後工程製造のためのFactory Scheduler
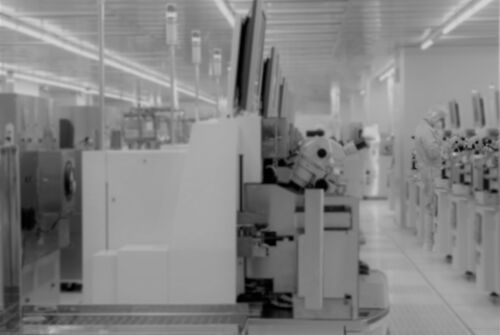
Factory Scheduler概要
半導体製造の初期には、「スケジューリング」は各ロットリストやルートを精査し、日々のWIP(仕掛品)をどのように運用するかを議論する人々のチームを意味していました。工場の規模が拡大するにつれて、そのようなアプローチは非現実的になり、技術的な支援が必要になりました。最初は自家製のシンプルなディスパッチリストが使われ、その後クリティカルレシオなどを利用した拡張ディスパッチ、そして装置中心のルールベースディスパッチが続きました。現在の最先端のアプローチは、工場全体の最適化されたスケジューリングの適用です。Factory Schedulerは、工場の現況と優先順位に基づいてスケジュールを生成するために高度なアルゴリズムを使用します。このスケジュールは、工場内の動的な状況に対応するために自動的に更新されます。
前工程Factory Scheduler
前工程工場は非常に複雑です。前工程工場に投入されたウェーハは、約45~60日で全てのプロセスステップを完了します。プロセス完了の速度と量のため、全体のスケジューラの更新頻度を最小化する必要があります。プロセスフロー全体を予測する代わりに、スケジューラは12時間後までの予測を数分以内に行います。典型的な前工程工場のフローの例を下に示します。
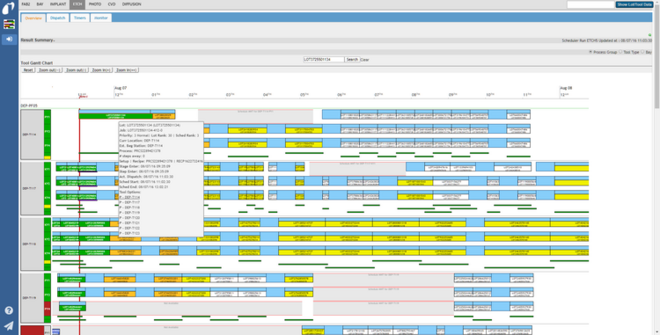
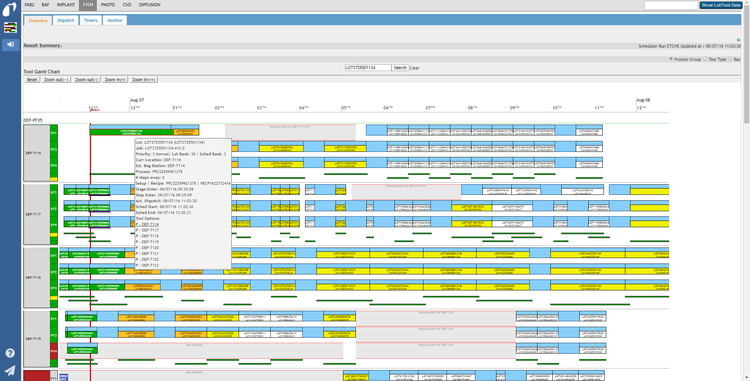
後工程Factory Scheduler
後工程工場は、前工程工場に比べるとそれほど複雑ではありません。後工程工場に投入されるウェーハは、約7~10日で全てのプロセスステップを完了します。これにより、INFICONはスケジューラを利用して後工程プロセス全体を考慮することが可能になりました。各後工程スケジューラ実行で、全てのステップに対して開始から終了までのWIP予測が生成されます。以下に典型的な後工程工場フローの例を示します。
