Mobility & Automotive
Reliable leak testing in an evolving industry
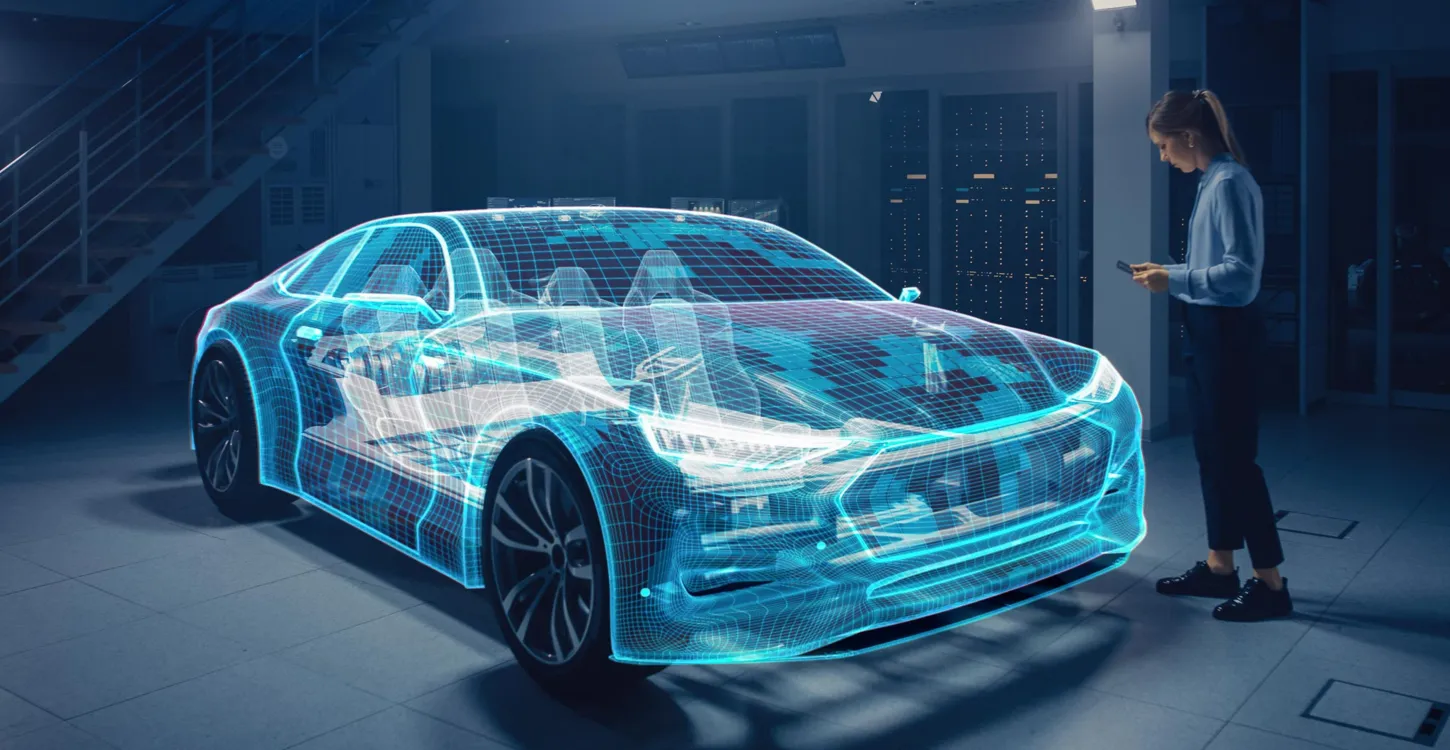
Changes in the automotive industry make leak testing even more important
You are already familiar with a wide variety of leak testing tasks in the production of automotive components, such as fuel tanks, injection systems, airbag gas generators. Now, electric cars (EVs) and fuel cell cars (FCVs) add similar and often even more stringent leak tightness requirements. Whether it's individual Lithium-ion battery cells or battery packs, the bipolar plates of hydrogen fuel cells or the ADAS sensors of autonomous vehicles - INFICON offers you the optimal leak detection solution for all automotive testing tasks.
As automobile manufacturing evolves, leak testing will continue to be an indispensable element of quality assurance in the production of more and more automotive components. Our experts will be happy to advise you on the ideal solution for your specific application combining maximum reliability, high throughput and moderate costs.
In the powertrain of vehicles with internal combustion engines (ICEs), there are a wide variety of components that you must leak test during the production process. Whether it's a matter of pre-testing gear box housings that are still empty or the oil-tightness of the automatic torque converter. You also have to leak test a dual-mass flywheel, as well as an intercooler.
For all these leak testing tasks, traditional methods such as pressure drop tests reach their limits. Intercoolers are sensitive to temperature fluctuations by their very nature. Temperature changes, however, can render the results of a pressure test completely unusable. A much more reliable solution are the tracer gas-based leak testing methods from INFICON - such as the LDS3000 in combination with a vacuum chamber or the LDS3000 AQ for the cost-effective accumulation chamber.
Due to stricter standards to prevent hydrocarbon emissions, the leak rate specifications for fuel tanks and fuel injection systems have steadily tightened worldwide in recent years. Fuel tanks and fuel lines are therefore often tested against leakage rates of 10-4 to 10-6 mbar∙l/s. Water bath and pressure methods cannot test to such low leak rates. Only tracer gas-based methods can do this job.
