Over 50 Years of Industrialized Mass Spectrometry
From Balzers, Liechtenstein, to the World and Beyond
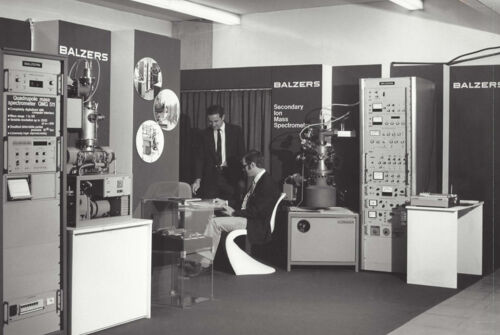
With over 50 years of experience in industrialized mass spectrometry, INFICON is proud to draw on deep technological expertise and a long-standing tradition of innovation. This journey has been shaped by both engineering excellence and the pioneering spirit of individuals like Dipl. El. Ing. ETHZ Remo Vogelsang, former lead electrical engineer at Balzers AG in Liechtenstein. He helped lead the development of the first digitally controlled quadrupole mass spectrometer in the 1970s. Without his and his team’s groundbreaking contributions, our current generation of mass spectrometers would not be possible.
As we look back on decades of development, we want to recognize and honor these achievements. We recently had the pleasure to speak with Remo Vogelsang about the early days of industrialized mass spectrometry, which nowadays plays a vital role in everything from semiconductor manufacturing to lunar exploration and volcanic activity monitoring.
The roots of this innovation trace back to the company Leybold INFICON and Balzers AG, a pioneering force in vacuum evaporation technology based in Liechtenstein. Over time, Balzers AG underwent several restructuring and parts of its instrumentation business were spun off to INFICON. We proudly carry forward this legacy, specializing in industrializing complex sensor and measurement systems.
