Non-Destructive Solution for Identifying Leaks on Plate Heat Exchangers
Leak Detection with Tracer Gas
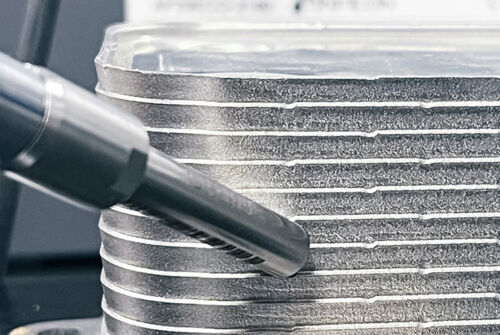
Heat exchangers are used in a wide range of industries and applications to facilitate the transfer of heat between two or more gases, liquids, or a combination of both. From power generation and manufacturing to healthcare and data centers, they improve the efficiency, safety, and energy savings of thermal processes. Heat exchangers can range from small units for domestic applications to large industrial units used in power stations, chemical plants, and oil refineries. Their size and volume vary greatly depending on the type, application, and amount of heat to be transferred.
This article explains why leak detection is crucial and how to effectively test plate heat exchangers (PHEs) for leaks.
Efficiency and Safety of Plate Heat Exchangers
Corrosion, thermal and mechanical stress and gasket damage are some of the conditions that can cause a plate to develop small cracks. Leak-free heat exchangers are crucial for several reasons:
- Efficiency: Leaks can lead to the loss of heat transfer fluid, which reduces the overall efficiency of the heat exchange process. By maintaining a leak-free system, operators can ensure optimal thermal performance and energy savings.
- Safety: Leaks can pose significant safety risks, including exposure to toxic substances or high-pressure fluids. Leak-free heat exchangers help mitigate these risks, protecting workers and the environment.
- Cost Reduction: Leaks can result in costly downtime and repairs. A leak-free system minimizes maintenance needs and operational interruptions.
- Environmental Protection: Leak detection avoids emissions that can harm the environment. This is especially important in industries with strict regulatory compliance requirements.
Traditional Methods
Various techniques have been used over the years to detect leaks in heat exchangers.
- Pressure decay: This method involves filling the heat exchanger with air, pressurizing it, and then checking the pressure drop over time. Pressure decay is, however, affected by temperature changes. Furthermore, the pressure drop gives an indication of the tightness of the system, but not of the exact location of the leak.
- Soap bubbles: After pressurizing the heat exchanger with air, a soap or detergent solution can be applied to potential leak areas. If there is a leak, bubbles generally form at the leak point. Commonly used for detecting small leaks in flanges, joints, seals and gaskets, this technique is simple and inexpensive, but the limited sensitivity makes it impossible to detect very small leaks.
- Water bath: After pressurizing the component with air or gas, water dunk testing is performed by simply immerging it in a tank of water. Bubbles appearing at the leak site typically indicate the location of the leak. However, the large number of bubbles makes it often difficult to identify leaks with accuracy. Water bath requires visual access to all surfaces of the component, including those that are hidden from the operator's eye.
These techniques aren’t suitable for large, complex systems or heat exchangers in use within an operating system or process, as their sensitivity is limited and they require shutdown and drying the heat exchanger afterwards.
The Solutions from INFICON
A non-destructive and more sensitive leak detection method is leak detection with a tracer gas. The process involves using forming gas (5% hydrogen in nitrogen) or helium as the tracer gas. Depending on the size of the heat exchanger, the required throughput, and the leak rate requirements, accumulation test and vacuum test are suitable alternatives.
