반도체 장비 제조사
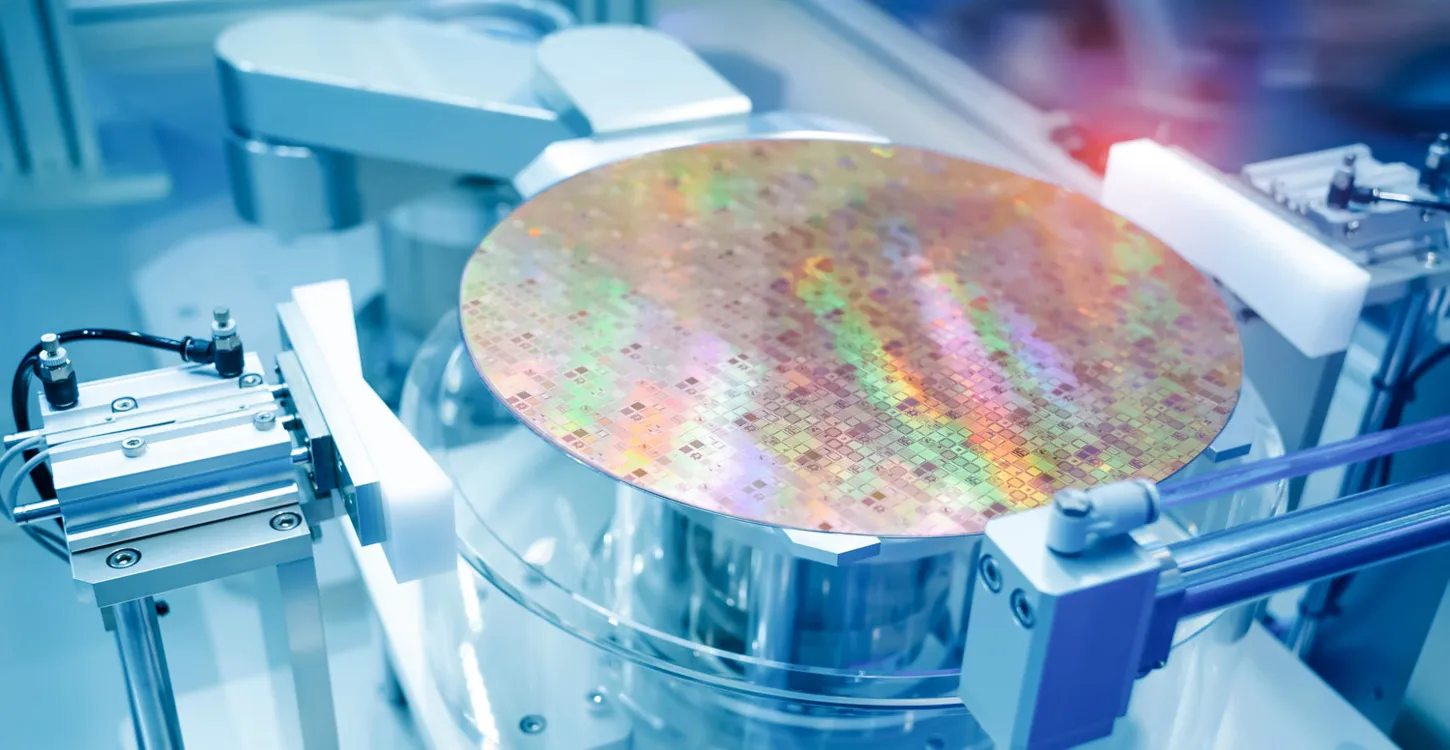
반도체 산업은 데이터 처리, 통신, 소비자 전자 제품, 자동차 및 항공 우주에 사용하기 위한 집적 회로의 설계, 제조, 조립 및 테스트로 구성됩니다. 반도체 장비 제조업체는 마이크로 전자 부품 제조용 반도체 웨이퍼 장비를 개발하고 판매합니다. 일반적으로 중앙의 자동 처리 장치 주변에 배치된 여러 웨이퍼 처리 스테이션으로 구성됩니다. 칩이 점점 더 복잡해짐에 따라 비용을 낮추고 생산성을 높이며 공정 신뢰성과 제품 품질을 개선하기 위해 더 높은 수준의 자동화가 필요합니다.