From the launch of the first quadrupole mass spectrometer in 1967 from Balzers AG to today’s AI-powered smart sensors from INFICON, we’ve enabled precise gas analysis across a wide range of industries. With a strong foundation in system integration and a clear commitment to innovation, we’ve played a key role in making mass spectrometry more accessible, reliable, and impactful for critical applications. Our conversation with Vogelsang sheds light on a defining era of instrument development and reminds us how far we’ve come since the early days of mass spectrometry.
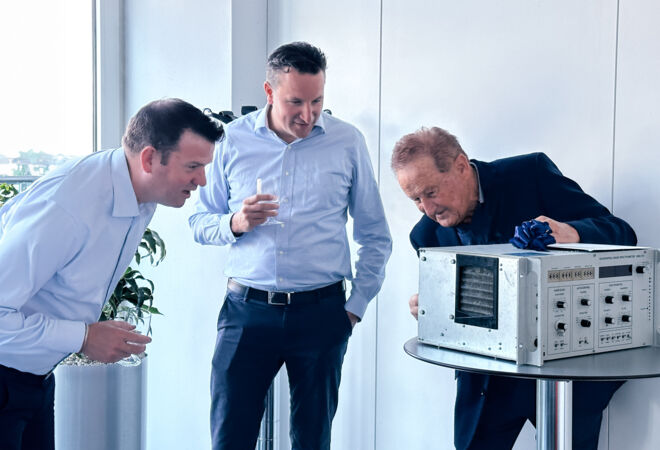
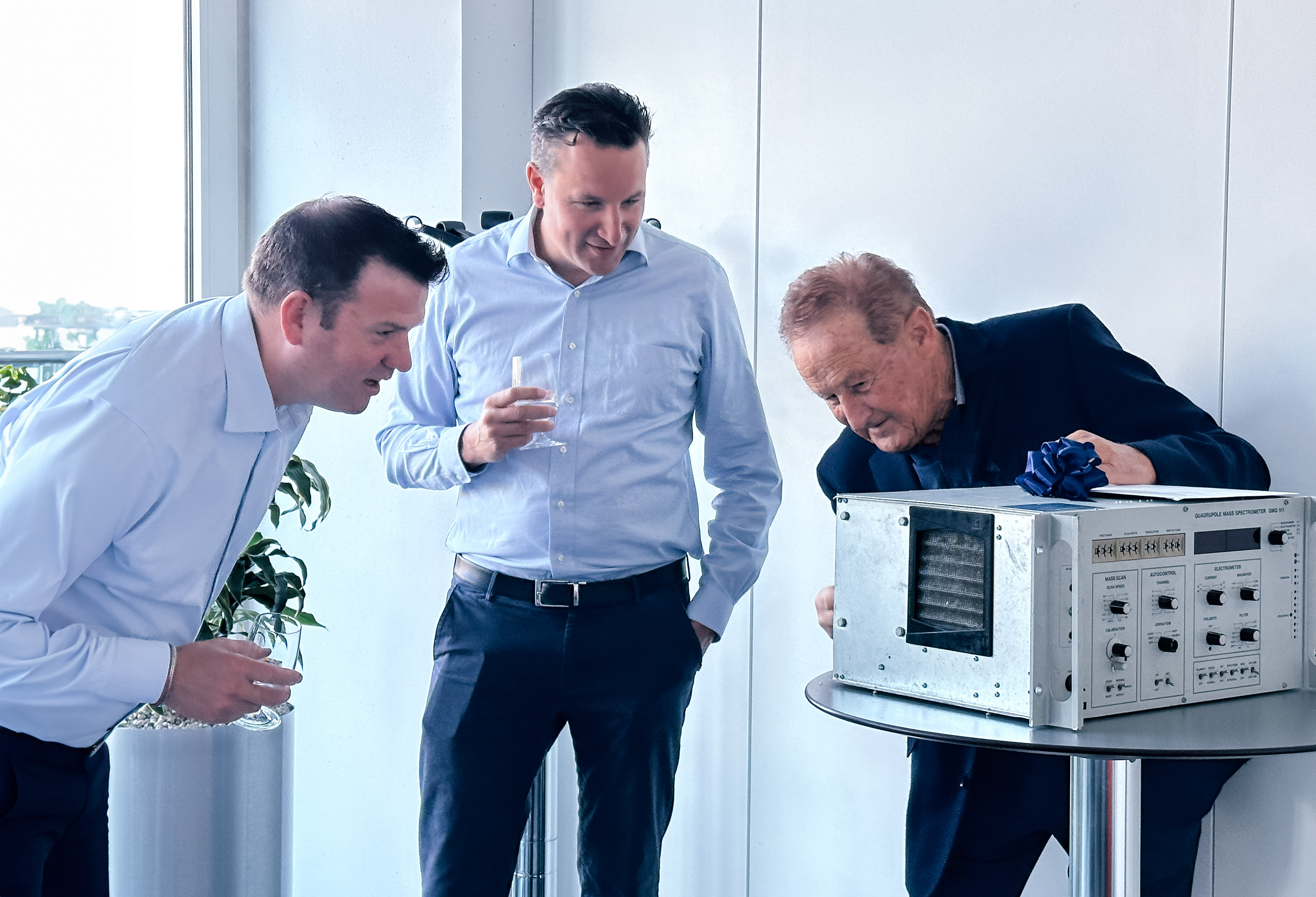
Engineering the QMG 511: From Tubes to Chips
In 1972, Remo Vogelsang joined Balzers AG as electronics were undergoing rapid transformation. Vacuum tubes were being replaced by semiconductors, and integrated circuits were opening up new possibilities for miniaturization and performance. Vogelsang, originally trained in tube-based systems, found himself in the midst of this shift.
Together with Hans Peter Egli, Vogelsang formed the core development team for the QMG 511. Their goal was to evolve the successful QMG 311 model into a more powerful and production-ready instrument. The team worked closely with physicists Dr. Huber, Dr. Rettinghaus and Dr. Selhofer, who were developing the new analyzer, and with marketing experts like Carlo Hofmann and Dr. Clinckemaillie to ensure the device met real-world industry demands.
