Jacob Maximizes Tool Uptime for Perovskite Solar Process
Download Application Note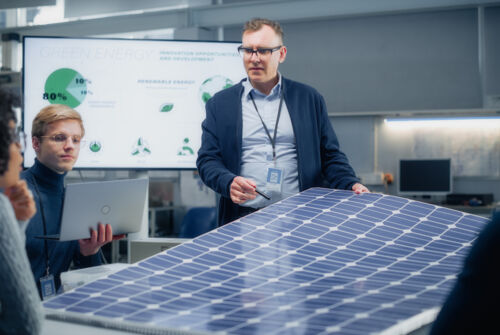
Longer Process Monitoring Time and Higher Productivity
Jacob is a photovoltaic equipment engineer at a major solar cell manufacturer. Jacob approached us looking for ways to increase the uptime on their tool and production capacity. The runtime on the tool was limited because the QCM needed to be changed frequently due to the harsh perovskite material causing the QCM to fail. For this reason, in the past, Jacob upgraded all of their tools with Crystal 12® rotary sensors. The Crystal 12 allowed the system to automatically switch to a brand-new crystal when the monitoring life expired and technicians could easily swap the crystal carousel with a spare that was already loaded with new crystals without any tools. However, Jacob was still looking for other unique ways to maximize their production capacity and knew he could rely on the application experts at INFICON for assistance.
Our team met with Jacob to discuss all of the process requirements and what instrumentation was currently being used on the tool. The first thing the team noticed was Jacob was using gold electrode QCMs. Gold electrode QCMs are excellent for low stress metals, but when it comes to harsh materials like perovskites, the QCMs must be changed much more frequently compared to alloy electrode QCMs which provide nearly 4 times more monitoring time. Jacob was eager to test these, so INFICON sent him a few samples from stock that were readily available.
