Managing One-of-a-Kind Tools
The impact of one-of-a-kind tools on fab cycle time, and ways to manage and improve cycle time when they are unavoidable
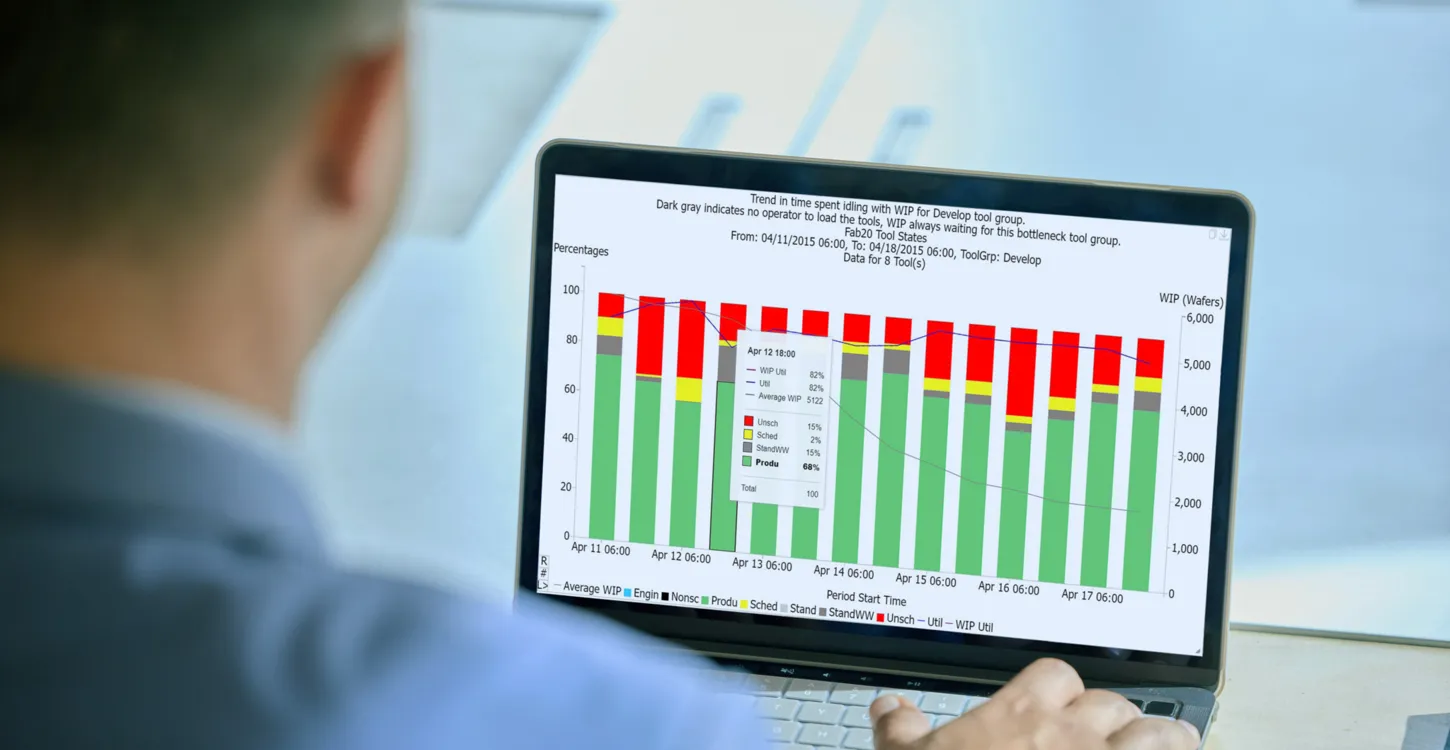
In a wafer fab, cycle time per visit is always higher for single path tools and operations. When a lot is in queue for a single tool, the lot is subject to all the variability that affects that tool. If the tool goes down for extended downtime, the lot must wait until the tool comes back up, because there is nowhere else to process it. If there are two like tools available for processing, the chances are reasonably good that they won’t both be down for extended downtime at the same time. On average, at the same utilization, cycle time X-Factor per visit is roughly twice as high for one-of-a-kind tools than for tool groups with two tools. For this reason, our top cycle time improvement recommendation for fabs that have tool redundancy is to identify and eliminate single path operations. We stand by that recommendation. But what about fabs that have true one-of-a-kind tools? These fabs might include:
- Pilot lines, even if within a larger site.