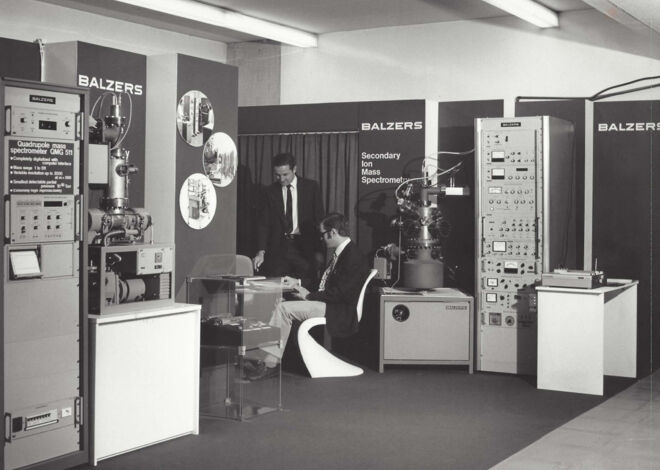
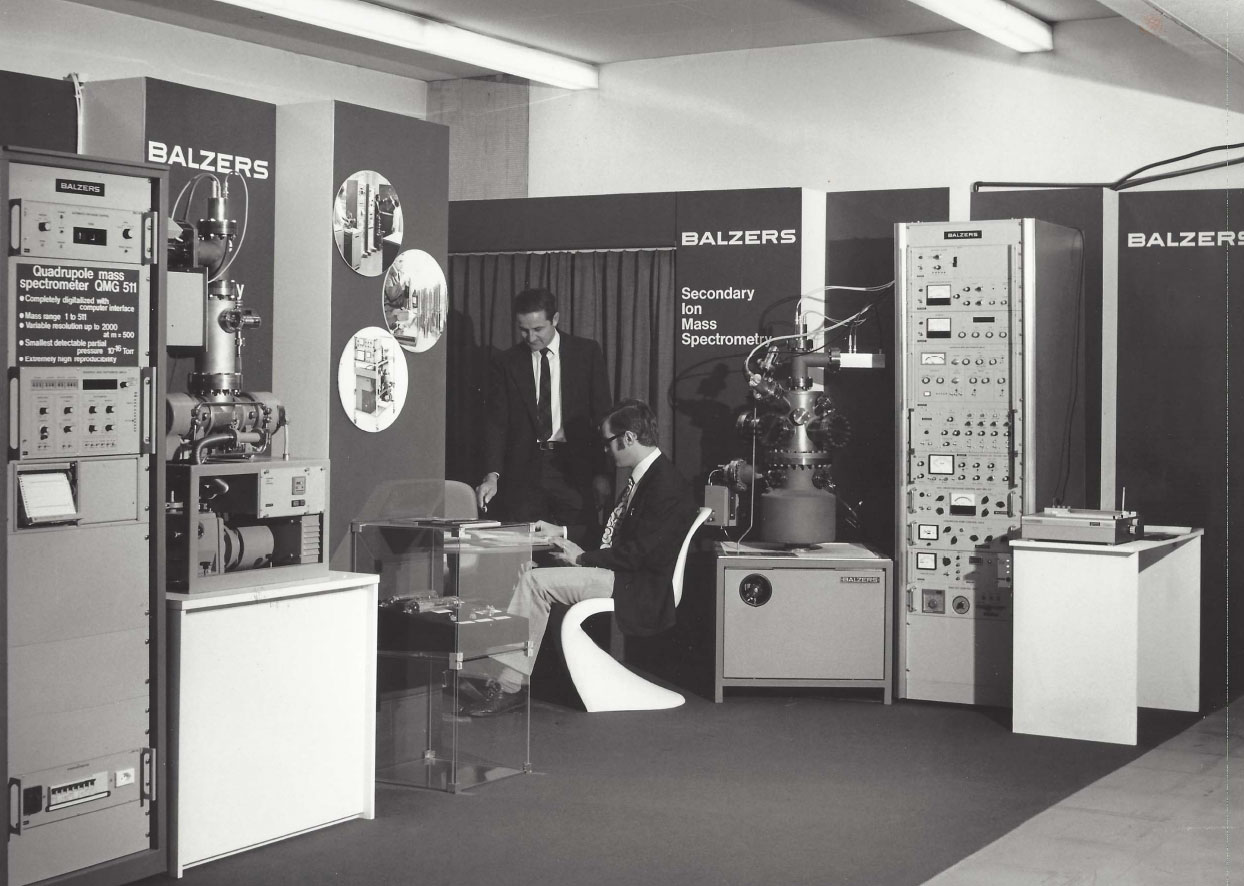
By mid-September 1972, the team had finalized a detailed technical specification. The QMG 511 was ready to launch—and with it, a new chapter in high-vacuum gas analysis began. Vogelsang recalls: “The QMG 300 and its predecessors performed well in laboratories, but their fully analog design made them unsuitable for industrial applications. I found it unacceptable that users had to constantly adjust knobs, making results inconsistent.”
With the QMG 511, he wanted a device that people would eagerly adopt because of its excellence. Vogelsang had two key priorities: First, from a marketing perspective, he wanted a product so good that people would eagerly adopt it. Second, reliability was crucial and he set his own high standards. That’s why the QMG 511 was designed to be both easy to use and simple to manufacture, ensuring seamless production without technical hurdles. It was a fully digital and robust system, finally bridging the gap between analog and digital technology.
