Smart Scheduling for the Future
Accurate, Effective Scheduling, and Decision Visibility
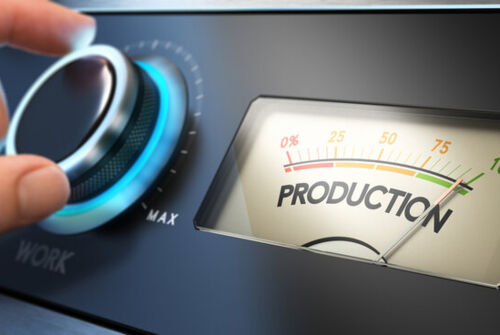
The INFICON FPS Factory Scheduler provides accurate plans for factory operations that respond to rapidly changing business conditions.
Informed by deployments in process areas across factories around the world, not long ago, we released new versions of the Factory Scheduler application. These new releases include features that expand our capability to make accurate scheduling decisions for the dynamic and complex scenarios seen in semiconductor factories, and improve visibility into the calculations behind those decisions.
See Us at Upcoming Exhibitions Worldwide
Don't miss the chance to experience our latest innovations in person. We will be showcasing cutting-edge solutions at industry-leading exhibitions around the globe. Explore our full exhibition calendar to find out where you can meet us next and see how our technologies are driving the future.
Decision Visibility
Knowing how Factory Scheduler is making decisions is key to knowing that Factory Scheduler is making the right decisions. We have significantly improved the visibility of the underlying calculations that are used in a decision of which process tool to schedule and when to schedule it.
For example, when a lot is scheduled, every tool that was a scheduling option at the time is assigned a score. Factory Scheduler now displays the relative scoring for each available tool with detailed explanations as to how those scores were calculated to provide better visibility into the scheduling decisions.
Throughput Modeling for Disc Batching Processes
Disc Throughput more accurately determines overall batch processing times, leading to improved schedules for tool utilization and next step arrival.
Correctly modeling the throughput of each tool and recipe combination across all equipment types in a factory is critical for accurate scheduling. Knowing how long each process will take is a key factor in transitioning from simple, isolated dispatch lists to an integrated factory schedule.
The added support for Disc Throughput, is the fifth major throughput model in the FPS Scheduler. Disc Throughput improves process time modeling for tools that run multiple wafers in a batch that is less than the size of a full production lot – a common characteristic in some implanters and other tools.
Complex Queue Timer Management
Queue timers (time limitations between processing steps) are critical for quality management in semiconductor manufacturing. Support for queue timers has been available in the Factory Scheduler since its inception.
We have enhanced our existing queue timer management logic to improving handling of more complex queue timer scenarios such as overlapping, back-to-back, and/or cross area queue timers. This change results in improved operational effectiveness without compromising the overall queue timer quality.
The Scheduler of the Future
The future of Factory Scheduler is about tighter integration across the enterprise, as well as improved analysis and optimization of the scheduler based on how well the scheduler meets the factory business objectives.
Integration throughout the Enterprise
From factory level integration between Factory Scheduler and systems like FabGuard® or the Metrology Sampling Optimizer, to business level integration with our Capacity Analyzer or Maintenance Optimizer, the future of the Factory Scheduler is as part of an integrated ecosystem for the business. This integration will enable quicker responses to changing conditions within the factory and also across the entire business.
Improved Analytics and Optimization
Building and extending upon our existing Key Performance Indicators (KPIs), upcoming versions of Factory Scheduler will provide a better understanding into how the Factory Scheduler is improving business objectives. The first step will be improved visibility into how the configuration of the Factory Scheduler is influencing the KPIs. Later versions will enable the system to recommend and eventually implement changes to configurations based on optimization of the scheduler to the business goals.
Read more Smart Manufacturing articles
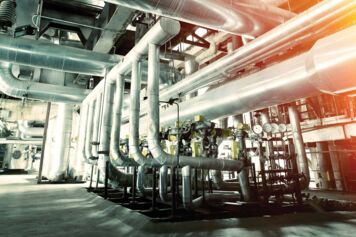
Visualize, Monitor, and Control the Subfab
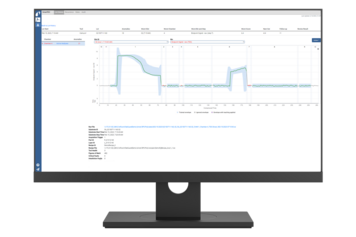
A well-configured FDC system requires intimate knowledge of processes, equipment, and failure modes as well as a concerted effort to setup and maintain the system. Even when it is fully set up, it is only as good as the fault conditions that have already been conceived.
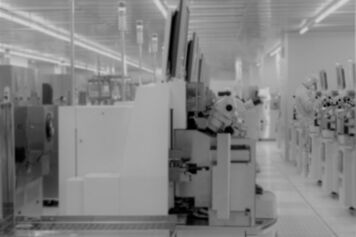
Following the success of FDC solutions in front-end wafer processing, several semiconductor manufacturers have chosen to implement FDC in their back-end wafer assembly processes.