Packaging Leak Test in the Food and Pharma Industry
The importance of packaging integrity and how advanced non-destructive packaging leak detectors improve package quality
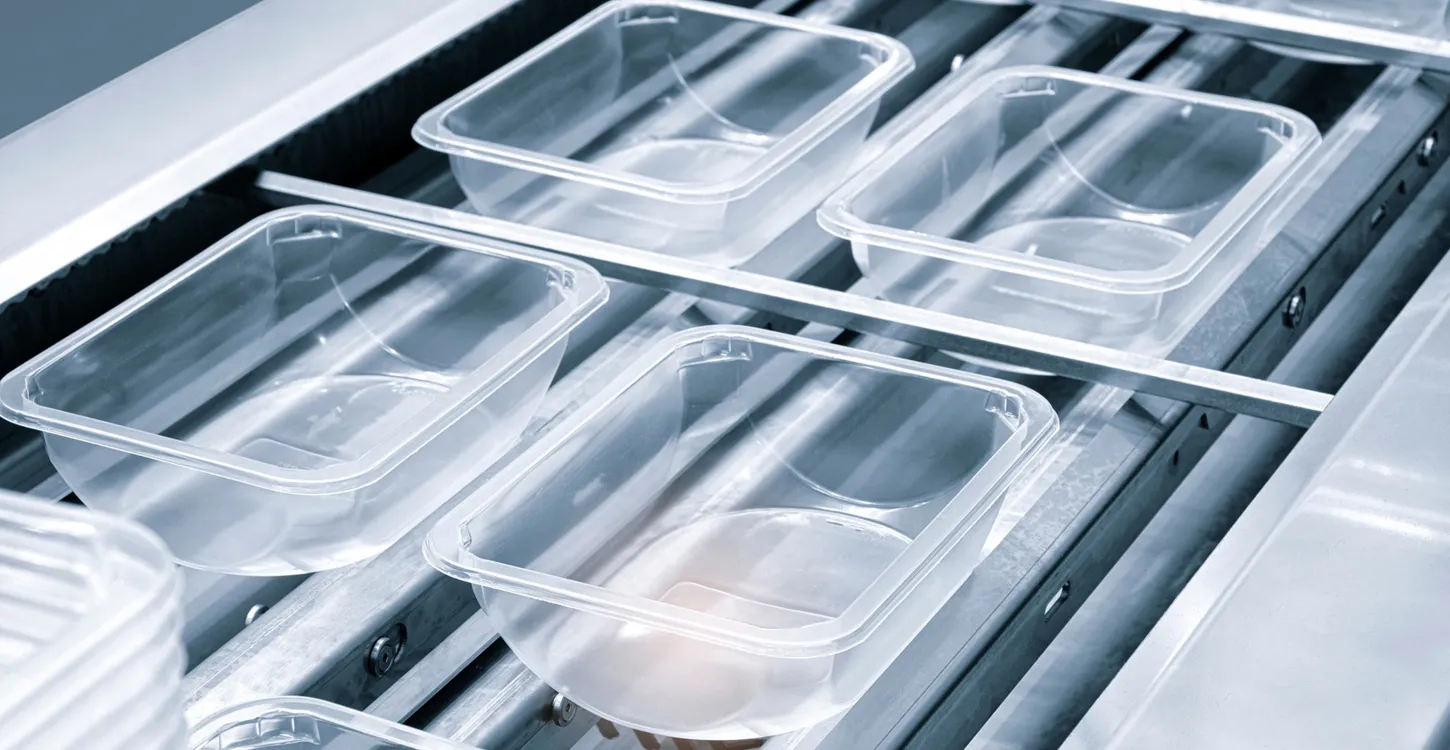
Introduction to Leak Testing
The seal integrity and tightness of packaging are crucial to ensure the quality and safety of products in the food and pharmaceutical industries. Ensuring seal integrity along the entire supply chain not only ensures product quality and safety, but also strengthens consumer confidence. Leaking packaging can lead to contamination, spoilage or loss of product efficacy. It is therefore essential that packaging is thoroughly tested for leaks to ensure that it reliably protects the contents.