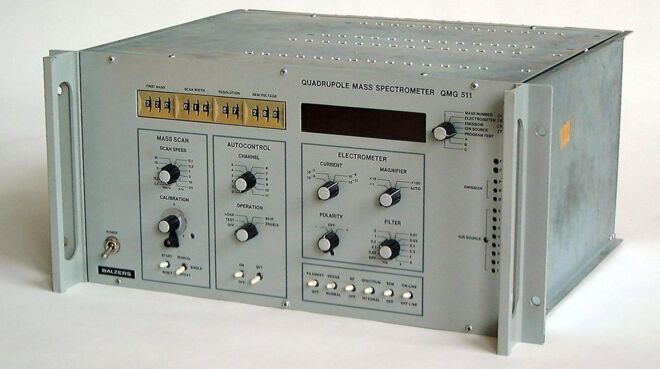
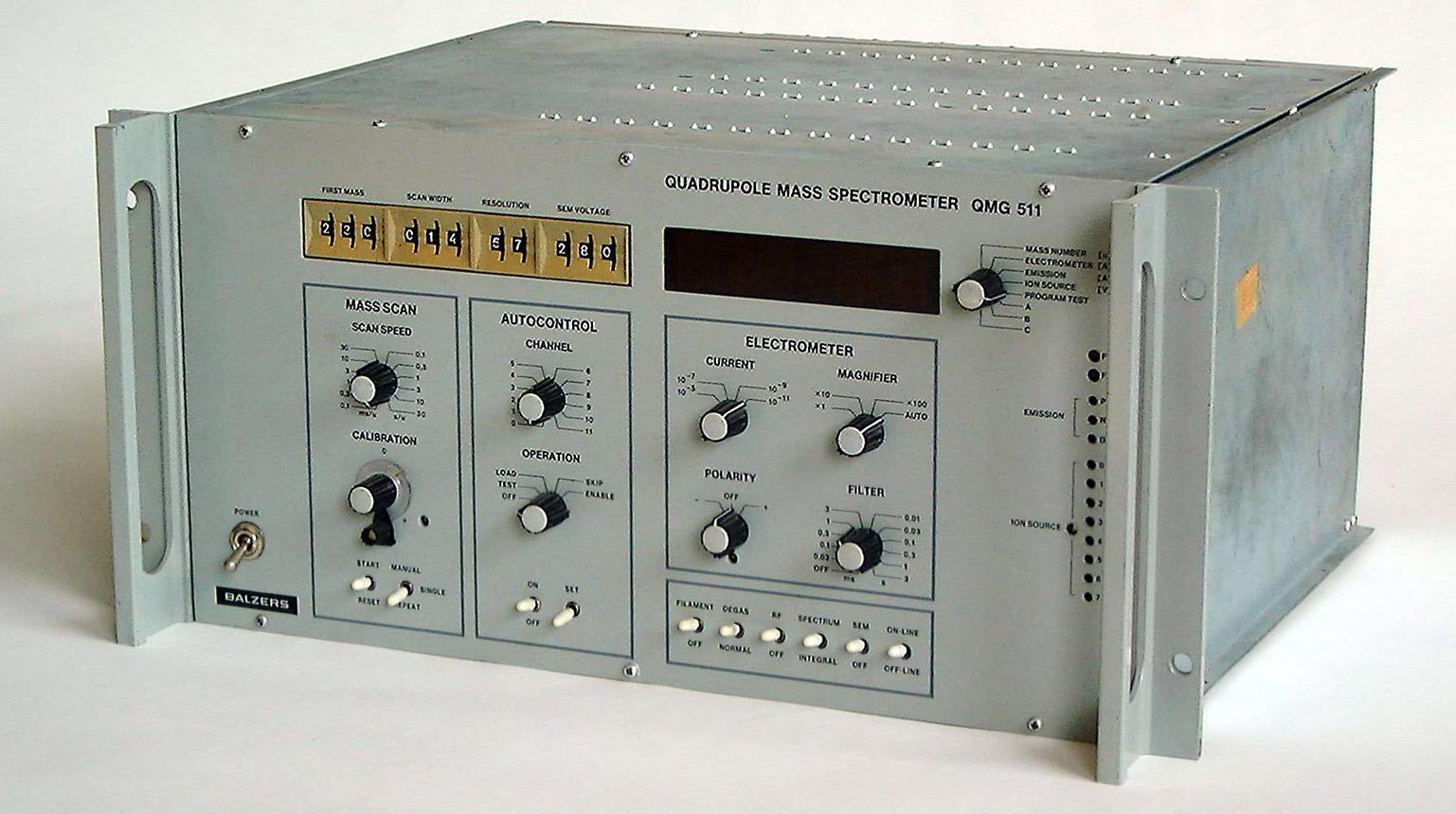
These two principles, strong market appeal and absolute reliability, were essential to Vogelsang and remain just as important today. One of the major engineering challenges was the lack of a 16-bit digital-to-analog converter.