Accumulation method | Vacuum leak testing | |
Leak rate requirements | Water-tight, oil-tight | Refrigerant-tight |
Throughput | Low to medium | Medium to high |
Part size | Small | Medium |

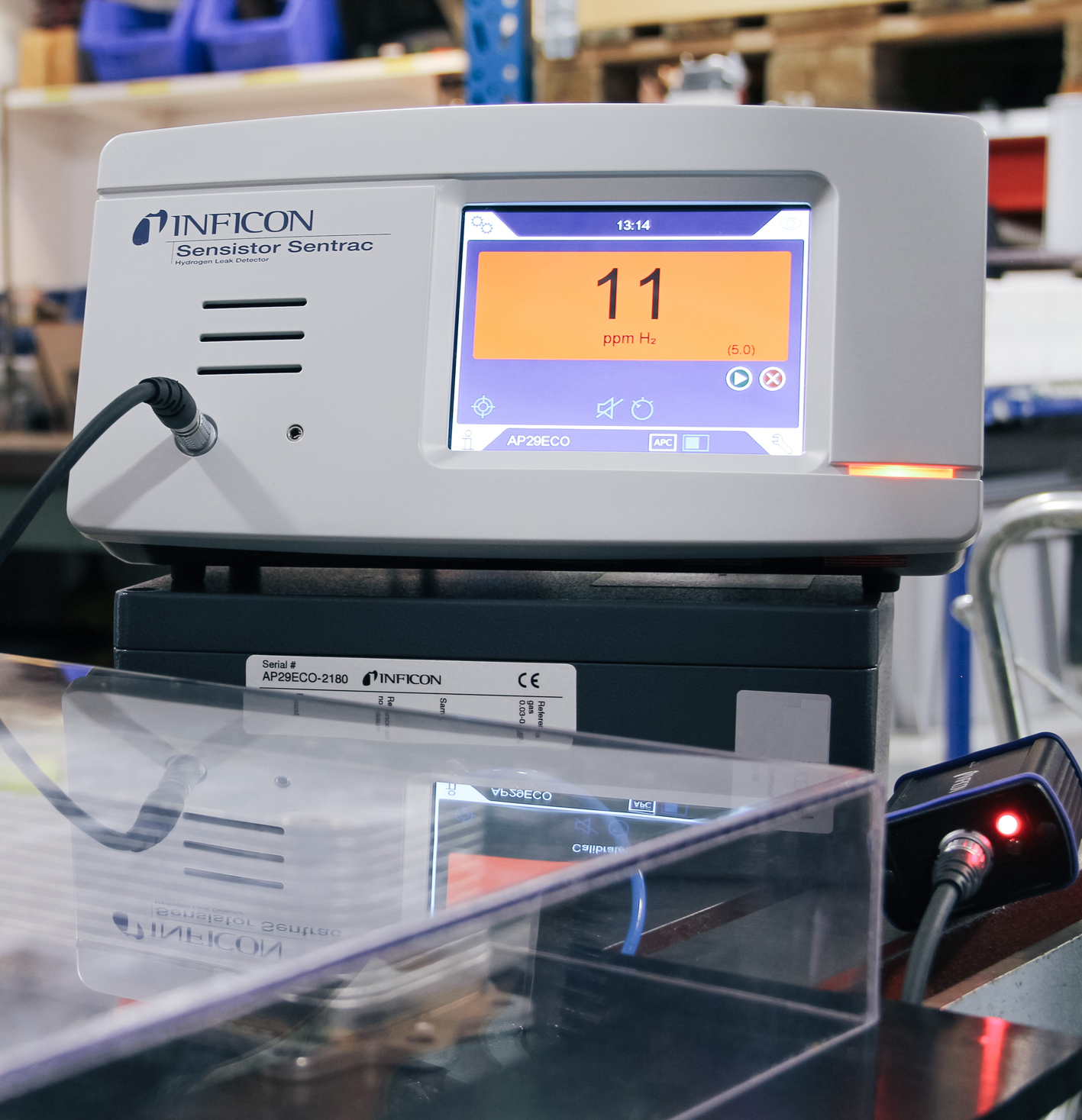
Accumulation Method
For small to medium heat exchangers that need to be tested for water/oil leaks with low to medium throughput, leak detection in an accumulation chamber (accumulation test) provides a highly reliable, cost-efficient solution.
The test begins by pressurizing the heat exchanger with forming gas at operating pressure and placing it in a chamber. A fan placed inside the chamber ensures a homogeneous concentration irrespective of the location of the leak. Any forming gas leaking from the object will remain within the chamber.
The solution from INFICON consists of the Sentrac Hydrogen Leak Detector, with dual probe connection as standard, and the AP29ECO Sampling Probe. Controlled by the Sentrac leak detector, the AP29ECO allows a certain time (accumulation time) before it takes a sample from the chamber and analyses the gas concentration. If the concentration exceeds the set reject level, the Sentrac leak detector gives an audio and visual alarm signal. The sniffer hand probe connected simultaneously to the Sentrac leak detector is then used for pinpointing leaks immediately after the integral test, while the part is still pressurized.
