Reduced Total Cost of Ownership with EcoBoost
The Intelligent Function for LDS3000 Leak Detectors
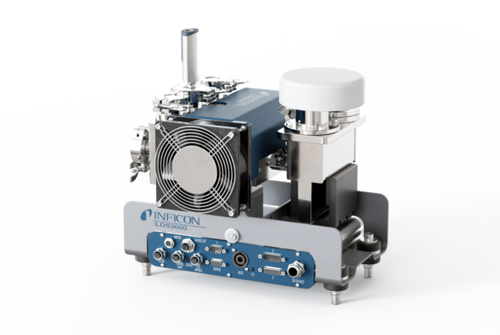
Juan, an experienced employee with 15 years of experience at the company, works for a Spanish company that produces aluminum transmission housings and battery trays and lids for the automotive industry. In his role as production manager, he recently faced a daunting challenge: reducing production costs by 20% to remain competitive in the market. Determined to find solutions, he delved into research, seeking out potential areas for savings.
When analyzing the detailed cost structure, Juan discovered that helium costs had risen over the last two years and were significantly contributing to the high production expenses. With 25 production lines requiring leak detection, the helium expenses were adding up quickly.
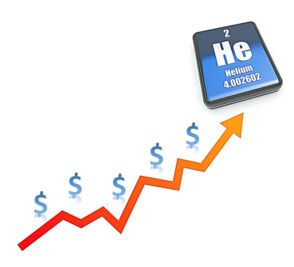

Seeking solutions, Juan reached out to the manufacturer of the leak testing systems for advice. Among some other suggestion, Miguel, the project leader from the equipment manufacturer, could make on increasing efficiency, he had also just received news from INFICON about their latest innovation: the EcoBoost feature for the LDS3000 leak detection system. This new feature promised to optimize helium usage in leak detection processes, potentially reducing costs without compromising efficiency.
Building on the excellent repeatability and linearity of the LDS3000, EcoBoost makes it possible to accurately predict the decrease of the helium background. The helium background forecast is taken into account to create a higher effective sensitivity of the helium leak detection system in industrial applications. |
---|
Juan learned that with EcoBoost small helium leak rates can be detected with high reliability even on an elevated and still decreasing background. Miguel explained that all of his leak testing systems were setup for short cycle times to meet the high throughput of his production lines. As in many industrial leak testing systems, this was achieved by starting the measurement while the helium background was still decreasing as the desired cycle time did not allow to wait for full pump down. Miguel explained that if smaller leak rates can be detected reliably (although the still decreasing background), this can be used to work with lower concentrations of helium, as in fact this will make a leak rate show up as a smaller leak rate in the detection process.
As this sounded very promising to Juan, he invited Miguel, the project leader from the equipment manufacturer, to test the EcoBoost feature in his production. Miguel promptly arrived at the facility and retrofitted one of the production lines undergoing maintenance with the new feature. Juan had ordered two bottles of test gas for the trial, one with 30%, one with 10% helium in air.
They started the test with 30% helium mixture and after adjusting the equipment settings, this yielded very promising results. A 1*10-5 mbar l/s test leak (representing the reject leak rate for the parts) could be detected very reliably with high repeatability (deviations well below 10%). Encouraged by these findings, Juan and Miguel decided to push the limits further and conducted tests with just 10% helium concentration. To their surprise, the system still performed with high repeatability, even with the reduced helium concentration.
