Understanding what you are doing during leak testing
Five important facts for direct electrolyte leak testing on lithium-ion cells.
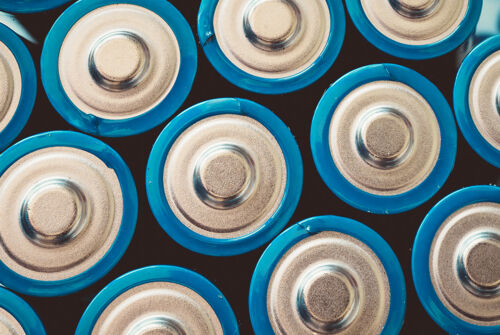
In the past, it was impossible to test lithium-ion and sodium-ion battery cells that had already been filled with electrolyte or even formed for leaks. INFICON has changed this with the new, patented method of direct electrolyte leak testing. Our standalone ELT3000 PLUS and our built-in ELT Vmax both use this ground-breaking test method: they detect when electrolyte leaks into a vacuum test chamber from tiny leaks in the single-digit micrometer range. However, there are common misconceptions that can stand in the way of a meaningful leak test of the battery cells. We would like to save you from this with this article. Here are five facts that will help you to ensure process reliability during your leak test.
1. Why helium and electrolyte leak rates can never be converted exactly
