Monitors
Our thin film monitors deliver real-time measurement of deposition rate and thickness for precise process control in display, semiconductor, optical coating, perovskite, and industrial thin film applications. Our high-precision technology ensures consistency, efficiency, and superior film quality.
Reset the filters to get results.
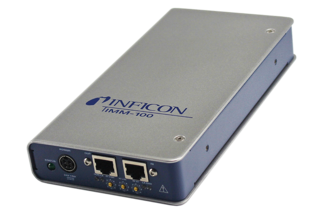
Compact deposition monitor built with ModeLock technology to maximize reproducibility and uniformity with the highest thickness accuracy, best measurement resolution, and lowest rate noise
- INFICON ModeLock technology provides the longest crystal life and ensures the most stable, highest resolution rate and thickness measurement available, even at very low rates
- Maximize yield with the best QCM thickness measurement possible
- Single channel rate and thickness monitor without unnecessary added features to compact size and minimize cost
- EtherCAT communications for seamless integration
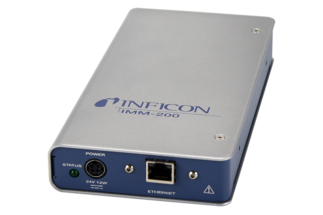
Compact deposition monitor built with ModeLock technology to maximize reproducibility and uniformity with the highest thickness accuracy, best measurement resolution, and lowest rate noise
- INFICON ModeLock technology provides the longest crystal life and ensures the most stable, highest resolution rate and thickness measurement available, even at very low rates
- Maximize yield with the best QCM thickness measurement possible
- Single channel rate and thickness monitor without unnecessary added features to compact size and minimize cost
- Ethernet communications for seamless integration

Multi-Film Rate / Thickness Monitor with averaged sensor control capability for large systems or assigned sensor inputs for different materials
- Two measurement channels standard, an additional four optional
- Analog outputs for rate/thickness recording
- High resolution option: 0.03Hz at 10 readings/sec
- RS-232 standard, USB or Ethernet optional
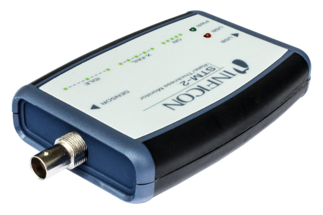
Combines the simplicity of USB connectivity with the accuracy of a precision measurement engine, all in a compact, inexpensive package
- Low cost deposition monitor
- USB connection
- Internal oscillator
- High accuracy at 10 measurements per second
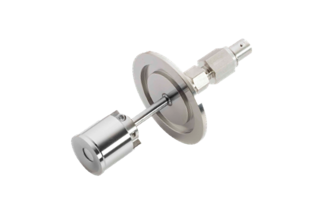
SemiQCM™ SR sensor is one component of a system for precursor monitoring with the other components being an IMM-200 and FabGuard (version 19.12.00-a or higher).
- Real-time, in situ process monitoring
- Prevent over-etching, identify chamber clean end point
- Identify equipment or process state fault
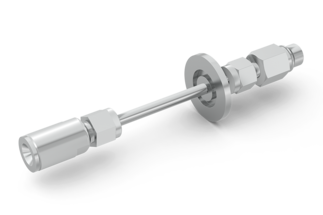
Real-Time, in situ process monitoring, prevent over-etching, identify chamber clean end point
- Real-time, in situ process monitoring
- Prevent over-etching, identify chamber clean end point
- Identify equipment or process state fault