백엔드 프로세스를 위한 FDC
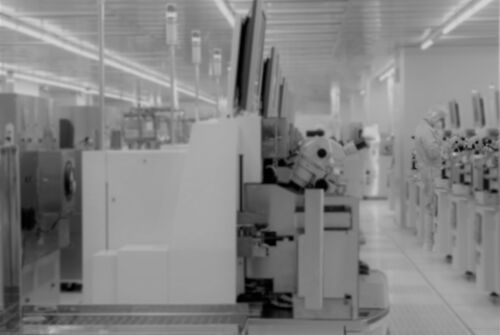
프론트엔드 웨이퍼 공정에서 FDC 솔루션이 성공을 거둔 후, 여러 반도체 제조업체가 백엔드 웨이퍼 조립 공정에 FDC를 구현하기로 결정했습니다. 이들 제조업체는 백 그라인드, 다이스 및 와이어 본드의 단위 작업에 FDC를 적용하는 것을 최우선 과제로 삼고 있습니다.
반도체 생산 공정의 후반 단계에 FDC를 구현하는 것은 공정의 초기 단계보다 훨씬 더 중요합니다. 완성된 각 공정은 웨이퍼에 가치를 더하며, 웨이퍼가 백엔드 공정에 도달하면 그 가치는 매우 높아지고 결함은 더 많은 비용을 초래합니다. 아날로그 분야에서는 반도체 제조업체에게 추가적인 이점이 있습니다. 아날로그 어셈블리 비용은 전체 생산 비용의 최대 35%에 달합니다. 총 생산 비용의 15%에 불과한 로직 어셈블리와 비교해보십시오[1].
데이터 수집 방법
백엔드 처리 장비의 다양성을 수용하기 위해 다음과 같은 여러 가지 데이터 수집 방법이 사용됩니다:
- SECS GEM 및 EDA 통신
- 파일 가져오기
- 아날로그
- 프로그래머블 로직 컨트롤러
많은 최신 백 그라인더, 다이서 및 와이어 본더는 데이터 수집의 기본 방법인 SECS 통신 표준을 지원합니다. 다른 방법은 장비가 SECS 통신을 지원하지 않거나 기록된 데이터의 충실도가 SECS 통신을 통해 얻은 데이터보다 우수한 경우에 사용됩니다.
백 그라인드 예제
백엔드 공정의 첫 번째 단계는 웨이퍼의 뒷면을 원하는 두께로 연마하는 것입니다. FabGuard FDC는 1Hz에서 SECS 통신을 사용하는 업계 표준 폴란드 그라인더 장비에 구현되었습니다. 이 특정 그라인더의 도전 과제는 도구 내 다양한 공정 단위의 수였습니다. 두 개의 연삭 스테이션, 폴리쉬 스테이션, 스피너 스테이션, UV 스테이션, OCR 스테이션 및 장비 레벨 설비 관리를 위해 액티브 데이터 수집을 구성했습니다.
FDC 구현은 스핀들 토크, 휠 속도, 척 속도 및 냉각수 공급과 같은 연삭 스테이션 파라미터를 모니터링하는 데 중점을 두었습니다. 프론트엔드 공정 모니터링과 마찬가지로 백엔드 공정 모니터링도 장비 사용률과 제품 믹스에 따라 달라집니다. 공정 고장을 감지하는 방법은 이러한 작동 조건의 변화를 고려해야 합니다.
다이싱 예시
웨이퍼를 원하는 두께로 연마한 후, 개별 칩을 커프 라인을 따라 절단하여 와이어 본딩 및 패키징을 준비합니다. 1Hz의 SECS 통신을 사용하는 산업 표준 블레이드 및 레이저 다이싱 장비에 FabGuard FDC를 구현했습니다. 절단에 블레이드를 사용하는 다이싱 툴의 경우 rpm, 블레이드 전류, 냉각수 유량 등의 파라미터를 모니터링했습니다.
커프의 실제 절단 시간은 10초 미만일 수 있습니다. 일반적인 SECS 통신 속도인 1Hz로는 모든 절단 결함을 감지하기에 충분하지 않을 수 있습니다. 필요한 경우 더 빠른 속도로 데이터를 수집하는 외부 센서를 사용하면 각 커프 절단별로 데이터를 요약할 수 있습니다.
