Understanding the Bubble Leak Test Method
How it works in detail, and what typs of more reliable, non-destructive packaging test solutions are available
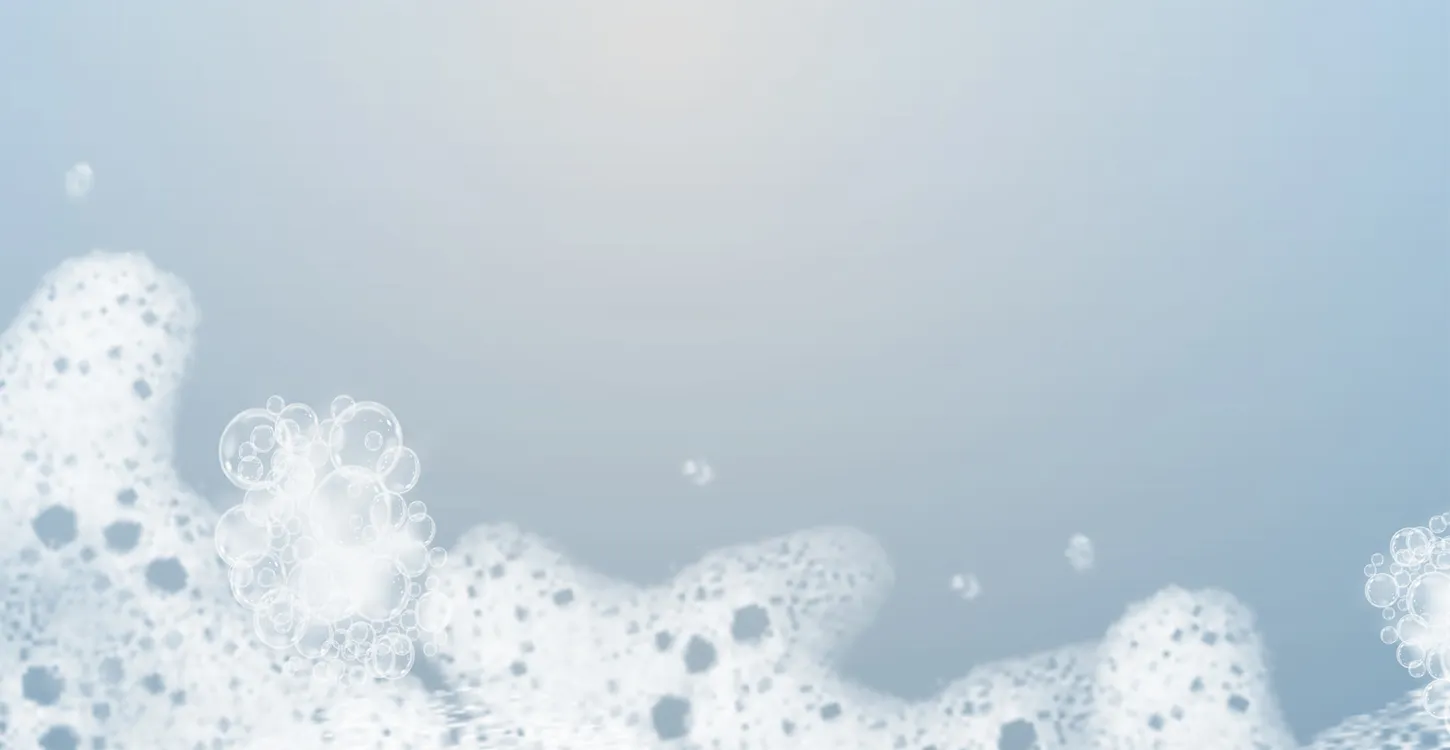
The bubble leak test, also called water bath leak test or bubble emission test, is a widely used and effective method for detecting leaks in various packaging and sealed systems. This testing technique is particularly valued for its simplicity, cost-effectiveness, and versatility across a range of applications but it has several limitations and disadvantages compared to advanced package leak detectors.
What is the Bubble Test?
The bubble leak test is a method used to identify and locate leaks in packages or containers and it can be used as seal integrity test. It involves immersing the test specimen in a liquid, typically water, and then applying a vacuum or pressure differential. Any leaks in the specimen will allow air or gas to escape, forming visible bubbles in the liquid. This simple visual indication of a leak makes the bubble test leak method an accessible and straightforward choice for many industries to test packaging quality.
