Subscriber Discussion Forum:
FabTime Newsletter, Volume 26, No 1
We have subscriber discussion this month about how equipment suppliers can help fabs to maximize productivity, what tool state to use for engineering lots, and the December issue on The Waddington Effect.
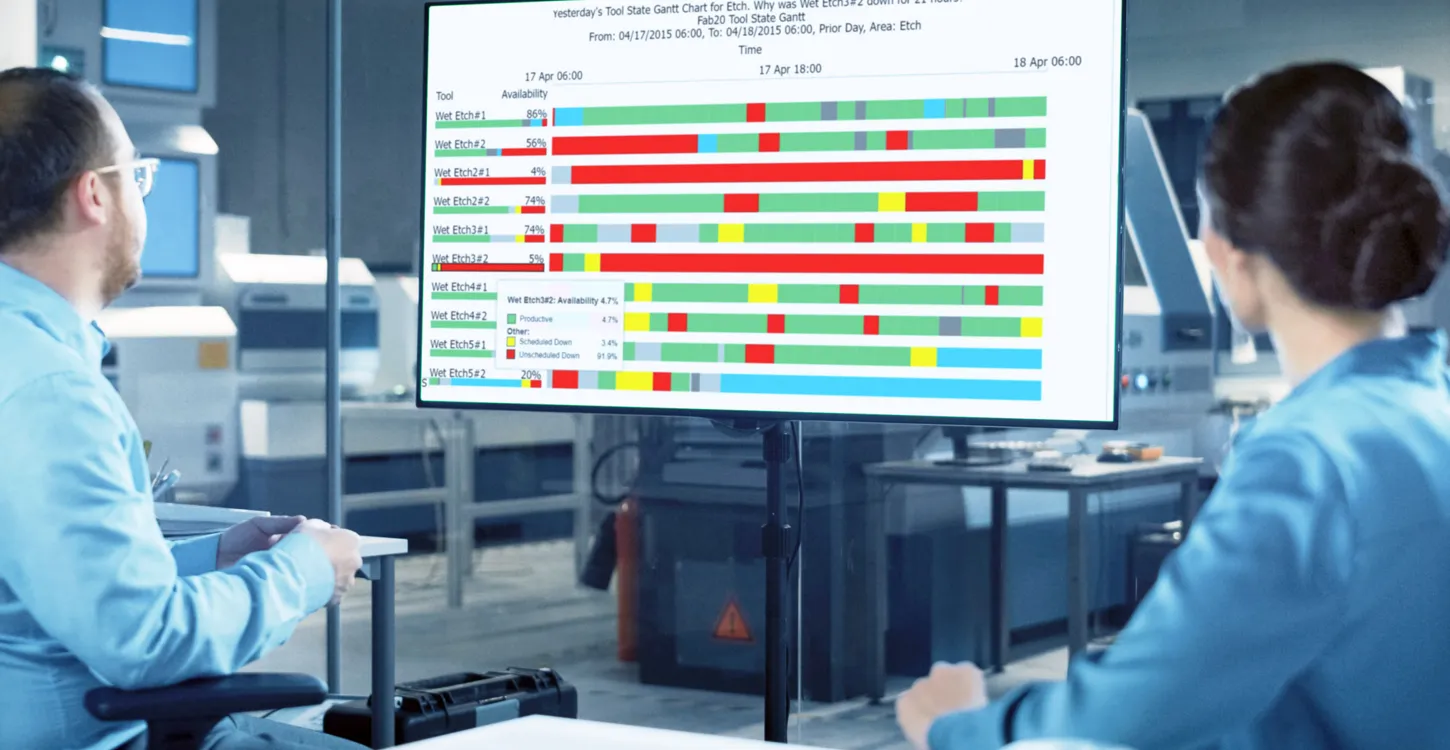
How can equipment suppliers help fabs to maximize productivity?
A Fundamentals of Fab Cycle Time webinar attendee from an equipment supplier wrote: “Do you have any models or experience working with equipment suppliers to understand how we can configure/operate tools to help fabs maximize productivity? We have done some internal work ourselves, but I wonder if there is more capability out there with collaboration to optimize the tool for fab operational efficiency (rather than over optimize unit process at the expense of fab efficiency).”
Response from Jennifer: I have done a special two-hour version of my Teams-based cycle time course for another equipment supplier, selecting the most relevant content from the typical four-hour class. This is more detailed and more interactive than the overview webinar that you mentioned. I also presented another webinar that focused on metrics for mitigating the impact of equipment downtime on fab cycle time, which has obvious relevance for equipment suppliers. But I haven’t directly looked at collaboration between the fabs and the equipment suppliers to optimize performance.