Package Leaks Despite Leak Testing
In addition to microscopic leaks in the packaging material or errors in the sealing of the packaging, the effects of environmental factors such as temperature fluctuations, humidity or exposure to light can impair the integrity of packaging and packaging materials and lead to contamination or spoilage of the goods.
It is particularly problematic when foods such as coffee, despite passing the leak test, leak and subsequently spoil prematurely. This can result in significant losses and a decline in consumer confidence in the respective manufacturer or packaging form. In turn, a thorough inspection of the packaging not only protects the products, but also promotes customer trust and satisfaction.
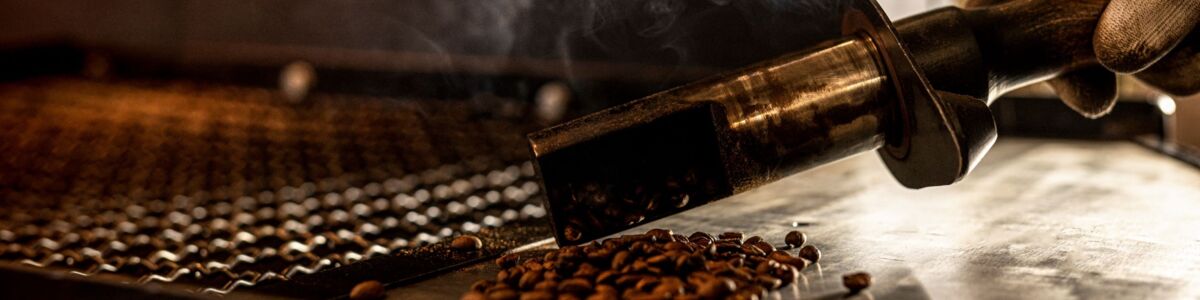
Download our Free Whitepaper
The following overview shows common topics and methods in packaging testing:
Seal testing and seal testing
Packaging often develops leaks or holes at the sealed seams. Seal testing, also known as seal testing, is a generic term for various methods of testing the tightness of sealed seams in packaging. Such tests are particularly important to ensure that the sealed seams do not leak and that the packaging is completely sealed. This prevents, for example, moisture from entering the packaging or the contents from being contaminated in any other way.
Leak testing of modified atmosphere packaging (MAP)
Modified atmosphere packaging (MAP) is often used to package sensitive food. Instead of air, the packaging around the actual product is filled with a suitable gas to ensure a longer shelf life for the product. A leak test on the packaging ensures that this modified atmosphere remains in the packaging for a long period of time and that there is no exchange with the ambient air, thus preserving the freshness and safety of the products.
Container Closure Integrity Testing (CCIT)
Container closure integrity testing (CCIT) is important to ensure that container closures do not leak. These tests are particularly important in the pharmaceutical industry, where container integrity is critical to the safety and efficacy of products.
Traditional methods of leak testing
The bubble test (bubble leak test), also known as the bubble tightness test or water bath test, is a widely used method for easily and inexpensively finding leaks in packaging. The gas-filled package is placed in a water bath and then observed to see if gas bubbles rise. The method is therefore only suitable for waterproof types of packaging. The great advantage of this method is that the user receives an easy-to-interpret result: if bubbles rise, the packaging is leaking. If no bubbles rise, the packaging is considered to be sealed. The limitations of this method include the fact that small leaks can easily be overlooked and that it is not possible to detect very small leaks. Furthermore, the contents of a leaking package must be disposed of and cannot be repackaged. Sometimes the packages tested burst under the pressure in the water bath, which may require the water bath to be cleaned. Furthermore, it is not possible to specify a leak rate, which means that an objective comparison of two packages is not possible.