How Does the Bubble Leak Test Work?
Test Procedure
- Preparation: The test specimen is prepared by sealing it if necessary and ensuring that it is in a condition representative of its intended use.
- Immersion: The specimen is immersed in a chamber filled with the test liquid, often water, and the chamber is sealed.
- Pressure Differential: A vacuum is applied to the chamber, or pressure is applied internally to the specimen. This causes any gas or air inside the specimen to seek a path of least resistance, escaping through any existing leaks.
- Bubble Observation: Observers watch for the formation of bubbles, which will occur at the location of any leaks. The size, frequency, and location of the bubbles provide information about the size and nature of the leak.
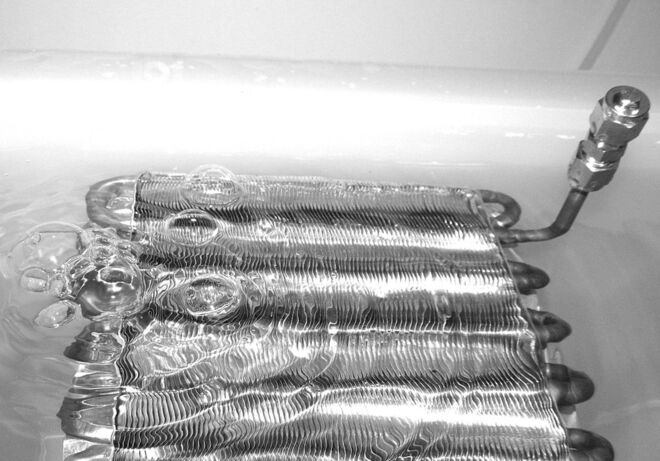
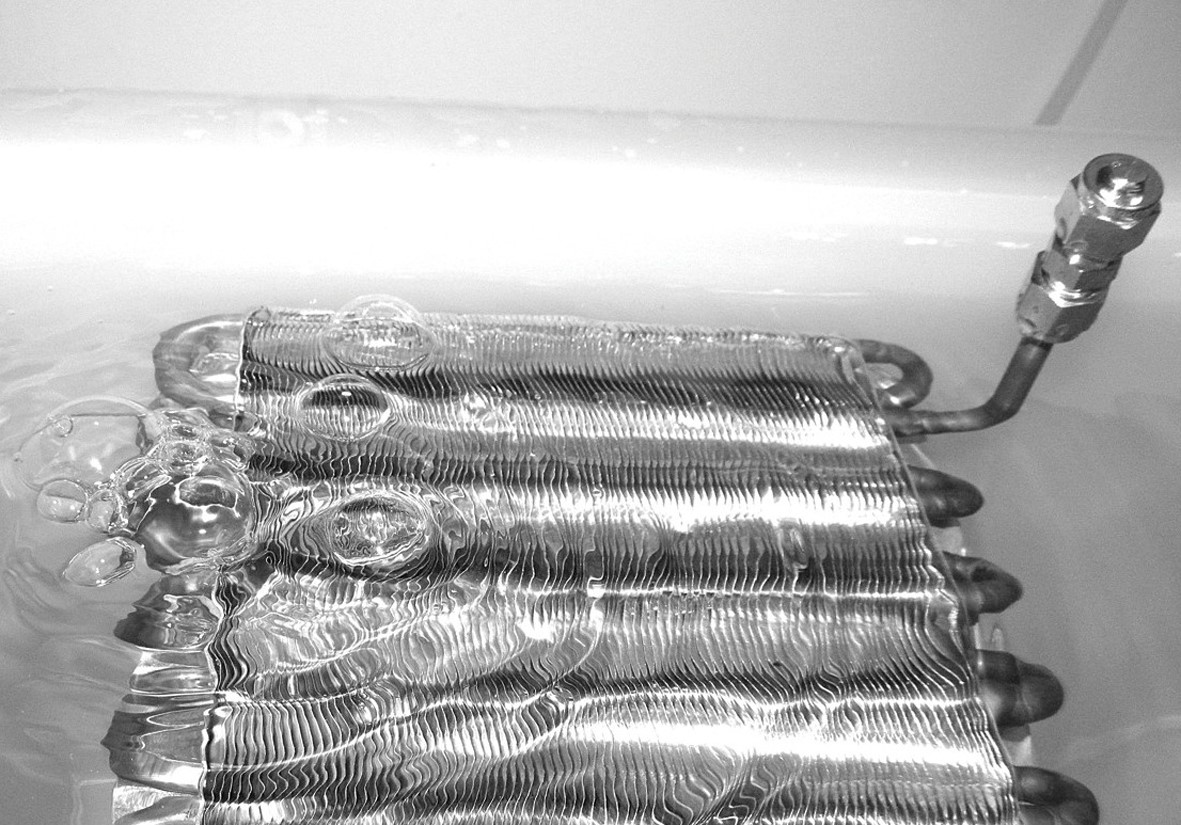
Applications of the Bubble Leak Test
- The bubble leak test is used in various industries and applications, including:
- Packaging: Ensuring the integrity of food, pharmaceutical, and consumer product packaging by identifying leaks that could compromise the contents.
