Ingress Protection Testing for Mobile Phone Housings
How to accurately detect leaks on mobile phone housings
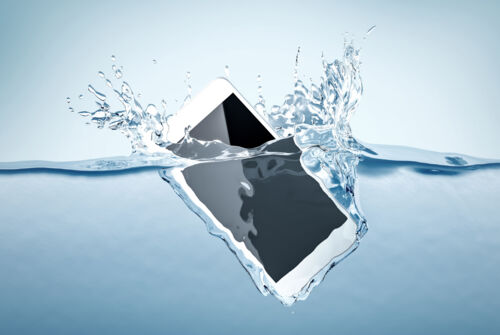
Ingress Protection (IP) testing refers to the process of determining how resistant an electronic product's housing is to the intrusion of solid objects (like dust) and liquids (like water) in order for the device to perform as expected in environments where extreme weather conditions may occur. The standard used for the leak test of mobile phone housings is the IP Code (International Protection Marking), which classifies the level of protection offered by casings of electrical devices. Electronic devices with higher IP ratings are more likely to withstand the rigors of everyday life, including exposure to rain, splashes, or dust.
Common IP Ratings for Mobile Phones
- IP53: The device is protected against limited dust ingress and can withstand spraying water.
- IP67: The device is completely dust-tight and can be submerged in water up to a certain depth (typically 1 meter for 30 minutes).
- IP68: The device is also dust-tight and can withstand submersion in water for longer durations or deeper depths (usually up to 1.5 meters for 30 minutes or more).
Why Leak Testing?
Liquid ingress through the mobile phone housings can damage the device. Water ingress is a typical example and most commonly occurs at critical areas subject to higher stress during regular use.
As many other electronic components, mobile phones must be humidity tight (weatherproof), and fulfill the requirements of ingress protection class IP67. By performing leak tests, manufacturers ensure that devices meet specific IP standards and perform well under real-world conditions.
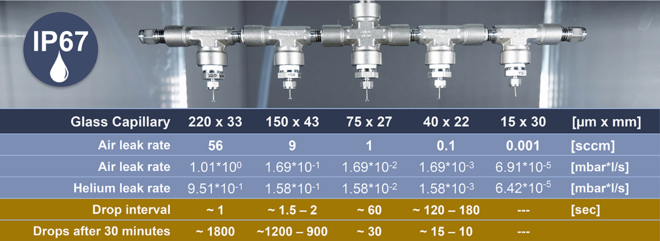
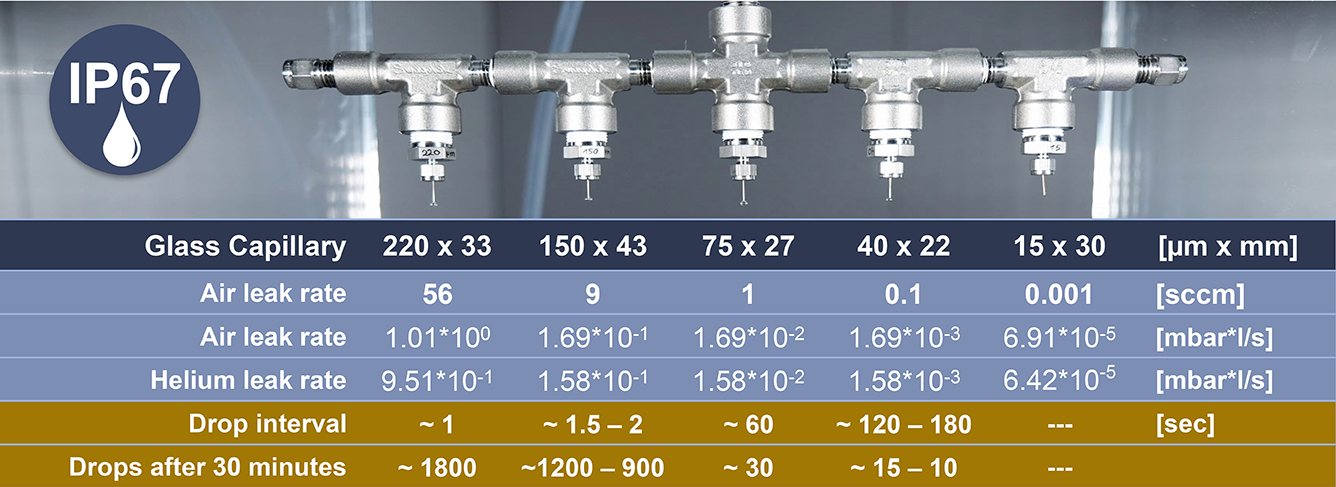
Can Traditional Methods Detect These Small Leaks?
