Capacity Model
Fast. Tactical. Manageable.
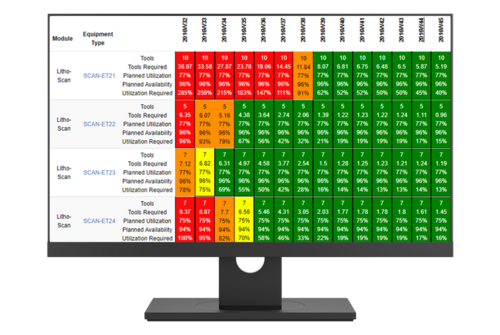
The Challenge
When planning for a production ramp or mix change, it is critical to have an accurate model to estimate capital expenditures and evaluate capacity constraints from different what-if scenarios. Capacity Analyzer creates estimates of tool utilization for given starts profiles using precise factory data and advanced algorithms. The model makes accurate predictions that allow you to properly allocate capital under future conditions, as well as evaluate the operational impact of a starts plan.
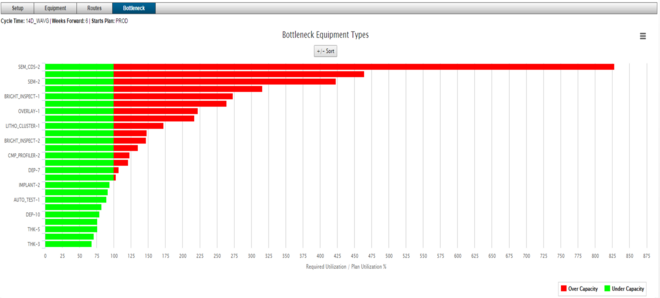
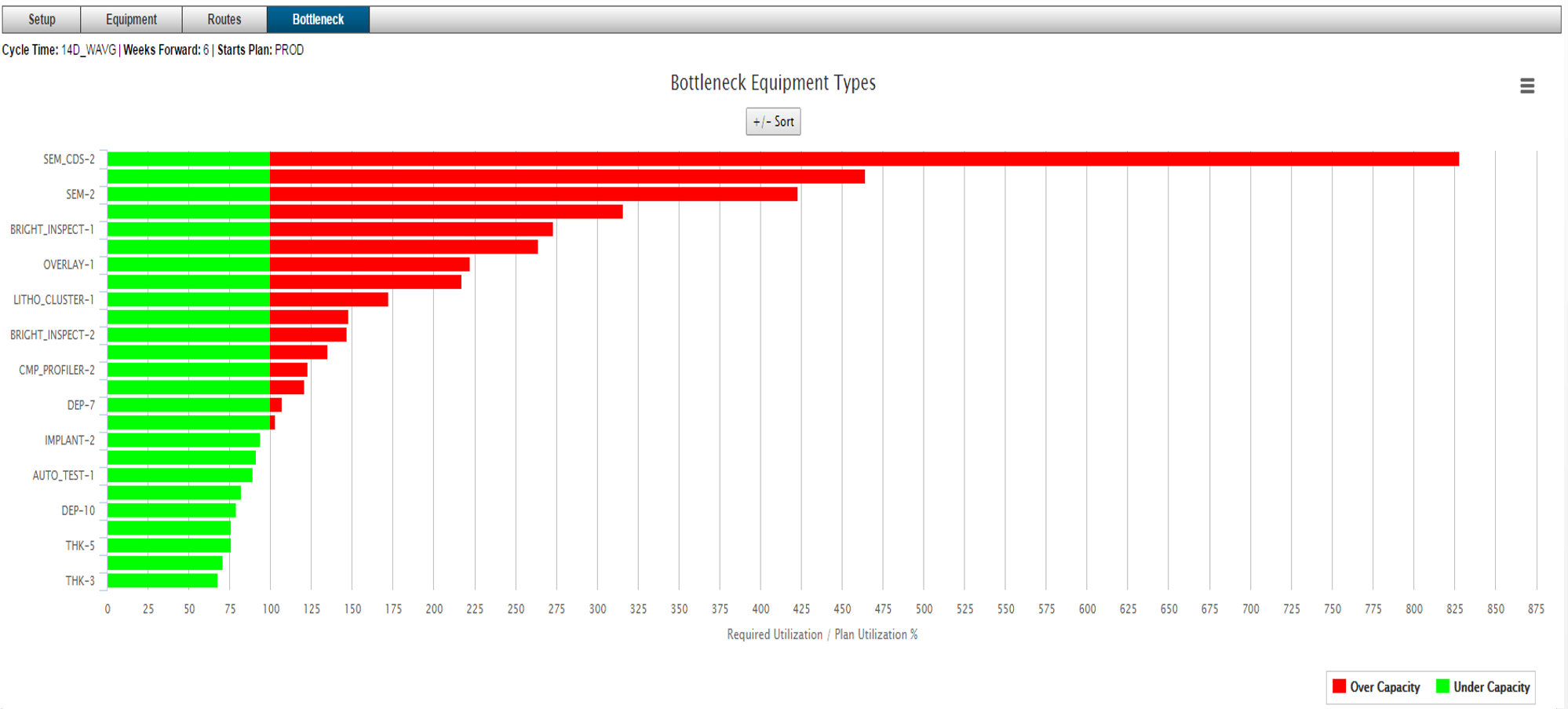
Real-Time Factory Data
Many capacity modeling software solutions require substantial effort to collect and maintain the necessary input data. With Capacity Analyzer, this hard work is already done. The application integrates directly with the Factory Digital Twin, allowing you to instantly leverage your real factory data, updating in real time. This architecture enables an enormous savings of time and labor hours spent getting up and running. You can immediately run Starts scenarios built on continuously updated cycle time and throughput data, giving realistic and accurate results with a minimum of startup cost.