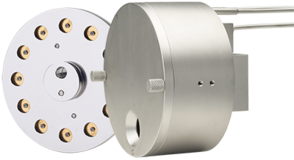
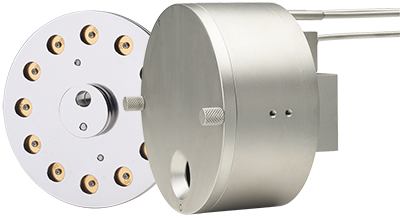
The team also learned that the tool was equipped with an active oscillator deposition controller, because it was a low-cost controller option. At the time this worked for Jacob, since production was just beginning and the controller met their product generation process. However, since then manufacturing expanded at Jacob’s facility and the solar cell demand was increasing, so it was time to refresh equipment to support the next solar cell product generation. We informed Jacob that active oscillator instruments have limited capability compared to our ModeLock controllers, like Cygnus® 2. ModeLock controllers have 10 times better resolution than active oscillator instruments and would double the QCM monitoring time for Jacob’s process, which was exactly what he was looking for. Not only was Jacob thrilled that productivity could be increased, but also that the higher resolution of the ModeLock controller could better support the process control requirements for the next generation of solar cells.
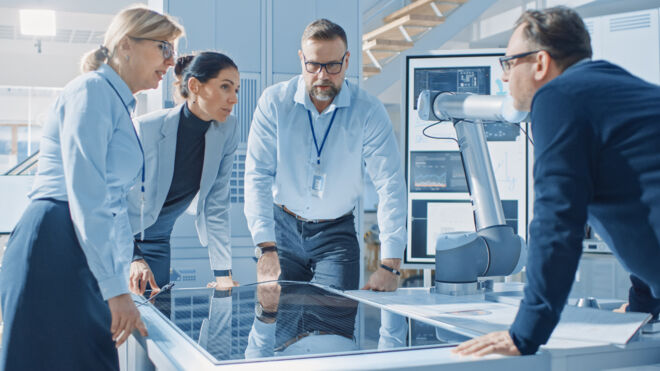
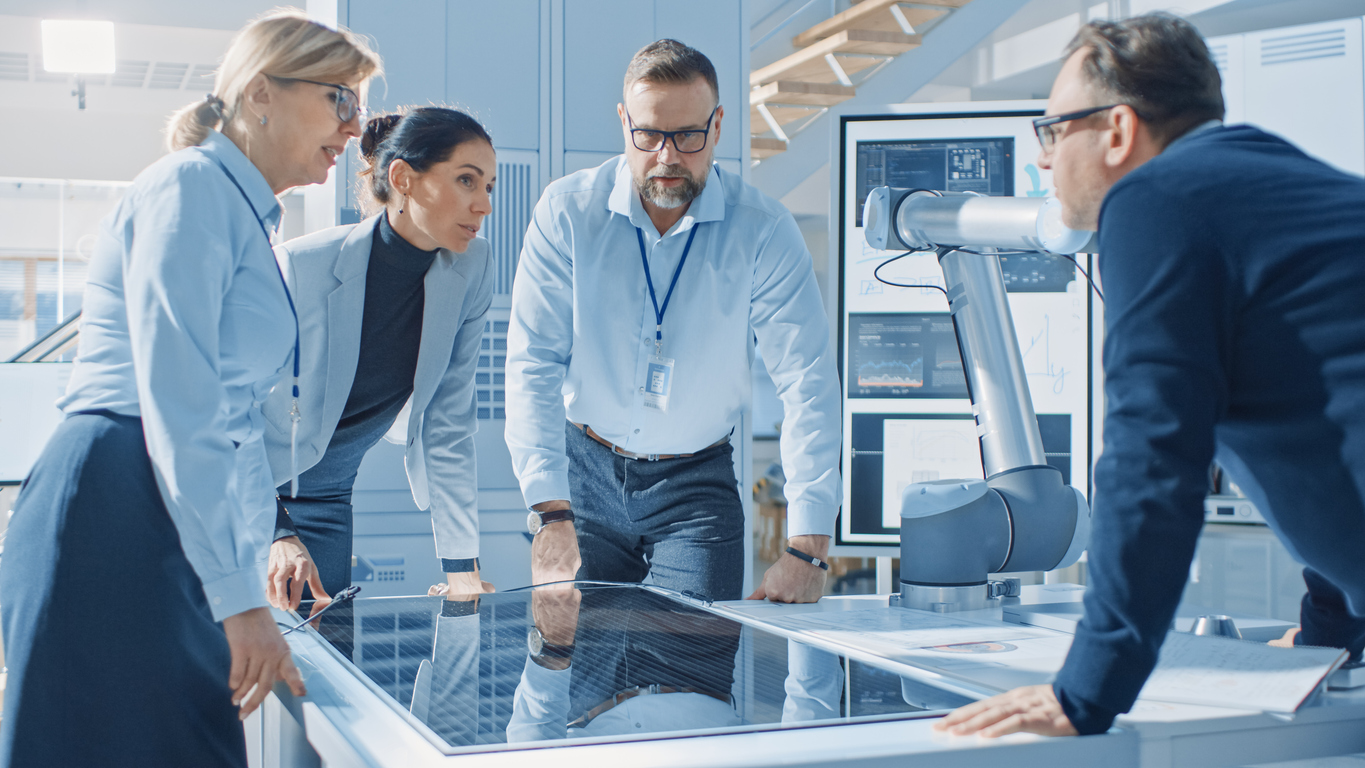
Jacob placed an order for a Cygnus 2 deposition controller and was pleased with the training and installation support INFICON offered. Since the upgrade and changing QCM electrodes, Jacob’s company has drastically increased their productivity and product quality.
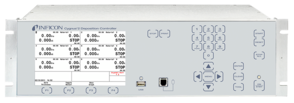
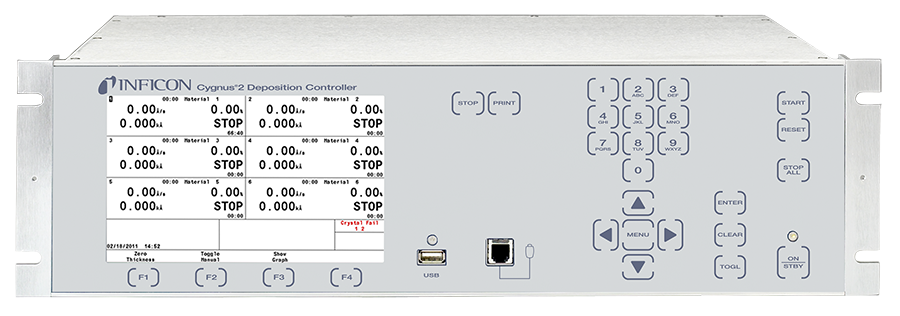