Detección de fallas en la fabricación secundaria.
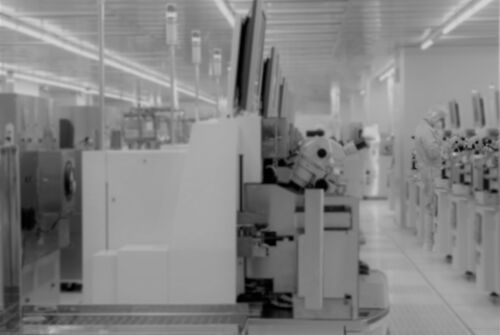
Tras el éxito de las soluciones FDC en la fabricación primaria de obleas. Muchas fabricantes de semiconductores han elegido implementar FDC en sus procesos de ensambles secundarios. La aplicación de FDC a las operaciones unitarias de rectificado, troquelado y unión por cable es la máxima prioridad para estos fabricantes.
La implementación de FDC en las últimas etapas del proceso de producción de semiconductores es incluso más importante que en las primeras etapas del proceso. Cada proceso completado agrega valor a una oblea; cuando una oblea llega a la fabricación secundaria, su valor es muy alto y las fallas son más costosas. Existe un beneficio adicional para los fabricantes de semiconductores en el espacio analógico. El ensamblaje analógico cuesta hasta el 35% del costo total de producción. Compárese esto con el ensamblaje lógico, que es solo el 15% del costo total de producción.
Métodos de recopilación de datos.
Hay múltiples métodos de recolección de datos que son usados para adaptarse a la diversidad de equipos de fabricación secundaria, Incluyendo:
- Comunicación SECS, GEM y EDA
- Importación de archivos
- Analógico
- Controladores lógicos programables
Muchas rectificadoras, cortadoras y soldadoras de alambre modernas admiten los estándares de comunicación SECS, que es el método preferido de recopilación de datos. Los otros métodos se utilizan cuando una herramienta no admite la comunicación SECS o los datos registrados tienen una mayor fidelidad que los datos obtenidos mediante la comunicación SECS.
Rectificado
El primer paso en la fabricación secundaria es el rectificado de la parte posterior de la oblea al espesor deseado. FabGuard FDC se implementó en una herramienta rectificadora polaca estándar de la industria utilizando comunicación SECS a 1 Hz. El desafío con esta rectificadora en particular fue la cantidad de unidades de proceso diferentes dentro de la herramienta. La recopilación de datos activa se configuró para dos estaciones de rectificado, una estación de pulido, una estación de hilado, una estación UV, una estación OCR y para la gestión de instalaciones a nivel herramienta.
La implementación del FDC se centró en la supervisión de los siguientes parámetros de la estación de rectificado: par del husillo, velocidad de la muela, velocidad del mandril y suministro de agua refrigerante. Al igual que la supervisión del proceso frontal, la supervisión del proceso posterior depende de la utilización de las herramientas y de la mezcla de productos. Los métodos para detectar fallos en el proceso deben tener en cuenta estos cambios en las condiciones de funcionamiento.
Corte
Una vez que las obleas han sido rectificadas al grosor deseado, los chips individuales se cortan a lo largo de las líneas de corte para prepararlos para la unión de cables y el embalaje. FabGuard FDC fue implementado en herramientas de cuchilla y láser estándar de la industria utilizando comunicación SECS a 1Hz. Para las cortadoras que utilizan cuchillas para el corte, se monitorean los siguientes parámetros: rpm, corriente de la cuchilla y flujos de agua de refrigeración.
El corte real de la cuchilla puede durar menos de 10 segundos. La velocidad de comunicación SECS típica de 1 Hz puede no ser suficiente para detectar todos los fallos de corte. Un sensor externo que recoja datos a una velocidad más rápida puede permitir resumir los datos por cada corte del margen si es necesario.