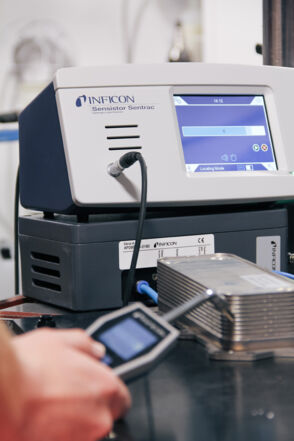
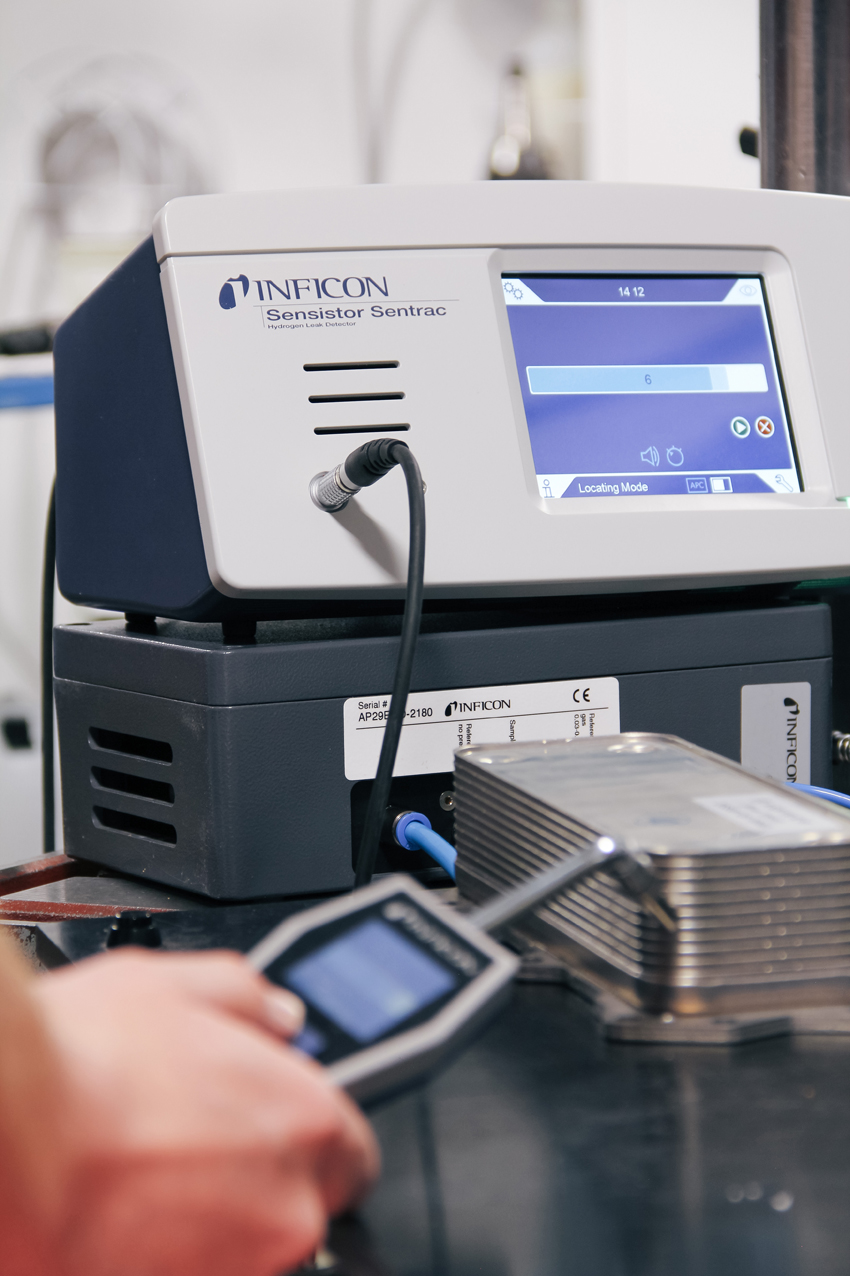
For very rapid leak tests, when extremely small leaks are expected or in all circumstances where a leak detector for both helium and forming gas is preferred, the LDS3000 AQ Leak Detector gives the highest sensitivity. The plate heat exchanger is filled with tracer gas and placed in the accumulation chamber. The LDS3000 AQ measures the speed of increase of the tracer gas level in the chamber and alerts the operator if this rises too quickly.
Vacuum Leak Test
For larger heat exchangers that need to be tested with medium to high throughput, or parts that need to be tested for refrigerant leaks, leak testing with helium in a vacuum chamber is the preferred solution. In this testing procedure, the heat exchanger is filled with helium before vacuum pumps create a vacuum in the chamber. If there is a leak, the LDS3000 Helium Leak Detector detects the helium gas as it exits the heat exchanger and gives an alarm signal.
Interested in Accumulation Leak Testing?
Look at our video or check out our solutions for accumulation leak testing!
Want to Stay Updated on Leak Detection?
Our newsletter offers regular updates on our latest products, applications, upcoming events, and other interesting news.