모든 반도체 장비는 세 가지 구성 요소 또는 구성 요소 그룹으로 구성됩니다. 다수의 공정/세정/냉각 챔버, 로딩 및 언로딩을 위한 챔버, 챔버 간에 웨이퍼를 이송하기 위한 다중 로봇. 각 챔버는 서로 다른 프로세스 가스 또는 플라즈마를 사용하여 서로 다른 압력에서 작동하며, 모두 신중하게 제어해야 합니다. 첨단 기술의 선도적인 센서 개발업체인 INFICON은 반도체 제조
장비를 위한 수천 개의 공정 모니터링 응용 분야에 사용되는 방대한 센서 포트폴리오를 제공 합니다. 당사의 핵심 기술에는 질량 분석법, 쿼츠 크리스탈 마이크로 저울, RF DC 감지기, 광학 센서, 진공 게이지 및 누출 감지기가 포함됩니다.
INFICON 제품은 생산성, 효율성, 가동 시간 및 수율을 높이는 것으로 입증되어 OEM(주문자 상표 부착 생산자)이 증가하는 반도체 요구 사항을 충족하는 장비를 성공적으로 판매할 수 있도록 합니다.
하위 시장
집적회로(IC) 제조 공정에서 실리콘 결정 웨이퍼 표면에 트랜지스터와 같은 부품을 포함하는 전자 회로가 형성됩니다. 증착, 포토레지스트 코팅, 리소그래피, 식각 또는 이온 주입과 같은 다양한 공정의 여러 단계가 필요합니다. 이러한 응용 분야는 다양한 압력, 주변 가스 및 플라즈마 처리에 걸쳐 있으며 정밀한 가스 조성 제어 및 능동적으로 모니터링되는 챔버 청결도가 필요합니다. INFICON은 진공, 질량 분석법, RF 및 QCM 센서의 최신 혁신 기술을 장비 제조업체에 제공하여 프로세스 품질과 장비 가동 시간을 향상시키기 위해 특정 첨단 응용 분야에 맞게 조정되었습니다.
실리콘 웨이퍼 제조 공정은 단결정 잉곳(CZ 방식)을 끌어당기는 단계와 실리콘 웨이퍼를 슬라이싱 및 연마하는 두 단계로 나눌 수 있습니다.
단결정 실리콘 풀링 방법으로 다결정 실리콘 너겟을 석영 도가니에 넣고 크리스탈 풀링 챔버의 흑연 히터로 둘러싸인 흑연 도가니에 넣습니다. 이 너겟은 진공 상태의 아르곤 분위기에서 가열하여 녹인 다음 종자 결정을 사용하여 천천히 끌어당깁니다. 진공 압력 제어 및 진공 챔버 무결성을 위해 당사의 진공 게이지 및 누출 감지기는 높은 생산량과 제품 품질을 보장합니다.
계측 및 검사는 반도체 제조 공정 관리에 중요합니다. 반도체 웨이퍼의 전체 제조 공정에는 400~600개의 단계가 있으며 1~2개월에 걸쳐 진행됩니다. 프로세스 초기에 결함이 발생하면 시간이 많이 걸리는 후속 단계에서 수행한 모든 작업이 낭비됩니다. 따라서 특정 수율을 확인하고 유지할 수 있도록 반도체 제조 공정의 중요한 지점에 계측 및 검사 공정이 설정됩니다.
INFICON은 전자 제조 산업을 위한 가장 종합적이고 진보된 공정 제어 및 유지보수 관리 소프트웨어 제품군을 제공합니다. 당사의 솔루션은 일탈 감지 및 예측, 복잡한 의사 결정 자동화, 업계 최고의 프로세스 제어 기능 제공을 통해 자본 생산성, 노동 효율성 및 전반적인 공장 효율성을 높이는 것으로 입증되었습니다. 올바른 정보 수집 - 올바른 데이터 분석 - 올바른 결정을 내립니다.