I do have a few ideas that might be helpful:
- To minimize the negative effect of downtime, equipment suppliers should ensure that tools have high overall availability, short down times (both scheduled and unscheduled), and low variability of availability from day to day.
- Equipment suppliers can also help fabs by reducing both the duration of and the variability of process times. Making process times more efficient (shorter) helps fabs to free up buffer capacity on the tools. Buffer capacity in turn helps protect against variability. Making process times more consistent from lot to lot reduces variability and helps bring down cycle time.
- Anything that an equipment supplier can do to make it easier to qualify additional tools for a given recipe, without sacrificing yields, would also be helpful for fab cycle time.
- Because of the impact of the number of qualified tools on fab cycle time, a fab will sometimes be better off having two slower tools, rather than one faster tool, especially if the reliability of the fast tool isn’t good. Of course there are other things to think about here (layout, staffing, etc.), but it might be worth studying this effect at some point.
What tool state should we use for engineering lots?
A subscriber from a mask manufacturing factory wrote to me after attending our equipment downtime metrics webinar: “In your Green-to-Green chart, what would you consider Engineering time? I’m having an ongoing debate with our process engineers about whether their experimental lots ought to run under green/productive time vs. engineering time. Today they run them under productive time and use engineering time when running recovery plates (goldens/monitors) after a down event. In our current use I would put engineering time inside of the down state window. I’m assuming your engineering time is more of the “recoverable” time, as from experimental lots?”
Response from Jennifer: Our green-to-green code classifies engineering time as a “green” state, meaning that it is treated like productive or standby time in terms of not being part of a green-to-green instance. We designate engineering time according to whatever is in SEMI E10. Or, in practice, whatever our customers log into the MES and then tell us to map into engineering time. My take is that any time the engineers are using the tool to run their own experiments, that’s engineering time. The tool is logged to an engineering state. If the production team is running a lot through the tool that is owned by the engineers, that time would usually count as productive time. (See more about Green-to-Green Charts in FabTime Newsletter 20.02, available for download from the FabTime Newsletter Archive. The archive is available only to subscribers. Details below.)
