Mastering Tracer Gas Leak Testing
Insights from a Leak Detection Expert
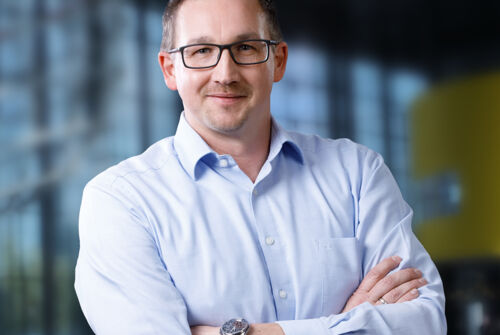
Tracer gas leak testing is a powerful method for detecting leaks, but requires careful tracer gas handling in order to get the highest test accuracy. Whether you’re an experienced quality technician or just starting out, understanding the common pitfalls in tracer gas testing can help you achieve more accurate and reliable quality test results.
We sat down with Steffen Mähler, Segment Account Manager EMEA, an expert in the field, to discuss the most frequent mistakes made during leak testing, how to avoid them, and some tips to improve your overall process.
What Are the Most Common Mistakes When Using Tracer Gas for Leak Testing?
Mähler explains that one of the biggest mistakes users make is releasing tracer gas into the test area after the leak test. “Tracer gas must be diverted away from the workplace in a defined manner after the test process has been completed” he explains. “If the gas escapes and contaminates the test area, you lose the ability to accurately measure leaks. This is a common issue, and it often leads to false positives or missed leaks.”
Besides workplace contamination, he highlights a few other factors that can throw off the testing process, including air pockets, dilution of tracer gas, and pressure fluctuations.
Let’s look deeper at each of these pitfalls.
Tracer Gas Contamination: A Silent Enemy
Improper venting or leaking connectors can also lead to tracer gas contamination, which might trigger false alarms or cause downtime. Mähler says that releasing tracer gas into the test area can result in an invisible “cloud” that contaminates the environment, making it difficult to detect small leaks. “To avoid contamination of the test station, ventilation must be properly considered, where gas is accurately directed to an exhaust system rather than being released into the room. Since tracer gases tend to move upwards, I always recommend introducing fresh air at the bottom of the testing area and setting up exhaust ventilation at the top” - he adds.
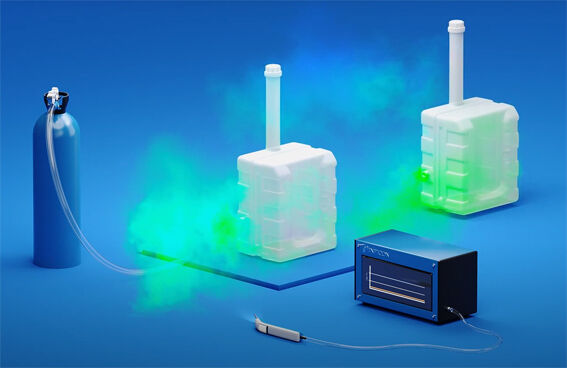
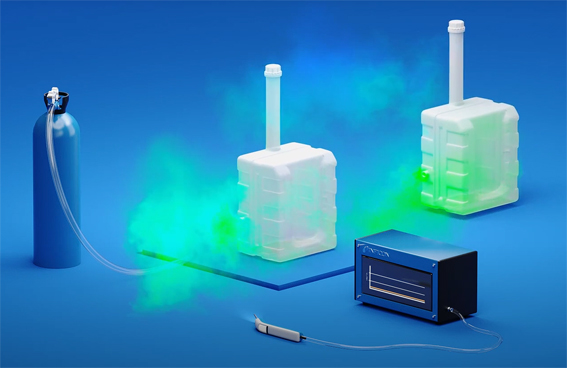
Air Pockets: The Leak-Hiders
Air pockets occur when ambient air is trapped inside the test part before it’s filled with tracer gas. “The trapped air gets pushed to the far end, or “dead end” of the object and “hide the leak” continues Mähler. This is especially true for small diameter pipes or parts with intricate internal structures.