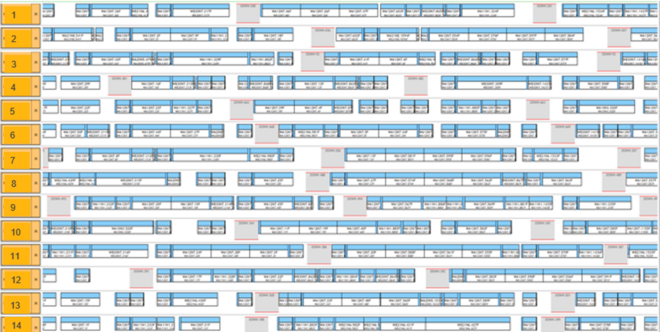
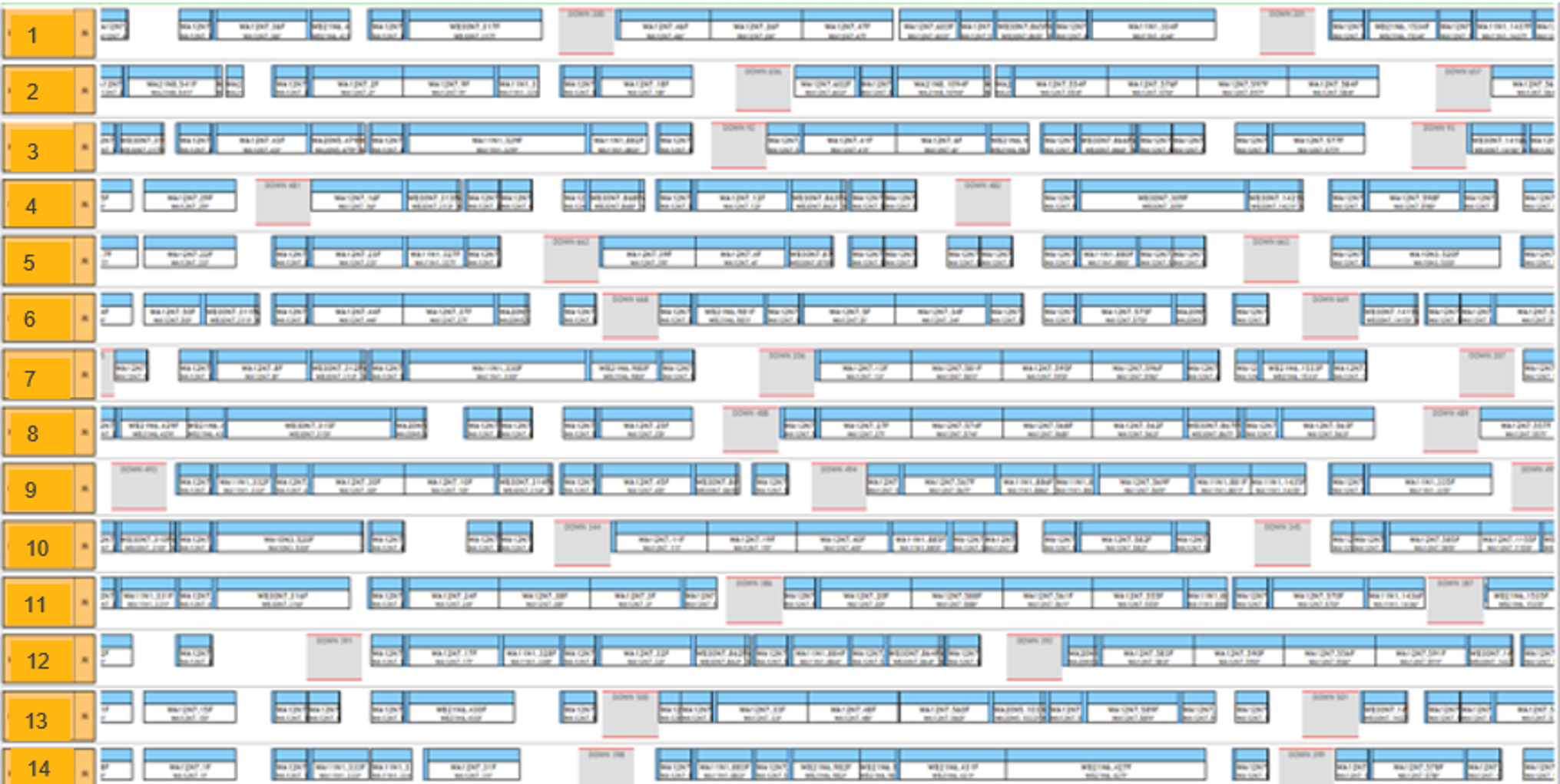
後工程強化1: モデル化された制約を伴うロード計画
Factory Schedulerがエンドツーエンドのスケジューリングに対応しているため、INFICONはファシリティプランニングチームがスケジューラを予測ツールとして利用できるように強化機能を提供しています。この目的のために、INFICONはファシリティチームがモデル化された工場の制約を入力するための方法を作成しました。例えば、設備タイプごとの停止率などを考慮し、それに基づいて4週間のスケジュールを生成します。このロード計画は各ロットごとに28日分表示されます。これは他のエンタープライズリソースプランニング(ERP)システムでは簡単に生成できないものです。
後工程強化2: NextMoveによるロード計画の実行
完全に制約されたスケジュールが生成された後、プロジェクトの次のステップは望ましい4週間の計画を実行することです。これにはNextMoveアプリケーションの実装が必要です。NextMoveの展開中に、いくつかの試験装置でインターロック違反または「生産停止」が発生しました。生産停止は、ツールが生産的な状態にあるが実際にはウェーハを処理していない場合に発生します。これらのイベントはNextMove内で「STOP」アイコンを使用して簡単に識別および表示できるため、これらのツールの損失時間が最小限に抑えられます。
まとめ
Factory SchedulerとNextMoveを組み合わせることで、半導体後工程のオペレーションにおいてサイクルタイムを短縮し、在庫を削減し、スタート計画と予測を改善し、ボトルネックとなるツールの能力を向上させます。