Ensuring Battery Safety & Efficiency – Join our Free Seminar in India on Leak Testing
Mastering Leak Testing in Lithium-Ion Battery Production
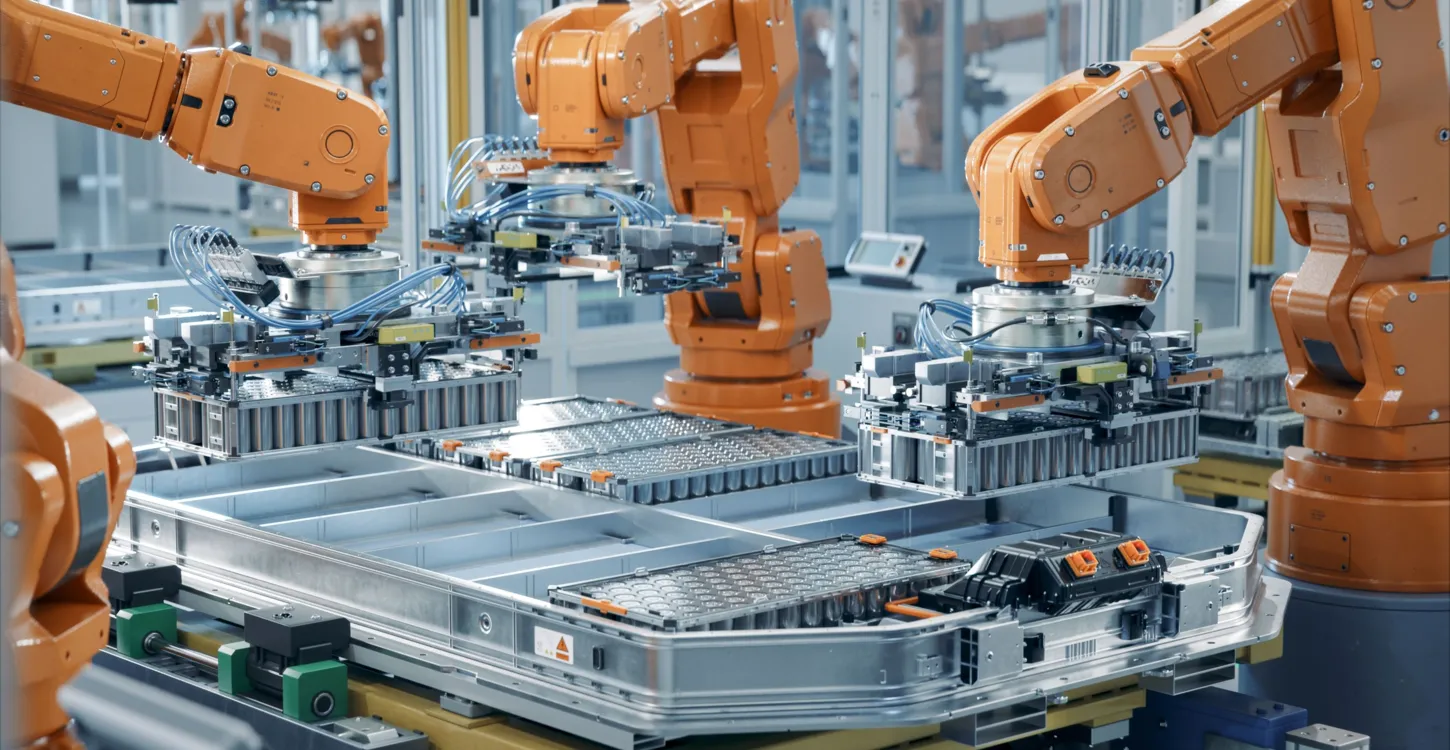
INFICON invites professionals in battery manufacturing, quality assurance, and R&D to a free seminar in India on Leak Testing in Lithium-Ion Battery Manufacturing, presented by Dr. David Kämpfer, Application Engineer Battery & Automotive at INFICON GmbH.
