半導体製造装置メーカー
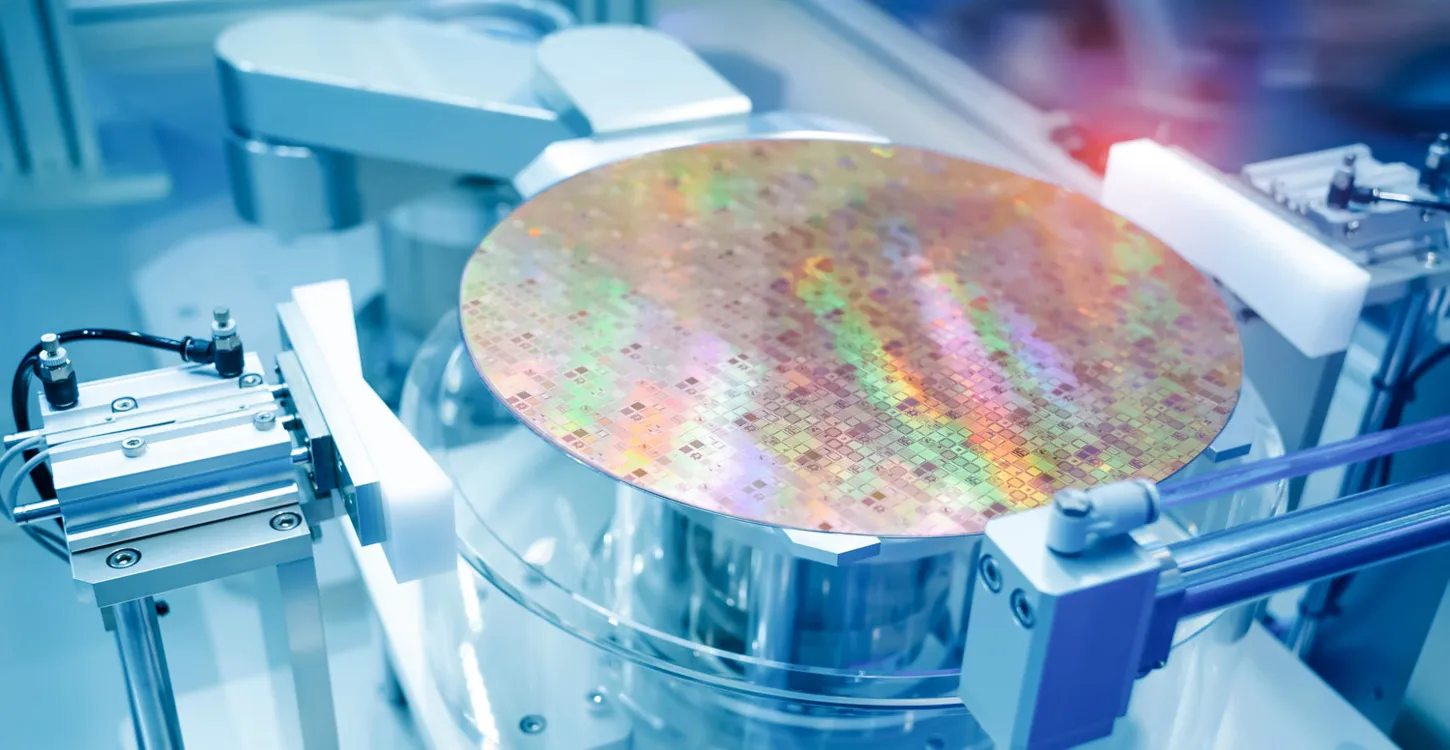
半導体産業は、データ処理、通信、家電、自動車、航空宇宙などで使用される集積回路の設計、製造、組立、テストから構成されています。半導体製造装置メーカーは、マイクロエレクトロニクス・コンポーネントを製造するための半導体ウェハー・ツールを開発・販売しています。半導体製造装置は通常、中央の自動処理装置の周囲に配置された複数のウェーハ処理ステーションで構成されています。チップの複雑化に伴い、コスト削減、生産性向上、プロセスの信頼性向上、製品品質向上のために、より高度な自動化が求められています。 半導体製造装置は、複数のプロセス/洗浄/冷却チャンバー、ロード/アンロード用チャンバー、チャンバー間でウェーハを搬送するマルチプラロボットの3つのコンポーネントまたはコンポーネント群から構成されています。各チャンバーは、異なる圧力、異なるプロセスガスやプラズマで動作し、これらはすべて慎重に制御される必要があります。 最先端の技術でセンサ開発をリードするINFICONは、半導体製造装置の 何千ものプロセス監視作業に役立つ、膨大なセンサのポートフォリオを提供しています。当社のコアテクノロジーには、質量分析、水晶振動子マイクロバランス、RF DCディテクタ、光センサ、真空計、リークディテクタがあります。 INFICONの製品は生産性、効率、稼働時間、歩留まりを向上させることが証明されており、半導体製造装置メーカー(OEM)が成長する半導体のニーズを満たす装置をうまく販売できるようにします。
集積回路(IC)の製造プロセスでは、トランジスタなどの部品を含む電子回路がシリコン結晶ウェハの表面で形成されます。 成膜、フォトレジストコーティング、リソグラフィー、エッチング、イオン注入など、さまざまな工程が必要とされます。これらのアプリケーションは圧力、環境ガス、プラズマ処理の範囲にまたがり、正確なガス組成コントロールとアクティブに監視されたチャンバークリーニングを必要とします。INFICONは真空、質量分析、RF、QCMセンサの最新かつ革新的な技術を装置メーカーに提供し、プロセス品質と装置稼働時間を高めるために、特定かつ最先端のアプリケーションに合わせて調整しています。
シリコンウェハーの製造工程は、単結晶シリコンの引き上げ(CZ法)と、スライス・研磨の2段階に分けられます。 単結晶シリコンの引き上げ法では、多結晶シリコンナゲットを石英ルツボに入れ、それを黒鉛ヒーターで囲んだ結晶引き上げ室にセットします。このナゲットを真空下のアルゴン雰囲気中で加熱して溶かし、種結晶を使ってゆっくり引っ張ります。真空圧力の制御と真空チャンバーの完全性については、当社の真空計とリークディテクターが高い生産量と製品品質を保証します。
半導体製造工程の管理には、計測・検査が重要です。 半導体ウェーハの製造工程は、全体で400~600の工程があり、1~2カ月かけて行われます。もし、工程の早い段階で不具合が発生すれば、その後の時間のかかる工程での作業がすべて無駄になってしまう。そのため、半導体製造工程の重要なポイントには、一定の歩留まりを確認・維持するための計測・検査工程が設けられています。 電子機器製造業界向けの最も包括的で高度なプロセスコントロールとメンテナンス管理ソフトウェアスイートはINFICONから入手可能です。当社のソリューションは、エクスカーションの検出と予測、複雑な意思決定の自動化、業界をリードするプロセスコントロール能力の提供によって、資本生産性、労働効率、工場全体の効率を向上させることが証明されています。正しい情報を収集し、正しいデータを分析し、正しい決断を下す。