- Start-up fabs.
- Small government fabs that have no plans to expand.
- Small to mid-size fabs that have redundancy in most of the tool groups, but not all of them.
- Fabs that have redundancy normally, but have key tools in an extended downtime state, with no backup.
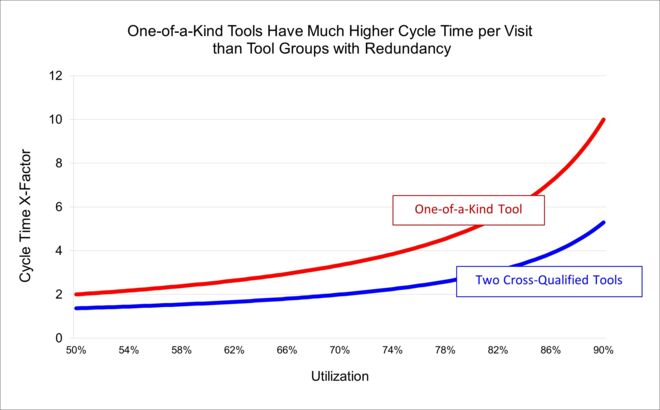
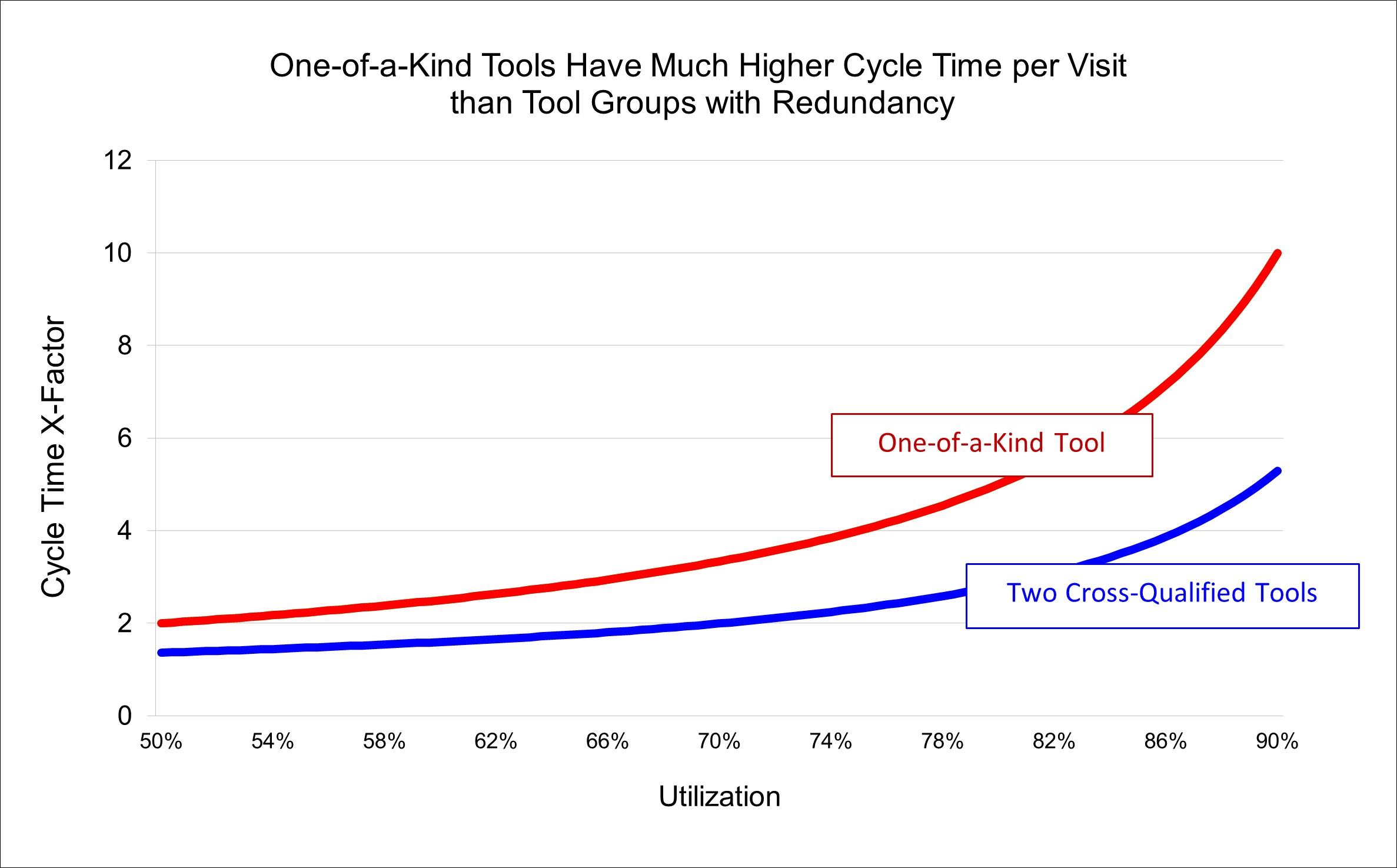
Understanding the impact of one-of-a-kind tools on fab X-Factor
A newsletter subscriber asked us what the cycle time X-Factor (cycle time / theoretical cycle time) would be for a fab consisting entirely of one-of-a-kind tools. We can use queueing models to estimate the X-Factor for a one-of-a-kind tool, as shown below. Under medium variability, the estimate for X-Factor is 1 / (1-Utilization), where utilization is defined as productive time out of the time that the tool is available to manufacturing. A slightly more complex version of this equation that incorporates different levels of variability can also be used and is available in our Operating Curve Spreadsheet below.
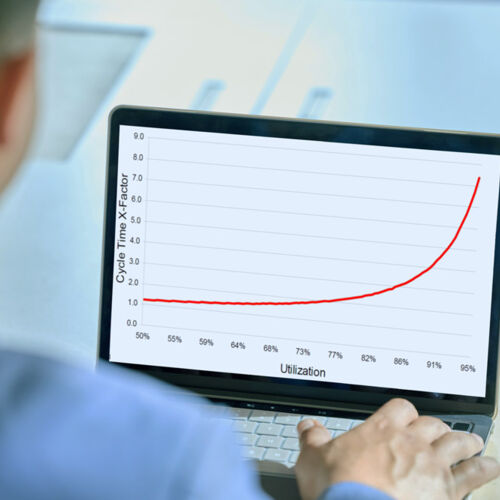
Free FabTime Operating Curve Generator
Unfortunately, there’s no obvious way to scale up from tool level to fab level in terms of the spreadsheet / queueing models. We did experiment with a spreadsheet that used the queueing models for each step, and then added up the estimates across the flow, with tool utilization at each step as a fixed input. However, this approach doesn’t capture the interaction between the tools, or the effect of operators. It’s also necessarily a snapshot in terms of the utilization and variability values for each tool. We lose the educational benefits of looking at the shape of the operating curve.
It’s possible to build a simulation model of the fab to estimate the overall X-Factor in the presence of a one-of-a-kind toolset. However, adding sufficient detail for accuracy (particularly in terms of the impact of operators), and maintaining that level of detail, tends to be prohibitive.
Our real-world experience has been that smaller fabs with multiple one-of-a-kind tools often operate at 4-5X overall (compared with larger fabs with more redundancy that can operate closer to 2.5-3X). However, the actual X-Factor could certainly be higher with many (or all) one-of-a-kind tools and/or if the fab is highly loaded. The full fab X-Factor doesn’t directly scale up from the bottleneck X-Factor(s) in practice because not all tools are equally utilized. We make up cycle time at the less utilized tools, while experiencing high X-Factors on the bottlenecks.