Helium is probably the best-known trace gas for vacuum leak testing. It is an established standard. For this reason, the electrolyte leak rates of battery cells are usually calibrated in the form of helium equivalent leak rates. However, the leakage rates of liquids depend heavily on the properties of the respective liquid. As these are often not precisely known, all devices in the ELT series, i.e., both the ELT3000 PLUS and the ELT Vmax, display a standardized helium equivalent leak rate for 100 percent dimethyl carbonate (DMC) and atmospheric fill pressure.
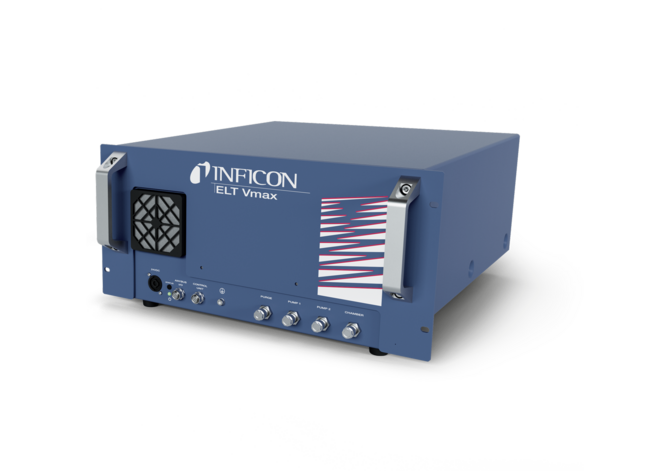
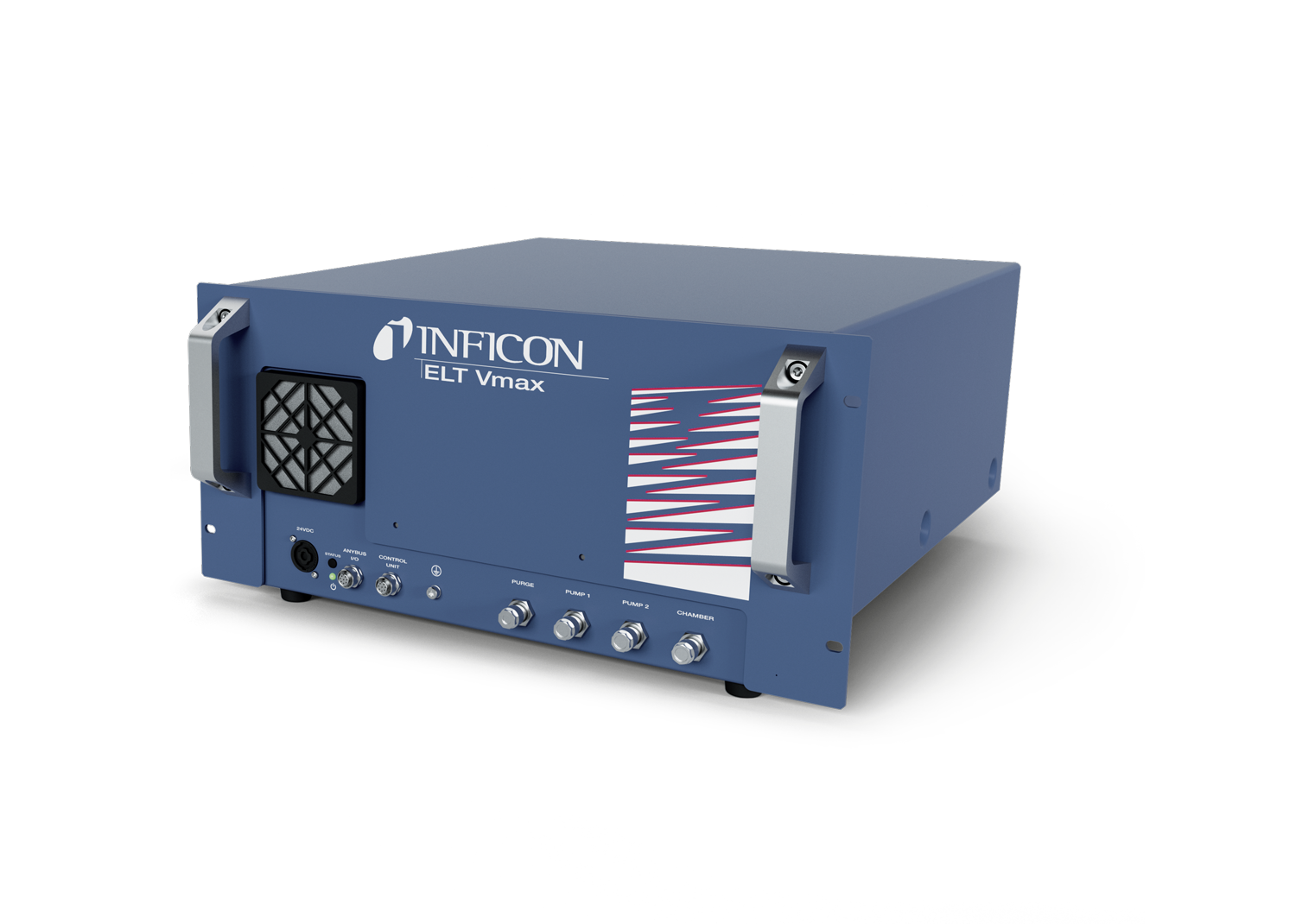
This means that a calibration with the E-Check test leak, for example, can only lead to an exact helium-equivalent leak rate if battery cellswere to be filled with pure DMC at atmospheric pressure. However, real battery cells will have only a certain percentage of DMC inside and often also have a certain underpressure.
How much exactly the two leakage rates differ – even with careful calibration – depends on many factors. Two examples using a simplified model calculation illustrate how large the difference can be in practice. It is important to bear this in mind when determining a suitable rejection leak rate.