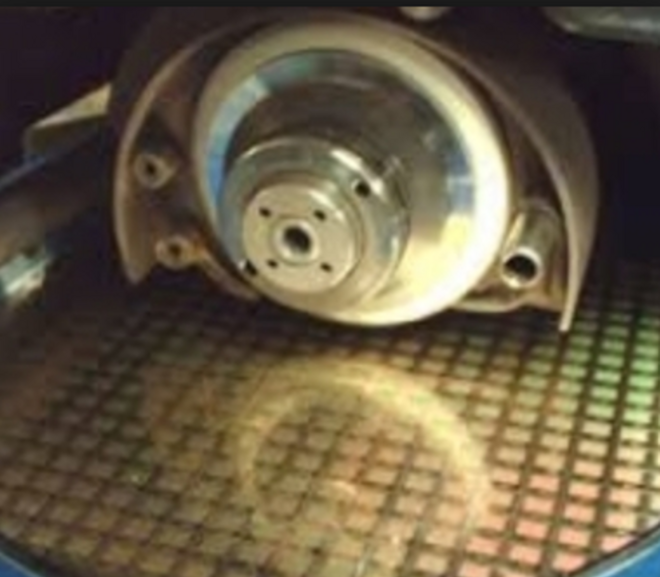
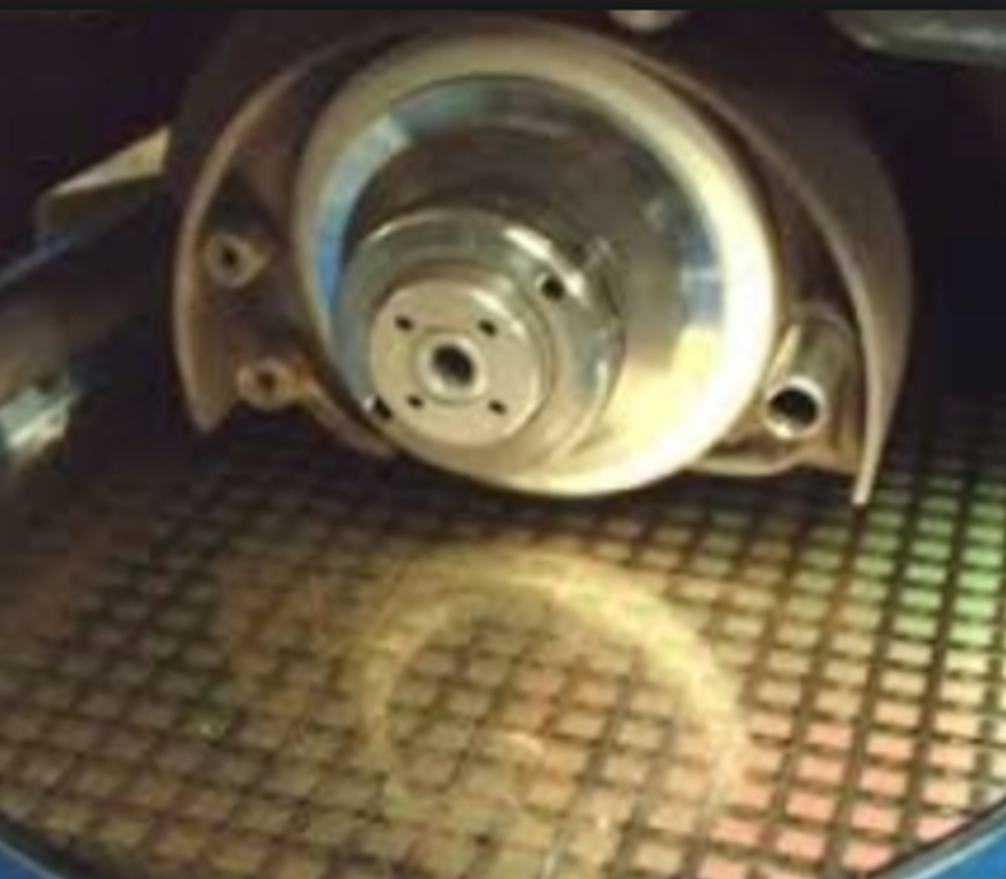
Unión por cables
Las implementaciones exitosas de FabGuard FDC en uniones de alambre estándar de la industria han empleado el uso de importadores de archivos. El proceso de unión en cada punto de unión es relativamente rápido, oscilando entre menos de un segundo y aproximadamente dos segundos. El uso de la comunicación SECS para recopilar estos datos a menos de 1 Hz es difícil para la mayoría de las herramientas.
La mayoría de los proveedores de herramientas proporcionan un archivo de datos al final de cada proceso de oblea que contiene los datos de series temporales de cada punto de unión. Dado que este formato de archivo está estandarizado entre los fabricantes de bonder, la configuración de FDC utilizando este método de recopilación de datos es rápida y sencilla. Los parámetros que suelen controlarse son la temperatura de los componentes y la superposición (desviación del objetivo).
Resumen
FabGuard FDC ha sido implementado exitosamente en herramientas de fabricación secundaria de esmerilado, corte y unión por cable. El FDC secundario proporciona protección adicional al proceso de fabricación cuando las obleas están en su punto más alto de valor.