We have come to believe that it’s more useful to measure actual X-Factor, at both the overall fab and the tool level, and then look for the largest improvement opportunities.
Mitigating the impact of one-of-a-kind tools
If you have true one-of-a-kind tools in your factory, there are three primary ways to mitigate their effect.
- Buy more tools.
- Increase buffer capacity.
- Reduce variability.
We will discuss each of these in turn.
1. Buy More Tools:
If you just have a couple of one-of-a-kind tools in your factory, you may find that they disproportionately affect cycle time, even if they are not heavily utilized on average. This is far from the case everywhere, of course, but if any budget is available for capital purchases, you should consider adding redundancy at the one-of-a-kind tools. If you’re deciding which tools to add first within the one-of-a-kind tools, consider tools that:
- Have relatively high utilization.
- Have poor and/or highly variable reliability.
- Are batch tools.
- Have short and/or predictable lead times.
Regarding batch tools, we worked on a project many years ago with Seagate (see Grewal et. al.) that found batch tools tended to be high value in terms of overall cycle time reduction per dollar. This is because running smaller batches smooths flow to downstream steps, reducing arrival variability.
2. Increase Buffer Capacity:
With one-of-a-kind tools, it’s vital to stay away from the steep part of the operating curve. Using our 1 / (1 – Utilization) formula, if we want to achieve 3X cycle time through a one-of-a-kind tool, under moderate variability, we need to keep the utilization to ~67% of available time:
(1 / (1 – Utilization)) = (1 / (1 – 2/3)) = 3
That is, we need about 1/3 of the time that the tool is available to manufacturing to be standby time, or buffer capacity. When planning capacity for one-of-a-kind tools, many fabs plan for a lower utilization than they would for a tool group with redundancy. For example, the chart below shows the operating curve for tool groups with one, two, and three tools where the target is a 3X cycle time. For three tools, under the specified variability assumptions, an 87% utilization target could be set (13% buffer capacity). For two tools, the utilization target drops to 81% utilization (19% buffer capacity), and for one tool it drops to 67% utilization (33% buffer capacity). If we try to run the one-of-a-kind tool at 87% utilization, the X-Factor will be close to 8.