“We had to combine two 8-bit converters,” Vogelsang explains. “That introduced some inaccuracies, which we corrected with a manual potentiometer, a clever workaround that worked surprisingly well.”
The team also tackled limitations in high-frequency signal generation using a gated, clocked switching method.
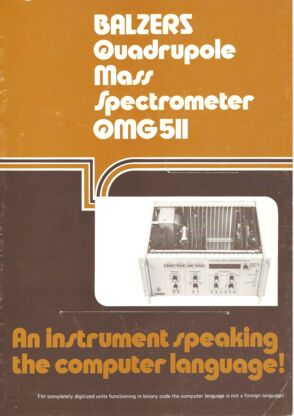
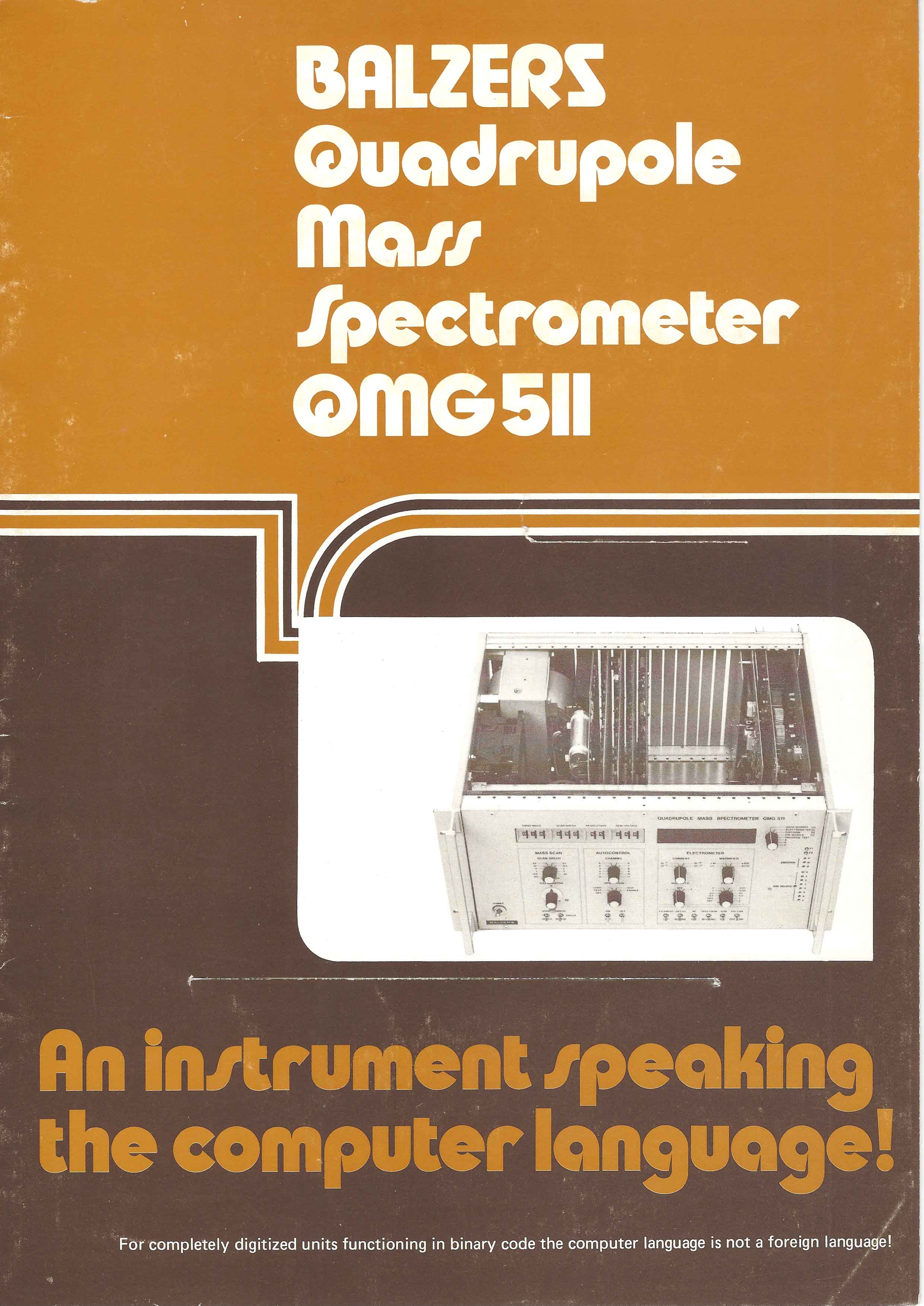
Improving Sensitivity, Speed, and Precision
Over time, mass spectrometry technology has undergone remarkable advancements. Early systems were bulky, required extensive calibration, and had limited sensitivity. Today, modern spectrometers are highly automated, offer real-time data processing, and integrate seamlessly into industrial production lines. INFICON played a crucial role in driving these improvements, building on the legacy from Balzers AG and expanding its expertise across global locations.