Scenario-Based Modeling
The input for the Capacity Analyzer is a scenario – Wafer Starts, Equipment, and Calculation scenarios.
Wafer Starts scenario is a spreadsheet containing the number of wafers to be started each week by route. An equipment scenario is a spreadsheet containing information on which tools will be available each week. This can be used to simulate adding new tools, or to account for long expected down times, etc. Calculation scenarios allow values such as throughput, sampling percentage, rework percentage to be overwritten from the values retrieved from the Data Warehouse. Once this information is loaded through a simple interface, the Capacity Analyzer program calculates the impact of running the scenario in every area of the factory.
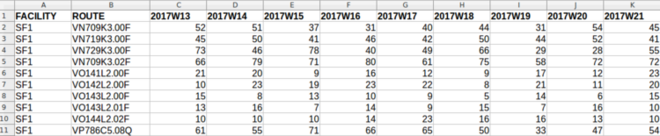
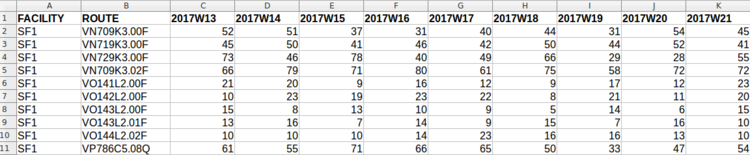
Algorithm
The Capacity Analyzer uses a combination of 14-day averaged Cycle Time (CT) and Throughput (THP) data to calculate the progress of wafer starts through the Fab. The Starts scenario is used in conjunction with CT data to project when WIP starts will arrive at each step in their route, grouped by 1-week intervals. The equipment types required to run the WIP at each step are identified. THP data is then used to calculate the amount of productive time required from each equipment type to process the weekly WIP amounts. This information relates directly to the number of tools required to run the projected amount of WIP in all fab areas.
Once the required productive time for each equipment type has been calculated, the algorithm compares this data to the planned productive and manufacturing time (based on SEMI E10 definitions) of the actual factory equipment or hypothetical inputted equipment scenario. Based on this comparison, equipment types are grouped into four categories indicating the degree to which the equipment type is able to meet the demands of the Starts scenario.


Visualization
Capacity Analyzer is a rich Web App that makes it easy to visualize the program inputs and outputs.
Inputs: When a Wafer Starts scenario is uploaded, a Starts per Week chart is generated. It can be colored by Lot Type, Route Group, or Route Family. Hover-over messages give more details on each segment.
Outputs: Calculation results are displayed in a way that makes it very simple to see bottleneck tools and constrained areas. The ‘Equipment’ view shows a weekly breakdown of key scenario inputs and outputs: available tools versus tools required, planned utilization and availability versus utilization required. The ‘Bottleneck’ view shows a pareto of equipment types organized by the difference between available capacity and capacity required. With these two views, constrained areas are immediately identifiable and quantitatively defined.
Key feature: Include factory WIP
The Capacity Analyzer has the ability to run a Starts scenario while including WIP that is already in the factory. Bottleneck equipment types can then be viewed by week. This is an extraordinarily valuable capability, as it allows the evaluation of a starts plan not only from the perspective of ideal factory capacity, but also from the real and current factory capacity. With this feature, Capacity Analyzer is not only a valuable planning tool, but a tactical Operations tool as well.
The Bottom Line
Excellent production planning requires the ability to answer questions like:
- Does the factory have enough tools in every module to run a planned Starts scenario?
- If not, how many of which types of tools need to be added?
- Where are the constrained modules that are close to their limits?
- How does factory capacity change if the product mix is changed?
The Capacity Analyzer is a quick, easy-to-use application that answers these questions. The calculations leverage the power of the Data Warehouse to ensure accuracy based on real factory data, but the inputs and outputs are straightforward, intuitive and maintenance-free. INFICON has removed all of the hard work of inputting and maintaining relevant calculation data from the process, allowing you to focus on what matters most: exploring different scenarios quickly, and making excellent planning decisions based on accurate capacity projections.