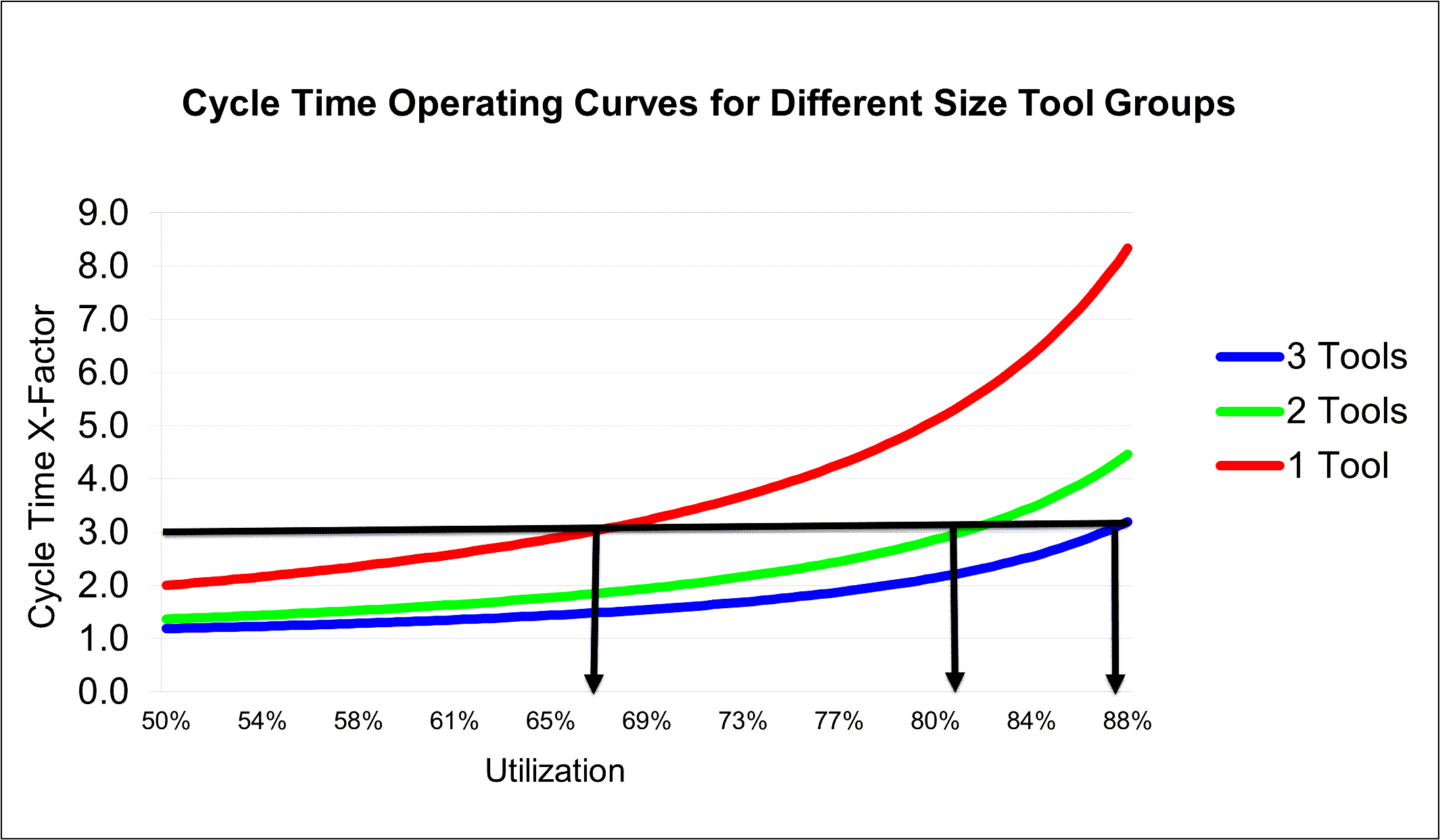
Here again we note that it’s not necessary to achieve a 3X cycle time on all tool groups to achieve a 3X cycle time for the fab. For fabs that have a mix of sizes of tool groups, it’s likely that they will accept a higher X-Factor on the one-of-a-kind tools and expect a lower one on the tool groups with more redundancy. Regardless of what the planned utilization is for a one-of-a-kind tool, the goal should be to increase standby time on the tool by using capacity more effectively. There are two broad ways to do this: by increasing the efficiency of the process time and by reducing the amount of time spent in non-value-added states.
Increase Efficiency of Process Time: The goal for all tools, but especially one-of-a-kind tools, should be to produce the targeted number of wafers in the minimum amount of time. Two things that can help with this are:
- Increase actual units per hour (UPH) rates on the tool. To do this, reduce delays due to alarms and setups and improve processes to be more efficient. An example includes using sensors that can reduce the need for over-etching. This will lower the utilization of the available time without reducing the throughput rate and convert wasted process time into buffer capacity.
- Reduce rework rates. Running rework lots on tools drives up the process time without improving throughput. Efforts to reduce rework, including reprocessing lots due to missed time windows, should focus especially on one-of-a-kind tools.
Reduce Capacity Losses: Capacity losses on a tool can quickly push performance to an unacceptable location on the operating curve. While important on all tools to identify and avoid such losses, it is particularly important to do this for the one-of-a-kind tools. Suggestions include:
- Avoid starving the one-of-a-kind tool. Consider having dispatch rules at upstream tools that prioritize feeding downstream one-of-a-kind tools. If you have a handful of one-of-a-kind tools in your fab, particularly if they are operating above the planned utilization value, it may be worth giving these tools special consideration in your dispatch rules. In cases where all the tools are one-of-a-kind tools, focus on those with high utilization.
