Commonly Reported Wafer Fab Cycle Time Contributors
Discussion of fab complexities like equipment downtime that are commonly reported as having a significant impact on cycle time
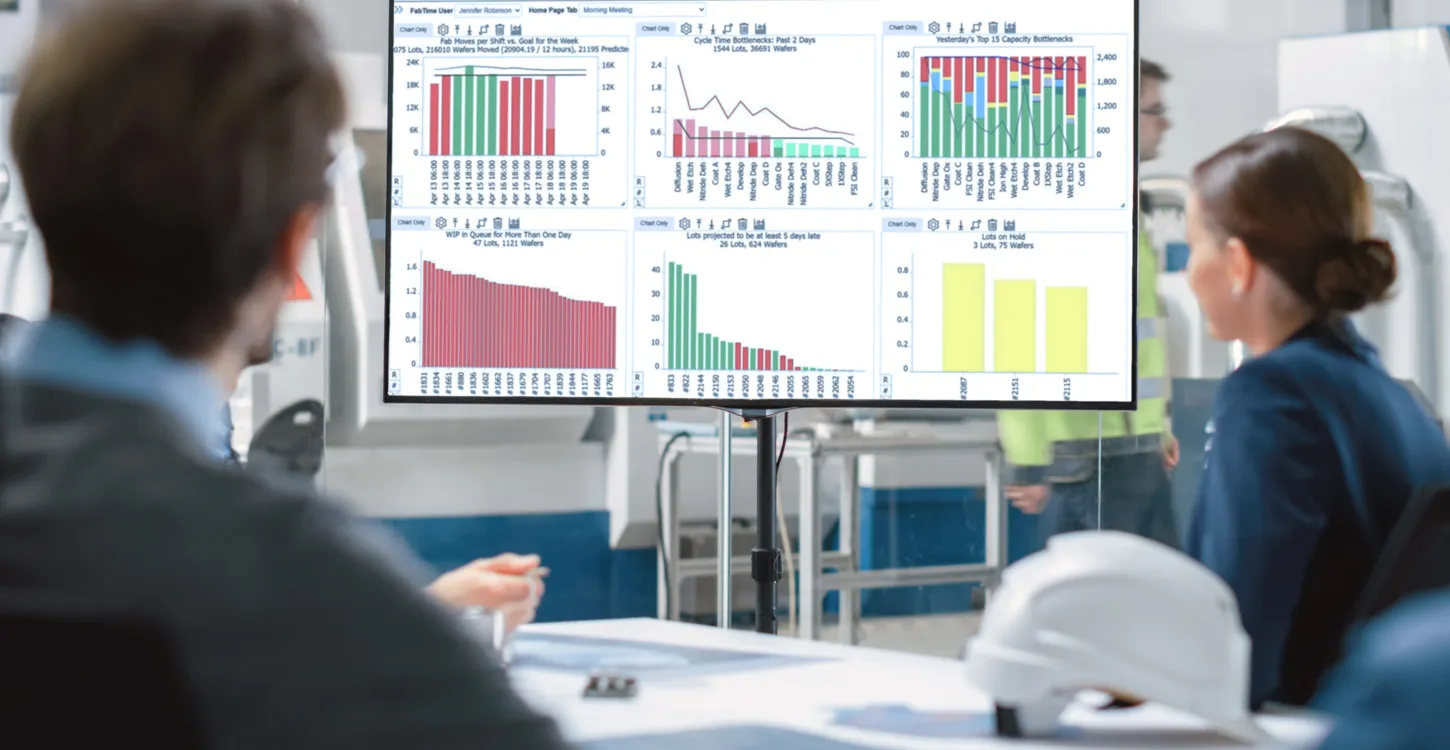
Introduction
By Jennifer Robinson, Cycle Time Evangelist
I’ve been hooked on wafer fabs since I got an internship at SEMATECH (a 90’s-era industry consortium) when I was in graduate school. I was studying operations research, with an emphasis on understanding and improving factories. Wafer fabs were, and are, hands-down the most interesting factories to study. They have long, reentrant process flows, different kinds of tools (batch tools, cluster tools, pre wafer tools, etc.), and endless sources of complexity.
Thirty years later, now with INFICON, I’m still learning about new sources of complexity. At the start of my cycle time improvement class, I always tell people that cycle time improvement can have a huge impact on a fab’s bottom line. If it was easy, I add, everyone would have great cycle time, and I would be out of work.