Leak testing of assembled mobile phone casings is typically done by pressurizing the component with air followed by soaping. After the soap is applied, each point that can potentially leak is inspected visually. However, soaping has several drawbacks. In the presence of large leaks, soap can damage the electronics. Additionally, this technique requires cleaning up and drying the housing after the leak test. In the case of large leaks, the soap spray can be blown away from the leak site, and when multiple leaks are close to each other, it becomes difficult to determine the size of each leak. The greatest limitation is, however, that the smallest leaks cannot be detected with soaping, especially those close to the IP67 specification. Finally, the test is operator-dependent and requires line-of-sight for effective visual inspection.
Pressure testing is another common method and involves placing the phone in a sealed chamber and gradually increasing the pressure inside. Pressure is applied to simulate the external environment similar to conditions that the device would face during use. If the phone is not properly sealed, the pressure difference will cause air to leak out. Pressure differences can be measured to obtain an indication on the tightness of the device. However, since mobile phone cases are flexible to some extent and can distort under pressure, they are not suitable for pressure testing. This method has several drawbacks when it comes to accurately pinpointing the leak position. It is also affected by temperature changes, which can influence the results and lead to inaccurate measurements. Additionally, it may not achieve the sensitivity required to meet the IP67 standard.
Tracer Gas Leak Detection for Accurate Ingress Protection Testing
Leak detection with tracer gas is a more effective method for identifying leaks on mobile phones. This technique involves injecting a small amount of helium or hydrogen (usually mixed with nitrogen) as a tracer gas into the housing to test and then using leak detectors to locate any escaping gas. The method is highly sensitive and versatile and is often employed in production leak testing to find leaks in the 5x10-4 – 5x10-3 mbar l/s range.
Two options are available for leak testing assembled mobile phones:
1. Automated, integral testing (accumulation testing) with helium tracer gas
Before leak testing, the housing is filled with tracer gas. Filling the housing should be done in a way that ensures a maximum concentration of tracer gas on the inside. The TGF11 Tracer Gas Filler from INFICON evacuates the air before filling and ensures that the tracer gas reaches all parts inside the product.
For automated integral testing of mobile phones, the housing is filled with helium and put in a chamber that closes and seals. If the part has a leak, helium will escape through the leak and accumulate inside the chamber over time. The consequent increase in helium concentration will be detected with the LDS3000 AQ Helium Leak Detector. During the leak test, the operator will obtain leak measurements and easily determine if the housing is tight or not. This method offers higher sensitivity, better repeatability, and faster cycle times compared to traditional methods such as pressure decay.