From Vogelsang’s perspective, the fundamental principles of mass spectrometry haven’t changed over the last 50 years, but everything else has improved. “What has changed is the reliability, precision, and how specific instruments have become to meet different market needs,” he said. “The basic principle is still the same, but now it’s faster, more compact, and optimized for real-world performance.”
These improvements are reflected in several key milestones in the evolution of mass spectrometry technology, including:
- Higher sensitivity through improved quadrupole and ion source design, critical for semiconductor and portable GCMS applications
- Ruggedness and portability, which are critical for space-ready mass spectrometers and vehicle-mounted GCMS applications
- Electron multiplier improvements to address very low-level detection in semiconductor processing
- Modernization of control systems for smaller, compact high-speed sensor systems
- Miniaturization of the quadrupole for extreme high-pressure applications
- Integration onto compact pumping systems for harsh chemical applications
- Display evolution, from built-in displays to software that mimics the display (SQX and MQX) to Windows-based software control
- Introduction of FabGuard Software, which integrates directly with tools and helps make smarter decisions using RGA data within the context of the manufacturing tool it is supporting
- Custom RGAs designed for Semiconductor Applications include
- Metal PVD monitoring
- Improved lifetime in CVD/ALD and Harsh environments
- Furnace and anneal monitoring
- Selective Etch monitoring
- Custom RGAs for Expanded Market Applications include
- Environmental
- Leak testing applications to monitor refrigerants, automotive, air conditioning
- Lithium-ion battery testing
The Future: Where We Go from Here
We are proud to be a global leader in mass spectrometry. Our technology is trusted by leading semiconductor manufacturers, both toolmakers and chipmakers worldwide. Advanced fabs in Asia, Europe and the U.S. use our mass spectrometers every day to ensure process control, trace gas detection, and contamination analysis at the highest level of precision.
This all began with the QMG 511, the world’s first industrialized mass spectrometer. Ever since, each new generation of our instruments has continued to set the benchmark as top-of-the-line products, empowering semiconductor manufacturers to push the limits of technology and reliability.
But our innovation doesn’t stop at semiconductors. We’re also the leading force in leak detection for EV and consumer batteries, helping ensure safety and performance in electric vehicles, smartphones, and other critical devices. Our HAPSITE mobile labs provide rapid, on-site chemical analysis for emergency response, environmental protection, and military use.
We’ve gone beyond the lab. Our instruments were part of the NASA PRIME-1 mission to the Moon, analyzing the lunar surface and proving the robustness of our technology in extreme conditions. We support pioneering research projects, like volcano forecasting, where our systems detect gas signatures that can provide early warnings for natural disasters. And we even take mass spectrometry underwater, enabling real-time analysis in the deep sea.
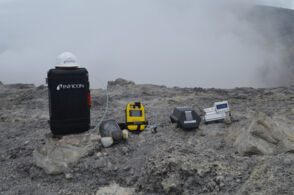

“When we built the first mass spectrometers, we were focused on vacuum chambers and fabs. The idea that one day a descendant of our technology would reach the Moon is incredible,” reflects Remo Vogelsang, co-developer of the QMG 511.
To the next generation of engineers, he offers this advice: “Find what truly fascinates you, something you’re passionate about. In engineering, every detail matters. If one small component fails, the whole system can. When a project is finished, move on. Technology constantly evolves, and that’s what makes this field so exciting.”
As we continue our journey, we remain committed to driving forward the future of mass spectrometry. Here’s to more than 50 years of excellence and to the next exciting innovations still to come in mass spectrometry!