Case study A: Cylindrical cell | |
---|---|
Filling pressure | 750 mbar |
Electrolyte | DMC-based (50 % DMC/50 % EC, 1.0 M LiPF6) |
Existing leak with a vacuum helium leak rate of: | 10-5 mbar∙l/s |
Electrolyte leak rate indicated by a calibrated leak detector of the ELT series: | 5∙10-7 mbar∙l/s |
Case study B: Pouch cell | |
---|---|
Filling pressure | 250 mbar |
Electrolyte | EMC-based electrolyte (100 % EMC, 1.0 M LiPF6) |
Existing leak with a vacuum helium leak rate of: | 10-5 mbar∙l/s |
Electrolyte leak rate indicated by a calibrated leak detector of the ELT series: | 10-6 mbar∙l/s |
2. A leak rate of zero is not a reasonable quality requirement
A fundamental fact of physics is that a leak rate can never really be zero. And even if a leak rate could be zero - there would be no way to measure it. Setting a limit leak rate of zero is therefore pointless. Rather, it is important to define the rejection leak rate in such a way that no more error modes harmful to the cells can occur.
Serious consequences caused by a leaking cell
- Loss of liquid electrolyte with corresponding loss of capacity
- Moisture ingress, reaction with the electrolyte forms corrosive hydrofluoric acid - causing even larger leaks and further loss of capacity
- Loss of mechanical integrity in pouch cells
It is vital that everything possible is done to prevent the exchange of liquids and gases between the battery cell and the atmosphere. The specific requirements for leak rates to help prevent this are discussed in section 3 below.
3. Liquids can effectively block leakage channels
Not every leak in a battery cell has ruinous consequences. During manufacture, battery cells are filled with a liquid. While there is a direct correlation between leak diameter and leak rate for gas leaks, this is not the case for liquid leaks (at least not over a wide range of leak channel diameters). So, the good news is that capillary forces can cause the liquid in the leak channel to simply block it. And through such a blocked leakage channel, neither liquid nor gas can penetrate into the battery cell, nor can they escape. This means that a blocked leakage channel can be considered tight.
In a detailed SAE Paper on the testing of lithium-ion cells, we described the phenomenon of leakage channel blockage and the resulting leakage rates comprehensively and quantitatively. In the two case studies below, we established the reject leak rates that would be blocked by liquid electrolyte.