But I don’t work directly on installation projects. I suspect there is some disagreement in general about this question. Therefore, I am including it here, to see if this will spark some discussion. Readers, do you think that experimental lots should be run under productive time or engineering time? If you have feedback, please let me know. I will share responses in the next issue.
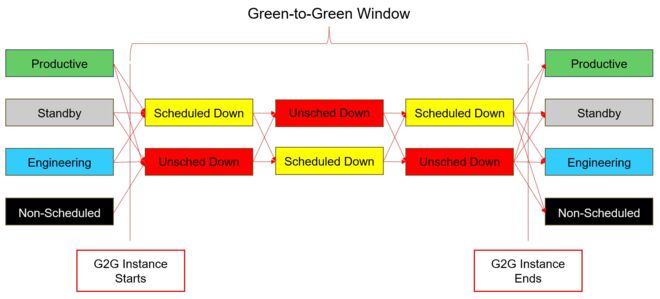
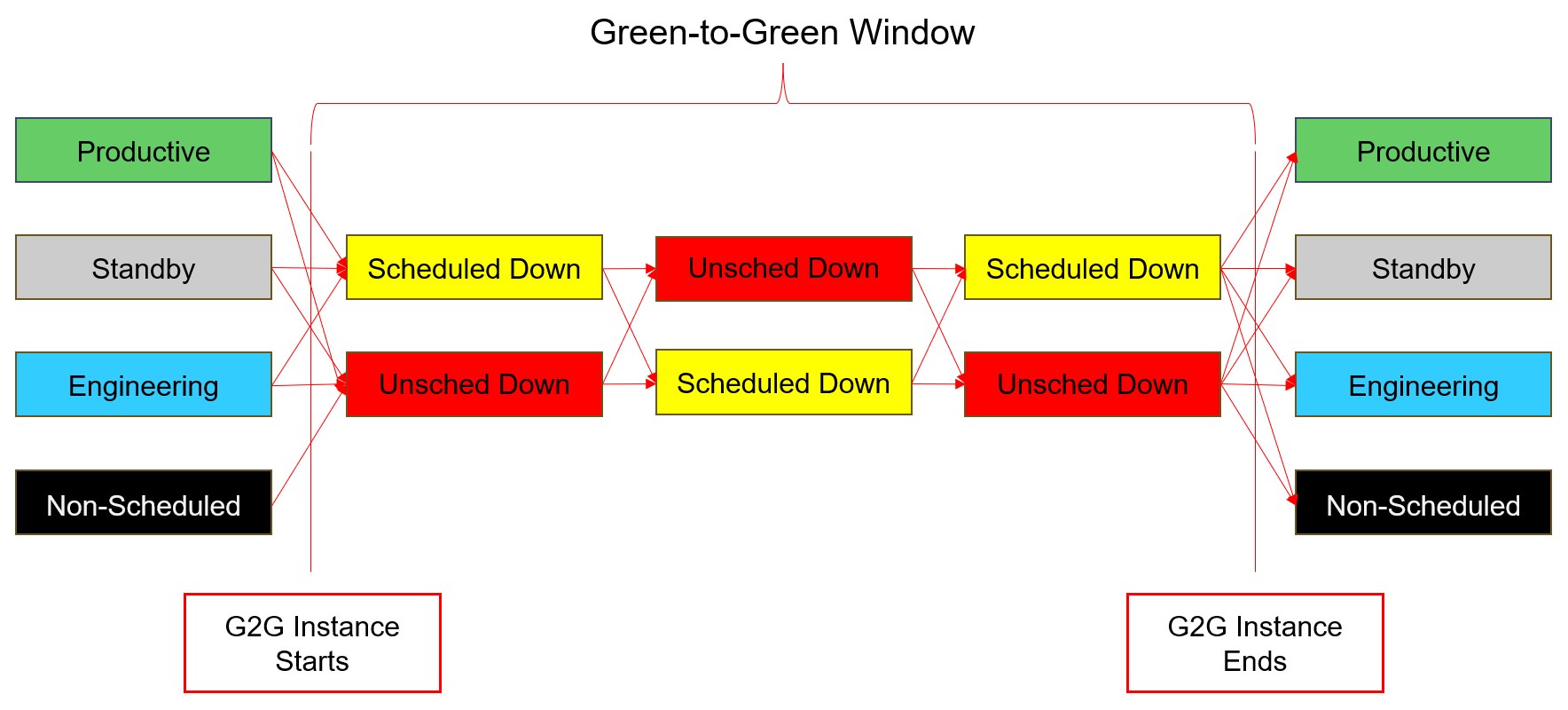
The Waddington Effect: Responses to the Last Issue
We received two responses from subscribers to the December newsletter article about The Waddington Effect (Volume 25, No. 6). The Waddington Effect is a condition in which doing scheduled maintenance can sometimes cause a short-term increase in unscheduled downtime.
A longtime subscriber wrote: “I never called it The Waddington Effect, but yes, I could see this happening. You’re doing a triggered PM and you don’t recover from the triggered PM and you can actually spend more time down than you planned on the flipside. You could be doing an unscheduled event and coupled with that pull in a PM activity and still have a bigger problem if you don’t recover. The article focuses on the PM activity, turning into an unscheduled event, which happens quite frequently. However, I’m not sure that it’s tied to the frequency of the PMs as much as the ability to properly execute the PM and recover and bring the system back up flawlessly.”
A subscriber who is an equipment engineering manager wrote: “That’s an interesting idea. I always had a feeling that there could be a connection between PMs and subsequent unscheduled downtimes. Now there’s something worth investigating. I’ll ask our improvement department to analyze this and will be curious to see your further results.”
The Subscriber Discussion Forum is a companion to the FabTime Cycle Time Newsletter, edited by Jennifer Robinson, Cycle Time Evangelist for INFICON.
Past issues of the newsletter are available for subscribers to download in PDF format. Existing subscribers can find the archive link in your most recent email newsletter. New subscribers will see the link upon registering.
Thanks for reading!
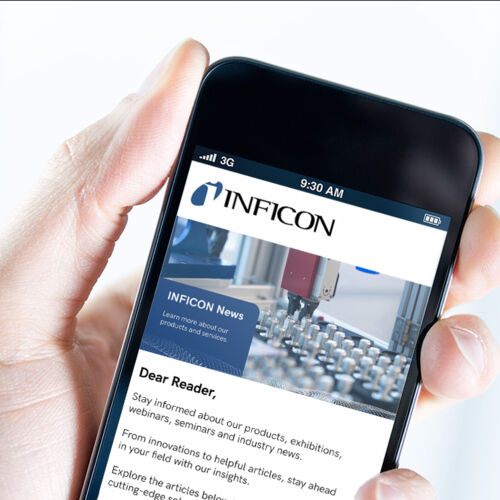