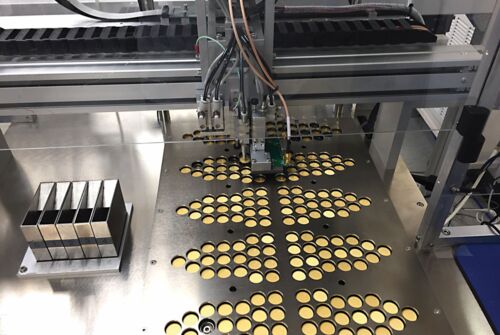
Nestled in the center of the United States in Overland Park, Kansas, INFICON has a dedicated quartz crystal manufacturing facility, INFICON EDC. INFICON EDC has a long history of manufacturing quartz monitor crystals to the highest standards of quality assurance for a global market.
From the beginning
EDC (Electro Dynamics Crystal Inc.) was started in 1963 to produce high-quality, high-volume quartz crystals for the consumer electronics and automotive industries. In 1992, in response to market demand, EDC began offering crystals for thin film deposition monitoring. As a result of this new offering, EDC became a supplier to INFICON in Syracuse, New York. The partnership between EDC and INFICON continued to strengthen over the years and culminated in INFICON acquiring EDC in 2006. The newly acquired company was incorporated as INFICON EDC, Inc.
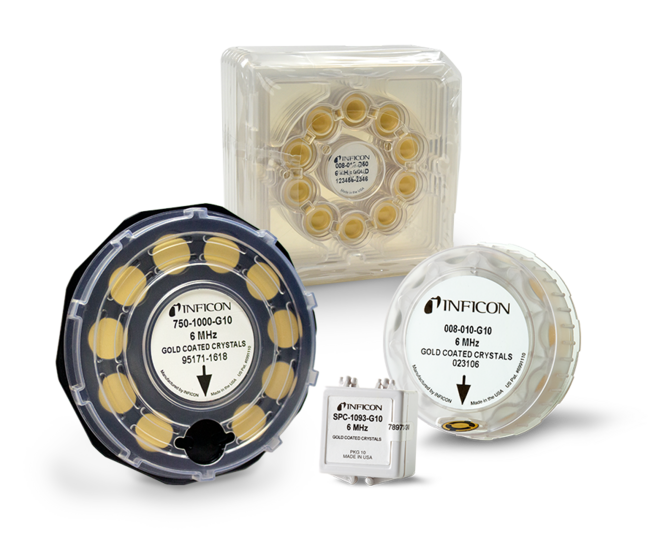
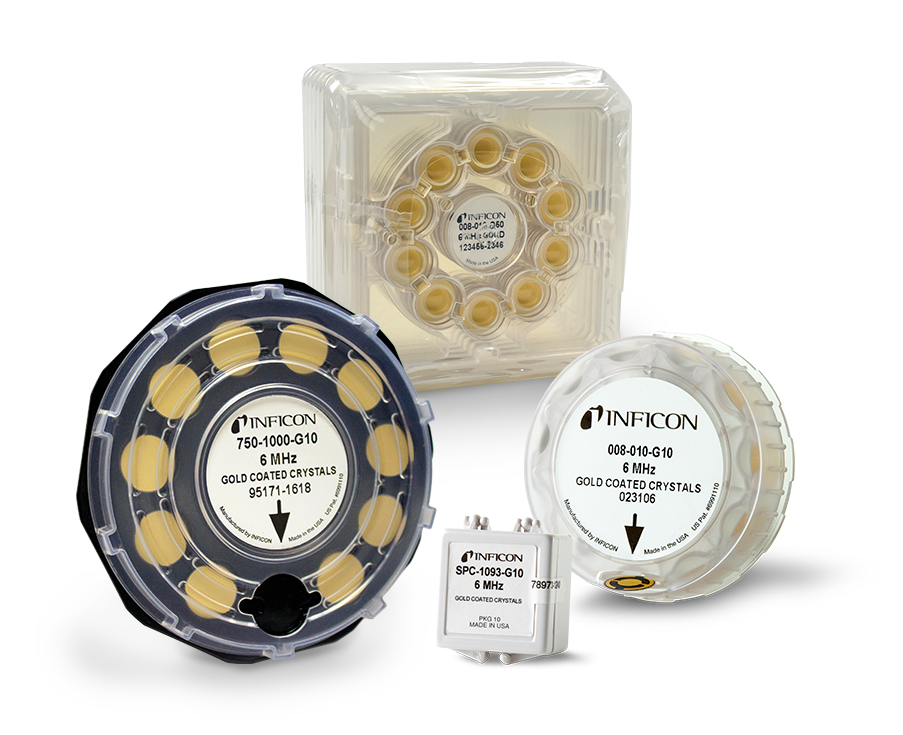
Quality crystals
INFICON EDC provides quality products to advanced manufacturers worldwide, and relies on automated equipment throughout the factory to manufacture these quality crystals at high volume. One hundred percent of the crystals produced are electrically tested on automated equipment to eliminate errors and ensure all crystals shipped meet or exceed specifications. Crystals are also 100% visually inspected to meet uniformity standards, as well as tested for curvature and performance. The vertical integration of crystal manufacturing into the INFICON controller, monitor, sensor, and crystal products allows deposition process optimization, enabling our customers to produce superior quality products. On-site manufacturing at INFICON EDC provides additional value with fast delivery, quick responding stock levels, and the ability to implement new crystal variations for application-specific requirements such as ALD depositions, OLED manufacturing and high precision optics.