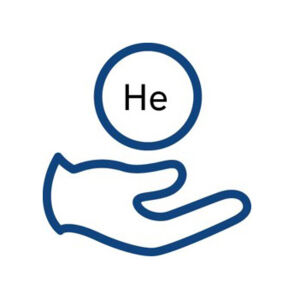
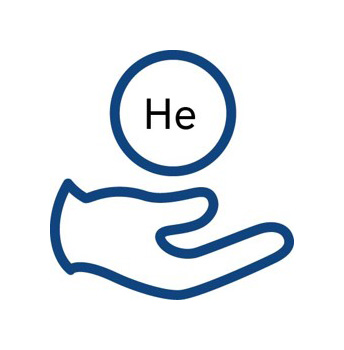
Juan was very encouraged by the trials and decided to order a helium mixer from his system integrator and run the line with 10% helium for a while for a longer-term test. For a four-week trial, he also implemented that a master part with the 1*10-5 mbar l/s leak installed was tested every two hours to see the long-term stability of the solution. The leak was detected at all times. After the four weeks trial, he also did some statistical analysis of the results and saw that the rate of defective parts detected stayed the same.
Confident in the efficiency of the EcoBoost feature, Juan made the decision to place the order to retrofit all 25 production lines during the next maintenance cycle. Over the course of 6 months, all helium leak testing systems were updated with EcoBoost. After completion of all production lines, a staggering 90% reduction in helium costs was achieved for the company, leading to substantial savings. The investment cost for the helium mixer and the cost of retrofitting the 25 leak testing systems was compensated by the helium savings within one year.
The saved budget of the consequent year was reallocated to address other critical investment needs, ensuring the continued success and sustainability of the facility.
Juan's strategic decision to implement EcoBoost not only significantly reduced production costs but also played a vital role in preserving the viability of the company's operation.
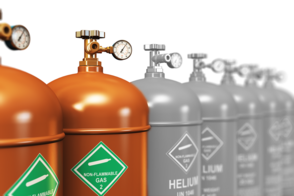
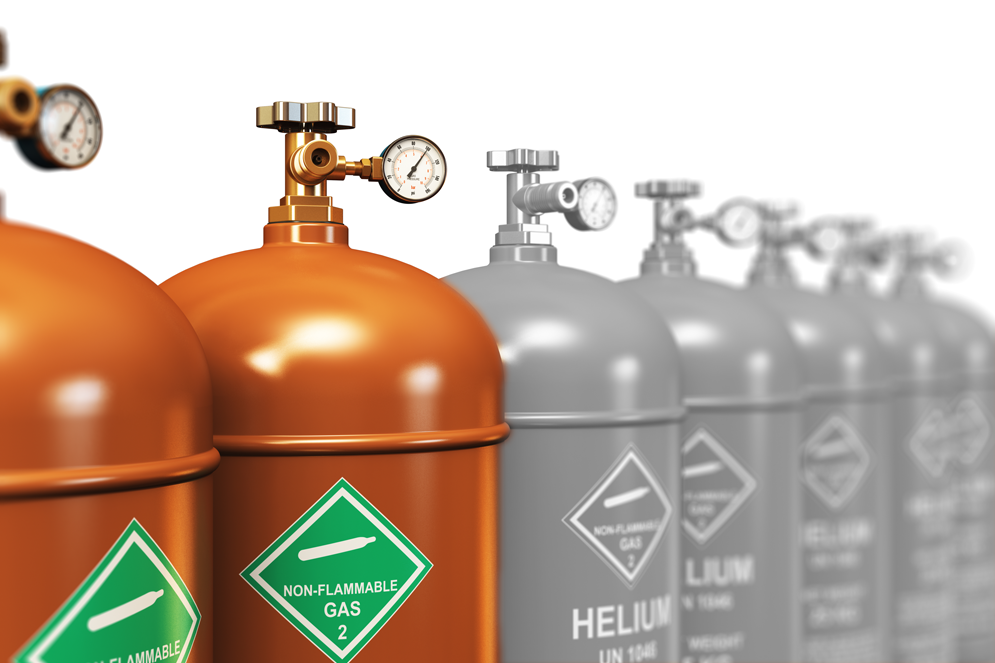
Juan was very satisfied with the collaboration with his supplier (the system integration company) and felt they really advised him well. When the company started planning two extra production lines for the production of battery pack coolers later in the year, Juan turned to Miguel again.
If you are interested in more information about EcoBoost, just register for our On-demand webinar about EcoBoost