📍 Mumbai – April 7, 2025
📍 Bangalore – April 10, 2025
Learn how to:
- Improve battery safety and longevity with advanced leak testing
- Reduce production costs by detecting defects early in the process
- Choose the right leak detection method for different battery manufacturing stages
Leak testing is a key factor in ensuring lithium-ion battery reliability. Small leaks can cause electrolyte evaporation, reduced capacity, safety risks, and production inefficiencies. With increasing industry demands and tighter regulations, manufacturers need precise and efficient leak detection to maintain high product quality.
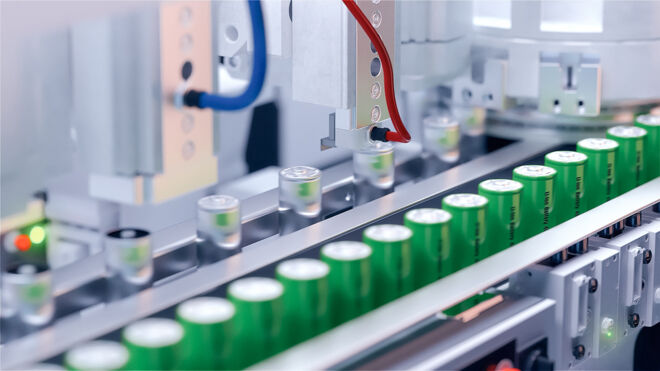
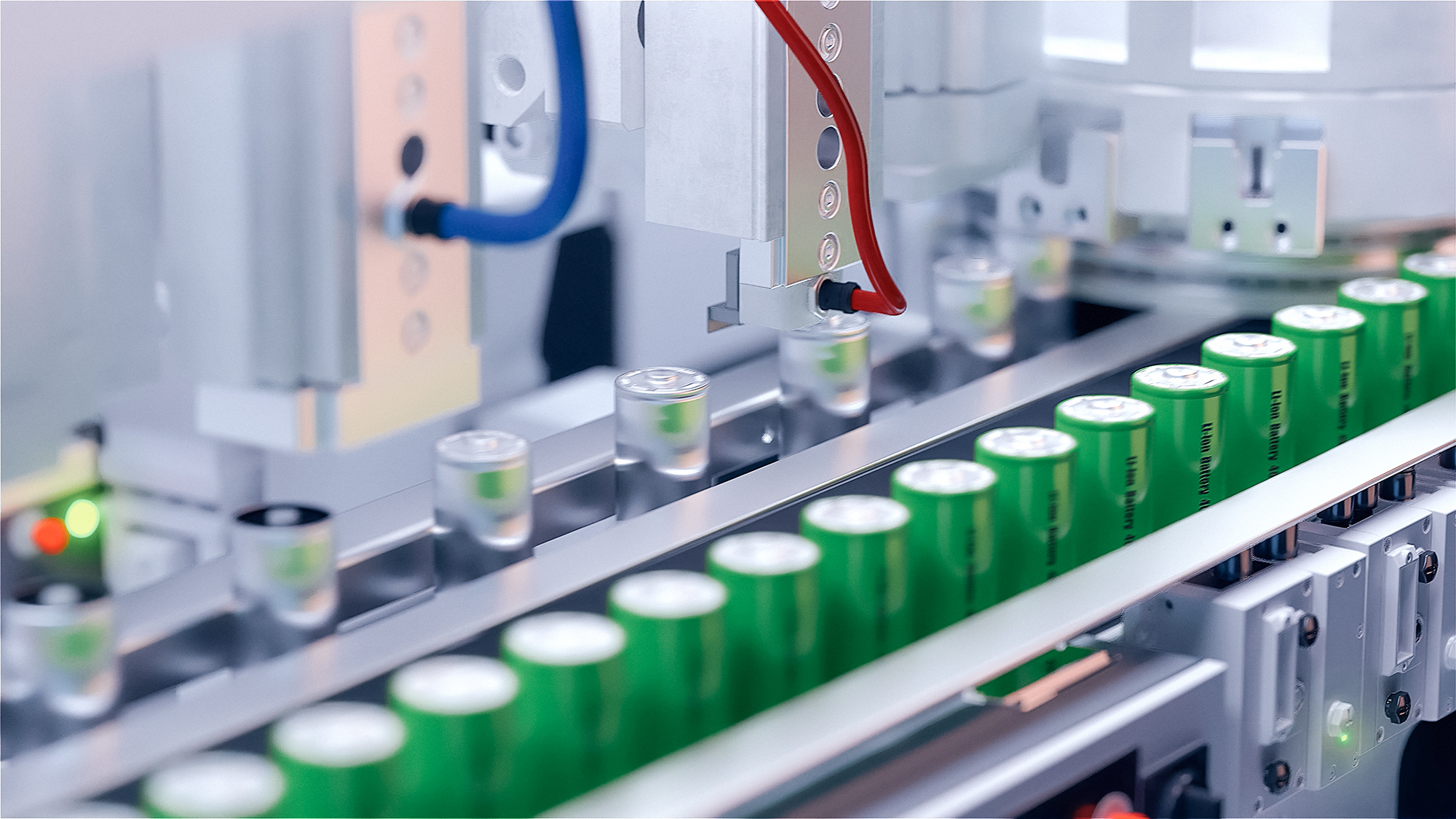
Where Leak Testing is Critical in Battery Production
Leak testing plays a role in multiple steps of the battery production process:
- Pre-Leak Testing of Cell Cases: Ensures that only leak-tight casings are used, preventing electrolyte loss and production inefficiencies.
- Leak Testing After Filling and Sealing: Verifies that the battery’s final seal is airtight, preventing degradation.
- Leak Testing After Forming and Aging: Identifies defects introduced during the conditioning phase, particularly in pouch cells.
- Final Leak Testing of Battery Modules and Packs: Confirms the integrity of fully assembled battery systems before they leave the production line.
Without effective testing, defective cells or modules can result in higher failure rates, rework costs, and compromised product safety.