It’s not easy because of the combination of cost and complexity of a fab. Because fabs are expensive to build and maintain, there is economic pressure to run them efficiently, with tool utilization rates as high as possible, and staff lean enough to keep up productivity numbers. Because market pressures drive change and improvement, fabs have high product mix, and relatively frequent new generations of tools (with consequent reliability issues). Because computer chip production is ever more complex (AI chip requirements, anyone?), process flows get longer and longer.
In working with fabs over the years, I’ve talked to many people about what contributes most, on a day-today basis, to fab cycle time. We’ve also collected data on this topic from the FabTime website and LinkedIn. I thought that readers would be interested in a quick review of the results, together with some thoughts on trends I’ve observed.
What Are the Things that Contribute to Cycle Time in Your Fab?
For more than 20 years, whenever someone filled out a form on the FabTime website we asked them an open-ended question along the lines of “What do you think contributes the most to cycle time in your fab?” Because the results are open format, they are a bit challenging to aggregate. However, I did a bit of searching and adding up of like terms for the most popular responses and came up with the following top five list. Many people listed more than one cycle time contributor in their response, so the results are shown as raw numbers rather than percentages. A response like “downtime on my one-of-a-kind bottleneck tool” is counted under downtime, utilization, and single path.
Downtime | 50 |
---|---|
Utilization/ Constraint/ Bottleneck/ Loading | 46 |
Variability/ Variation/ Variance | 41 |
Single Path/ One-of-a-Kind Tools/ Process Restrictions | 27 |
Product/ Process Mix | 19 |
Holds | 12 |
I’ve also been asking this question at the start of each session of our cycle time management course, and the results are consistent with the above list. Just about every fab mentions downtime, utilization, product mix, and at least one thing that can be categorized as variability. Most mention one-of-a-kind tools or process restrictions. And every fab has other issues that are less common but are a problem for that fab (“running undersize lots”, “ramping starts”, “keep aging equipment online”, “queue time loops”, etc.). Every fab’s story is interesting and unique.