Case study A: Cylindrical cell | |
---|---|
Filling pressure | 750 mbar |
Electrolyte | DMC-based (50 % DMC/50 % EC, 1.0 M LiPF6) |
Limit leakage rate for effective blocking of leaks | 5∙10-6 mbar∙l/s |
Case study B: Pouch cell | |
---|---|
Filling pressure | 250 mbar |
Electrolyte | EMC-based (100 % EMC, 1.0 M LiPF6) |
Limit leakage rate for effective blocking of leaks | 5∙10-7 mbar∙l/s |
4. Leaking cells are unsuitable as a calibration standard
Using leaky cells to calibrate your electrolyte leak tester may seem like a possible option at first glance. On closer inspection, however, such an approach proves to be far too unreliable. There are a number of reasons for this:
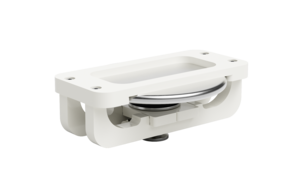
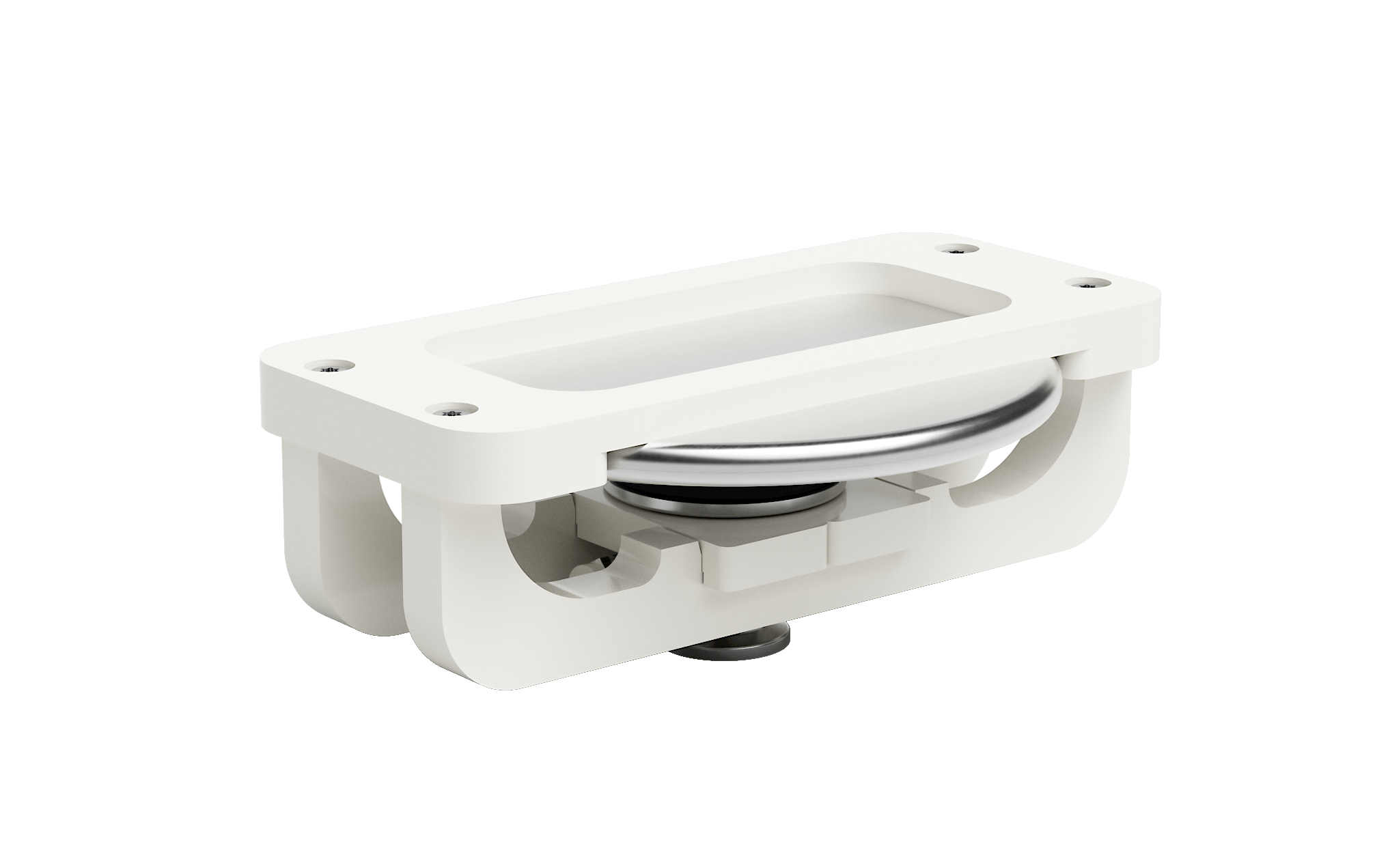
- Leakage channels that originally existed on the leaking cell can become blocked.
- Repeatability of the measurements is not possible with a leaky cell (see point 5).
- In this way, you are not working with a certified leak rate.
- As a defective component, a leaky cell is inherently unstable.
- It is extremely difficult to achieve the desired leak rate by deliberately manipulating the battery cell.
- A "calibration" per leaking cell does not create any process reliability.
Against this background, it is much more expedient to use a certified calibration leak such as the E-Check 2.0 from INFICON. The E-Check 2.0 is filled with DMC electrolyte solvent, is integrated into the vacuum chamber and is always ready for operation. This means that automatic test measurements lasting only seconds are also possible at preset intervals, for example every two hours or at the start of each shift. Unlike a defective cell, the certified calibration leak is stable against external influences and has a defined and always repeatable leak rate. The result: maximum process reliability for your fully automatic in-line testing.
5. The leak rate of a leaking cell decreases with further measurements
If you test the same leaking cell a second time in quick succession, you will measure a different leak rate - typically a slightly lower one than before. This leads some users to draw the wrong conclusions. This is not a sign that the test device is unreliable - it is, in fact, a real characteristic of the leakage channel.