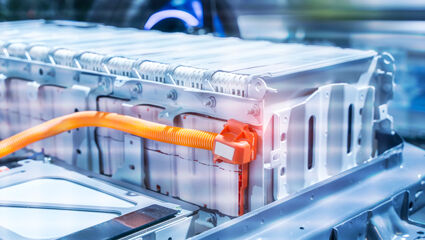
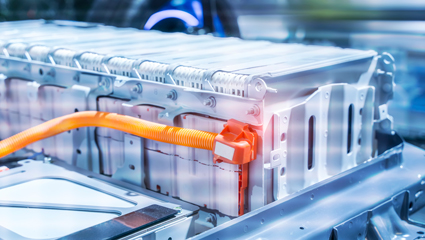
Experience Our Leak Detection Solutions in Action
Participants in the seminar will learn about three advanced leak detection technologies that optimize battery production:
✔ Vacuum Leak Detection: Highly sensitive, precise, and efficient for identifying the smallest leaks using helium tracer gas. INFICON’s EcoBoost algorithm optimizes the process by reducing helium consumption while maintaining accuracy. ✔ Sniffer Leak Detection: Ideal for testing assembled battery packs, this method allows operators to locate specific leaks and perform targeted repairs. ✔ Direct Electrolyte Leak Detection: A specialized technique that detects evaporating electrolyte from a leaking battery in a vacuum chamber, making it a reliable solution for pilot production as well as high volume manufacturing. |
---|
Each method offers distinct advantages depending on the production stage and specific quality control needs. Our high-speed, industrialized leak detection systems support manufacturers in improving efficiency while maintaining compliance with safety standards.
Learn from an industry expert, explore real-world applications, and optimize your production process.
Register Today – Secure Your Spot
📍 Mumbai – April 7, 2025
📍 Bangalore – April 10, 2025
Participation is free, but seats are limited! Register now!