- Medical Devices: Testing the seals and joints of medical devices to ensure sterility and performance.
- Automotive and Aerospace: Checking components like fuel tanks, radiators, and air conditioning systems for leaks.
- Consumer Products: Verifying the integrity of products like inflatable items, electronics enclosures, and sealed containers.
Advantages of the Bubble Leak Test
- Simplicity: The test requires minimal equipment and is straightforward to perform, making it accessible for a wide range of applications.
- Cost-Effectiveness: Compared to more complex testing methods, the bubble leak test is relatively inexpensive and quick to execute.
- Visual Indication: The formation of bubbles provides a clear and immediate indication of leaks, making it easy to identify and address issues.
Limitations and Considerations
While the bubble leak test offers numerous benefits, there are some limitations to consider:
- Sensitivity: The test may not detect very small leaks, as the pressure differential and the viscosity of the liquid limit bubble formation.
- Subjectivity: The test relies on visual observation, which can introduce subjectivity and potential human error.
- Destructive: The packaging is no longer sellable after testing. Additionally, moisture penetration or seal stress can lead to false positive results or even cause the package to burst
- Environmental Conditions: Temperature, pressure, and the properties of the test liquid can affect the test's accuracy and sensitivity.
- Material Composition: Modern packaging increasingly relies on sustainable materials that may not be waterproof over the long term, making them unsuitable for water bath testing.
Better Alternative the Bubble Leak Test
While the bubble leak test remains a popular choice for leak detection due to its simplicity and cost-effectiveness, it is no longer considered state-of-the-art. The test's reliance on human observation and limited sensitivity can lead to inconsistent results, especially for detecting small leaks. In industries where precision and reliability are critical, more advanced technologies have become necessary.
One such advanced solution are the package leak detector Contura S-Series. These advanced leak detection system offer several advantages over traditional bubble testing:
- Precision and Sensitivity: The Contura S-Series provides highly accurate leak detection with sensitivity to the smallest leaks, far surpassing the capabilities of bubble testing.
- Automated Testing: The system automates the testing process, eliminating human error and subjectivity. This ensures consistent, repeatable results across a wide range of test specimens.
- Speed and Efficiency: With rapid test cycles and easy integration into production lines, the Contura S-Series enhances productivity without compromising accuracy.
- Non-Destructive and Versatile: Unlike the bubble leak test, the Contura S-Series is non-destructive and suitable for various applications, from packaging and medical devices to automotive and aerospace components.
If you are interested in learning more about how the Contura S-Series can provide a more reliable and modern testing solution, please contact us for a free packaging leak test demo. This will allow you to experience firsthand the benefits of this advanced technology and how it can improve your quality assurance processes.
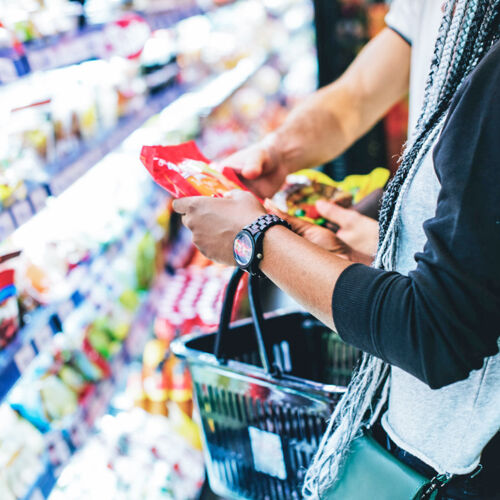