Metrology Sampling Optimizer
Supporting the Autonomous Driving Zero Defect Challenge - World’s First Smart Integrated Sampling Management System
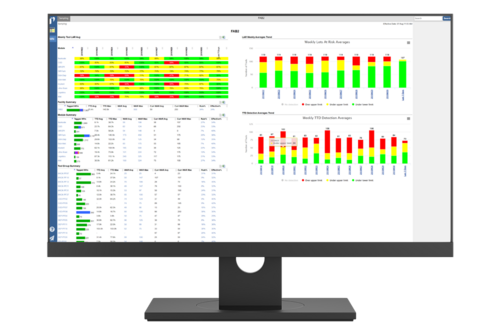
Measurements When it Matters
In a typical fab without comprehensive metrology sampling, it is impossible to know if the factory is over or under sampling measurements. Over sampling wastes productive time and under sampling increases scrap risk.
The Metrology Sampling Optimizer (MSO) uses real-time data and factory conditions to determine what to measure to minimize scrap risks and optimize measurement capacity. MSO has demonstrated a 30% reduction in lots at risk.
Utilizing user-defined rules that leverage practical constraints and real time information, MSO decides when and what to measure product. The sampling plans update in real-time to managing sampling for the entire facility guaranteeing continuously relevant results amidst the dynamic conditions of the facility.
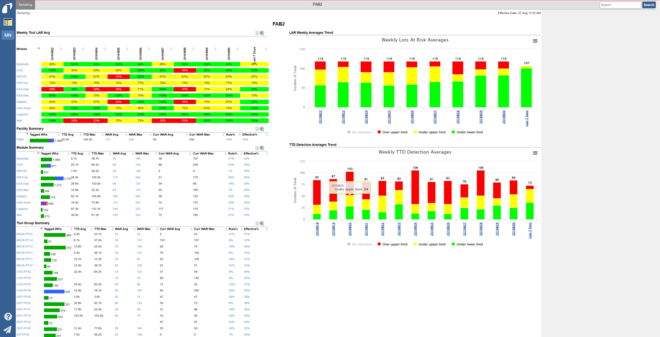
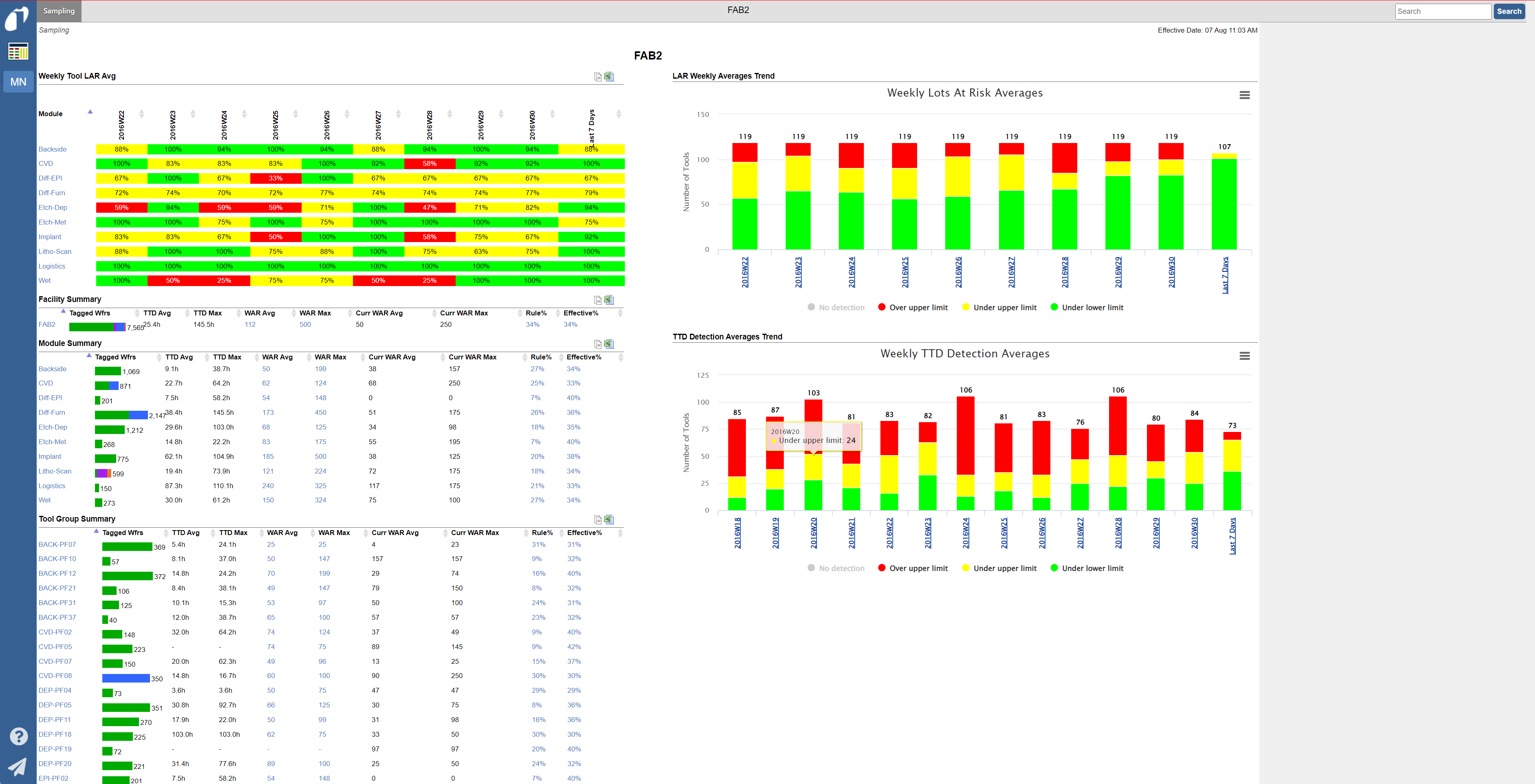
Customize Sampling for Better Coverage
Legacy sampling systems are limited; they apply rules in isolation and fail to adapt to important tool events and changing factory conditions. This results in over sampling of some products and under sampling of others which increases cycle time and product risk.