There are a couple of trends that I’ve observed in the responses. Product mix wasn’t a huge issue when we first started asking this question back in the early 2000s but has been climbing the ranks over the years. Perhaps because of higher mix, we’re hearing more about holds now than in the past. During the pandemic, we heard about lack of operators more than ever in the past. Hot lots, on the other hand, seem to be declining in importance to overall cycle time, though most (all?) fabs still have them.
Eventually, we converted the question on the FabTime website to a drop-down list, in the interest of gathering more readily analyzable information. We started asking “What do you think is the biggest contributor to cycle time in your fab?” People could only select one response. Here is a snapshot of the responses:
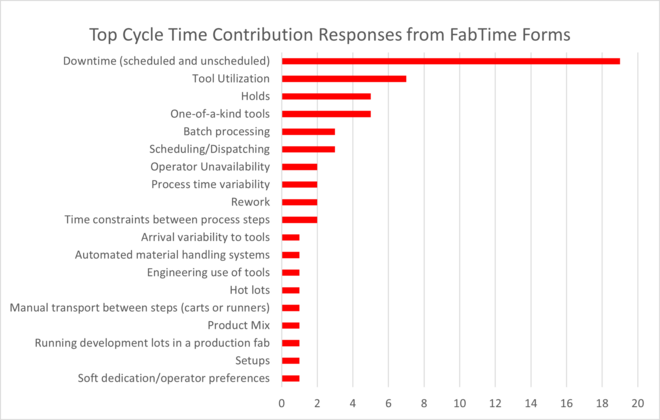
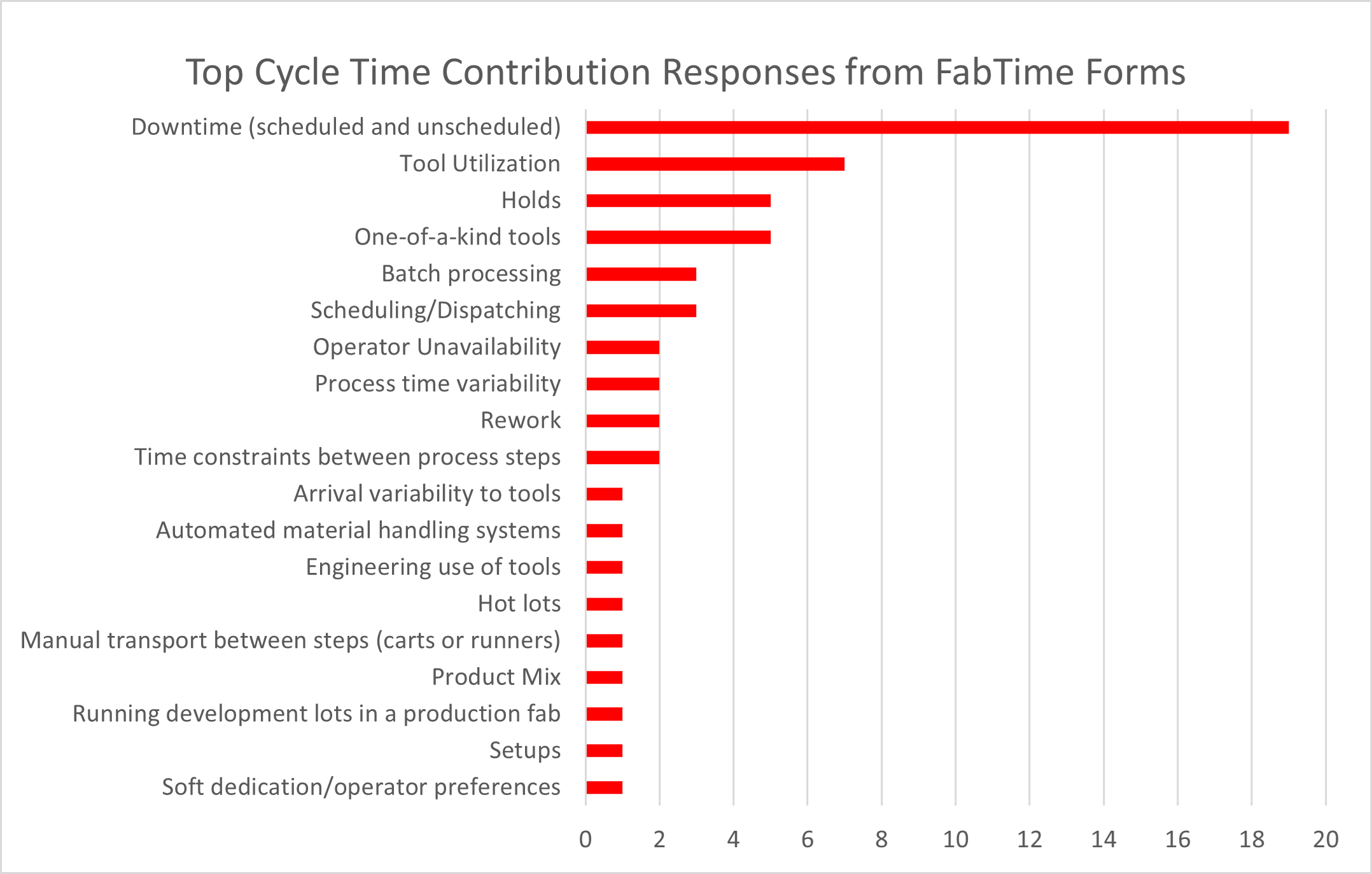
Other contributors listed on the form but not selected include:
- Process restrictions/single path operations
- Lot release
- Reentrant flow
- Scrap
Conclusion
Cycle time improvement in wafer fabs is challenging because fabs are so complex and so expensive. I’ve been asking people for years which factors they think contribute the most to their fabs’ cycle time. The consistent number one response since I started asking the question is equipment downtime.
Utilization, variability, and number of qualified tools, which we have long written about as the fundamental drivers of fab cycle time are at this point well-understood as major cycle time contributors. Other factors like batch processing, holds, product mix, and various specific sources of variability are often mentioned, too. When asked open-ended questions, people cite these common sources, as well as other things ranging from “OEE rate losses” to “lack of line balance” to “insufficient real-time data” to “inefficient changeovers.”
The discussions about which factors affect cycle time in a given wafer fab are my favorite part of teaching the cycle time classes. I learn something new every time. That learning is why I am still working with fabs after 30+ years. They are never dull. In fact, I think that if you have read this far, you should consider recommending to the young people in your life that they learn a bit about fabs, too. You never know. They might get hooked by the complexity, too.
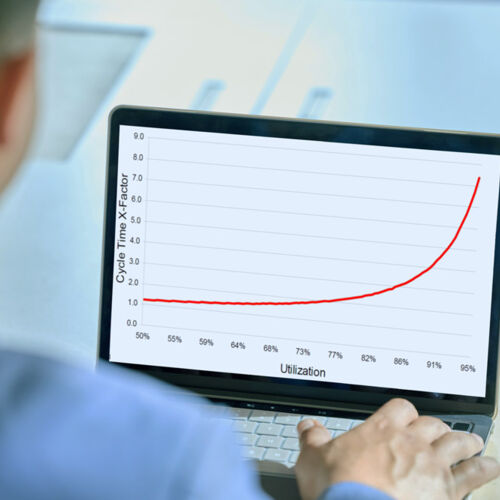