- Look for standby-WIP-waiting time when the one-of-a-kind tool is available but not being run. Often this indicates a lack of operators. Consider adding operators (if you can find them in the current environment) or modifying staffing patterns to ensure that the one-of-a-kind tools have better operator coverage.
- Focus availability improvement efforts on highly utilized one-of-a-kind tools. Work to reduce the duration of downtimes on the one-of-a-kind tools, particularly time waiting for parts or waiting for technicians. One-of-a-kind tools are one of the first places you should consider investing in spare parts. Technicians should know (for fabs with a mix of one-of-a-kind tools and larger groups) to prioritize fixing the one-of-a-kind tools.
- Minimize hand-carry hot lots, where you hold tools ahead of the hot lot, in your fab. If you have discretion over which tools to hold, try not to hold the one-of-a-kind tools for as long.
- Don’t hold batch tools idle while you wait for full batches to form.
3. Reduce Variability:
One-of-a-kind tools are disproportionately impacted by variability. Therefore, they benefit most of all the tools in your fab from variability reduction efforts. Some specific ideas include:
- Break up maintenance events instead of grouping them.
- Release lots into the fab in smaller, more frequent batches.
- If you use carts to transport lots between tools, encourage operators not to wait until they are full before delivering lots downstream, especially if delivering to a one-of-a-kind tool.
- Minimize periods of non-scheduled time on tools.
We once worked with a fab that had a high-capacity one-of-a-kind tool that they only ran every other shift. A pile of WIP would build up during the off-shift. The pile would be quickly worked off when the tool was run, but the arrival variability to tools downstream of that tool was high. Making a change to run that tool on both shifts reduced cycle time for the entire fab.
Conclusions
Single path operations in wafer fabs should be avoided wherever possible. They have a disproportionate effect on cycle time. Sometimes, however, single path operations can’t be avoided because the fab has one-of-a-kind tools. A pilot line or startup fab might have all, or nearly all, one-of-a-kind tools, while a slightly larger fab might have only a few. As Thomas Beeg proposed in an article on the Factory Physics and Automation blog, a “Golden Rule” for capacity planning in fabs should be: “avoid one of a kind tools as much as possible – or plan with very low tool utilization for these situations.” But, of course, this “Golden Rule” is a luxury in many real-world situations.
In this article, we have made recommendations for where you should consider buying capacity to add redundancy at one-of-a-kind tools, if that is an option. Where that’s not an option, all you can do is focus on fundamentals: avoid high utilization, especially from forced idle time, on the one-of-a-kind tools and do everything in your power to reduce variability in arrivals and process times at those tools.
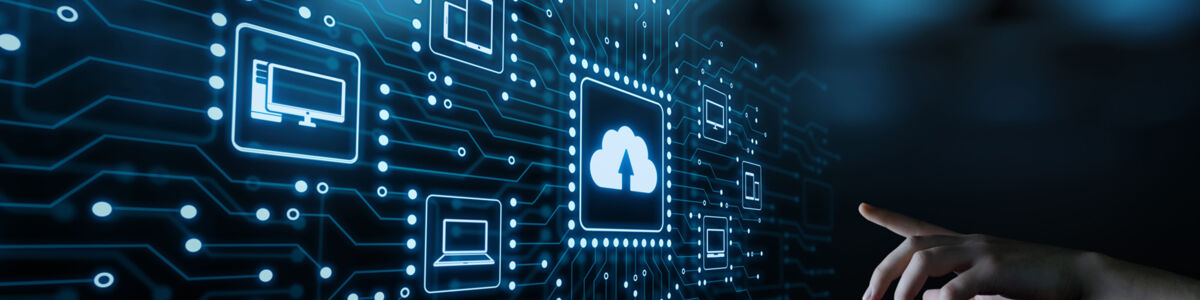