MSO minimizes sampling by evaluating all related rules whenever a rule triggers sampling. All related rules that would be cleared by sampling the same material are reset even though they were not yet due.
Example:
If two sampling rules, one for Photo and one for Etch, are applied to the same product measurement and the Etch rule becomes due, the Metrology Sampling Optimizer will also consider the Photo rule satisfied for the particular scanner on which the same lot ran, assuming it meets all of the appropriate rule criteria, and vice versa. The sampling plan is satisfied and metrics are updated in real time as each new measurement is recorded.
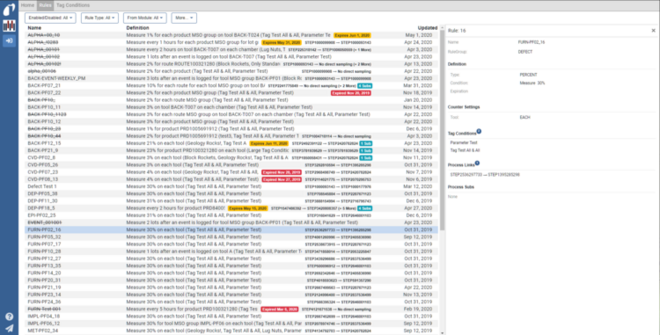
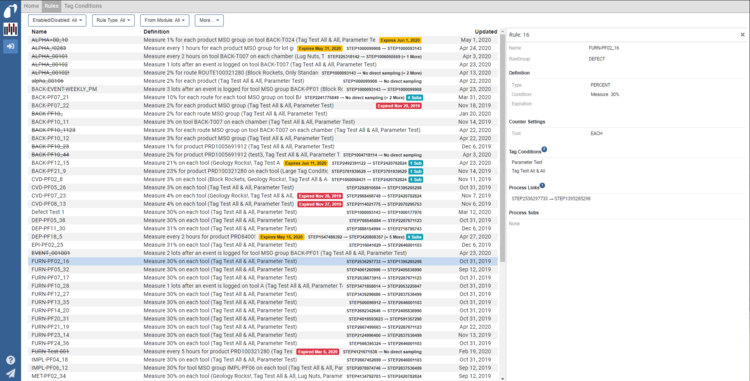
Enabling Smart Manufacturing
The Metrology Sampling Optimizer provides integration to help optimize work-in-process scheduling and provide superior excursion management. Integration with the scheduling system enables MSO to drive high priority or blocking material through measurement sampling as quickly as possible.
Integration with Fault Detection Systems, such as FabGuard, or Excursion Management Systems enables rapid sampling of at-risk material to minimize excursion impact.
- Scheduling and Dispatch. Maximize metrology usage and coverage by coordinating with WiP management
- Manufacturing Execution Systems. Identify which parts have metrology recipes and have measurement steps.
- Fault Detection. Validate FDC detected excursions and sample at-risk lots
- Advanced Process Control. Align sampling plan with APC needs to maximize yield benefits of APC
- Corrective and Preventative Maintenance. Adjust sampling plans based upon corrective and preventative maintenance tasks.
Understand Decisions
The Metrology Sampling Optimizer dashboard shows the real-time state of metrology coverage.
The simple to interpret dashboards help engineers to determine the metrology and defect scan coverage, the mean time to excursion detection, and the number of at-risk lots or substrates. The MSO Dashboard helps engineers to focus the factory sampling efforts by providingvisibility of coverage, current state of sampling, and real-time monitoring. The MSO Dashboard enables immediate action to manage sampling and excursion management.