To avoid this, he recommends starting the leak test with a pre-evacuation. This step involves removing ambient air from the test object before filling it with tracer gas, helping ensure that the gas is evenly distributed inside the entire part to test, and not hidden by air pockets.
Tracer Gas Dilution: Weakening Your Test Results
Another challenge is dilution. When tracer gas mixes with ambient air, it dilutes, reducing the sensitivity of your leak test. For example, at one bar test pressure, the dilution is 50% due to the 1 bar of atmospheric air pressure in the test part, which significantly impacts the reading on your leak detector. Higher test pressures reduce this effect, but for applications like battery housings or gearboxes with thin walls, low test pressures are often necessary. To better understand tracer gas dilution, let’s use an everyday example such as making a cup of coffee.” explains Mähler.
“Imagine you’re brewing your coffee,” he says, “and you carefully measure the right amount of coffee grounds. But then, instead of using pure water, you decide to dilute it with a little bit of milk. As you add more milk or water, the coffee becomes weaker — it still has some flavour, but it’s less concentrated and not as strong or effective at giving you that energizing kick you rely on.”
Just like how diluting your coffee with too much milk or water results in a weaker drink, diluting tracer gas with ambient air reduces its concentration, making it harder to accurately detect leaks. If you dilute the tracer gas too much, the leak detection process becomes less sensitive, and you might miss even a small but critical leak.
Pressure Changes: A Threat to Accuracy
Pressure fluctuations during the leak testing process can lead to false readings or missed leaks. Whether it’s due to manual adjustments or small leaks in the test chamber, a drop in pressure can distort the results. A steady pressure is essential for reliable leak testing.
Safety First: Handle with Care
Handling pressurized gases requires care, and safety should always be a top priority. Even at low pressures, tracer gas can pose risks if handled wrongly. By using the proper equipment and following safety protocols users can minimize risks.
For example, you would never drive a car with the gas tank completely full and leave the cap loosely screwed on — it would spill gas and create a dangerous situation. Just like how spilling fuel can cause a fire hazard, improper handling of tracer gas can lead to unsafe conditions, even if the pressure is low.
Best Practices for Successful Tracer Gas Leak Testing
So, how can you improve your tracer gas leak testing process and avoid these common mistakes? Mähler shares a few tips:
- Pre-Evacuation: Remove ambient air from the test part before introducing tracer gas. This helps with better gas distribution and reduces the chance of dilution.
- Gross Leak Testing: Before you start the tracer gas phase, perform a gross leak test to catch any obvious issues and avoid contamination or excessive gas costs.
- Controlled Venting: Ensure that any released tracer gas is vented safely and directed to a proper exhaust system. This prevents contamination of the test area.
- Post-Evacuation: After testing, remove any residual tracer gas from the tested parts. This reduces the risk of outgassing and false alarms in future tests.
While these steps are crucial for accurate tracer gas testing, they can be time-consuming and prone to human error. That’s where proven solutions come into play and simplify the entire process. Tracer gas fillers such as the TGF11 or ILS500 F from INFICON streamline gas handling, saving time, ensuring consistency and accuracy with less reliance on operator skill.
“In other words, just having a great leak detector isn’t enough if the gas itself isn’t handled correctly. Investing in accessories like the fillers alongside your detector guarantees users are getting the most out of both, saving time, reducing costs, and ensuring more reliable results.” concludes Mähler.
Want to Learn More about Correct Tracer Gas Filling and Evacuating?
Download our Application Note or watch our On-Demand Webinar "Not finding all relevant leaks? The essentials of tracer gas handling"!
Interested in More Tips&Tricks from Our Leak Detection Experts?
Read about the 8 Tips and Tricks from Our Leak Detection Experts