Expanding capabilities to meet your growing requirements
INFICON EDC is committed to our operation’s quality and continued growth. In 2021, we began to embark on a legacy to expand cleanroom operations and increase capacity. This completely new cleanroom meets the particle specification of an ISO 6 (class 1K) cleanroom. Additionally, a new electrostatic control system was implemented that reduces particles in the cleanroom. New LED lighting was installed to lower energy consumption and foster our ongoing efforts in regards to sustainability. Production commenced in the newly added cleanroom in 2022. This addition has increased our capacity to be able to manufacture more than 10,000,000 crystals annually, allowing us to quickly respond to growing customer and market requirements.
Focus on Sustainability
INFICON EDC has made sustainability an important focus for lowering our carbon footprint. In addition to LED lighting was installed throughout the facility, we also utilize 100% wind generated sustainable electricity. The wind farm generates an impressive 122% of our energy consumption, leaving capacity to continue to grow and expand without the need for additional power sources.
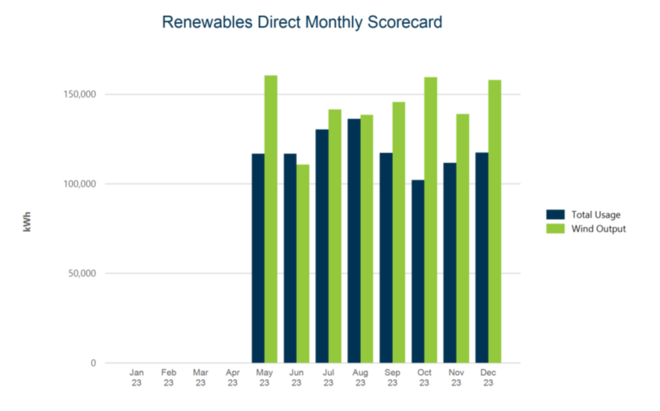
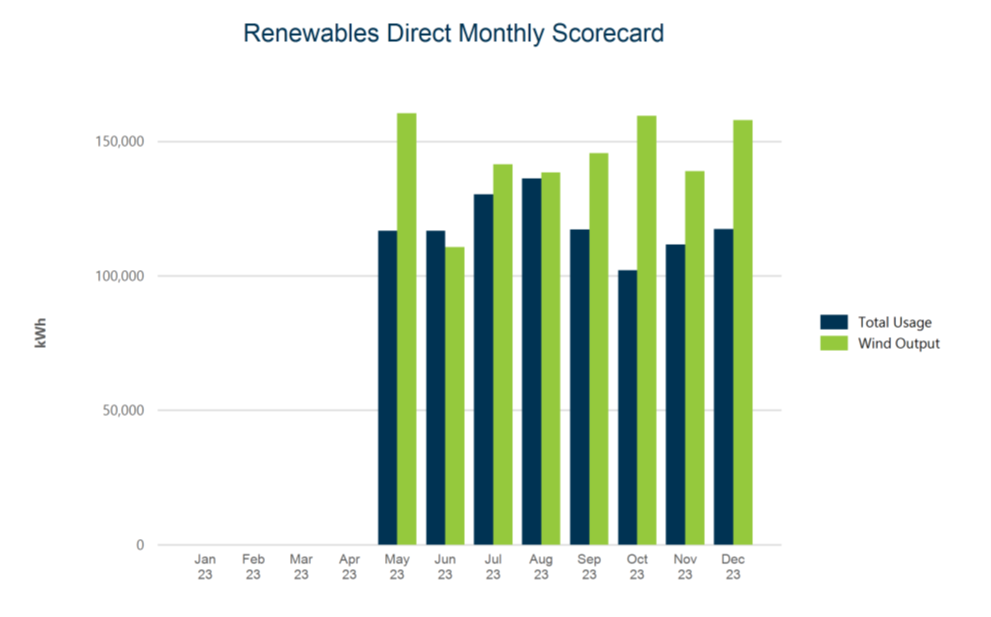
Crystal packaging was also an area where we looked into sustainability and were able to reduce waste during the package manufacturing process, thus saving around 2,950 kg (6,500 lbs.) of material each year.