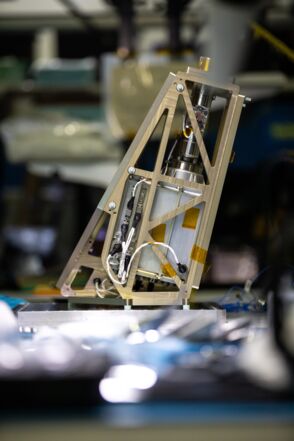
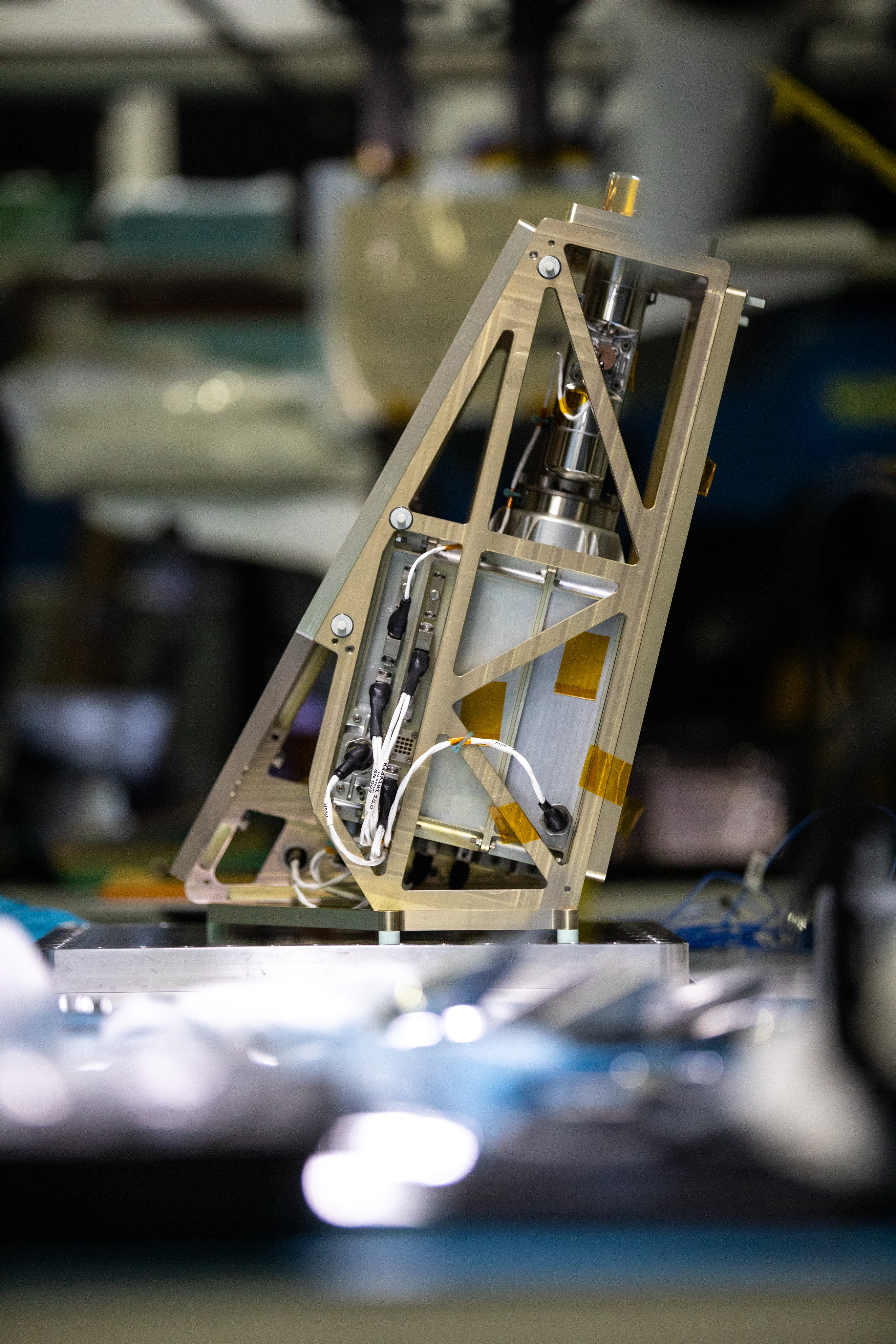
A Timeline of Mass Spectrometry Milestones
Over the past five decades, the development of quadrupole mass spectrometry has been marked by continuous technological advancement. The following timeline highlights key milestones in the evolution of our instrumentation—from the earliest prototypes to today’s smart, connected platforms.