ウェハーダイシングは、完成したウェハーを個々のチップにスライスする半導体製造のバックエンドプロセスです。 自動化された方法としては、メカニカルソーイングとレーザーカッティングがあります。メカニカルソーは、丸いダイシングブレードを使ってダイを35mmから0.1mmのサイズにカットします。その後、ダイハンドリング装置でチップをダイボンディング工程に移します。個々のチップは、単独で扱うには小さすぎ、またデリケートです。安全かつ効率的な方法で電子テストを行いながら、保護する必要があります。ダイボンドはダイ・アタッチとも呼ばれ、ベアダイを基板に固定する工程です。後の工程で、基板はチップのミクロなスケールと電子機器製造のマクロなスケールの間のインターフェースとして機能することになります。また、PCボードに見られるチップの保護パッケージの基盤にもなります。ダイボンドの後、ワイヤーボンド工程では、ダイ上の各パッドと基板上の対応するパッドを細い金線で接続します。これにより、チップパッケージ内のシリコンダイと外側のピンが電気的に接続されます。ワイヤーボンドプロセスは、虫の足のように銀色のピンが突き出た黒い長方形のパッケージでおなじみのデュアルインラインパッケージ(DIP)や、4辺が導線になっているPLCCパッケージなどの従来のチップパッケージに使用されています。ワイヤーボンディングに代わり、現代的なフリップチップは「逆さまに」実装されます。そのため、「フリップチップ」と呼ばれます。ワイヤーボンディングのようにチップの周囲にワイヤーを接続するのではなく、チップの表面に「バンプ」と呼ばれる突起を形成し、このバンプをチップと外装パッケージの接続点として利用します。
フリップチップ技術の利点は以下の通りです。
- ワイヤーボンディングでは、ワイヤーの長さ、静電容量、インダクタンスにより信号速度が制限されるのに対し、フリップチップでは、チップへの接続性が向上します。
- 半導体製造の後工程では、ボンディングされたダイとフレームが、プラスチック成形品や封止蓋で封止されます。これで、シリコンダイは電子機器製造に使用できる状態になります。
- サイズ縮小と生産量増加のため、真空は通常、バックエンドプロセスを改善するために使用されます。真空圧コントロールと真空室の完全性のために、INFICONの真空計とリークディテクタは高い生産量と製品品質を保証します。
動作するチップを持つシリコンウェハーを作るプロセス全体は、何千ものステップから成り、デザインから生産まで3ヶ月以上かかることもあります。 ウェハーからチップを取り出すために、ダイヤモンドソーで個々のチップにスライスして切り分けます。半導体製造に最もよく使われる300mmウェハーから切り出される、いわゆる「ダイ」は、チップによって大きさが異なります。数千個のチップを搭載できるウェハーもあれば、数十個のチップを搭載できるウェハーもあります。 チップのダイは、次に「基板」の上に置かれます。これは、マイクロチップのダイのベースボードの一種で、金属箔を使ってチップの入出力信号をシステムの他の部品に導くものです。そして、その蓋を閉めるために、「ヒートスプレッダ」を乗せます。このヒートスプレッダーは、冷却液を保持する小型で平らな金属製の保護容器で、動作中のマイクロチップを確実に冷却する。
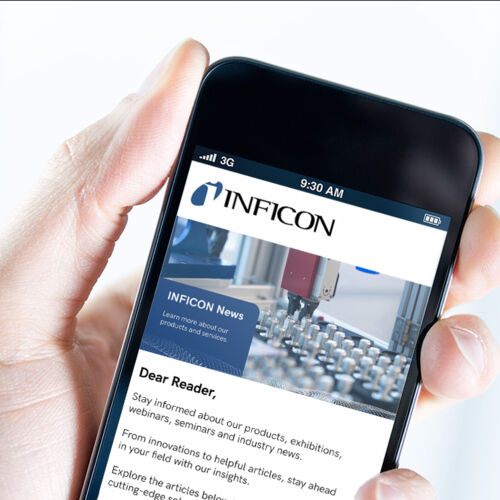