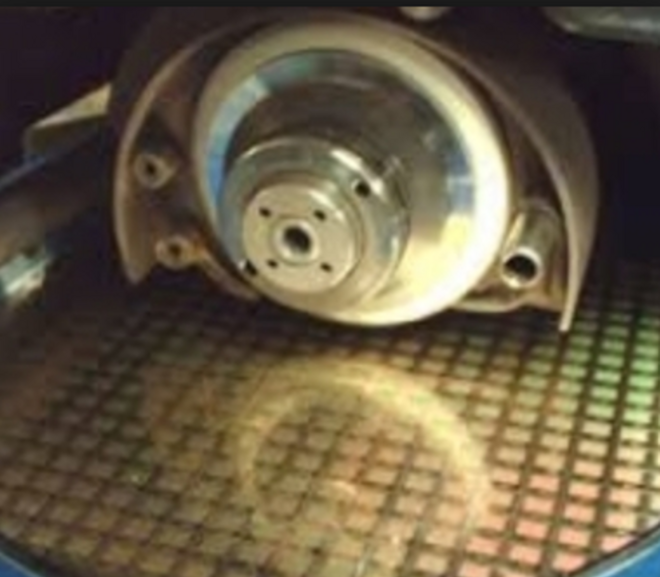
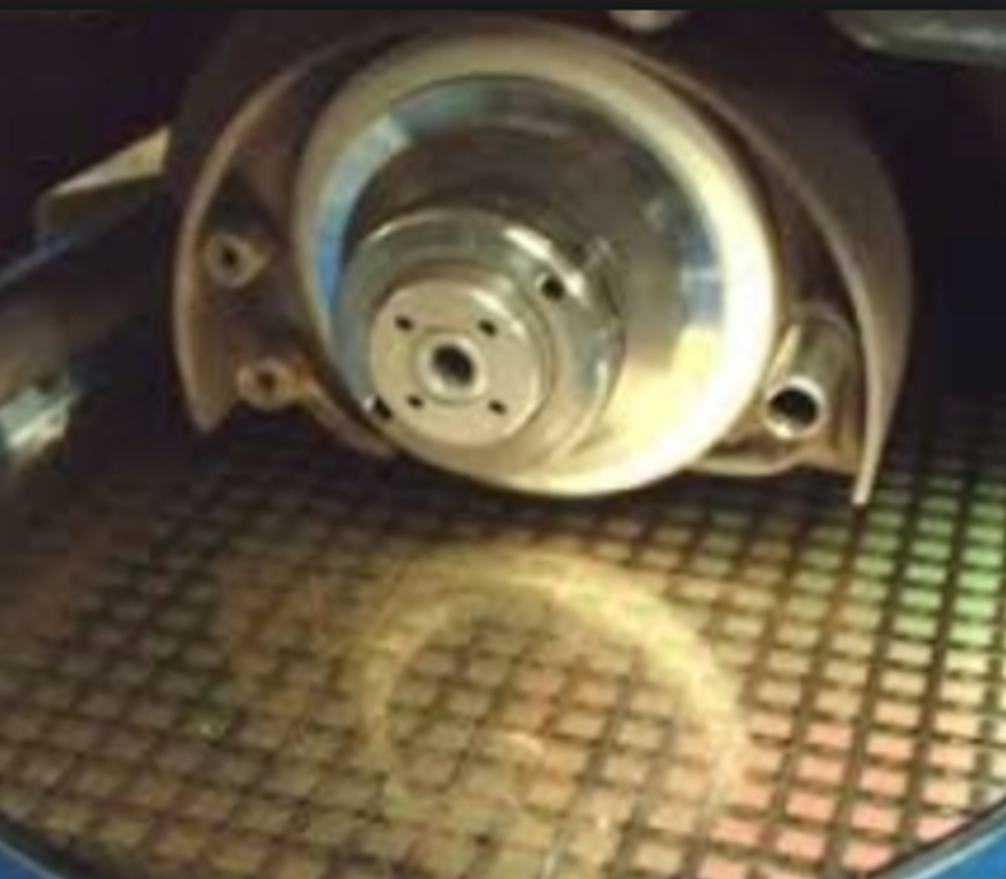
와이어 본드 예제
업계 표준 전선 본더에 FabGuard FDC를 성공적으로 배치한 사례는 파일 가져오기를 사용했습니다. 각 본딩 부위에서의 본딩 프로세스는 1초 미만에서 약 2초 정도로 비교적 빠릅니다. 대부분의 장비에서 1Hz 미만의 속도로 이 데이터를 수집하기 위해 SECS 통신을 사용하는 것은 어렵습니다.
대부분의 장비 공급업체는 각 웨이퍼 공정이 끝날 때 각 본드 사이트에 대한 시계열 데이터가 포함된 데이터 파일을 제공합니다. 이 파일 형식은 본더 제조업체 전반에서 표준화되어 있으므로 이 데이터 수집 방법을 사용하여 FDC를 구성하는 것은 빠르고 간단합니다. 일반적으로 모니터링되는 파라미터는 부품 온도와 오버레이(타겟에서 오프셋)입니다.
요약
FabGuard FDC는 백 그라인드, 다이스 및 와이어 본드 백엔드 공정 장비에 성공적으로 구현되었습니다. 백엔드 FDC는 웨이퍼의 가치가 가장 높을 때 제조 공정에 추가적인 보호 기능을 제공합니다.