웨이퍼 다이싱은 완성된 웨이퍼를 개별 칩으로 슬라이스하는 백엔드 반도체 제조 공정입니다. 자동화된 방법에는 기계적 톱질 및 레이저 절단이 포함됩니다. 기계식 톱질은 원형 다이싱 블레이드를 사용하여 다이를 35mm에서 0.1mm 범위의 크기로 절단하는 다이싱 톱으로 수행됩니다. 그런 다음 다이 핸들링 장비를 사용하여 칩을 다이 본딩 공정으로 옮깁니다. 개별 다이는 자체적으로 처리하기에는 너무 작고 섬세합니다. 그들은 안전하고 효율적인 방식으로 전자적으로 테스트되는 동시에 보호되어야 합니다. 다이 부착이라고도 하는 다이 본드는 베어 다이를 기판에 고정하는 공정입니다. 이후 단계에서 기판은 칩의 미시적 규모와 전자 제품 제조의 거시적 규모 사이의 인터페이스 역할을 할 것입니다. 또한 PC 보드에서 볼 수 있는 보호용 칩 패키지의 기초가 될 것입니다. 다이 본드 후 와이어 본드 프로세스는 얇은 금선을 통해 다이의 각 패드를 기판의 해당 패드에 연결합니다. 이것은 칩 패키지 내부의 실리콘 다이와 외부의 핀 사이에 전기적 연결을 형성합니다. 와이어 본드 공정은 이중 인라인 패키지 또는 DIP와 같은 고전적인 칩 패키지에 사용되며, 은색 핀이 벌레 다리처럼 튀어나온 친숙한 검은색 직사각형 직사각형과 4면 모두에 도체가 있는 PLCC 패키지에 사용됩니다. 와이어 본딩에 대한 최신 대안인 플립 칩은 "거꾸로" 장착됩니다. 따라서 이름은 "플립 칩"입니다. 와이어 본딩과 같이 칩 주변에 와이어를 연결하는 대신 칩 표면에 "범프" 어레이가 형성됩니다. 이 범프는 칩에서 외부 패키지로의 연결 지점으로 사용됩니다.
플립 칩 기술의 장점은 다음과 같습니다
- . 신호 속도를 제한하는 여분의 길이, 커패시턴스 및 인덕턴스가 추가되는 와이어 본딩과 달리 칩에 더 잘 연결됩니다.
- 백엔드 반도체 제조 공정을 마무리하면 본딩된 다이와 프레임이 몰딩된 플라스틱 컴파운드 또는 밀봉된 뚜껑의 부착에 의해 밀봉됩니다. 실리콘 다이는 이제 전자 제품 제조에 사용할 준비가 되었습니다.
- 크기 감소 및 증가하는 출력 요구 사항 진공은 일반적으로 백엔드 프로세스를 개선하는 데 사용됩니다. 진공 압력 제어 및 진공 챔버 무결성을 위해 INFICON 진공 게이지 및 누출 감지기는 높은 생산량과 제품 품질을 보장합니다.
작동하는 칩으로 실리콘 웨이퍼를 만드는 전체 프로세스는 수천 단계로 구성되며 설계에서 생산까지 3개월 이상이 소요될 수 있습니다. 웨이퍼에서 칩을 꺼내기 위해 다이아몬드 톱으로 슬라이스하고 다이싱하여 개별 칩으로 만듭니다. 반도체 제조에 가장 자주 사용되는 크기인 300mm 웨이퍼에서 잘라낸 이 소위 '다이'는 칩마다 크기가 다릅니다. 일부 웨이퍼는 수천 개의 칩을 포함할 수 있는 반면 다른 웨이퍼는 수십 개만 포함할 수 있습니다.
그런 다음 칩 다이를 '기판' 위에 놓습니다. 이것은 칩의 입력 및 출력 신호를 시스템의 다른 부분으로 전달하기 위해 금속 호일을 사용하는 마이크로칩 다이용 베이스보드 유형입니다. 그리고 뚜껑을 닫으려면 상단에 '히트 스프레더'를 얹는다. 이 히트 스프레더는 마이크로칩이 작동 중에 냉각 상태를 유지하도록 하는 냉각 솔루션이 들어 있는 작고 평평한 금속 보호 용기입니다.
고객의 구체적인 요구 사항을 해결하기 위해 긴밀히 협력하겠습니다.
반도체 혁신 센터에서 여러분과 함께 일하게 되어 기쁘게 생각하며, 이곳에서 전문성, 솔루션, 고객 서비스가 한데 어우러져 반도체 산업의 성공을 이끌고 있습니다.
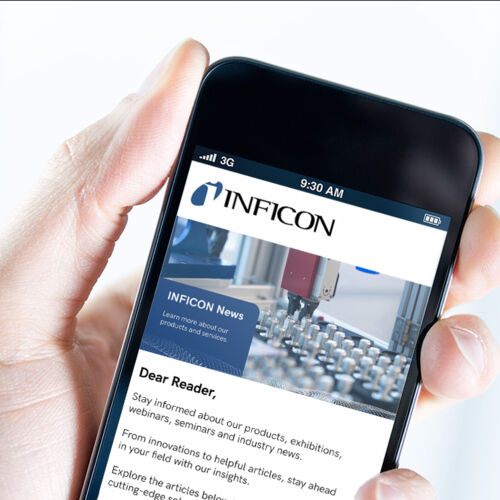