Year | Milestone |
---|---|
1962 | Development begins at Balzers AG, in Liechtenstein on the first quadrupole mass spectrometer |
1967 | Launch of the QMG 101, the first widely usable quadrupole mass spectrometer |
1972 | Introduction of the QMG 511, the first digitally controlled quadrupole mass spectrometer—developed for industrial use |
1973 | Release of the QMG 311, a cost-effective analog alternative to the QMG 511 |
1977 | Introduction of IQ200 (Leybold INFICON) mass spectrometer, the first microprocessor-controlled, digital RGA |
1978 | QMG 064, intelligent RGA with direct output of partial pressures |
1985 | Introduction of Quadrex 200 (INFICON) with first sensor head for RGAs |
1986 | QMG 420 introduces a new control unit and RF generators |
1987 | Quadstar 420 and Plus 420: menu navigation, analysis modes, multistream sequencer |
1992 | QMG 421 with integrated detection modes: Faraday, SEM, ion counting QuadStar 421/2 supports Microsoft Windows Introduction of Transpector Residual Gas Analyzer, compact electronic enclosure sensor mounted, just requiring +24V and serial communications to interface to a PC. Featured auto-ranging electrometer with dual detector (FC/EM). |
1996 | Introduced Transpector XPR residual gas analyzer—the world’s first RGA to work at extended pressure ranges |
1997 | QMG 422 introduces fast auto-ranging and new electrometer amplifier |
2000 | Introduced FabGuard Sensor Integration and Analysis System |
2002 | Quadstar 32-bit software platform |
2004 | Launch of HiQuad and QMG 700: modular, fast, Ethernet-interface QUADERA software suite for intuitive multi-document interface |
2025 | Launch of the QMG 800: INFICON’s next-generation analytical platform |
Interested in Collaborating with us?
Let us know if you are looking for a solution in a difficult and challenging environment, or if you want to collaborate on any of our projects.
Explore more mass spectrometer stories here
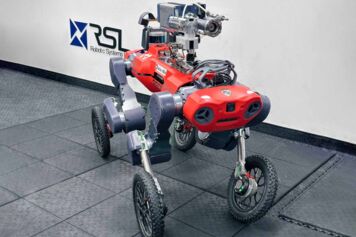
In collaboration with ETH Zurich's Robotic Systems Lab, we are working on a project named ARAMMIS – Autonomous Robots for Area Mapping, Monitoring, and In-situ Sensing.
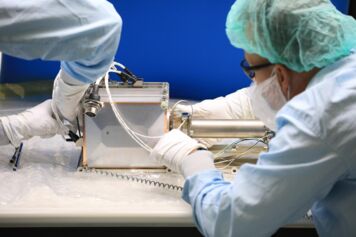
As experts in gas sensing and vacuum measurements in many industries including semiconductor, energy and security, our teams are always looking for the “what’s next” in innovation.
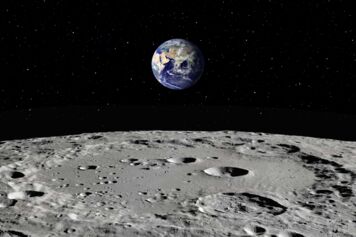
Powering Space Exploration through Lunar Gas Detection
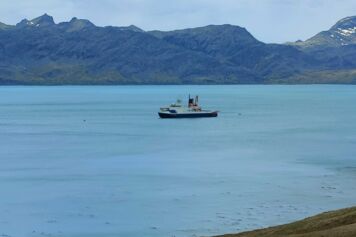
Expedition in the South Atlantic: On the trail of emissions from the seabed
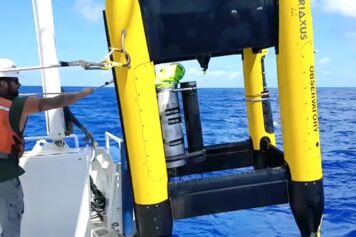
A Collaboration with the University of Rhode Island
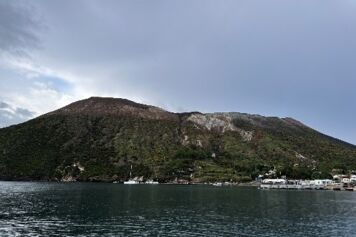
Overcoming Complex Challenges to Protect People and the Environment