Dye Penetration Tests
Dye penetration tests, such as the Rhodamine dye test, are invasive and destructive methods for leak testing. In these tests, dye solutions are applied to one of the two sides (inside or outside) of the packaging and visually inspected for dye transfer to the other side. Although effective, they destroy the tested packaging and are therefore not suitable for all applications. It is also difficult to quantify the size of the leak using dye penetration tests.
Pressure Decay Leak Test
Pressure decay leak tests are another method of leak testing. In this method, the pressure in the packaging is monitored. Often, a stamp is used to press on a large area of the packaging and the packaging height is determined. After applying as much pressure as possible to the packaging for a defined period of time, the height is determined again. If it has decreased, this indicates a leak. This method can be easily automated, but it cannot detect the smallest leaks. As with the bubble leak test, there is also a risk of the packaging bursting during the test.
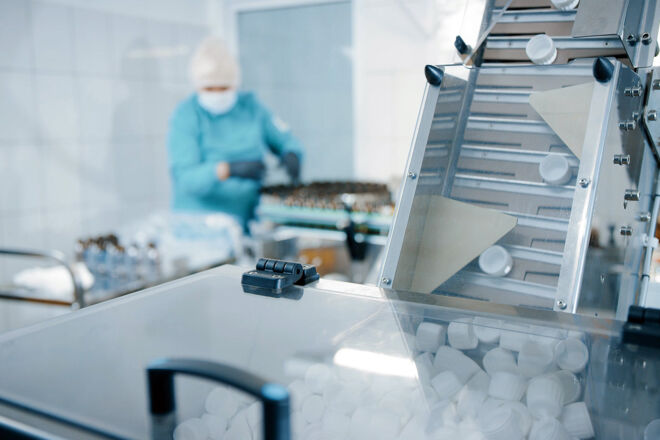
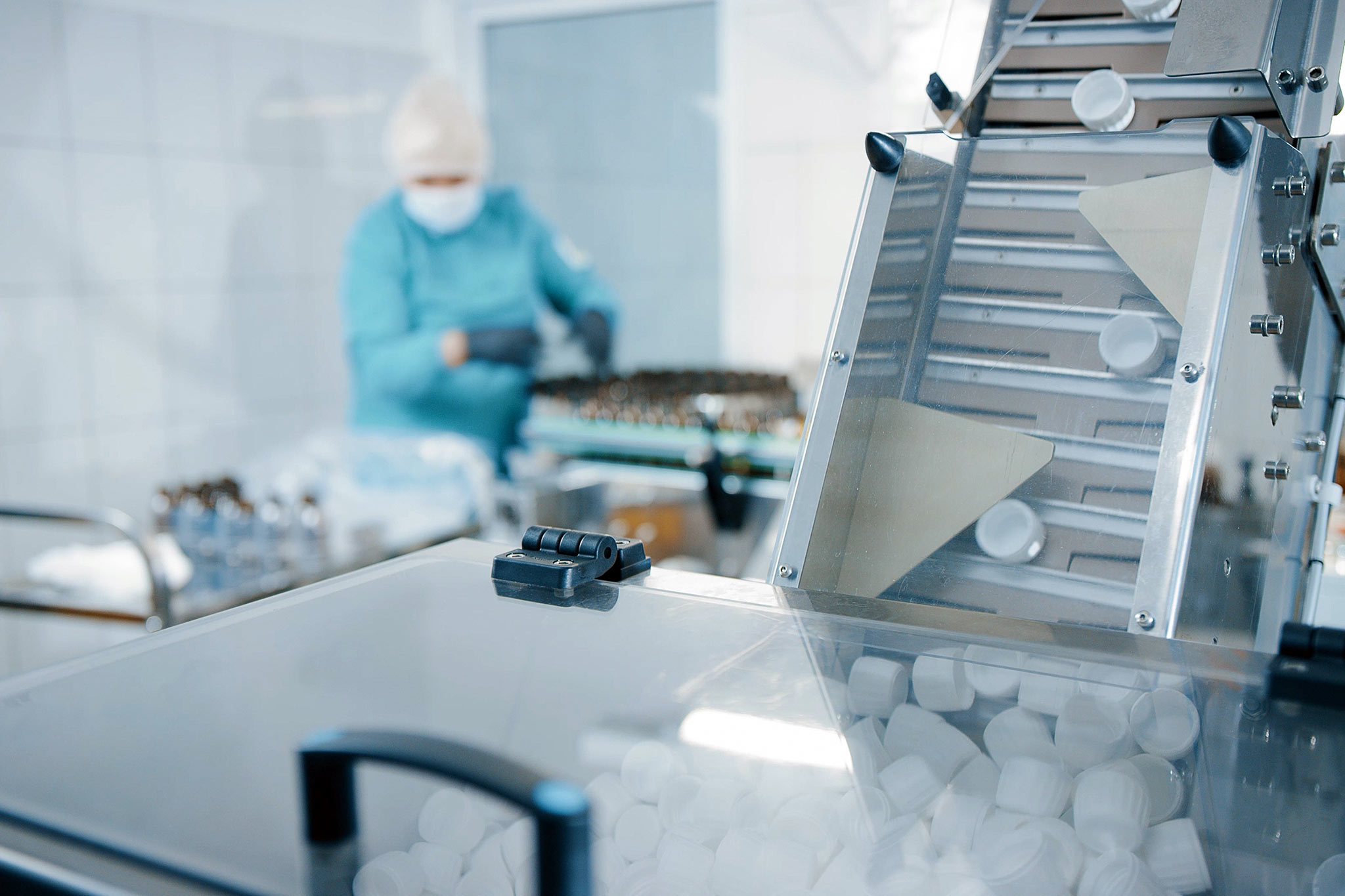
Pressure Rise measurement
In recent years, pressure rise measurement has established itself as a particularly effective method of leak detection. In this process, the packaging is placed in a vacuum chamber and any increase in pressure in the chamber is observed using pressure sensors. If the packaging is not airtight, gas will escape from the packaging into the vacuum chamber, causing a measurable and quantifiable increase in pressure.