It is the principle of direct electrolyte leak testing: the electrolyte solvent that penetrates through a leakage channel evaporates in the vacuum of the test chamber. This turns it into a test gas, so to speak, the concentration of which is detected by the mass spectrometer in the test device. As a result, the concentration of the electrolyte solvent in the leakage channel is initially reduced with each measurement in a vacuum. Subsequent measurements only show a reduced concentration of the solvent and result in a correspondingly lower leak rate.
However, if you wait for a period of time (one hour or even better, longer) between two measurements, the electrolyte solvent in the leak channel returns to its original concentration by diffusion, which significantly reduces the effect of the apparently shrinking leak.
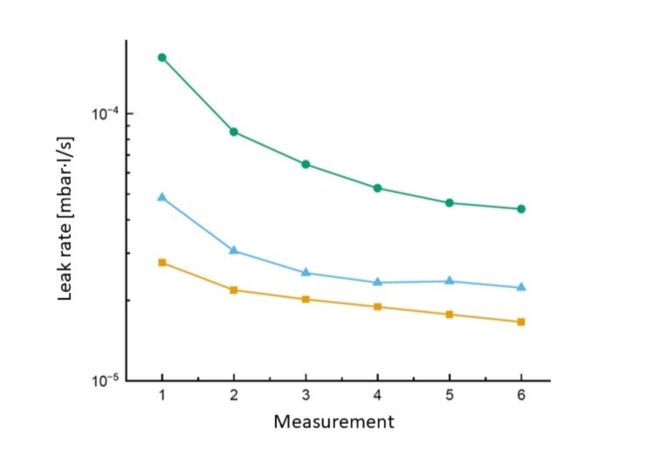
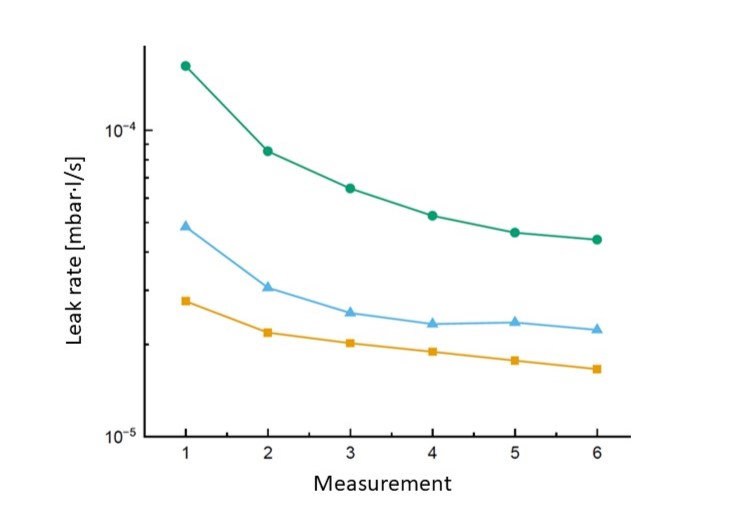
The decisive finding from all these considerations: The leak rate determined by the original, first measurement remains correct. If you wanted to test the same leaking cell again shortly afterwards, the measurable electrolyte solvent concentration - and therefore the measurable leak rate - would be lower. However, the reason for this is not a malfunction or a lack of process reliability in your test system, but the physics of the leak channel.
Conclusion: Fully automated testing with proven process reliability
Generally speaking, direct electrolyte leak testing has proven its worth in the quality assurance of lithium-ion cells. In industrial production, it even allows fully automated 100 percent tests to be carried out during the production cycle - with outstanding process reliability. However, to assure the most reliable leak testing of lithium-ion and sodium-ion battery cells, it helps to keep our five tips top of mind.
For more information please visit the product page of our ELT Vmax. You can also watch our on-demand Webinar.