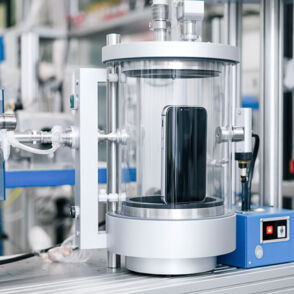
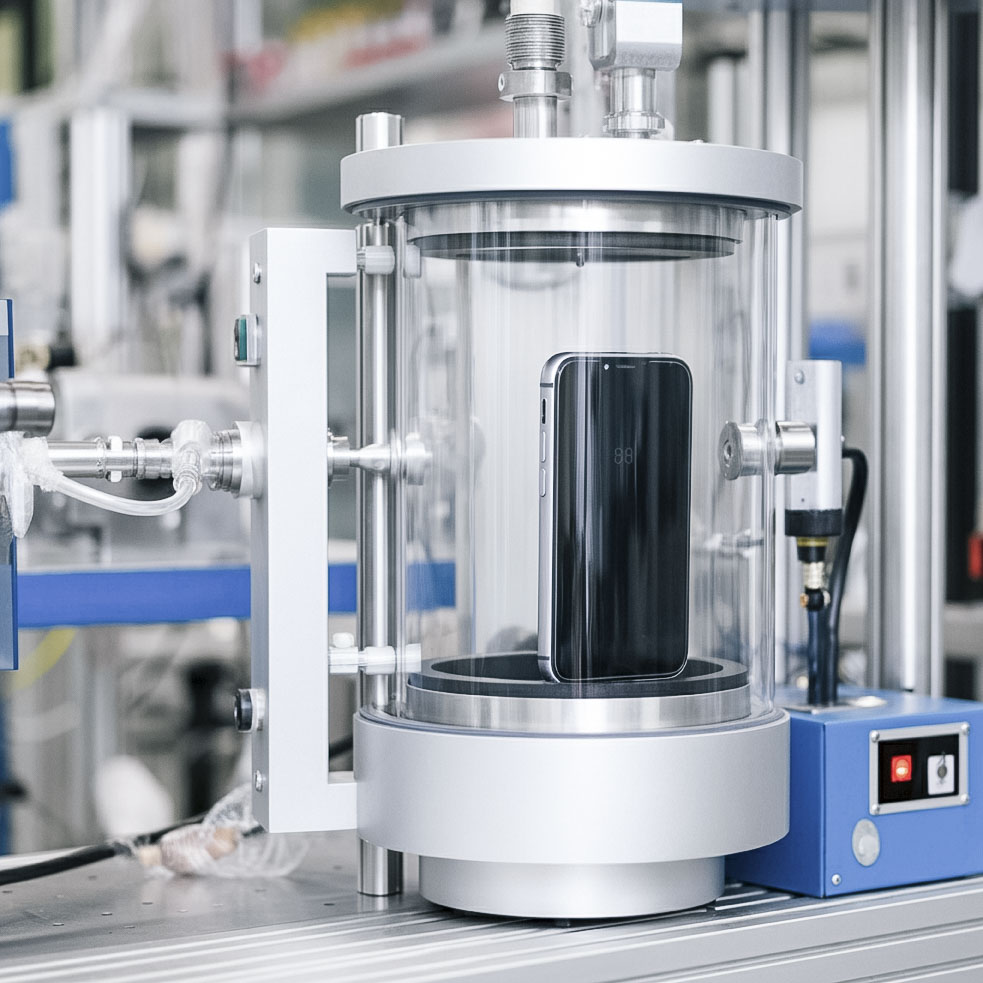
2. Leak testing in predefined areas with hydrogen tracer gas
Before leak testing, the housing is filled with tracer gas as described earlier. Once filling with tracer gas is completed, the leak testing can begin. All critical points are tested by moving the sniffing hand probe of the Sensistor® Sentrac® Hydrogen Leak Detector across those areas. If any leak occurs, the forming gas will escape from the leak and be detected by the leak detector. The exact leak location can be determined by moving the probe tip back and forth and is found where the highest leak rate is shown.
When the test is complete, the TGF11 Tracer Gas Filler releases tracer gas in a controlled way avoiding contamination of the test area.
Accumulation and sniffing can be effectively combined for added efficiency. If the integral test indicates the presence of leaks, accumulation can be followed by manual leak location with tracer gas to pinpoint the exact location of the leak. This streamlines the process for users, allowing them to fill the part only once and efficiently focus on locating the leak in the identified areas, saving both time and resources.
Advantages of Leak Detection with Tracer Gas
- Temperature independent
- Well suited for testing soft/flexible components (like plastic mobile phone housings)
- Fast pinpointing of the leak position
- No operator interpretation of the leak size - precise measurement obtained
- Reliably detect even the smallest leaks close to the leak rate limit
- Volume independent test
- No time wasted in cleaning up or drying after testing
- Easy to find leaks even with limited visual access
Interested in Learning More?
Leak tightness requirements are constantly increasing. Download this paper or watch our on-demand webinar and learn more about leak testing requirements.
Want to Stay Updated on Leak Detection?
Our newsletter offers regular updates on our latest products, applications, upcoming events, and other interesting news.