The Contura S is a seal testing device that implements this method at the highest level. Two flexible membranes are placed directly on the surface of the packaging. This protects the packaging, which could otherwise burst in the vacuum. On the other hand, the accuracy of the leak detection is improved by minimizing the chamber size. The flexible chamber allows for quick testing of a wide variety of packaging types. These can be both rigid (e.g. cans) and flexible (e.g. bags of crisps). It is also easy to switch between different types of packaging without the need for any modifications. The Contura S offers precise and reliable leak detection and is ideal for leak testing in the food and pharmaceutical industries. It sets new standards in this field and offers outstanding accuracy and reliability.As the food and pharmaceutical industries evolve, so need the methods and technologies for packaging and testing be up to date. These innovations are vital for addressing the ongoing challenges of packaging integrity and safety.
Conclusion
The choice of the right method for leak testing depends on the specific requirements and conditions. As the food and pharmaceutical industries continue to evolve, packaging and testing methods must also remain up to date.
Modern technologies, such as pressure rise measurement with the Contura S, represent a significant advancement in package leak testing, overcoming the limitations of conventional methods like visual inspection in a water bath. They set new standards in quality assurance.
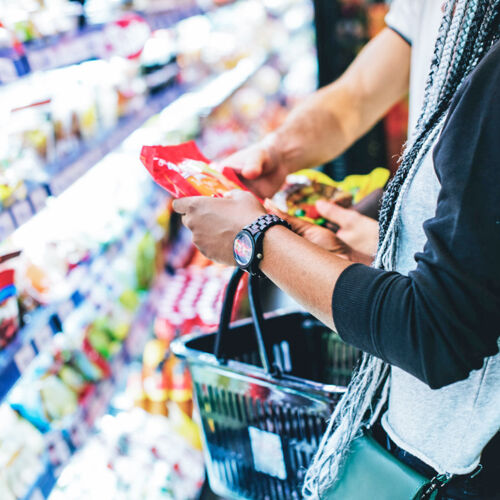