Accurate leak testing is also indispensable if you manufacture fuel injection valves or fuel pumps. For common-rail injection systems, the requirements are often even stricter because of the high operating pressures. Components used in common-rail systems are leak tested against leak rates in the range of 10-4 to 10-6 mbar∙l/s. Leak detectors like the INFICON LDS3000 and LDS3000 AQ have proven themselves time and again in industrial use for these applications.
After final assembly, all connections between pretested subsystems and components need to be leak tested. INFICON offers you a variety of sniffer leak detectors for this purpose. The procedure: You fill the component with the test gas and then guide the sniffer tip of the device either manually or automatically with the help of robots over the critical areas. Helium or forming gas are suitable test gases, as are gaseous operating media such as R1234yf or CO2.
INFICON refrigerant leak detectors, like the HLD6000 and the Ecotec E3000, are recommended for the connectors of air conditioning systems, fuel injection systems or battery thermal management systems. The Sensistor Sentrac® sniffer leak detector, which uses low-cost forming gas, is used for testing oil and water circuits of combustion engines. Tracer gas sniffer leak detectors, such as the INFICON XL3000flex and the Protec® P3000XL are suitable for dynamic robotic sniffing leak detection because of their high gas flow.
The need to improve AC repair skills is now more important than ever, and solid leak detection is an imperative part of repair best practices. This is driven by several factors affecting the automotive aftermarket including the rising cost of R1234yf, the RRR leak test misconception, and the connection between climate control and battery operation of electric vehicles.
With the increasing price of refrigerant, technicians need to be able to make repairs correctly the first time. When a leak is missed due to faulty or insufficient leak testing, the result will be a customer comeback, with likely all of the expensive refrigerant drained from the system. INFICON Automotive Service Tools (AST) offers a full line of electronic leak detectors that help technicians catch leaks and avoid customer comebacks.
The RRR machine, an equipment requirement for shops that perform AC repair in the U.S., has a leak testing function that checks for large, gross leaks. The idea that this equipment can detect all problematic leaks provides a false sense of security that will result in costly re-repairs. In order to eliminate customer comebacks, technicians should use a dedicated electronic leak detector that can find small leaks that can cause large issues, such as AST300PPM or AST200IR.
The growth in the electronic vehicle market presents yet another reason to use an electronic leak detector. The climate control system in an EV also controls the battery compartment. If the AC is not working, the vehicle will shut off for safety reasons. Because of this, it is crucial that leak testing best practices are followed for EV AC repair.
From AST100, perfect for everyday RAC maintenance, to the intrinsically safe AST100FG that makes it safe to find leaks with hydrogen forming gas, INFICON has a leak testing solution for your application.
Download free E-Mobility E-Book
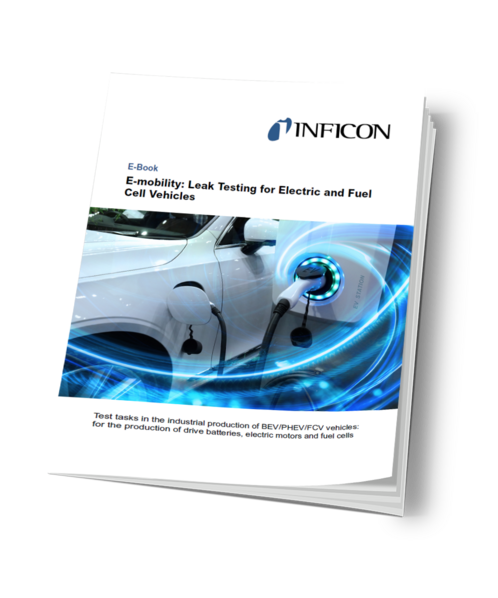
Download Free Leak Testing E-Book
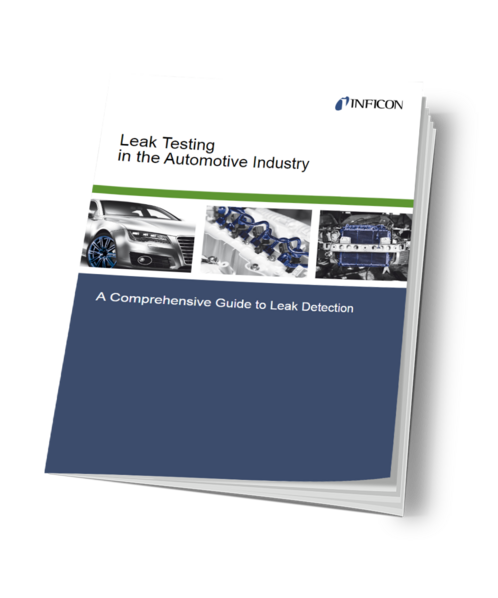
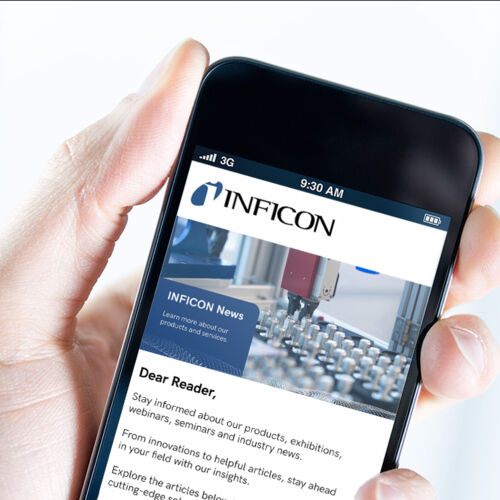